Электро-химико-механическая обработка
самая современной ступенью развития химико-механического способа есть электро-химико-механическая обработка. Еще в 30-х годах было обнаружено, что производительность химико-механического способа зависит от химической природы обрабатываемого прочности и материала защитного слоя, появляющегося под действием раствора. С повышением прочности сцепления защитного слоя с главным металлом производительность понижается.
По данной причине очень активные в химическом отношении сплавы и металлы (алюминий, никель, другие сплавы и нержавеющие стали с высоким содержанием легирующих элементов) в ходе обработки в растворах электролитов легко пассивируются. Происхождение пассивной защитной пленки на поверхности обрабатываемого металла, владеющей большой прочностью сцепления, затрудняет ее удаление и благодаря этого понижается производительность.
В этих условиях нужно использовать средства, каковые не нарушали бы удаления процесса и непрерывность образования химических соединений на обрабатываемой поверхности.
Наложение электрического тока на химико-механический процесс с присоединением обрабатываемой заготовки к хорошему полюсу (аноду) разрешает решить эту задачу. Используя разные составы электролитов и изменяя режимы тока, вероятно на обрабатываемой поверхности создавать химические соединения в виде пленок прочности и различного состава.
Вероятно получение совсем непрочных соединений, легко растворимых в электролите, и, так, осуществление управления процессом обработки металлов. Химико-механический способ с наложением электрического тока сейчас подвергается изучению во многих государствах и благодаря неустановившейся технологии именуется по-различному: электро-химико-механическим, анод-но-механическим и просто электрохимическим.
Интенсивное развитие этого нового направления стимулируется все возрастающим применением в современной технике жёстких полупроводниковых материалов и сплавов, химически стойких, жаропрочных и магнитных сплавов с высоким содержанием легирующих элементов (Cr, Ni, Ti, W, Mo, Al, Si).
Легирующие элементы повышают прочность, окалиностойкость и химическую стойкость, но ухудшают обрабатываемость сплавов резанием.
Соединения Si, Al, Ni, W и Ti владеют абразивными особенностями.
Сочетание абразивных низкой теплопроводности и свойств ограничивает скорости резания до 5—8 м/мин при обработке быстрорежущим инструментом и до 15— 20 м/мин — при резании твердосплавным инструментом.
Во многих случаях не достигаются требуемая качество поверхности и точность размеров в связи с недостаточной стойкостью инструмента.
При обработке сложных профилей, к примеру, фрезерованием посредством фрез из быстрорежущей стали с подачей не более 20—30 мм/мин и глубине резания до 5 мм особенно возрастает трудоемкость процесса.
Помимо этого, при разработке автомобилей и устройств в новейших областях науки и техники появляется необходимость получения фасонных отверстий и полостей, щелей, каналов, микроскопических размеров и прорезей малых в недоступных местах.
Многие из этих работ не смогут быть осуществлены без наложения тока.
Сущность электро-химико-механической обработки
Процесс электро-химико-механической обработки, основанный на удалении и непрерывном образовании химических соединений с обрабатываемой поверхности, реализовывают следующим образом.
Металл заготовки соединяют с хорошим полюсом источника постоянного тока. Заготовка, следовательно, является анодом, а катодом — инструмент, подключенный к отрицательному полюсу источника тока.
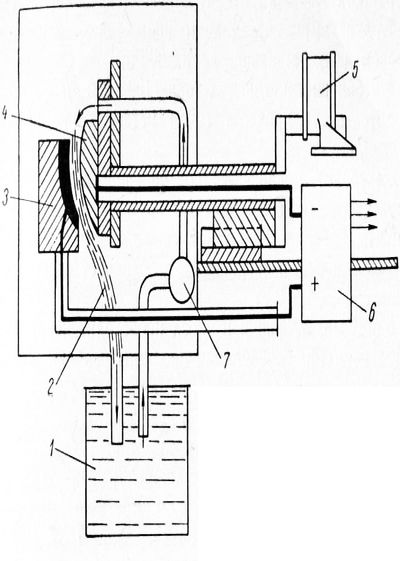
Рис. 1. Схема установки для получения фасонных полостей:
1 — бак с электролитом; 2 — поток электролита; 3 — анод (заготовка); 4 — катод (инструмент); 5—механизм автоматической подачи электрода; 6 —источник тока; 7 — насос для прокачивания электролита.
В качестве катода-инструмента может служить абразивный круг или железный брусок, профиль которого есть зеркальным отображением профиля изготовляемой подробности. В другом случай и том катод-инструмент отделен от обрабатываемой поверхности (анода) зазором. В межэлектродный зазор обильно подают раствор электролита посредством насоса.
Под действием электрического тока, проходящего через электролит, непрерывно происходят процессы электрохимического (удаления) и анодного растворения продуктов реакции. В зависимости от назначения процесса продукты реакции удаляют неоднозначным методом:
1. В процессах формообразования (получения фасонных полостей), как продемонстрировано на рис. 29, инструменту-электроду придают нужную форму. При электролизе стремительнее растворяются участки заготовки, находящиеся ближе к инструменту, и его профиль копируется на заготовке.
Полости, образующиеся в обрабатываемой заготовке, воспроизводят форму инструмента-катода с точностью 0,1—0,15 мм. В некоторых случаях точность возможно повышена до 0,03—0,04 мм. Обрабатываемая поверхность свободна от заусенцев. Источником питания помогают выпрямители постоянного тока, доходящие в современных установках до 100 000 а.
При громадных плотностях тока (150—250 а/см2) производительность процесса (съем металла) образовывает 1000 см3/час.
Электролит, подаваемый под громадным давлением в межэлектродный зазор, стремительным потоком уносит в бак продукты реакции. При таковой схеме процесса инструмент-электрод не изнашивается, а сохраняет вес и свою форму.
Процесс уноса и растворения происходит непрерывно лишь в том случае, если продукты реакции, приобретаемые на поверхности анода, не образуют прочной защитной пленки, а растворимы в электролите.
Анодное растворение сопровождается выделением газов на электродах. На аноде анализом выявляют кислородные соединения. В зависимости от состава электролита это смогут быть окислы азота (NO, N02), СО, С02 и 02. На катоде выделяется эквивалентное количество водорода. Как показывают испытания, с повышением концентрации электролита, в большинстве случаев, улучшается газовыделение.
Выделяющиеся газы, вытесняя электролит из межэлектродного зазора, воздействуют на качество и производительность процесса приобретаемой поверхности.
Электро-химико-механический процесс по большей части подчиняется закону Фарадея, т. е. количество растворенного металла пропорционально количеству прошедшего через электролит электричества, либо скорость электрохимического растворения металла на аноде пропорциональна анодной плотности тока (а/см2).
2. В процессах правильного шлифования, заточки и доводки (рис. 2) применяют абразивный токопроводный круг. Выступающие из токопроводной (медной либо графитовой) связки корундовые либо алмазные зерна размером 0,02—0,04 мм образуют щель между заготовкой и связкой круга, в которую поступает электролит. Используемые в этом случае режимы и электролиты тока создают пассивную предохранительную пленку, которая мешает процессу анодного растворения.
Удаление пленки происходит механическим методом зернами абразивного круга.
Рис. 2. Схема установки для шлифования:
1 — бак с электролитом; 2 — подвод электролита; 3 — электропроводный абразивный круг (катод); 4 —шпиндель; 5—источник тока; б —стол с заготовкой.
Процесс электрохимического растворения облегчает съем металла, и благодаря этого в 2 раза увеличивается производительность с одновременным уменьшением износа инструмента.
Преимущества и недочёты электро-химико-механической обработки
Наиболее значимое преимущество электро-химико-механической обработки — высокая производительность. Современные установки разрешают достигнуть съема металла 200 мм3/мин, снабжая наряду с этим 7—8-й классы шероховатости. Высокая производительность сочетается с применением способа для обработки любых сплавов и металлов, причем не зависит от вязкости и твёрдости обрабатываемого материала.
При данном ходе отсутствуют какие-либо обстоятельства, каковые смогут привести к износу инструмента. И вправду, при этих условиях износ круга ничтожно мелок и определяется трением о мягкую анодную пленку либо вовсе не отмечается износа при удаления продуктов химической реакции потоком электролита.
При электро-химико-механической обработке нет дуговых ‘либо искровых разрядов, а, следовательно, исключаются образование кратеров и плавление металла на электродах. В качестве жидкой среды используют электролиты в виде не сильный растворов солей, а не жидкое стекло либо керосин (дугогасящие и нейтральные жидкости), как при электромеханическом и электроискровом методах.
Все это выгодно отличает его от химических и электрофизических способов.
Затраты на изготовление инструмента в десятки раз меньше, чем на инструмент для механической обработки.
Инструмент изготовляют из материалов, не требующих термической обработки. К нему не предъявляют требований по структуре и твёрдости.
Вероятно использование нескольких инструментов-электродов для одновременного получения нескольких полостей, причем инструмент применяют многократно.
Электро-химико-механическая обработка технологически подготовлена к автоматизации: ненужными являются сложные и громоздкие вентиляционные устройства, по причине того, что в качестве электролитов используют безвредные растворы.
Наровне с преимуществами электро-химико-механиче-ской обработке характерны и значительные недочёты.
Необходимость применения громадных плотностей тока требует замечательных источников постоянного тока (500— 100 000 а). Требуются громадные количества электролита. Практически 75%’ площади цеха занимают бак и выпрямители для электролита.
Площадь, занимаемая современными установками, доходит до 20 ж2.
Появляются проблемы с подачей электролита в межэлектродный зазор и обеспечением равномерного протока электролита по всему пространству криволинейного зазора.
Непросто решается задача подвижного электрода, машинально сохраняющего постоянную величину зазора.
Трудности согласования формы инструмента с требуемой формой детали и потока и распределения давления электролитического раствора в зазорах довольно часто не разрешают обеспечить однообразную плотность тока на всех участках поверхности. Это ведет к неравномерному съему металла, чрезмерному нагреву электролита, растравливанию отдельных участков поверхности и не разрешает во многих случаях использовать электро-химико-ме-ханическую обработку.
Условия процесса
На качество и производительность процесса приобретаемой поверхности воздействуют состав электролита, плотность тока, скорость перемещения инструмента-электрода, совокупность подачи электролита, величина межэлектродного другие условия и зазора.
Электролиты. Для электро-химико-механической обработки предложено много электролитов.
Пригодность электролита определяется в первую очередь его электропроводимостью: чем она больше, тем больше кроме этого допустимая плотность тока и, следовательно, выше производительность процесса. Электропроводимость, со своей стороны, зависит от температуры и концентрации электролита.
Не считая электропроводимости, при выборе электролита нужно учитывать вредное воздействие его на организм персонала , коррозийное воздействие электролита, вероятную продолжительность применения, другие условия и стоимость.
Из предложенных электролитов на данный момент в производстве используют составы на базе растворов хлористого натрия, фосфорнокислого натрия, натрия и азотнокислого калия, сернистого натрия, углекислого аммония и буры.
Применением в качестве электролитов азотнокислого и азотистокислого натрия достигается громаднейшая производительность процесса. Но эти соли при повышенных плотностях тока растравливают обрабатываемую и смежную с ней поверхности.
Рис. 3. Удельная проводимость электролита при разной концентрации и температуре:
1 — 5%; 2 – 10%; 3 – 15%; 4-30%.
Использование хлористых солей натрия и аммония и калия и сернокислых солей натрия снижает производительность процесса. То же отмечается и при применении растворов буры.
При обработке жёстких сплавов электролитами образуются нерастворимые соединения, загрязняющие электролит. Исходя из этого в состав электролитов вводят фтористый натрий, что предотвращает образование нерастворимых соединений.
Хлористые и сернокислые электролиты корродируют детали станка, соприкасающиеся с электролитом. С целью этого в состав электролитов вводят ингибитор. Не снижая производительности процесса, он сокращает коррозийную активность электролита.
Не обращая внимания на пара пониженную производительность, в особенности заманчивым есть использование раствора поваренной соли — самого недорогого и дешёвого электролита. Раствор поваренной соли разрешает действующий при плотности тока 200 а/см2.
Гидрат закиси железа, окисляясь на воздухе, переходит в гидрат окиси железа и выпадает в осадок в виде шлама. Часть шлама может попасть на поверхность катода и загрязнить его. В этом случае приходится чистить катод крацовочной щеткой.
При шлифовании жёстких сплавов в шламе выявляют выкрошенные частицы карбидов и абразива вольфрама, каковые кроме этого загрязняют электролит.
Анодное растворение сопровождается обильным выделением газов на электродах. На аноде анализом обнаруживаются СО, 02, С02 и окислы азота (NO; N02). На катоде выделяется эквивалентное количество водорода.
Как показывают испытания, с повышением концентрации электролита начиная с 6% (NaN02 + NaN03) улучшается газовыделение. Выделяющиеся газы воздействуют на проводимость раствора, вытесняют электролит из межэлектродного зазора и, в конечном итоге, ограничивают производительность процесса.
Чрезмерный нагрев электролита (больше 40 °С) в ходе электролиза ведет к разъеданию поверхности. Помимо этого, при кипении электролита он начинает выкристаллизовываться, что скоро снижает производительность процесса.
Плотность тока. Но повышать беспредельно плотность тока запрещено по двум обстоятельствам.
Прямое возрастание плотности тока благодаря сильного окисления поверхности анода уже скоро ведет к его пассивированию. Образование пассивной электроизоляционной не хорошо растворимой пленки на аноде существенно тормозит процесс анодного растворения, а при чрезмерном накоплении продуктов реакции прекращаетего. Образование пассивной пленки не разрешает повысить плотность тока, сокращает выход по току и быстро снижает эффективность.
Помимо этого, направляться не забывать, что на нагрев электролита расходуется 80— 90% всей подведенной электроэнергии. Учитывая теплопроводность электролитов (приблизительно 0,9 кал/см – час • град), высокая плотность тока требует интенсивного перемещения электролита в обрабатываемой полости, в другом случае наступает кипение электролита.
Плотность тока зависит и от природы обрабатываемого материала. Ниже приведены допустимые плотности тока для некоторых металлов:
Плотность тока воздействует не только на производительность, но и на шероховатость поверхности. Из рис. 5 направляться, что в области повышенных плотностей тока шероховатость фактически не зависит от плотности тока.
Потому, что производительность находится в прямой зависимости от плотности тока, это разрешает в значительной мере преодолеть несоответствие, характерное механической и электрофизической обработке, в которых чем больше съем металла, тем больше шероховатость.
Вместе с тем благодаря кавитации либо разделения потока на обрабатываемой поверхности появляются бугры и радиальные полосы. Согласно данным японских ученых, введение в поток углекислого газа для смещения прокачиваемого электролита ликвидирует данный недочёт.
Рис. 4. Зависимость производительности от плотности тока:
1— при упрочнении 12 кг/е-и2; 2 — при упрочнении 6 кг/см2.
Напряжение. Повышение напряжения, со своей стороны, разрешает повысить плотность тока. Но эта зависимость скоро нарушается.
Уже при напряжении приблизительно 12 в появляются искровые и дуговые разряды.
Напряжение между электродами должно быть больше потенциала поляризации анода. Фактически напряжение должно быть в пределах 8—10 в.
Скорость перемещения инструмента-катода
При вращающемся инструменте-катоде (абразивный электропроводный круг) с повышением скорости стремительнее удаляются продукты реакции с обрабатываемой поверхности и постоянно совершенствуются условия для протока электролита. Исходя из этого, как направляться из рис. 7, плотность тока, а с ней и производительность процесса сперва возрастают, после этого при плотности тока около 80— 100 а/см2 производительность достигает собственного громаднейшего значения, после этого остается постоянной, а за пределом скорости 25—30 м/сек пара понижается.
Учитывая огромные скорости химической реакции, было бы очень действенно расширить скорость вращения шлифовальника. Для осуществления процесса с громаднейшей производительностью следовало бы максимально приблизить скорость механического удаления к скорости химической реакции, дабы вовремя освобождать обрабатываемую поверхность от продуктов реакции и подготовлять ее к новому химическому действию. Но фактически этому мешают центробежные силы, растущие пропорционально квадрату скорости вращения шлифовальника, каковые не разрешают электролиту удерживаться на поверхности.
Рис. 5. Влияние плотности тока на шероховатость поверхности.
Рис. 6. Зависимость между скоростью перемещения вращающегося инструмента-катода и плотностью тока при давлениях:
1 — 9 кг/см2; 2 — 6 кг/см3 — 3 кг 1см2.
При поступательном перемещении инструмента-катода плотность тока, а следовательно, производительность определяются скоростью подачи электрода, снабжающего оптимальный межэлектродный зазор.
Межэлектродный зазор.
Повышение зазора между катодом и анодом сокращает сопротивление электролита, что ведет к понижению плотности тока и соответственно производительности. Исходя из этого нужно всегда сохранять заданную величину зазора, для чего достаточно поддерживать напряжения и величин оптимальные значения тока между электродами. самая прогрессивной есть электронная следящая совокупность с автоматической обратной связью, которая разрешает непрерывно осуществлять контроль подачу электродов и снабжать нужный зазор.
Давление. Из рис. 7 направляться, что с повышением удельного давления инструмента производительность процесса возрастает. Происходит это благодаря уменьшения межэлектродного зазора с повышением давления. Но при давлении 15—18 кг/см2 межэлектродный зазор делается так малым, что смогут появиться искровые разряды с образованием электроэрозионных лунок на инструменте и заготовке.
Это ведет к стремительному износу инструмента. Оптимальное давление должно составлять 10—12 кг/см2.
Подача электролита. Совокупность подачи электролита в межэлектродный зазор обязана осуществляться так, дабы вся обрабатываемая поверхность всецело заливалась электролитом без происхождения мертвых завихрений и зон.
Наличие мертвых территорий ведет к разъеданию поверхности, а завихрения уменьшают скорость протока электролита, снижая производительность. Устранить завихрение возможно понижением давления поступающего электролита или закруглением углов у инструмента. Помимо этого, при конструировании инструмента направляться предусматривать в нем отверстия и шлицевые прорези, снабжающие лучшие условия для подачи электролита и высокую скорость потока.
Особенное внимание направляться обратить на подачу электролита у самого входа в рабочую территорию. В случае если подать электролит на поверхность вращающегося катода на некоем расстоянии от рабочей территории, то целый электролит будет скинут с катода под действием центробежной силы. При невращающемся катоде при удаления продуктов износа потоком электролита пара постоянно совершенствуются условия подачи.
Но в случае если очертания зазора смогут привести к кавитации, то это срочно уменьшит площадь соприкосновения электролита с поверхностью анода, увеличит омическое сопротивление и уменьшит предельную плотность тока. Исходя из этого при обработке в протоке электролита нужно избегать кавитации, что возможно достигнуто при расстоянии между анодом и катодом не более 0,5 мм. Оптимальная ширина зазора — 0,3 мм.
Рис. 7. Зависимость между плотностью тока и зазором при скоростях подачи электролита:
1 — 0,5 л\мин\ 2 — 5 л\мин.
Станки. На данный момент в СССР и за границей созданы уникальные модели станков для обработки электролитами. Громаднейший интерес воображают полуавтоматы АГЭ-2 и ЭХО-1. Полуавтомат модели АГЭ-2 рекомендован для электрохимической обработки профиля пера лопаток турбин и
компрессоров. Процесс двусторонней обработки подробности (анода) осуществляется при синхронном сближении двух электродов-инструментов (катодов) за одну технологическую операцию, наряду с этим на сторонах подробности происходит негативное отображение электродов и образуется необходимый профиль. Сближение электродов длится до получения заданных размеров профиля.
Контроль за подачей электродов осуществляется электронной следящей совокупностью. Момент окончания обработки подробности (достижение заданных размеров) определяется особым датчиком. В один момент заканчивается подача электродов (с них снимается рабочее напряжение).
Износа электрода-инструмента не происходит. В качестве электролита используется 7—10%-ный раствор поваренной соли в воде.
Внедрение в производство только одного полуавтомата АГЭ-2 разрешило снизить трудоемкость обработки набора в 6 раз, высвободить 13 металлорежущих станков и снизить электроэнергии и расход инструмента.
На одном из фирм Москвы создан полуавтомат ЭХО-1. Электроды-инструменты выполнены из нержавеющей стали, рабочая поверхность их есть обратной копией спинки и корыта изготовляемой турбинной лопатки. Полуавтомат ЭХО-1 складывается из фактически станка, источника питания, ванны для электролита, центробежного насоса для центрифуги и нагнетания электролита.
На станке ЭХО-1 применена автоматическая следящая совокупность, разрешающая осуществлять процесс размерной обработки с постоянным минимальным межэлектродным зазором, что снабжает точность и высокую производительность. Для следящей совокупности используется автоматическая обратная сообщение. Для сигнала обратной связи применяют поляризацию.
Рис. 8. Влияние давления электрода на производительность процесса
При внедрении электрохимической обработки в 4 раза возрастает производительность труда (если сравнивать с механическом методом) и уменьшается цикл обработки, в 50 раз понижаются затраты на инструмент, и уменьшается количество потребного оборудования.
Создана электрохимическая установка для снятия заусенцев в подробностях топливной аппаратуры (трубопроводы, корпуса). С ее помощью возможно создавать многопозиционную одновременную обработку подробностей либо многих отверстий в одной подробности. Использование ее усиливает условия труда, механизирует ручной труд и повышает уровень качества изделий. Производительность—15 подробностей в час.
Установка внедрена на последовательности машиностроительных фабрик. Все станки демонстрируются на Выставке достижений народного хозяйства СССР.
Сконструирован кроме этого станок для электро-химико-механического плоского шлифования с применением алмазных кругов (модель 2-ПЭШ). Он рекомендован для шлифования твердосплавных подробностей торцом токо-проводящего алмазного круга. Головка станка имеет вертикальную ручную подачу, перемещение которой контролируется нониусным устройством.
Рабочий стол приводится в перемещение гидравлической совокупностью (продольная подача). Электролит поступает через шпиндель головки непрерывно. Источником постоянного тока помогает выпрямитель напряжением 6 в при токе до 2000 а.
Согласно данным В. Ю. Веромана, данный станок в 8— 10 раз повышает производительность шлифования алмазным кругом и во столько же раз сокращает износ алмазного круга.
В станках для обработки электролитами используют стандартные комплектующие изделия, производимые отечественной индустрией:
1. Полупроводниковые источники постоянного тока моделей ИПП-3000/12 и ИПП-5000/12 с номинальным рабочим током на 3000 и 5000 а и напряжением 12 в.
2. Насосы центробежные для нагнетания электролита модели ЗМК-6 производительностью 40—70 м3]час при дардеции 6 атм. Мощность электродвигателя 20 кет. Не считая центробежного насоса используются винтовые и центробежно-вихревые насосы (модель МС).
3. Центрифуги отстойные периодического действия моделей ОТВ и ОТН для очистки электролита от шлама (продуктов электрохимического растворения). Используются кроме этого центрифуги, непрерывно машинально очищающие электролит от шлама.
Из зарубежных моделей воображает интерес большой станок, созданный компанией «Цинциннати». На нем смогут обрабатываться подробности размерами до 900 X 900 X 900 мм.
Станок рекомендован для обработки особых материалов, каковые не смогут быть обработаны иными способами. Согласно данным компании, он снабжает обработку отверстий с точностью до ± 0,04 мм, наряду с этим поверхности свободны от напряжений и заусенцев. Станок имеет три рабочие головки с дистанционным направлением. Скорость их подачи изменяется бесступенчатым регулированием от 0,5 до 15 мм!мин на длине хода 560 мм.
Привод головок осуществляется от гидромотора при помощи шариковых ходовых винтов по роликовым направляющим. Каретки головок имеют вертикальное перемещение (по колонне) 700 мм и горизонтальное (по траверсе) 900 мм. Подробность в камеры возможно перемещена на расстояние 610 мм и развёрнута на поворотном столе на угол 36°.
Для исполнения экспериментальных работ камера имеет 9 патрубков для вводов и 40 электролита для электрических цепей.
Для предотвращения коррозии все подробности и узлы, соприкасающиеся с электролитом, выполнены из коррозийно стойкого материала. Направляющие покрыты защитными чехлами. Для наблюдения за ходом процесса в камере имеются 3 окна и внутреннее освещение.
Станок занимает площадь 46 м2, добрая половина которой занята совокупностью фильтрации и подачи электролита.
Не считая указанного станка, компания производит серию станков для электрохимической обработки с величиной рабочего тока от 1000 до 10 000 а. Электронная совокупность управления сигнализирует на основной пульт о положении электродов и может осуществлять их отвод при достижении заданной позиции. Источник питания постоянным током снабжает силу тока в 10 000 а. Электролит подается в зону обработки под давлением 24 атм из бака емкостью около 4000 л. Расход электролита образовывает 567 л/мин. Рабочая территория станка заключена в закрытую камеру с целью предотвращения разбрызгивания.
Не обращая внимания на то что остается еще большое количество нерешенных вопросов, кое-какие разновидности электро-химико-механической обработки внедряются в производство.
На данный момент на последовательности фабрик реализовывают:
1) шлифование и доводку твердосплавных фильер;
2) профилирование стружкозавивательных канавок дисковых и призматических резцов;
3) калибровку шлицевых отверстий в подробностях, закаленных до твердости RC = 62—63;
4) шлифование и доводку измерительных инструментов, оснащенных жёстким сплавом (скобы, ровные круглые калибры);
5) точение кольцевых канавок в подробностях топливной аппаратуры;
6) отделку подробностей из высоконикелевых сплавов;
7) полирование страниц нержавеющей стали;
8) хонингование отверстий;
9) доводку и заточку твердосплавного режущего инструмента (многолезвийного);
10) снятие заусенцев с шестерен.