Групповой метод литья в песчано-глинистые формы
На данный момент изготовление отливок производится многими методами, но в условиях единичного, мелкосерийного а также серийного производства подавляющее количество (до 85%) их приобретают способом заливки в разовые формы из песчано-глинистых смесей.
Стремительное и качественное получение отливок с применением машинных способов формовки, конвейерной заливки, механизированной выбивки и очистки литья возможно осуществить самый экономично и в малейшие сроки методом внедрения группового способа, широкого применения стандартной оснастки, автоматизации и механизации производственного процесса.
Экономическая эффективность организации таких механизированных литейных цехов мелкосерийного и серийного производств достаточно полно подтверждается практикой.
Подготовительная работа по организации группового производства отливок обязана вестись в следующей последовательности: разработка классификатора и разработка отливок групповых и типовых технологических процессов; выбор, изготовление и проектирование нужной оснастки; выбор оборудования; ответ задач по автоматизации и механизации; планирование и организация группового производства.
Неспециализированная методика классификации отливок. Выбор совокупности классификации отливок обязан проводиться с учетом основных показателей, воздействующих не только на уровень качества изготовления отливок, но и на их себестоимость. Нужно учитывать возможности применения унифицированной и стандартной оснастки, машинных способов формовки, выбивки, очистки.
В один момент с классификацией направляться проводить работу по унификации размеров и элементов подробностей, материалов, технологической оснастки.
Главными показателями, учитываемыми при определении группы подробностей, являются конструктивно-технологические изюминки отливок (габаритные размеры, масса, материал и т. п.), и информацию о технологической оснастке и оборудовании.
На рис. 1 продемонстрирована одна из схем построения классификатора, в соответствии с которой вся номенклатура отливок разбивается на классы, типы и подклассы.
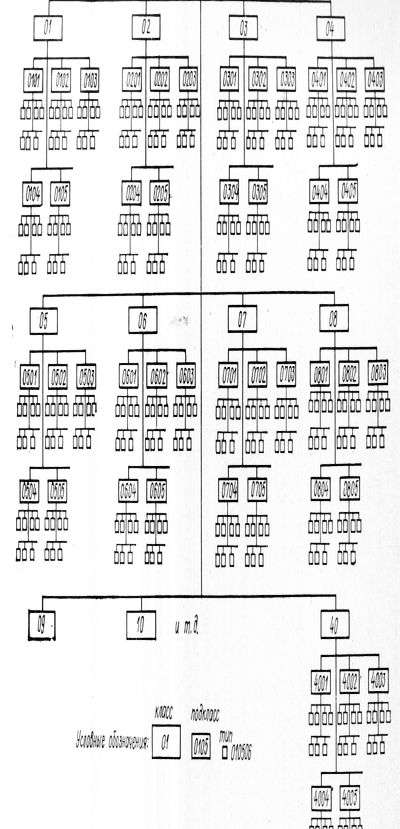
Рис. 1. Классификатор подробностей
Главным показателем, по которому отливки относятся к определенному классу, являются характеристики имеющихся моделей формовочных автомобилей, каковые определяют возможность машинной формовки отливок в пределах тех либо иных габаритных размеров. По этим показателям отливки, габаритные размеры которых приводятся в миллиметрах, подразделяются на следующие классы:
До 300
300—500
500-700
700-900
900-1100
1100—1300
1300-1500
1500—2000
2000—2500
2500-3000
На базе таковой классификации определяется типаж оборудования, нужного для различных групп. Отливки размером более 2000 мм целесообразно изготовлять методом жакетной формовки.
Подкласс составляют отливки, имеющие неспециализированные технологические изюминки. К примеру, отливки, для которых формы изготовляют на формовочных автомобилях, рекомендуется подразделять на следующие подклассы.
Подкласс 1 (шифр 0101) — отливки, формуемые по безразъемным моделям, расположенным в нижней опоке. Это в основном бестержневые отливки либо отливки, имеющие простой центровой стержень без верхнего символа.
Подкласс 2 (шифр 0102) — отливки, формуемые по безразъемным моделям, с висячим дураком.
Подкласс 3 (шифр 0103) — отливки, формуемые по моделям с разъемом, без стержней либо -с несложным центровым стержнем.
Подкласс 4 (шифр 0104) — отливки, формуемые по моделям с разъемом, с внутренними полостями, для образования которых требуется один либо пара стержней.
Подкласс 5 (шифр 0105) — отливки, формуемые по моделям с разъемом, со стержнями для образования внутренних полостей подробности и чтобы получить элементы наружной поверхности.
Подклассы отливок делятся на типы. Под типом понимается совокупность отливок, родных по конструктивному подобию: к примеру, тела вращения и части тел вращения, отливки трубчатые, коробчатые, рычажные, призматические и т. д.
Имея подобного рода классификаторы, возможно приступить к группированию подробностей, что есть главной целью классификации. Комплектование групп подробностей будет производиться, в большинстве случаев, из подробностей, относящихся к одному подклассу.
Учет подробностей, входящих в определенные класс, под. тип и класс, ведется по особой классификационной ведомости.
При многономенклатурном производстве рекомендуется использовать совокупность особенностей и кодирования элементов каждой отливки. В этих обстоятельствах классификация подробностей на группы производится посредством ЭВМ по заданным показателям, характеризующим особенности каждой группы отливок.
Для получения отливки нужно комплексное ответ последовательности технологических вопросов, связанных не только с процессом литья, но и с рядом запасных операций, таких как приготовление формовочной и стержневой смеси, изготовление стержней и форм. Значительное значение имеет и разработка плавки металла и т. п.
В производстве отливок в песчаные формы должны активно использоваться типовые и групповые технологические процессы, при разработке которых нужно применять имеющиеся производственный опыт и рекомендации передовых литейных цехов.
На протяжении проведения работы по классификации отливок нужно проводить отработку конструкции на технологичность. Большой уровень технологичности повышает уровень качества и облегчает разработку групповых и типовых технологических процессов. Вследствие этого конструирование подробностей в условиях единичного и мелкосерийного производства должно- учитывать требования групповой разработке. Одним из основных вопросов есть определение положения подробности при заливке.
Практически во всех случаях оно сходится с положением при формовке.
Определяя положение подробности при заливке, нужно обеспечить:
1) направленное затвердевание, разрешающее взять более плотную отливку, чем при равномерном затвердевании;
2) простоту формовки, выражающейся в применении чистой модели, мельчайшего количества стержней, размещении всей отливки в нижней полуформе;
3) размещение поверхностей, требующих механической обработки внизу либо в вертикальном положении.
Обычно при разработке разработки нереально выполнить все эти условия. Исходя из этого нужно при конструировании либо при отработке подробности на технологичность выделить самые важные требования и положить их в базу определения положения подробности при заливке.
Возможность исполнения этих требований обеспечивается унификацией технологии и типизацией конструкции. При проектировании новых отливок целесообразно максимально применять типовые элементы конструкций, а вдруг быть может, то стремиться к большому сходству их с подробностями, входящими в группы.
При ответе неспециализированной качества повышения отливки и задачи производительности требуется разработка последовательности типо-ответов, которые связаны с выбором опочной оснастки, стержневых коробок, литниковых совокупностей, моделей доходов, арматуры для стержней. Громадное значение имеет унификация марок материала, составов формовочных и стержневых смесей.
Литниковая совокупность есть очень серьёзным элементом, и ее выбор особенно действенно отражается на увеличении качества литья, сокращении расхода металла, упрощении разработки разработки. Расчет ее достаточно сложен и в большинстве случаев проводится для отливок подробностей многочисленными партиями. При групповой технологии целесообразно сделать расчет литниковой совокупности для определенной группы подробностей, приняв ее как типовую для остальных.
Одним из ответственных источников увеличения выхода годного литья помогает понижение расхода металла на прибыли. Благодаря унификации в каждом случае возможно применять прибыли рациональной оптимальных размеров и формы, и применить особые технологические способы (обогрев доходов, теплоизоляцию).
Выбор смеси для стержней и форм имеет громадное значение при проектировании групповых и типовых технологических процессов. Темперамент смеси и связанные с ним особенности разработки изготовления формы влияют на чистоту поверхности отливок, отсутствие в них трещин и песочных раковин, точность размеров. Особенного внимания требует выбор смеси для стержней как самые ответственных частей формы.
Все эти моменты должны учитываться как при разработке конструкции подробностей, так и технологического процесса.
Выбор, изготовление и проектирование литейной оснастки. Одним из главных вопросов, определяющих уровень и возможность механизации литейного производства в условиях изготовления подробностей небольшими сериями, есть использование и рациональный выбор технологической оснастки.
Создание в полной мере определенных групп отливок на базе их конструктивно-технологической общности есть базой применения и разработки стандартизованной модельно-опочной оснастки, в основном ее неформообразующих частей (опок, модельных плит, корпусов, стержневых коробок, сушильных плит и т. д.), что в условиях мелкосерийного производства получает особенное значение.
Применение таковой оснастки ведет к тому, что при освоении нового изделия нужно изготовить лишь ее формообразующие части. Это в значительной мере уменьшает сроки подготовки производства, удешевляет себестоимость литых подробностей и снабжает возможность применения машинных способов формовки.
При проведении работ по стандартизации нужно стремиться к созданию минимального, но достаточного количества разных типоразмеров оснастки, снабжающих возможность формовки разных стержней и деталей к ним.
Стандартизованная литейная оснастка отыскала широкое использование на многих фабриках и детально обрисована многими авторами.
Разглядим возможности применения стандартной оснастки при применении группового способа в условиях мелкосерийного производства.
Экономическая эффективность машинной формовки в условиях мелкосерийного производства определяется верным применением разных унифицированных конструкций переналаживаемых модельных плит, использование которых позволяет перевести на машинную формовку не только отливки, изготовляемые небольшими сериями, но и отливки единичного производства.
На данный момент в литейных цехах используются разные виды модельных плит, снабжающие закрепление и установку разных групп подробностей: координатная модельная плита; координатная плита с прижимными планками и клетью; универсальная рамка с быстросменной модельной плитой; универсальная модельная плита с крестообразными гнездами; универсальный координатный стол; универсальная подмодельная плита с гнездами для быстросменных вкладышей.
Конструкция модельных плит обязана снабжать:
1) стремительную и смену моделей и точную установку на плитах;
2) стремительную и несложную смену плит на автомобилях.
Одной из самый оправдавших себя конструкций плит, снабжающих исполнение поставленных условий, есть координатная плита.
Габаритные размеры модельных плит определяются в зависимости от размеров опок и при машинной формовке соответствуют типу формовочной автомобили.
Главной изюминкой координатных модельных плит есть наличие совокупности отверстий, просверленных по правильной координатной сетке. Ход сетки устанавливается в зависимости от размеров плиты. Громадный ход использовать не рекомендуется, гак как он затрудняет установку на плите разных элементов литниковой совокупности. Размерной базой координатной сетки являются осевые линии, проходящие через отверстия установочных штырей.
Высокая точность размещения отверстий по шагу, снабжающая совпадение координат отверстий одной плиты с соответствующими отверстиями второй, достигается при помощи сверления по кондуктору либо на координатно-расточном станке. Конструкция таковой плиты продемонстрирована на рис. 2.
В один момент с координатными плитами рекомендуется изготовлять из листовой стали шаблон плиты, по которому производится разметка отверстий в моделях.
Для самоё рационального применения координатных модельных плит нужно в первую очередь создать монтажную схему размещения групп подробностей по групповому классификатору) и выбрать рациональную литниковую совокупность, снабжающую получение качественных отливок.
Рис. 3. Шаблон
Рис. 4. Схемы монтажа моделей на координатных плитах:
1 — модели; 2 — питатели
Рис. 5. Кондуктор для сверления отверстий
Порядок подготовки модельной оснастки пребывает в следующем. Как в большинстве случаев, изготовляются разъемные модели и деревянные модели литниковой совокупности. В соответствии с монтажной схеме, одна из литниковой моделей системы и половинок детали устанавливается на разметочный шаблон плиты и закрепляется на нем струбцинами.
Через отверстия в шаблоне на обратной стороне закрепленной модели производится разметка под сверление гнезд для древесных шипов и зажимных штырей. Затем модели снимаются и просверливаются по кондуктору. Просверленные половинки моделей спариваются со вторыми половинками, и в последних просверливаются отверстия через отверстия первых половинок моделей.
По окончании сверления отверстий в каждую из половинок модели вставляют древесные калиброванные шипы, изготовленные из жёстких пород дерева. При помощи этих шипов модели устанавливаются на координатные плиты и закрепляются на них одним шурупо.
Рис. 6. Крепление модели на координатной плите
Для моделей, закрепляемых на координатных плитах, вместо древесных шипов используются калиброванные металлические штыри, каковые крепятся при помощи особой планки, врезанной в модель заподлицо с плоскостью разъема. Крепление моделей в этом случае обеспечивается особым устройством клети.
На некоторых фабриках используются координатные плиты со встроенным пневмоприводом для закрепления моделей. Таковой метод монтажа и подготовки моделей разрешает скоро и легко поменять на плите модели по окончании изготовления нужного количества форм.
Элементы крепления плиты к формовочной машине определяются в зависимости от типа стола используемых автомобилей.
Одной из рациональных конструкций плит, применяемых в условиях мелкосерийного производства, есть клишевая плита, дающая возможность в один момент формовать разные подробности. Конструкция плиты складывается из вкладных плиток и коробчатого основания с закрепленными на них моделями. При таковой конструкции модельной плиты возможно не только создавать формовку разных подробностей в один момент, но и при необходимости относительно быстро заменять одну модель второй.
Рис. 7. Координатная плита со особым устройством клети:
1 — координатная плита; 2 — клеть; 3 — зажимная планка; 4 — винт; 5 — гайка
На рис. 10 продемонстрирована подмодельная плита, отлитая из алюминиевого сплава, на рабочей поверхности которой выфрезеро-ваны три посадочных гнезда в виде креста. В зависимости от габаритных размеров и массы отливок количество гнезд на плите возможно разным.
В гнезда плиты вставляются алюминиевые кресты с закрепленными на них моделями. Кресты фиксируют модели на плите. От перемещения в вертикальной плоскости при вытяжке и набивке модели крест удерживается с одной стороны питателем, с другой — зажимом в виде узкой металлической пластины, вольно вращающейся около оси, зафиксированной па плите. Крепление моделей к кресту осуществляется винтами либо шурупами,
Рис. 8. Чертеж координатной плиты со особым устройством
Рис. 9. Односторонняя сборная клишевая плита:
1 — основание; 2, 3 — типоразмеры вкладных плиток; 4 — прижимной винт; 5 — штыри
Рис. 10. Быстросменная подмодельная плита для верхних полуформ с тремя гнездами:
1 — зажим; 2 —верхняя добрая половина модели; 3 — пи-тающе-распределительная бобышка; 4 — шлакоуловитель; 5 — шпилька под стояк
Для питания металлом на плите монтируется дроссельная литниковая совокупность, благодаря применению которой значительно уменьшается брак от шлаковых включений и газовых раковин. Самый действенно эта совокупность употребляется при заливке подробностей развесом от 1 до 25 кг. Расчет литниковой совокупности ведется по средней массе отливок, монтируемых на данной паре плит.
Модели смогут устанавливаться и сменяться на плите независимо одна от второй. При необходимости на кресте возможно закрепить пара моделей, питая их одну через другую, что возможно лишь при отливке малоответственных подробностей.
Чтобы исключить неточности при монтаже моделей на плитах, предназначенных для формовки верха либо низа, рекомендуется около соответствующих гнезд выбивать номера, а на крестах, к каким прикреплены нижние половинки моделей,— букву Н.
Рис. 11. Крепление модели к кресту:
1 — алюминиевый крест; 2 — древесная модель; 3 — шуруп; 4 — винт; 5 — замазка
Рис. 12. Дроссельная литниковая совокупность:
1 — отливка; 2 — питающая бобышка с питателем; 3 — шлакоуловитель; 4 — дроссель; д — шпилька под стояк: 6 — стояк
При групповом способе производства для того чтобы разных типоразмеров на последовательности фабрик используются переналаживаемые стержневые коробки, каковые складываются из постоянного для данного типа автомобили стандартного сменных вкладышей и металлического корпуса. В зависимости от размера партии вставки смогут быть железными либо древесными, они изготовляются из стандартных заготовок.
Размеры переналаживаемых стержневых коробок в зависимости от типа формовочной автомобили приняты от 300 X 200 X 150 До 200 X 1200X500 мм. Использование переналаживаемых стержневых коробок разрешило изготовлять до 90 % номенклатуры стержней машинным методом. Трудоемкость изготовления стержней по цеху снижена на 50%, а уровень качества стержней и от. ливок быстро повышено.
Групповым способом должны быть охвачены не только небольшие и средние подробности, но и большие отливки, поскольку для них кроме этого свойственны элементы конструктивной общности.
Не обращая внимания на то что большие отливки в основном изготовляются небольшими партиями, а время от времени и единичны, все же и в этом случае удается использовать стандартную оснастку. Это разрешает отказаться от изготовления моделей, ям, постелей методом замены их жакетами со стандартизованными поперечными сечениями трапецеидального профиля. Формы в этом случае
образуются методом сборки стержней. Протяженность форм может изменяться в достаточно широких пределах благодаря применению в жакетах переставных торцовых стенок.
Жакеты смогут выполняться железными либо из температуростойких сортов бетона, не подверженных большому термическому расширению.
Выбор оборудования. Механизация формовки не только быстро увеличивает производительность труда, но и содействует увеличению качества отливок, снабжая их изготовление с более правильными размерами, чем при ручной формовке.
Классификация отливок, использование стандартной оснастки обусловили возможность машинной формовки отливок в условиях не только крупносерийного, но и мелкосерийного а также единичного производства.
В зависимости от конструктивно-габаритных размеров и технологических особенностей отливок используются разные типы формовочных автомобилей. Встряхивающие автомобили имеют значительные недочёты — низкую производительность, громоздкость конструкций, интенсивный износ подробностей, и сильный шум при работе. На последовательности фабрик отыскал использование способ прессования форм под большим удельным давлением на пневморы-чажных и гидравлических прессах.
Исследования продемонстрировали, что для получения приемлемой плотности форм нужно удельное давление в диапазоне 1,2—2,0 МПа.
Использование автоматических линий и установок для того чтобы форм прессованием под большим давлением разрешает приобретать формы для отливок самых разных подробностей, снабжает условия для автоматизации и механизации готовления литейных форм и быстро усиливает условия труда. Как пример разглядим прессовую установку, созданную на ПО «Кировскии завод».
Рис. 13. Обычный переналаживаемый стержневой ящик
Прессовая установка П-457 предназначена для готовления литейных песчаных форм способом прессования в опоках размером 1200X600X300 мм для отливок единичного И мелкосерийного производства.
Установка складывается из пресса, двух подвижных столов, двух пневматических цилиндров для движения столов, двух бункеров, двух съемников опок, двух пневматических подъемников, рольганга безлюдных опок, рольганга готовых тележки и форм для передачи готовых форм с рольганга готовых форм на рольганги-накопители форм.
Прессовая установка трудится следующим образом. Безлюдные опоки с рольганга безлюдных опок захватываются пневматическим подъемником и устанавливаются на столы, на одном из которых смонтированы модельные агрегаты верха, а на втором — низа. Затем подвижный стол совместно с модельным агрегатом и опокой низа подается пневматическим цилиндром под бункер, где происходит наполнение опоки формовочной смесью до отметки наполнительной рамки.
После этого пневматический цилиндр подает стол с опокой под пресс. Упрочнение прессования контролируется манометром. По окончании окончания прессования опока подается на позицию протяжки, где штифтовой пневматический съемник создаёт протяжку формы. Готовая форма снимается электрическим тельфером (не продемонстрирован на рисунке), кантуется и устанавливается на рольнанг готовых форм.
В то время, в то время, когда произведится протяжка формы опоки низа, опока верха подается под бункер, заполняется смесью, перемещается под пресс, и потом осуществляется тот же технологический цикл, что прошла и опока низа. Поочередно изготовленные на прессовой установке формы низа и верха собираются на рольганге готовых форм и передаются на заливку. Управление дистанционное с двух пультов. Производительность установки для опоки с большими размерами — 40 полуформ в час.
Установку обслуживают два человека. Занимаемая площадь 9X6 м (без насосной станции). Высота установки над уровнем пола 4,5 м.
На этом же заводе создана и прессовая установка ПФ-200, предназначенная для изготовления крупногабаритных литейных форм способом прессования в опоке с габаритными размерами 2100X1500X750 мм для единичного и мелкосерийного производства чугунного литья.
практика и Теоретические разработки продемонстрировали, что использование группового способа при литье в песчаные формы в условиях мелкосерийного производства разрешает:
1) механизировать приготовление формовочной смеси, транспортировку ее к формовочным автомобилям, подачу горелой почвы к бегунам;
2) перейти от ручной формовки к машинной;
3) внедрить конвейерную щеку, применяя для транспортировки опок на заливку 33 выбивку линию приводных рольгангов либо более сложные транспортеры;
4) создавать заливку в близи от плавильных агрегатов, что упрощает транспортировку жидкого металла к формам;
5) сосредоточить выбивку в одном Lecre на выбивной решетке.
Рис. 14. Прессовая установка П-467
Все это снабжает организацию механизированных литейных цехов в условиях мелкосерийного производства.
На рис. 15 продемонстрирована схема участка сборки, выбивки и заливки форм. Сборка форм производится на рольгангах, идущих от формовочных автомобилей, на которых осуществляется формовка разных групп подробностей. Собранные формы поступают на площадки конвейера и передвигаются к месту заливки.
Залитые формы охлаждаются в охладительном тоннеле и пневматическим подъемником подаются на выбивную решетку. По окончании выбивки безлюдные опоки тем же подъемником устанавливаются на площадках конвейера и возвращаются к формовочным автомобилям.
очистки литья и Дальнейшие операции обрубки кроме этого механизированы.
Но внедрение автоматизированных процессов формовки, заливки, выбивки и очистки, стержней и изготовления смесей обусловливает необходимость исполнения последовательности непростых задач. Первая из них связана с формовкой. Одним из условий автоматизации формовки есть использование опок одного размера на одной автоматической линии, поскольку при разных размерах приходится вводить сложную переналадку.
Исходя из этого необходимо специализировать производство литья по конфигурации и массе. Использование способа групповой формовки разрешает в опоках одного размера формовать подробности широкой номенклатуры.
Вторая задача — это автоматизация заливки. Кроме того в лучших механизированных и автоматизированных литейных цехах стали и заливка чугуна производится вручную. Чтобы не останавливать опоки в момент заливки, ковш с металлом и сам заливщик перемещаются со скоростью перемещения опок, но однако заливка производится вручную.
Одним из способов ответа данной задачи есть использование способа групповой заливки. Опоки должны быть разбиты на пара групп по массе заливаемого металла, к примеру по 50, 70 и 90 кг. В соответствии с этим в подвижные ковши на весовом дозаторе наливается заданное количество металла.
На автоматической линии металл из ковша всецело выливается в опоку.
Если не удается подобрать группу отливок, суммарная масса которых соответствовала бы емкости ковша, то формуется маленькая дополнительная прибыль для избыточного металла. Данный пример иллюстрирует возможности применения группового способа при ответе таковой непростой технической задачи, как автоматизация заливки.
Рис. 15. Схема механизированного участка сборки, выбивки и заливки форм
Третья задача — автоматизация процесса- остывания форм. В большинстве случаев на конвейер для остывания ставятся все опоки, причем шходится подбирать скорость конвейера по самый медлительно остывающей подробности. К примеру, в случае если такая подробность требует на стывание 2 ч, то целый конвейер двигается с таковой скоростью, дабы любая’из опок пребывала на нем 2 ч. Это увеличивает площадь и длину конвейера, занимаемую им. Положение изменяется при применении группового способа.
В одном из цехов все подробности разбиты на восемь групп по срокам остывания — от 2 ч до 15 мин. В соответствии с этим установлено восемь конвейеров по одному для каждой группы с различной скоростью перемещения. В зависимости от группы подробностей опокам задается адрес конвейера остывания, куда они машинально транспортируются.
Такая совокупность разрешает многократно уменьшить площадь цеха и приобретать отливки, остывшие приблизительно до однообразной температуры.
При групповом способе получения отливок открылись довольно широкие возможности и для их очистки. Исполнение данной операции осуществляется разными способами — дробе- и пескоструйными аппаратами, методом обкатывания и электрогидравлическим методом. Все эти установки проектируются и используются в зависимости от конструкции отливки, ее габаритных размеров и веса, т. е. для определенной группы изделий.