Групповой метод изготовления поковок
Процессы ковки и штамповки поковок нашли достаточно широкое распространение в условиях крупносерийного и массового производств, так как в этом случае используется наиболее передовая технология, экономически вполне себя оправдывающая.
Однако в условиях мелкосерийного и индивидуального производств экономически целесообразно лишь в редких случаях применять подкладные штампы простой конструкции, например для завершающих (финишных) операций.
Известно, что кованые заготовки отличаются сравнительно высокими припусками, а потому основным направлением совершенствования кузнечного производства является замена ковки тем или иным способом штамповки.
С помощью группового метода оказывается возможным либо существенно рационализировать процессы ковки, либо (что еще лучше) заменять ковку штамповкой, т. е. переходить к другому, более совершенному способу формообразования поковок. Это ведет к сокращению области применения индивидуальной технологии (с помощью универсальных плоских бойков) и расширению области использования групповой технологии с применением специального фасонного инструмента, штампов и пр. Таким образом, создается возможность получения поковок более сложной формы с высоким качеством поверхности и малыми припусками.
Наибольший эффект дает применение групповой технологии при индивидуальном и мелкосерийном выпуске поковок. Весьма ощутимый результат получается при серийном производстве и даже в условиях массового производства поковок.
При разработке групповых процессов за номенклатурную единицу принимается не отдельная поковка, а группа технологически сходных поковок.
Технологическая подготовка группового метода изготовления поковок требует выполнения следующих работ: классификации и анализа номенклатуры деталей с целью унификации поковок; группирования поковок; разработки групповой технологии ковки— штамповки; проектирования групповой оснастки; выбора нового специального оборудования или модернизации оборудования, используемого при групповой технологии; расчета ожидаемого технико-экономического эффекта внедрения группового метода ковки — штамповки.
Основными предпосылками успешного внедрения группового метода являются: максимально широкое проведение работ по унификации поковок (как внутризаводской, так и межзаводской), что позволяет увеличить размер партии и избежать индивидуального изготовления целого ряда поковок; изучение и обобщение передового опыта по разработке, практике внедрения и применения групповых технологических процессов.
Основные принципы классификации поковок. Классификация поковок (на группы) должна производиться в зависимости от их конструктивного и технологического подобия, единства потребного для их изготовления оборудования, оснастки и общей последовательности выполнения операций и переходов ковки — штамповки,
Первым этапом классификации является разбивка поковок на классы с учетом следующего: химического состава обрабатываемого металла; состояния (вида) исходного сплава (слиток, продольный или поперечный прокат и др.); конструкции поковки; технологии ковки или горячей штамповки; применяемого оборудования (нагревательные устройства и машины-орудия); механизирующего устройства. В пределах каждого класса поковки разбиваются на группы, являющиеся основой для создания соответствующей групповой технологии.
Классификация ведется с таким расчетом, чтобы обработка каждой группы производилась бы с применением не только одного и того же оборудования (молот, пресс, ковочная машина и т. п.), но и общей технологической оснастки (штампы, специальные приспособления, механизирующие устройства и т. п.) при одной и той же наладке.
В основу подразделения классов на группы деталей положена предельно допустимая поковка для каждой группы, которая определяется при штамповке по максимальной площади проекции фигуры на плоскость разъема, а при ковке по предельно допустимому сечению поковки.
Определение предельно допустимой поковки должно производиться применительно к условиям выполнения основной операции, для осуществления которой требуется наибольшее давление (усилие) машины-орудия.
Если групповая технология разработана с учетом пооперационного использования нескольких машин-орудий (например, ковочных вальцов, молота-пресса, обрезного пресса, калибровочного пресса), то устанавливается главная операция (переход) применительно к каждой машине.
Наличие классификатора и разработанных групповых технологических процессов с указанием предельно допустимых поковок для каждой группы позволяет при получении новых заказов (в том числе и разовых) без разработки новых процессов в короткий срок подготовить всю технологическую документацию, произвести небольшое количество расчетов и быстро организовать производство заданных поковок.
В качестве одного из примеров можно привести опыт некоторых заводов по технологической классификации деталей мелкосерийного многономенклатурного кузнечно-штамповочного производства.
Технологическая классификация деталей для кузнечно-штамповочного производства строится на основе следующих положений.
1. Классификации подлежат окончательно обработанные детали, так как конфигурация штамповок и поковок во многих случаях определяется выбранным способом их производства.
2. Детали классифицируются по основным признакам, которые оказывают существенное влияние на технологический процесс, так как чрезмерная детализация в значительной степени разукрупняет технологические группы деталей,
3. Классификация деталей строится на конструкторских признаках, взятых из чертежа детали, так как технологические признаки на этой стадии еще не определены.
4. Состав и градация признаков классификатора выбирается так, чтобы обеспечить однозначное адресование к групповому (типовому) технологическому процессу.
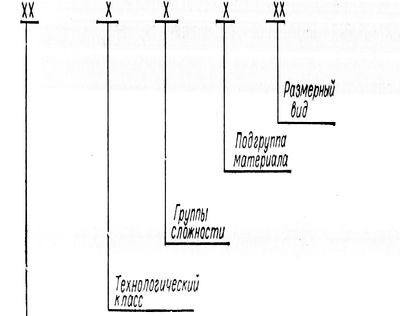
Рис. 1. Структура технологического кода
Для деталей первого класса оптимальными методами производства являются способы закрытой штамповки в цельных матрицах, для второго — процессы с минимальным отходом металла в облой, основанные на методах осадки в торец или высадки. Технологическим процессом для деталей четвертого класса является многопереходная облойная штамповка. Изгиб оси основного элемента у деталей пятого класса определяет добавление специального перехода или операции гибки.
Каждый из указанных классов подразделяется на группы технологической сложности на основе дополнительных признаков формы, относящихся как к детали в целом, так и к ее отдельным элементам.
Состав этих признаков выявлен на основе совместного анализа номенклатуры и технологических процессов как существующих, так и возможных.
Такими признаками являются: наличие или отсутствие выступающих дополнительных элементов на детали (ребер, выступов, отростков, развилин, фланцев); форма и относительные размеры дополнительных элементов; параметрические признаки (относительная длина или высота, относительные объемы утолщения, соотношение сечений детали). Для различных классов деталей состав классификационных признаков различен и находится в соответствии с вариантами технологических процессов штамповки деталей данных классов.
По характеру использования признаки формы подразделяются на разделительные и ограничительные. На основе разделительных признаков объединяются детали, обладающие различными признаками в различных классификационных группировках. На основе ограничительных признаков детали переадресуются из рассматриваемой классификационной группировки в другую.
Ограничительные признаки применяются с целью сокращения общего числа классификационных группировок.
Технологический класс и группа сложности кодируются двумя знаками, образующими третий и четвертый знаки технологического кода детали.
Рассматриваемая классификация предусматривает подразделение деталей по двадцати группам технологической сложности, в том числе деталей первого класса — по трем, деталей второго класса — по шести, третьего —по восьми и четвертого— по трем группам.
Подгруппы деталей организуются по общности технологических свойств марок материалов. Материалы, применяемые в кузнечно-штамповочном производстве, разделены на группы исходя из возможности совместной обработки деталей по однотипному технологическому маршруту. Материалы деталей, принадлежащих к одной подгруппе, обладают общими технологическими свойствами и имеют подобный состав. Подгруппа кодируется одним знаком, образующим пятый знак технологического кода детали.
Всего предусмотрено семь подгрупп.
Размеры деталей и их соотношение влияют на состав переходов ковки и штамповки, а также на мощность необходимого оборудования. Причем на выборе переходов формообразования сказываются в основном относительные размеры, тогда как абсолютные размеры определяют выбор оборудования. Применяемая в рассматриваемом классификаторе размерная характеристика отвечает этим задачам.
Размерные типы деталей формируются по габаритной ширине (или диаметру) и по максимальной длине (или высоте). Размер детали по ширине образует шестой, а по длине — седьмой знаки технологического кода. Градация размерной характеристики и значность кода выбраны таким образом, чтобы по коду можно было судить как об относительной длине, так и о площади проекции детали.
Рассмотренная выше схема классификации деталей кузнечно-штамповочного производства оформлена в виде стандарта предприятия, в котором даются описание последовательности классификации и формирования технологического кода, кодировочные таблицы классификационных признаков, иллюстрированный определитель групп технологической сложности.
Осуществленная классификация деталей показала, что количество формируемых типов деталей не превосходит 150, причем классификаций поддается абсолютное большинство серийно изготовляемых в кузнечно-штамповочном цехе деталей основного производства. На основании разработанного классификатора возможно однозначное объективное группирование деталей,причем на низшем классификационном уровне формируется ограниченное число группировок, обладающих достаточной емкостью для эффективного практического применения групповых (типовых) технологических процессов.
Разработка группового технологического процесса. Основным требованием, предъявляемым к групповому технологическому процессу, является обеспечение изготовления любой поковки данной группы без каких-либо значительных отклонений от выбранной технологической схемы с наибольшей технико-экономической эффективностью. При разработке группового процесса необходимо учитывать ряд параметров, влияющих на выбор проектируемого варианта.
Рассмотрим основные из них.
Исходный металл, его марка, состояние поставки и форма определяют термомеханический режим обработки, способы раскроя заготовок (способ резки проката на заготовки и т. п.), конструкцию и тип нагревательных устройств, количество нагревов-выносов, способ удаления облоя (в холодном или нагретом состоянии), форму, качество и размеры рабочих поверхностей обрабатывающего инструмента, финишные операции и некоторые другие факторы технологического процесса.
Размеры и вес обрабатываемых поковок определяют требуемое усилие пресса или вес падающих частей молота, способ ковки или штамповки, необходимые транспортные и механизирующие процесс обработки устройства, методы контроля качества продукции, конструкцию и размеры применяемого инструмента.
Конструктивные особенности поковок диктуют выбор последовательности операций (предварительно формообразующие, гибочные, правка, калибровка и т. п.) и схемы процесса; конструкции инструмента и необходимых специальных устройств (например, для выталкивания поковки из штампа и т. п.).
Технические условия на поковки в большой степени определяют схему технологического процесса (включение специальных операций — промежуточной осадки, отжига и т. п.), конструкцию поковки (с учетом ее испытания на прочность), жесткость соблюдения заданных режимов обработки.
Последующая обработка поковок должна учитываться с тем, чтобы обеспечить необходимые минимальные припуски, сокращение величии напусков, наивысший коэффициент использования металла и наилучшую обрабатываемость поковок на металлорежущих и других станках, шероховатость поверхности заготовок.
Наиболее удачным вариантом технологии является такой, когда все поковки данной группы обрабатываются по единой схеме группового технологического процесса; в этом случае достигается наиболее высокий технико-экономический эффект.
В то же время допустимы одна или несколько групповых операций в общем процессе. Например, изготовленные различными способами (по различным технологическим схемам) поковки объединяются в группу для калибровки или поковки, изготовленные с помощью различных многооперационных групповых технологий, проходят по единому процессу доводочно-отделочную, термическую или очистную обработку.
Рис. 2. Группы поковок
Следовательно, могут быть однооперационные и многооперационные групповые технологические процессы с законченным или незаконченным циклом обработки в пределах кузнечно-штамповочного цеха.
Формы технологической документации при групповом методе производства поковок отличаются от обычно принятых.
Можно рекомендовать следующие формы.
1. Классификатор с разбивкой поковок на классы.
2. Классификатор с разбивкой поковок на группы (подгруппы), причем такие классификаторы могут быть составлены для каждого класса поковок раздельно.
3. Альбом поковочных чертежей (по классам или по группам) с соответствующими техническими условиями.
4. Альбом схем технологических процессов ковки и штамповки поковок каждой группы и номенклатуры поковок этой группы.
5. Карты технологических процессов обработки для каждой группы или подгруппы, составленные из расчета ковки — штамповки предельно допустимой поковки для каждой группы или подгруппы. j
6. Инструкции по установке и переналадке группового инструмента.
С целью упрощения проектирования технологических процессов и устранения излишне громоздких документов должны быть составлены формы карт отдельно для горячей штамповки (в нескольких вариантах в зависимости от способов штамповки и принятых схем процессов), для ковки из проката, ковки из слитка и т. д.
При наличии карты технологического процесса изготовления предельно допустимой поковки для каждой группы отпадает необходимость в разработке аналогичных карт для каждой поковки данной группы.
Рассмотрим возможности использования групповой технологии при различных способах получения поковки.
Ковка под молотами. В качестве примера рационального применения группового метода при изготовлении поковок мелкими сериями может быть приведен опыт работы кузнечного цеха ЛЭО «Электросила» имени С. М. Кирова. При классификации деталей для молотов выделены три группы поковок, для которых разработана групповая технология.
За основу при группировании были приняты два показателя: габаритные размеры поковок в плоскости разъема и их высота.
В результате классификации к первой группе отнесены поковки, вписывающиеся в рабочие вкладыши диаметром 320 мм и высотой 120 мм, поковки второй группы вписываются во вкладыши диаметром 220 мм и высотой 100 мм. Третья группа штампуется во вкладышах диаметром 160 мм и высотой 75 мм.
На рис. 3 представлена конструкция группового блока для штамповки деталей первых двух групп; на рисунке в скобках указаны размеры для второй группы, а без скобок — для первой.
Блок состоит из двух половин — верхней и нижней. Обе половины имеют цилиндрические гнезда для сменных вкладышей. Крепление вкладышей производится при помощи клиньев, захватывающих небольшую часть цилиндрической поверхности.
Для центрирования половин блока предусмотрены направляющие колонки и втулки.
Предварительная осадка или расплющивание исходной заготовки производится на специальной осадочной площадке, имеющейся на нижней части блока. В нижней половине блока помещены подкладка и толкатель. При переходе на групповую штамповку в конструкцию штамподержателя молота были внесены некоторые изменения.
В центре расточено глухое отверстие, в котором смонтированы поршень, манжета и шток.
Рис. 3. Конструкция группового блока (для групп деталей, показанных на рис. 1.14)
В торце штамподержателя просверлены два отверстия. Одно из них соединено с магистралью сжатого воздуха, ‘другое (верхнее)— с атмосферой. В данном случае штамподержатель, помимо своего прямого назначения, выполняет роль пневматического цилиндра.
Проведение такой модернизации необходимо для осуществления замены вкладышей.
Замена рабочих вкладышей в блоке производится следующим образом. При сомкнутом положении вкладышей (т. е. опущенной бабе молота) расклинивают верхний вкладыш и поднимают бабу, ставя ее на предохранительную стойку. При этом верхний вкладыш выходит из своего гнезда и его снимают с блока. Затем расклинивают нижний вкладыш и подают сжатый воздух в канал
Зазор между вкладышем и соответствующим гнездом делается в пределах 0,3—0,4 мм по диаметру, что обеспечивает центрирование вкладышей и свободное удаление их из гнезда при замене.
Время, необходимое для смены вкладышей, составляет 10— 12 мин вместо 80—90 мин, затрачиваемых на перестановку цель-ноблочных штампов.
При восстановлении ручья в изношенных вкладышах высота последних уменьшается. Компенсация производится соответствующими подкладками 1 различной толщины.
Во избежание выпадания верхнего клина во время штамповки боковые его грани не должны быть параллельными. Поэтому со стороны вкладыша угол наклона клина составляет 7°, а со стороны блока — 15°.
Ковка на гидравлических прессах. Гидравлические прессы используются главным образом для производства крупных поковок. Производство их носит единичный и мелкосерийный характер, поэтому внедрение группового метода в этих условиях особенно целесообразно.
Так как изготовление крупных поковок производится из больших слитков с многократным нагревом металла и использованием металлической (тяжелой) оснастки, то применение группового метода должно прежде всего обеспечить следующее: снижение расхода металла, уменьшение количества нагревов (выносов), сокращение количества и веса применяемой оснастки, повышение производительности труда.
Имеется значительный опыт внедрения группового метода в прессовых цехах. Так, например, на одном из заводов в результате группирования поковок крупного веса, использования прессов усилием 10 000 и 15 000 кН и применения специализированных удлиненных слитков потери металла при ковке сократились на 14%, а также был устранен один вынос (нагрев) по сравнению с индивидуальной технологией. В итоге получена годовая экономия в сумме 0,8 млн. руб.
Для класса пустотелых крупных поковок (полые цилиндры) были применены пустотелые слитки; в результате достигнуто снижение числа нагревов с пяти до двух, сокращение операций с 11 до 5 и расхода металла на 25—30%.
Известен положительный опыт внедрения групповой технологии ковки крупных бандажей и колец («Уралмаш» завод), обеспечивающий повышение производительности труда кузнечных бригад на 30—50%, снижение расхода металла, топлива и других затрат.
На ленинградских заводах также успешно освоена групповая технология ковки турбинных дисков, компрессорных поковок и других деталей с использованием новейших прессов усилием от 10 000 до 12 000 кН.
Ковка на кривошипных прессах. Весьма прогрессивным методом получения поковок в условиях мелкосерийного производства является комбинированная ковка и горячая штамповка. Обработка осуществляется многопереходным процессом с помощью подкладного инструмента или в ручьях одного штампа. Предварительное формообразование поковки должно обеспечивать конфигурацию, близкую к заданной. Окончательное формообразование производится в чистом ручье.
Этот принцип работы создает наиболее благоприятные условия для применения простой быстросменной оснастки, предназначенной для получения поковок определенных групп деталей.
Рассматриваемый способ может применяться для изготовления самых разнообразных поковок, для которых необходимы операции осадки, вытяжки, гибки, рубки, обкатки в различных цилиндрических и фасонных обжимках и штамповки в ручьях открытых штампов.
При групповом методе в условиях мелкосерийного производства номенклатура изготовляемых поковок может быть тем шире и технико-экономические показатели тем выше, чем тщательнее разработана классификация поковок и чем рациональнее выбрана оснастка для изготовления соответствующих групп поковок. В основу классификации поковок положены конфигурация поковки, требуемое усилие деформирования и конструкция группового блока.
Рассмотрим примеры комбинированной ковки — штамповки под кривошипными прессами с применением групповой технологии.
На рис. 4 показаны поковки, разбитые на три класса по требуемым усилиям для штамповки поковок. В зависимости от нормализованных размеров штампов и их конструкции каждый класс деталей разбит на группы: катков (а), цилиндрических шестерен (б), конических шестерен (в), ступиц (г), фланцев (д), фигурных деталей (е).
Рис. 4. Типовые представители классов поковок
Для штамповки данных деталей применены групповые блоки со сменными вкладышами.
Конструкция группового блока с четырьмя направляющими колонками, предназначенного для горячей штамповки на кривошипных прессах, показана на рис. 5. Для поковок меньших размеров применяются аналогичные по конструкции групповые блоки, но с двумя направляющими колонками.
Групповые блоки-штампы состоят из постоянных плит, связанных между собой колонками, и сменных элементов — матрицы и пуансона. Подобные блоки отличаются не только быстросменностью штампа, но и значительной стойкостью при малом расходе инструментальных сталей.
Рис. 5. Сборный групповой блок для горячей штамповки
Группы поковок, для которых характерна удлиненная форма (ступенчатые валики и т. п.) и формообразование которых достигается главным образом операцией вытяжки, могут быть изготовлены с помощью группового блока, показанного на рис. 6. Нижняя плита блока закрепляется на столе пресса четырьмя болтами, а верхняя с помощью хвостовика крепится к ползуну пресса. Нижние бойки для протяжки заготовки являются быстросменными.
Они свободно заводятся в прямоугольный паз нижней плиты блока (боек показан штриховой линией, так как предполагается, что в рассматриваемый момент он снят).
Для вытяжки поковки круглого сечения в блок по мере надобности устанавливаются (свободно в нижний паз плиты) быстросменные пружинные обжимки, входящие в комплект к групповому блоку. Комплект обжимок состоит из нескольких штук, различающихся по диаметру рабочего отверстия в пределах 30—80 мм, через каждые 10 мм.
Рис. 6. Групповой блок для горячей вытяжки удлиненных заготовок
Быстросменные нижние бойки по форме представляют собой прямоугольные призмы, набор которых является принадлежностью к блоку.
Ковка прямоугольной пластины в том же блоке производится с помощью только Двух пар бойков 1—2 и 3—4.
Как показала практика работы, групповая комбинированная ковка и горячая штамповка под кривошипными прессами в условиях мелкосерийного производства наиболее экономична и Должна заменить ковку и штамповку под паровоздушными или пневматическими молотами с весом падающих частей до 20 кН.
Штамповка на фрикционных прессах. Устройство современных фрикционных прессов позволяет регулировать величину хода, скорость движения ползуна и энергию удара, использовать нижний выталкиватель поковок из штампов, наносить жесткий удар в конце хода ползуна. Их конструкция проста, они надежны в эксплуатации и могут успешно применяться для штамповки поковок, особенно в условиях мелкосерийного производства.
В ряде случаев применение фрикционных прессов взамен паровоздушных молотов позволяет уменьшить штамповочные уклоны, припуски и допуски у поковок, а также применять более прогрессивные способы штамповки в закрытых безоблойных штампах, выдавливание и калибровку.
Рис. 7. Схема ковки прямоугольной пластины
Рис. 8. Группа поковок
Рис. 9. Групповой блок с выталкивателем
Рис. 10. Группа поковок
Наибольший интерес представляет опыт использования фрикционных прессов для безоблойной штамповки.
На рис. 8 показана группа деталей, штамповка которых производится в закрытых штампах на фрикционном прессе.
Технологический процесс получения поковки состоит из операций резки заготовки, нагрева ее и штамповки. Резка заготовок производится на токарно-отрезном станке с допуском на Длину по 11 — 12-му квалитетам точности. С учетом допуска на Диаметр окончательная длина заготовки устанавливается после Штампбвки 10—12 шт. поковок. Нагрев заготовок осуществляется
в муфельных электрических печах до 500—600 °С. Штамповка производится на фрикционном прессе усилием 1600 кН.
Конструкция группового блока с выталкиванием поковки из матрицы толкателем фрикционного пресса, применяемого для изготовления поковок данной группы, показана на рис. 9. Блок состоит из подкладной плиты, основания, охлаждающей рубашки со штуцерами, сменной матрицы, нижнего пуансона, выталкивателя, пуансонодержателя, сменного верхнего пуансона, крепежного винта и фиксирующего штифта. Пуансоны, а также матрица являются сменными.
Охлаждение матрицы осуществляется водой, протекающей по винтовым канавкам рубашки.
Для изготовления других групп поковок, представители которых показаны на рис. 10, применяются другие конструкции групповых штампов с цельной и разъемной матрицами.
На рис. 11 показана конструкция блока с цельной сменной матрицей. Блок выполнен из двух узлов — верхнего и нижнего.
Нижний узел штампа состоит из основания с Т-образным пазом, обеспечивающим удержание сменной матрицы, и затвора. На подушку с пуансоном-выталкивателем устанавливается сменная матрица с рукояткой и закрепляется винтами. Подушка имеет пазы для направления и точной фиксации матрицы в рабочем положении.
Верхний узел блока состоит из сменного пуансона, закрепляемого в пуансонодержателе, и хвостовика с винтом. Для предохранения пуансона от разворотов служит фиксирующий штифт.
На рис. 12 показан блок для штамповки деталей, форма которых обусловливает необходимость применения разъемных матриц. Блок состоит из основания, сменной разъемной матрицы с направляющими штифтами и ручкой, пуансоно-держателя, сменного пуансона, винта и фиксирующего штифта.
Рис. 11. Групповой блок с матрицей
Работа проводится в следующем порядке. Нагретую заготовку укладывают в ручей разъемной матрицы в вертикальном положении и при рабочем ходе пресса пуансоном проталкивают в рабочую полость матрицы, где происходит процесс деформации. После штамповки матрица вынимается из конусного гнезда основания и поковка выбрасывается.
Рис. 13. Групповой блок с разъемной матрицей
Рис. 14. Групповой блок для высадки
Другая конструкция группового блока, предназначенная для высадки (штамповки), приведена на рис. 15. Переналадка блока осуществляется непосредственно на прессе.
Штамповка на кривошипных горячештамповочных прессах (КГИ1П). В качестве примера рассмотрим штамповку на прессе МКП-1500, на котором можно штамповать большую номенклатуру поковок с применением быстропереналаживаемых блоков различных конструкций.
При использовании этих прессов широко применяется процесс горячего выдавливания металла для производства точных поковок в ковочных штампах, причем возможно получение поковок и без облоя.
Для крепления инструмента и штампов на прессе применяются различные приспособления и блоки. Рассмотрим некоторые из них.
На рис. 16 показана конструкция болстерной плиты, применяемой для предохранения рабочих поверхностей клинового стола и ползуна пресса от механических повреждений, неравномерного износа и для создания надежного крепления блоков
и инструмента на прессе. Верхняя и нижняя плиты имеют в середине пазы типа «ласточкин хвост» одинаковых размеров, в которые крепятся блоки для удержания штампов. По краям плит имеются Г-образные пазы под квадратные головки болтов для крепления различных приспособлений и инструмента. В пазах обеих плит предусмотрены гнезда для шпонок, препятствующих смещению блоков вдоль паза. В верхней плите просверлено восемь отверстий для болтов и шпилек, которыми она крепится к ползуну пресса.
Нижняя плита имеет четыре отверстия под болты и боковое крепление двумя встречными клиньями с уклоном 1:32. В середине нижней плиты предусмотрено сквозное отверстие овальной формы для выталкивателя.
Для высадки заготовки с одного конца за один ход ползуна пресса применяется блок с вкладышами (штампами), конструкция которого показана на рис. 17. Блок состоит из основания корпуса с разъемной сменной матрицей в сборе с выталкивателем и наконечником.
Корпус крепится к основанию прижимной шайбой и болтами, а матрица фиксируется в корпусе упорными винтами. Верхняя половина блока состоит из плиты, на которой монтируется корпус с помощью винтов. В гнездо корпуса устанавливается сменный пуансон, который крепится с двух сторон упорами, передвигаемыми винтами, пропущенными через хомуты.
Последние привинчиваются к корпусу винтами. Нижняя и верхняя половины блока крепятся к болстерным плитам с помощью клиньев.
Операция высадки производится за один ход ползуна пресса. Во время обратного хода ползуна нижний выталкиватель пресса ударяет по выталкивателю и перемещает его вверх, а заплечики его опираются верхним пояском в наклонную поверхность выточки матрицы, приподнимают и раздвигают ее, освобождая из ручья высаженную заготовку. Гнездо корпуса и наружная поверхность матрицы имеют конические сопрягаемые поверхности, что обеспечивает зажим обеих ее половин при ходе ползуна пресса вниз.
Наконечник является сменным; за счет его Длины можно регулировать длину высаживаемого хвостовика заготовки.
Рис. 16. Элемент конструкции группового блока (болстерная плита)
Рис. 17. Групповой блок в сборе с формовклады шем для высадки
На рис. 18 показаны дополнительные детали для блока, приведенного на рис. 1.27, с помощью которых удается высадить заготовку с одного конца за два хода ползуна пресса.
В этом случае корпус устанавливается и крепится вместо пуансона, о корпусе имеется Т-образный паз, в котором располагается -перемещаемый пуансон с двумя ручьями. На боковой поверхности пуансона имеется глухой паз, куда входит конец винта, фиксирующего положение ручья пуансона относительно ручья матрицы при перемещении пуансона за рукоятку. При совмещении первого ручья пуансона с ручьем матрицы производится конусный набор металла, а при совмещении второго ручья — окончательная высадка головки в размер.
Детали типа втулок с глухими перемычками в середине и фланцем с одной стороны могут быть изготовлены выдавливанием за один ход ползуна пресса. Характерным является то, что металл течет в кольцевой ручей штампа в прямом и обратном направлениях.
Прессы КГШП получают все большее распространение взамен паровоздушных штамповочных молотов. Имеется опыт применения КГШП усилием до 63 ООО кН взамен штамповочных молотов с весом падающих частей до 40—50 кН в условиях крупносерийного массового производства поковок. Такая замена расширяет область применения группового метода горячей штамповки, так как конструкции штампов, используемых на КГШП, представляют собой блок-пакеты с быстросменными вставками, содержащими ручьевые полости.
Автоматизация подготовки производства и изготовления поковок. В настоящее время проведены работы по автоматизации конструирования как самих поковок, так и штампов с использованием стандартных блоков и вставок, а также проектирования технологических процессов штамповки на основе классификации поковок и группового метода. На рис.
19 и 20 показаны комплексные поковки, из которых может быть сделано несколько различных деталей типа тел вращения. На рис. 1.31 показана схема автоматизированного проектирования технологии конструирования поковок и штампов для осесимметричных поковок с помощью ЭВМ. Работа начинается с кодирования профиля детали, который задают в виде координат точек перелома линии, очерчивающей контуры сечения детали, и выбранной линии разъема штампов. Эти координаты кодируются на перфокартах.
Затем на основе формализованного набора правил конструирования определяют параметры поковки — штамповочные уклоны, радиусы скруглений, припуски на обработку резанием и на профиль детали наносят профиль поковки. На этой стадии включаются программы расчета массы поковкщ а) формы и размеров заусенечного мостика, размеров заготовки, усилия штамповки и потребной энергии деформации.
Массу поковки и тип линии разъема штампов используют в качестве исходных данных в программе назначения допусков. Затем получают чертеж поковки в виде таблицы. На ЭВМ контуры стандартных штамповых вставок и выталкивателей подстраиваются (дорисовываются) к профилю поковки. После этого получают чертеж штампа в сборе и чертежи отдельных вставок и выталкивателей, а также спецификацию деталей штампов.
Затем рассчитываются технико-экономические показатели процесса штамповки.
Рис. 18. Блок для крепления штампов, в которых высадка осуществляется за два хода ползуна пресса
Рис. 19. Варианты заготовок: а — заготовки из прутка и вытачиваемые из них детали; б — комплексная поковка; в — детали, вытачиваемые из поковки
Рис. 20. Комплексная деталь для группы типа тел вращения и комплексная поковка: а — группа деталей; б — комплексная деталь 1 и поковка 2
В настоящее время на ряде заводов применяются различные технологические комплексы, позволяющие автоматизировать ряд: ручных операций при изготовлении заготовок на операциях горячего формообразования.
При изготовлении заготовок методом горячей высадки для метизов, заклепок, валиков, клапанов применяются технологические комплексы, состоящие из устройств подогрева заготовки токами высокой частоты (ТВЧ), пресса типа ФА1730, ФА1732, промышленных роботов типа «Циклон-5.01», «Бринг-10Б», систем транспортировки из нагревательных устройств к матрице и штампа.
Рис. 21. Схема автоматизированного проектирования технологии конструирования поковок и штампов для осесимметричных поковок
Схемы компоновки технологического модуля горячего формообразования заготовок приведены на рис. 22 и 23.
Технологический комплекс на базе пресса КГШП-2500 с применением промышленного робота «Циклон-5.01» предназначен для изготовления поковок, круглых в плане и близких по конфигурации. В технологическом комплексе осуществляются операции: подачи заготовок в рабочую зону, смазки штампов, включения пресса, межручьевого переноса, удаления поковки и облоя. Обработка ведется следующими переходами: осадка, штамповка, обрезка, правка.
Масса поковки до 4 кг. Смазка штампов осуществляется с помощью форсунок, расположенных в верхней и нижней части пакета. Загрузка заготовок в нагреватель производится роботом с магнитным захватом. Передача заготовок от нагревателя к прессу выполняется цепным транспортером до бокового окна пресса.
Установка заготовки в штамп и удаление поковок осуществляются промышленным роботом.
Рис. 22. Схема компоновки технологического модуля горячего формообразования:
1 — установка ТВЧ; 2—пресс; 3 — штамп; 4 — смазка штампов; 5 — тара для облоя и окалины; 6 — устройство разгрузочное; 7 — устройство управления; 8 — промышленный робот
Рис. 23. Схема компоновки технологического модуля горячей штамповки на базе пресса КГШП:
1 — установка ТВЧ; 2 — пирометр; 3 — транспортер; 4 — промышленный робот, 5 — разгрузочное устройство поковок; 6 — промышленный робот; 7 — тара для поковок; 8—тара для облоя; 9 — пресс; 10— устройство смазки штампов; И — тара для перегретых и иедогретых заготовок; 12 — устройство управления