Фанерование
Фанерованием именуется оклеивание лицевых поверхностей столярных изделий, изготовленных из древесины несложных пород, узкими страницами древесины полезных пород, отличающихся цветом и красивой текстурой. Такие узкие страницы в виде облицовочной фанеры (строганой, пиленой, лущеной) производят из дуба, ореха, бука, карельской березы, красного, других пород и лимонного дерева, и из наплывов и капов. Столярные изделия, изготовленные полностью из древесины полезных пород, стоят дорого, да к тому же древесины полезных пород мало.
Древесина большинства обширно распространенных мягких пород — сосны, ели, осины, ольхи и др. — не имеет прекрасной текстуры, но отличается малым весом, легко обрабатывается, владеет достаточной прочностью. Помимо этого, она дешевле, чем древесина пород жёстких, в особенности полезных. Фанерованные изделия прочнее, чем нефанерованные: они (особенно щиты) меньше коробятся и растрескиваются.
Если сравнивать с изделиями из древесины жёстких пород они легче, а исходя из этого эргономичнее для применения. Фанерование существенно облегчает подбор древесины по цвету и текстуре при изготовлении столярных изделий и высококачественной мебели.
Фанерование не редкость одностороннее и двухстороннее, однослойное и двухслойное.
Одностороннее фанерование возможно лишь для брусков, ширина которых не превышает их двойной толщины. В таких брусках в случае если и отмечается поперечное коробление при сильном трансформации влажности, то оно так незначительно, что не отражается на качестве изделия.
При одностороннем фанеровании фанеру наклеивают волокнами параллельно волокнам основания.
Двухстороннее фанерование лучше, поскольку в один момент оклеиваются обе стороны изделия и их усадка при высыхании по окончании оклеивания однообразна, коробления не происходит. Двухстороннее однослойное фанерование производится в обязательном порядке в один момент с обеих сторон.
Двухстороннее двухслойное фанерование есть наилучшим. Первый слой облицовочной фанеры либо шпона располагают волокнами перпендикулярно к волокнам подробности, второй — перпендикулярно к волокнам первого слоя, отчего получается переклеенный щит в пять слоев с взаимно перпендикулярным размещением волокон. Он отличается большой прочностью, прекрасно противостоит растрескиванию и короблению.
Для первого слоя лучше использовать лущеный либо строганый шпон из древесины лиственных пород (березы, ольхи, липы), так как они владеют равномерной и большой плотностью. Щиты, филенки, коробок и бруски рамок, ширина которых превышает толщину более чем вдвое, необходимо фанеровать с двух сторон. Двойное фанерование направляться вести в два приема: сперва с обеих сторон базой — шпоном и после этого лишь, по окончании выдерживания и просушки, облицовочным слоем.
Лицевые кромки коробок, щитов и рамок направляться фанеровать либо обкладывать массивом той же породы, что и облицовочная фанера. В некоторых случаях фанеру наклеивают в один момент по два слоя с каждой стороны.
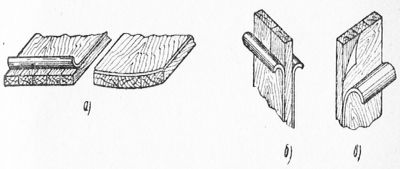
Рис. 1. Виды фанерования:
а — однослойное одностороннее, б — однослойное двухстороннее, в — двухслойное
Внутренние нелицевые стороны подробности возможно оклеивать фанерой недорогих пород, а лицевые — фанерой более полезных пород. Фанеровать возможно как отдельные подробности, так и целые изделия либо его узлы. Щиты принято фанеровать собранные, а рамки — в подробностях.
При сборке фанерованных подробностей требуется высокая точность их обработки, поскольку провесы тут недопустимы, по причине того, что при толщине фанеры 0,5—1 мм зачистка провеса может привести к срезке наклеенной фанеры. Но избежать провесов большей частью практически нереально и исходя из этого в конструкции изделия в том месте, где они смогут появиться, предусматривают платики.
Лицевые кромки коробок, щитов и рамок нужно фанеровать либо обкладывать массивом той же породы, что и облицовочная фанера. Допускается использовать массив второй породы, в случае если ее текстура и цвет соответствуют облицовочной фанере.
Частенько брусковые подробности нужно облицовывать с трех либо четырех сторон. Тогда на широкие стороны наклеивают фанеру, а на узкие кромки — фанеру либо обкладку из массива. На данный момент при массовом изготовлении отличной мебели, отличающейся простотой форм, красота внешнего вида ее создается, в основном, умелым применением декоративных изюминок древесины, которой фанеруют изделие.
Подборка фанеры требует вкуса и навыка, поскольку необходимо мочь создавать прекрасные сочетания естественного рисунка древесины либо составлять методом подбора неестественный рисунок.
Процесс фанерования складывается из подготовки фанеруемой поверхности, ее наклеивания и подготовки фанеры.
Подготовка фанеруемой поверхности
Подготовка фанеруемой поверхности (базы), особенно лицевых сторон, должна быть очень тщательной, дабы поверхность была совсем ровной и ровной. При наличии кроме того незначительной неровности на фанеруемой поверхности уровень качества прозрачной отделки изделия, в особенности полированного, будет снижено. Исходя из этого волны, оставшиеся по окончании строгания детали на станках, направляться удалить шлифованием на шлифовальных станках либо цинубелем.
Незначительные вмятины, вырывы, отщепы и трещины, оставшиеся по окончании выравнивания поверхности, зашпаклевывают клеевой шпаклевкой, приготовленной из толченого угля либо мела и клея. Клей для шпаклевки берут тот же, которым будут наклеивать фанеру. В шпаклевку на карбомидном клею мел класть не рекомендуется, поскольку под действием мела карбомидный клей теряет клеящую свойство. Зашпаклеванные места по окончании затвердевания шпаклевки направляться пронинубить.
Ручное шпаклевание — трудоемкий процесс.
Рис. 2. Недостатки фанерования, появляющиеся в следствии небрежной подготовки базы:
а — воздушный пузырь «чиж», образующийся в месте, где имеется вмятина либо иное углубление, б — выпучивание фанеры сучком при усыхании базы благодаря неодинаковой усушки древесины в различных направлениях, в — проседание фанеры на сучке при разбухании подробности, г — проседание фанеры благодаря усадки клея
Шпаклевать возможно способом воздушного распыления. Для нанесения шпаклевки способом воздушного распыления рекомендован пистолет-распылитель С-592, выпущенный Вильнюсским заводом покрасочных аппаратов. Он складывается из корпуса с ручкой, головки, сопла со штуцером, иглы, курка и двух ниппелей для материального и воздушного шлангов. Шпаклевка подается из красконагнетательного бака через канал и ниппель иглы в сопло.
При помощи сжатого воздуха шпаклевка в головке раздробляется, перемешивается с ним, и масса наносится на обрабатываемую поверхность. Производительность инструмента 75 м2/час, вес распылителя 0,7 кг.
Имеющиеся на фанеруемой поверхности дефектные места в виде сучков, глубоких задиров, серниц заделывают пробками либо вставками. Сучки, выходящие на поверхность торцов, мешают приклейке фанеры и сами не хорошо ее держат, а при сушке они выступают на поверхность и поднимают фанеру. Сучки вырезают либо высверливают и заделывают вставками из древесины в виде треугольников и ромбиков.
Направление волокон вставок должно совпадать с направлением волокон базы.
Торцы фанеруются весьма не хорошо. Исходя из этого все торцовые поверхности рекомендуется заделывать долевыми брусками на клею. Заделку торцов и полуторцов таким методом направляться создавать в соответствии с вязкой деталей и конструкцией изделия.
Связанные шиповым соединением углы коробки срезают впо-луторец и наклеивают на них долевые бруски трехгранного сечения либо планки со скошенными кромками. Торцы щитовых столярной и заготовок плиты заделывают кроме этого долевыми наклейками. Стыки брусков разных соединений заделывают перекрывающими все шиповое соединение косынками либо отдельными, имеющими закругленное сечение наклейками, и треугольником, суживающимся в сторону внутренних кромок рамки.
Дабы устранить необходимость делать наклейки, используют особенной формы шиповое соединение, при котором место стыка смещено.
В случае если узкая строганая фанера полезных пород (0,4—0,7 мм) Имеет громадную свилеватость либо очень сильно развитые сердцевинные лучи, и большие сосуды, то ее рекомендуется наклеивать по марле. При однослойном фанеровании марлю накладывают с клеем на базу, а при двухслойном — на первый слой фанеры (шпона).
Рис. 3. Методы заделки торцов и стыков перед фанерованием:
а — трехгранным бруском, б —планками со скошенными кромками, в — долевыми наклейками, г — косынкой, д — вставками
Подготовка фанеры
Подготовка содержится в сортировке и раскрое фанеры, фуговании ее кромок, подборе фанеры в страницы и стяжке (скреплении) страниц.
раскрой и Сортировка фанеры. Поступает облицовочная фанера на деревообрабатывающие фирмы пачками, упакованными в пакеты. Пакет фанеры, взятой из одного кряжа и уложенной без нарушения порядка размещения древесины в стволе, именуется кнолем. В пакет укладывают 10—20 пачек. Любая пачка содержит 10—20 страниц. При верной укладке страниц фанеры на заводе пачки имеют однообразный рисунок. Перед раскроем фанеры пачки подбирают по внешнему виду первого страницы.
Для фанерования широких поверхностей щитов отбирают более широкие пачки высокого качества, для фанерования узких брусков либо кромок берут пачки меньшей ширины и низкого качества.
Рис. 4. Шиповое соединение со смещенным стыком
Размечают фанеру по длине в соответствии с размерами предназначенной для фанерования подробности, прибавляя припуск 30 мм на обе стороны. Раскрой фанеры по длине создают в пачках на круглопильном станке с горизонтальным перемещением пильного диска. Раскроенные по длине страницы фанеры сортируют, удаляя заболонь, недо-пускаемые техническими условиями сучки и другие пороки.
Вырезку страниц по ширине, срезку рваных кромок, заболони и удаление недостатков делают в пачках фанеры на круглопиль-ных станках для продольной распиловки.
На фирмах, где фанерование производится редко либо в маленьких размерах, фанеру возможно раскраивать в маленьких пачках мелкозубыми лучковыми пилами, ножовками, а в отдельных местах — фанерной пилкой либо ножом по линейке.
Фугование кромок фанеры. Для получения широких страниц (рубах) из узких полос фанеры подобранные полосы соединяют, наряду с этим кромки их профуговывают.
На мебельных фабриках Фугование кромок строганой (ножевой) фанеры создают на особом кромкофуговальном станке. На рабочий стол станка укладывают пачку Фанеры толщиной до 90 мм, 21* кромки которой выравнены с одной стороны, и особым прижимным устройством прижимают к столу. По направляющим станины, параллельно кромке уложенной пачки фанеры, движется электрифицированный суппорт с вертикальной фрезой и мелкозубой пилой.
в первых рядах расположенная выпивала совсем подравнивает кромки, срезая излишек фанеры, а фреза отфуговывает кромки для ребрового склеивания. Завершив фугование одной стороны, пачку фанеры вынимают, сглаживают кромки иначе и фугуют вторую сторону. При маленьком количестве работ кромки фанеры прифуговывают на фуговальных либо фрезерных станках в приспособлениях и специальных шаблонах.
На фрезерном станке уровень качества фугования выше, чем на фуговальном, поскольку на фрезере шпиндель делает большее число оборотов.
Рис. 5. Фугование кромок фанеры:
а — фугование кромок на кромкофуговальном станке, б — фугование вручную на донде, в — фугование вручную на верстаке
На передовых фирмах кромки строганой фанеры фугуют не строганием, а опиливанием строгальными пилами либо рубкой гильотинными ножницами, что дает большую экономию времени.
В маленьких мастерских при отсутствии оборудования кромки фанеры фугуют ручным фуганком на донце либо в струбцинах на верстаке. К донцу пачку прижимают рукой при помощи планки. Точность прифуговки фанеры контролируют так. Фанерные полосы укладывают прифугованными кромками друг к другу на плоском совершенно верно выверенном щите. Между ними не должно быть никакого просвета.
Применение для прифуговывания строганой фанеры простых бумагорезательных автомобилей дает высокую точность.
Подбор фанеры. Полученные по окончании раскроя страницы фанеры редко соответствуют размерам громадных фанеруемых поверхностей. Исходя из этого фанеру, в большинстве случаев, необходимо соединять в более большие страницы. Фанеру необходимо подбирать по цвету, слою и рисунку (текстуре) применительно к определенному изделию, с учетом назначения и размеров фанеруемых подробностей.
Подбор нужно создавать так, дабы лист получался однотипным, с симметричной текстурой, без заметного выделения отдельных полос.
Для фанерования узких подробностей берут мелкослойную (радиальную) фанеру, а для широких щитов — широкослойную (тан-гентальную) фанеру. При подборе направляться кроме этого учитывать требования к парным частям мебели, так, к примеру, дверки платяного шкафа должны оклеиваться страницами фанеры с однообразным рисунком.
Применяя особенности текстуры древесины, возможно взять прекрасный рисунок. Так, подбором фанеры с прифуговкой полос под различными углами к направлению волокон получаются, различные орнаменты. По характеру рисунка различают следующие комплекты фанеры: в рост, «в елку», «в крейцфугу» (в уголок), «в конверт», «в шашку», «в полуелку», с фризом.
Время от времени комплект создают из полос разных полезных пород, приобретая шахматное размещение квадратов, ромбов, конусные и волнистые полосы.
Стяжкой фанеры (ребросклейкой) именуется соединение заблаговременно подобранных полос фанеры в страницы. Стяжку создают вручную либо на особом станке. Ручная стяжка весьма трудоемкая и продолжительная операция, ее делают на столе с чисто отфугованной поверхностью.
Подобранные полосы фанеры укладываются лицевыми сторонами кверху, кромками прочно прижимают одну к второй и стягивают поперечными полосами гуммированной ленты. Время от времени полосы соединяют планками с наклейкой на стык гуммированной бумажной ленты шириной 25 мм, предварительно увлажненной водой при помощи губки. Наклеенную ленту приглаживают древесными брусками-гладилками.
Для предупреждения повреждений торцов собранного страницы рекомендуется наклеивать на них бумажную полосу во всю их ширину.
Ленту потом счищают шкуркой и циклей, время от времени ее смывают либо удаляют шлифованием на шлифовальных станках.
Вместо гуммированной ленты наклеивают и обычную узкую бумагу либо марлю шириной 2—2,5 см, причем клеем смазывают лишь бумагу либо марлю, а не фанеру. По окончании стяжки лист фанеры выдерживают планками в течение 15—20 мин. После этого высвобожденный от планок лист с опаской откладывают к готовым страницам.
Переносить маленькие страницы склеенной фанеры направляться одной рукой за продольную кромку, а громадные страницы — обеими руками за обе продольные кромки. Запрещено давать странице очень сильно прогибаться по ширине, поскольку от этого может случиться излом фанеры на протяжении волокон.
Рис. 6. Методы комплекта облицовочной фанеры:
а — в рост, б — в елку, в — в крейцфугу, г — в .конверт, д — в шашку, е — в полуелку, ж — с фризом
Стяжку фанеры комфортно делать на особом трехстороннем вращающемся столе. Все три его стороны по размерам и устройству однообразны. На нем стягиваемая фанера укрепляется пружинными планками, один финиш которых заводится в борт стола, второй—под мобильные крюки, засунутые в продольные прорези стола.
Собрав лист на одной из сторон стола, находящейся в горизонтальном положении, ее поворачивают около продольной оси стола на 120° и начинают собирать очередной лист фанеры’ на второй горизонтально расположенной стороне, а после этого методом поворота стола третьей стороной собирают еще один лист фанеры.
Рис. 7. Стяжка фанеры:
а — на прижимных планках, б — на трехстороннем вращающемся столе
Собрав третий лист, поворачивают стол первой стороной; к этому времени полосы бумаги на первом странице уже успевают приклеиться и просохнуть. Первый собранный лист снимают, укладывают в стопку, а на освободившейся стороне стола подбирают новый лист. Так, не тратится время на ожидание просушки клея.
Стяжка наборной фанеры производится равно как и стяжка страниц, но вместо полос бумаги довольно часто применяют полосы марли либо недорогой узкой ткани. При стяжке покоробленные и волнистые полосы фанеры подлежат выправлению. Для этого их смачивают горячей водой, укладывают между совершенно верно выстроганными досками под груз и выдерживают до полного подсыхания.
Лист собранной фанеры должен иметь кое-какие припуски и обрезаться совершенно верно по размеру фанеруемой поверхности перед самым наклеиванием либо по окончании него, при зачистке поверхности.
На некоторых мебельных фабриках созданы особые методы наклеивания гуммированной ленты с внутренней стороны комплекта страниц строганной фанеры. В этом случае используют перфорированную гуммированную ленту на более узкой бумажной базе и с меньшей плотностью (30—50 г/м2), чем у простой. На Рижском мебельном комбинате № 3 гуммированную ленту снимают паром при помощи особого пистолета, в который подается пар через резиновый шланг из паропровода.
При нажатии на рычаг пистолета раскрывается клапан, и струя пара, выходя через сопло, направляется на обрабатываемую поверхность. Пистолет перемещают по гуммированной ленте и снимают ее при помощи скребка, укрепленного на финише сопла пистолета. Использование для того чтобы приспособления увеличивает производительность труда более чем вдвое.
НИИ мебели и фанеры (ЦНИИФМ) создан следующий метод стяжки строганой фанеры. На отфугованные кромки хорошо сжатой пачки фанеры наклеивается с обеих сторон конденсаторная бумага толщиной 0,01 мм. По окончании того как клей подсохнет, бумагу разрезают узким ножом через всю пачку и лист фанеры развертывают в щиток.
Все страницы щитка оказываются скрепленными со стороны кромок узкой бумагой, швы же мало заметны.
На многих мебельных фабриках стяжка производится на ребросклеивающих станках РС-6. Стяжка фанеры па ребросклеивающем станке выполняется следующим образом. Стягиваемые полосы подаются под прижимные ролики, хорошо сжимающие кромки.
После этого на образуемый шов наклеивается гуммированная лента.
По пути перемещения лента проходит через аппарат, смачивающий ее клеевую сторону. Намерено обогреваемый ролик прижимает ленту ко шву и в один момент высушивает ее. Станок владеет громадной производительностью, и стяжка фанеры происходит весьма скоро.
Трудящийся на таком станке обязан обеспечить точность подгонки рисунка стягиваемых полос и, помимо этого, весьма совершенно верно подавать фанеру по направляющей линейке торец в торец.
Индустрией выпущен станок для безленточной ребро-склейки. Кромки сложенной в пачки фанеры предварительно наназывают 50—60-процентным раствором столярно-желатинного клея и просушивают в течение 1—2 час. При стяжке на станке кромки полос фанеры смачиваются 10-процентным раствором формалина, хорошо прижимаются друг к другу и прогреваются при температуре 120—150 °С.
Станок устанавливается на больших мебельных фирмах для стяжки строганой фанеры и на фанерных фабриках для ребросклейки шпона.
Рис. 8. Пистолет для снятия паром гуммированной ленты:
1 — рычаг, 2 — клапан, 3 — сопло
Рис. 9. Ребросклеивающий станок РС-6:
а — неспециализированный вид: 1 — станина, 2 — рабочий стол, 3 — прижимной ролик, 4 — гуммированная лента; б — схема работы: 1 — обогреваемая ванночка с водой, 2 — рулон гуммированной ленты, 3 — направляющая линейка, 4 — склеиваемые полосы фанеры, 5 — подающий мелкорифленый валик, 6 — прижимной ровный ролик, 7 — конические ролики, стягивающие кромки склеиваемых полос
На мебельном комбинате Мособлсовнархоза для стяжки фанеры используется таковой станок несложной конструкции. Станок имеет рабочий вал, обтянутый резиной, направляющие конусные ролики, направляющую линейку, стол, кронштейн и электродвигатель для катушки с гуммированной лентой.
Перед склеиванием строганую фанеру подбирают по размерам и текстуре страницы в набор. После этого набор укладывают на стол по направляющей линейке, снабжающей выравнивание кромок в соответствии с углом соединения. Выравненные страницы по кромкам склеивают гуммированной лентой под рабочим валиком. Диаметр валика 70—80 мм, число оборотов 200—220 в 60 секунд.
Давление на склеиваемую поверхность осуществляется весом самого валика. Снизу под валиком
имеются направляющие конусные ролики. Конусность нужна для предупреждения образования щели между кромками страниц. Для обеспечения перемещения склеивающей ленты на всех перегибах имеются ролики, вращающиеся в регулирующихся центрах.
Перед подачей к рабочему валу, куда уже подана стыкуемая фанера, ленту смачивают водой в ванночке.
Приклеивание фанеры
Наклеивать фанеру на базу возможно тремя методами: притиркой, прокаткой и запрессовкой. Наклеивание делают на глютиновых, казеиновых и синтетических клеях. Из глютиновых чаще используется мездровый клей, из синтетических карбамид-ные клеи.
Фанерование на глютиновых клеях возможно создавать запрессовкой и притиркой, а на казеиновом и синтетических клеях— лишь запрессовкой. В любых ситуациях смазывать необходимо лишь базу, а не фанеру.
Рис. 10. Схема ребросклеивающего станка:
1 — рабочий валик, 2 — катушка с гуммированной лентой, 3 — гуммированная лента, 4 — склеиваемые страницы фанеры, 5 — направляющие конусные ролики, б — стол, 7 — электродвигатель
Метод прокатки, используемый на фирмах, содержится в том, что подробность с наложенной фанерой прокатывают между нагретыми вальцами, каковые прессуют и высушивают клеевое соединение.
При наклейке впритирку лист фанеры с лицевой стороны смачивают горячей водой, дабы предотвратить его скручивание и накладывают на основание, разглаживая руками от середины к
краям. Притирку создают особым притирочным молотком, весом до трех килограмм, двигая его на протяжении волокон, от середины к краям. Сперва молоток двигают медлительно, слабо нажимая на него, позже стремительнее и посильнее, так, дабы выдавить излишки клея и вытеснить оставшийся под фанерой воздушное пространство (рис.
324, б). Молоток рекомендуется подогревать. Тепло от молотка не дает клею очень сильно густеть под фанерой и в один момент пара размягчает фанеру, делает ее эластичнее, чем предотвращается появление разрывов на протяжении волокон.
Неприклеившиеся места, так именуемые «чижи», в большинстве случаев выявляют методом простукивания пальцем либо молотком. В таких местах получается дребезжащий глухой звук. В случае если это оказалось оттого, что клей остыл, то «чижи» разогревают горячим утюгом, предварительно намочив фанеру горячей водой.
Клей разогреется и схватит фанеру.
При избытке либо недочёте клея фанеру бережно прорезают на протяжении волокон и в первом случае выжимают его, а во втором намазывают опять и притирают это место тяжелым молотком.
На Столичной фабрике № 8 надрезы не делают, а пользуются для Внесения клея под фанеру медицинским шприцем. Это есть более стремительным и надежным методом.
При наклеивании впритирку нескольких страниц в ряд подобранной по цвету и текстуре фанеры без прифуговывания укладывают на клей с маленькой нахлесткой одного страницы на другой и притирают. По окончании притирки прорезают нахлестнутые кромки полностью фанерной пилкой с зубчатым венцом либо острой стамеской и, немного подняв края обоих страниц фанеры, удаляют обрезанные кусочки, смазывают эти места клеем, шепетильно вправляют обрезанные кромки, по окончании чего делают окончательную притирку. На все прорезей и места стыков наклеивают полосы бумаги, дабы предотвратить при высыхании образование и коробление щелей.
Рис. 11. Прием работы притирочным молотком:
а — притирочные молотки, б — приемы притирки
Рис. 12. Фанерование щитов и широких деталей без предварительной стяжки фанеры:
а — притирка перзой полосы фанеры, б — притирка второй полосы, подобранной по цвету и текстуре, в — прорезка кромок, г — удаление срезков, д — дополнительное временное скрепление шва полосой бумаги либо гуммированной лентой
Небольшие подробности довольно часто фанеруют при помощи простых струбцин. Подкладка под винты (доска либо брусок) толщиной 30— 50 мм обязана соответствовать размерам фанеруемой подробности.
Фанерование впритирку и при помощи простых столярных струбцин трудоемко и малопроизводительно, исходя из этого рекомендуется его заменять методом запрессовки. Метод запрессовки пребывает в том, что подробность с наложенной фанерой помещают в пресс либо в хомутовые струбцины, давление которых передается неспешно от середины к краям. Подробности возможно закладывать в пара слоев (пакетами), переложив прокладочными страницами.
Прокладки предохраняют подробности от склеивания между собой.
Прокладками смогут быть страницы клееной фанеры и железные страницы. Наилучшими считаются цинковые страницы, поскольку они не покрываются коррозией и при изгибе легко выпрямляются. Железные прокладки возможно нагреть, а это содействует ускорению склеивания и даёт предупреждение застудневание клея при долгом формировании многослойного пакета.
Прокладка из клееной фанеры должна быть прекрасно отшлифована, а перед укладкой ее нужно натирать кусковым мягким мелом либо мылом, дабы она не приклеилась к облицовочной фанере. Значительно лучше покрывать ее нитролаком. Прокладки из фанеры направляться оберегать от вмятин, вырывов и отщепов, а по окончании потребления осматривать и где необходимо очищать от клея.
Железные прокладки направляться промывать.
При формировании пакета все щиты укладывают один на другой и прекрасно сглаживают их края, дабы кромки фанеры не остались неприклеенными. Формируя пакеты из брусков, бруски укладывают последовательностями во всю ширину пакета с маленькими промежутками. В каждом вертикальном последовательности бруски должны быть расположены один над вторым.
Бруски с конусами укладываются в одном последовательности толстыми финишами в одну сторону, а во втором последовательности толстыми финишами в другую сторону.
приспособления и Оборудование для фанерования
На фирмах с малым количеством фанерования запрессовку создают в хомутовых струбцинах. Хомутовая струбцина—это прочная прямоугольная рамка из четырех массивных древесных либо железных брусков. В верхнем бруске рамы имеются гайки, через каковые пропущены 3,5 либо 7 винтов, завинчиваемых торцовым ключом с воротком.
При пользовании струбциной сперва завинчивают средние винты, после этого ближайшие к ним и, наконец, крайние, дабы выдавить излишки клея из середины к краям. количество винтов и Размеры струбцин в них зависят от ширины фанеруемых подробностей, а количество струбцин — от длины подробностей.
На фирмах с громадным количеством работ по фанерованию используются механические (винтовые), гидравлические и пневматические прессы. Механический (винтовой) фанерный пресс продемонстрирован на рис. 327.
В гидравлическом прессе фанерование производится горячим методом на синтетических клеях. Подогрев достигает 110—130 °С под давлением от 3 до 15 кг/см2. Плиты пресса имеют размер от 1200X2200 мм и более. В любой пролет пресса может загружаться не одна, а пара заготовок однообразной толщины.
Многопролетный (8—10 пролетов) гидравлический пресс с паровым обогревом плит продемонстрирован на рис. 328.
Рис. 13. Фанерование с запрессовкой в хомутовых струбцинах:
а — вид с торца, б — вид в плане
Рис. 14. Механический (винтовой) пресс для фанерования
Сборку заготовок при одновременном изготовлении щитов и фанеровании их создают на железных страницах-прокладках. На железную прокладку, установленную около пресса на столе, укладывают лицевую рубаху из строганой фанеры. При фанеровании в два слоя на лицевую рубаху накладывают черновую (внутреннюю) рубаху, намазанную с обеих сторон клеем.
На черновую рубаху устанавливают серединку щита — столярную плиту либо реечное заполнение,—а на нее опять укладывают с двух сторон намазанную клеем черновую рубаху из шпона и закрывают сверху второй лицевой рубахой. Целый пакет накрывают железной прокладкой. Готовый пакет поме
щают в пресс вручную либо при помощи загрузочного лифта, которым в один момент загружаются все пролеты пресса. По окончании загрузки включают насос, и плиты пресса смыкаются, создавая нужное давление. Пакеты выдерживают в прессе 5—20 мин.
Зафанеро-ванные заготовки выгружают тёплыми либо по окончании охлаждения.
При фанеровании с применением костного либо мездрового клея температура нагрева плит пресса доводится до 60—65 °С и заготовки выдерживаются 20—25 мин. с постепенным охлаждением плит.
Рис. 15. Гидравлический пресс с обогреваемыми плитами
Рис. 16. Матрицы для фанерования пилястр в гидравлическом прессе:
1 — алюминиевое основание спаренной матрицы, 2 — древесные бруски, 3 — лоток из листового алюминия, 4 — лист декоративной фанеры, 5 — пилястра, 6 — накладка
На Столичной мебельной фабрике № 8 восьмипролетный пресс применяют для фанерования пилястр. Для этого изготовлены матрицы несложной конструкции. Представляет собой матрица лоток из двух древесных брусков, укрепленных параллельно на алюминиевом основании. К верхним кромкам брусков прикреплен второй лоток из листового алюминия, выгнутый соответственно конфигурации пилястры.
В эту матрицу закладывают заготовки и накрывают прокладкой, одна сторона которой облицована листовым алюминием. На одном основании монтируются матрицы, по ширине пресса их укладывают восемь. Запрессовка при температуре до 100 °С производится а течение 15—17 мин.
При таком методе фанерования пилястр производительность намного выше, чем при пользовании пневматическими ваймами.
Для фанерования смогут быть использованы кроме этого гидравлический пресс ПГ-1 и пневматические прессы ПП-2 и ПП-3.
При фанеровании и склеивании древесины для обеспечения равномерного давления используются пневматические прессы. Они позволяют приобретать щиты более большого качества. Всесоюзным проектно-конструкторским и технологическим университетом мебели (бывш. ЦМКБ) сконструирован пневматический пресс с перемещаемой верхней поперечиной.
Пресс несложен по конструкции и возможно изготовлен в ремонтно-механиче-ской мастерской.
Пресс вертикальный складывается из двух поперечин: верхней, перемещаемой, и нижней, неподвижной. Они связаны между собой двумя ходовыми винтами, установленными в направляющих втулках и закрепленными с двух финишей гайками 5. Верхняя поперечина перемещается по ходовым винтам. В нее находится электродвигатель, зубчатая передача, вал, две гайки и червячные передачи. Вал связан с червячной передачей двумя твёрдыми муфтами и укреплен в подшипниках скольжения.
Верхнюю поперечину перемещать возможно и вручную съемной рукояткой, надеваемой на выходной финиш оси правого червяка. На нижней поперечине установлены эластичные резиновые пневмокамеры, для которых ложем есть древесный щит. Над пневмокамерами расположена подъемная древесная плита, обшитая листовой сталью.
При работе пресса плита поднимается и опускается, двигаясь по цилиндрическим направляющим. Поднимается плита пневмокамерами, приводимыми в воздействие сжатым воздухом. Под подъемной плитой для выгрузки щитов и облегчения загрузки расположены роликовые шины, установленные в цилиндрических направляющих.
Рис. 17. Пневматический пресс с перемещаемой поперечиной:
1 — верхняя перемещаемая поперечина, 2 — нижняя неподвижная поперечина, 3 — ходовые винты. 4 —направляющая втулка. 5 —гайка, 6 — электродвигатель, 7 — зубчатая передача, 8 — вал, 9 — червячная передача, 10— съемная рукоятка, 11 — резиновая пневмокамера, 12 — древесный щит, 13 — подъемная плита, 14 —цилиндрические направляющие плиты, 15 — роликовые шины, 16 — цилиндрические направляющие, 17 — пульт управления, 18 — кран управления пневмокамерами, 19 — манометр, 20 — реверсивный тумблер, 21 — регулятор давления воздуха в пневмокамерах, 22 — древесный щит, 23 — муфта
На каркасе нижней поперечины установлен пульт управления 17, в котором вмонтированы кран управления пневмокамерами, манометр, реверсивный тумблер электродвигателя, приводящего в перемещение верхнюю поперечину, и регулятор давления воздуха в пневмокамерах. При увеличении давления в сети воздушное пространство, действующий на поршень, преодолевает сопротивление пружины, и клапан приоткрывается, благодаря чего давление в пневмокамерах сохраняется в установленных пределах.
Обе поперечины — это сварные рамы из проката стандартного профиля. Главными несущими элементами поперечин помогают продольные двутавровые балки, на каковые передается давление через поперечные двутавровые балки. Снизу к балкам верхней поперечины прикреплен древесный щит, обшитый с рабочей стороны листовой сталью.
Муфта, предохраняющая электродвигатель от перегрузки, находится на валу электродвигателя подвижной поперечины.
Для фанерования употребляются и сборные пневмокаме-ры, созданные ЦМКБ,каковые весьма несложны в изготовлении и надежны в работе. С успехом они используются на ростовской мебельной фабрике им. Урицкого. Камеры планируют из Двух слоев резины, каковые покрыты снаружи двумя слоями ткани и стянуты замкнутой сварной рамой и разъемными древесными накладками 4 при помощи болтов.
Для большей герметичности пневмо-камеры под накладки и сварную раму уложены прокладки из резины.
Сжатый воздушное пространство подается через штуцер в середину камеры снизу по прорезиненным рукавам. Пресс с верхней перемещаемой поперечиной позволяет запрессовывать пакеты различной высоты, не закладывая запасных щитов для заполнения свободного пространства.
Рис. 18. Сборная пневмокамера:
1 — резина, 2 — ткань, 3 — сварная рама, 4— разъемная накладка, 5 — резиновая прокладка
При склеивании и фанеровании подробности перед загрузкой набирают в пакет, что сверху и снизу ограничивают щитами. В случае если пакет набирается из нескольких пачек различных подробностей, для компенсации малом отличия по высоте между отдельными пачками на каждую пачку накладывают лист резины толщиной 5—6 мм. Подробности по длине и ширине пакета направляться укладывать не близко друг к другу, а с зазорами не меньше 20—30 мм.
Собранный пакет вкатывают по роликовым шинам в пресс. Под нижний и на верхний щиты укладывают балки для стягивания пакета. Располагают балки на равных расстояниях-одну от второй так, дабы верхняя пребывала под соответствующей ей нижней.
После этого включают электродвигатель и опускают верхнюю поперечину близко на пакет, по окончании чего электродвигатель выключают, а в пневмокамеры из пневмосети либо от личного мобильного компрессора впускают сжатый воздушное пространство.
Под давлением воздуха пневмокамеры возрастают в количестве, и подъемная плита прижимает пакет к верхней поперечине. Давление пневмокамер, доведенное до требуемой величины, передается склеиваемым подробностям равномерно по всей площади. После достижения требуемого давления на финиши балок накладывают болтовые стяжки. Это позволяет при снятии пресса сохранить полученное давление на пакет. По окончании 10—15 мин. болтовые стяжки опять подтягивают, а давление снимают.
Пневмокамеры под тяжестью пакета сжимаются до начального размера, а пакет в стяжках опускается на роликовые шины. Пакет выкатывают из пресса, включают электродвигатель и поднимают верхнюю поперечину.
Выдержка пакета вероятна и в прессе. В этом случае в прессе остаются лишь нижние балки, служащие для передачи давления пакету от подъемной плиты. Контролируется давление по манометру, установленному на пульте управления.
Рационализаторы деревообработки направляют свои силы на большое применение механизации в самые трудоёмких процессах. Особенное место занимает декоративное фанерование, приклейка к щитам пилястр, других деталей и реек, и склейка и сборка узлов и деталей. Используется пара способов ускоренного контактного склеивания: методом обогрева парового, электрического и высокочастотного.
Обширно фанерование производится в пневматических ваймах с контактным электрообогревом. В случае если раньше склейка потребовала 3—5 час. выдержки, то на данный момент, с применением электроконтактного метода, технологический процесс доведен до 2—3 мин.
Обработанные таким методом заготовки смогут срочно подвергаться предстоящей обработке.
Пневматическая вайма с контактным обогревом предназначена для фанерования трех кромок у щитов с круглыми углами. Вайма представляет собой железный каркас, сваренный из уголков, в котором смонтированы прижимные брусья. Эти брусья под действием раздувающихся пневматических мешков перемещаются, сжимая фанеруемую подробность.
В качестве таких мешков употребляется хлопчатобумажный, изнутри прорезиненный, пожарный рукав с наружным диаметром 70 мм.
Рис. 19. Пневматическая вайма с контактным обогревом:
1— каркас, 2 — прижимные брусья, 3 — латунная лента для электрообогрева, 4 — воздушные рукава, 5 — воздушный кран, 6 — понижающий трансформатор
Между прижимами посередине каркаса установлена нагревательная пластина. Электродом, прикрепленным к переднему и боковым прижимным брусьям, есть латунная лента толщиной 0,5 мм. Она жестко крепится лишь к задним финишам боковых брусьев, в середине же лента может при маленьком Упрочнении передвигаться.
Передвижение это нужно при об-тяге круглых углов.
Между прижимными брусьями и лентой имеется прокладка из листового асбеста либо листовой теплостойкой резины и ровные дюралевые полосы. Прокладка помогает для ослабления и изоляции передачи тепла, полосы — для выравнивания плоскостей брусьев. Питание нагревателя производится от сети переменного тока напряжением 220 в, что понижается трансформатором до 5 в.
По окончании укладки подробности в вайму через кран впускается сжатый воздушное пространство в рукав для нажима бруса на переднюю кромку, после этого через второй кран в рукав заднего мобильного бруса для обтяга круглых углов и, наконец, через третий кран в рукава боковых нажимных брусьев. Поеде зажима подробности включают нагрев ленты через магнитный пускатель. Спустя время, нужное для выдержки, воздушное пространство производят, снимая давление, и подробность вынимают из ваймы.
Наряду с этим выключение нагрева производится машинально, поскольку оно сблокировано с краном. В качестве клея для фанерования подробностей в вайме используется карбамидная смола М-70.
Внедрение пневматических вайм разрешает существенно сократить цикл фанерования, повысить производительность труда, заменить дорогостоящий столярный клей более недорогим смоляным клеем, улучшить уровень качества фанерования.
Сейчас на передовых мебельных фабриках используют прессы с высокочастотным обогревом заготовок, что разрешает осуществить прогрев в весьма маленький срок и снабжает равномерность обогрева независимо от толщины материала. Фанеруемые подробности помещают между двумя электродами, создающими равномерное высокочастотное поле.
Наровне с высокочастотными прессами на данный момент используется и ручной инструмент с высокочастотным нагревом. Воображает он собой ручной склеивающий аппарат (утюжок), дающий возможность в течение нескольких секунд склеивать древесные заготовки. Прибор эргономичен в работе, он весит 1360 г.
В случае если фанерование производится вручную, то клей наносят либо широкой кистью, либо на клеенамазочном станке. На клеена-мазочном станке клей наносится узким ровным слоем. Это достигается тем, что вальцы покрыты листовой резиной с небольшим рифлением.
Станки бывают одновальцовые и двухвальцовые. Вальцы приводятся в перемещение ременной либо зубчатой передачей.
Рис. 20. Ручное приспособление для высокочастотного нагрева при склеивании
Довольно часто при фанеровании используется клеевая пленка. При применении пленки отпадает необходимость в намазывании клея в ходе фанерования пакетов, чем и упрощается целый процесс склеивания.
Криволинейные профильные подробности фанеруют посредством разных приспособлений — контрпрофильных колодок, реечных, сыпучих и эластичных цулаг, нагнетательных и вакуумных камер, автоклавов.
Рис. 21. Цулаги для фанерования профильных подробностей:
а — контрпрофильная колодка, б — реечная цулага, в, г — сыпучие цулаги (мешок с песком)
Контрпрофильные колодки должны иметь профили, обратные профилю фанеруемой подробности. Ввиду того что фактически тяжело добиться правильного совпадения профиля колодки с профилем подробности, на фанеру накладывают листовую резиновую прокладку, чем и достигается равномерное распределение давления. Прижимается колодка струбцинами либо наложением груза.
Давление должно быть перпендикулярным к фанеруемой подробности; особенно нужно обеспечить давление по краям, в другом случае прочного склеивания не окажется.
Использование контрпрофильных колодок связано с изготовлением для каждого размера и каждого профиля отдельной колодки, а это требует громадных расхода материала и затрат труда.
Реечная цулага используется для фанерования подробностей разных несложных профилей. Она делается из реек однообразных размеров, наклеенных на ткань параллельно друг другу с маленькими промежутками. Зажим фанеруемых подробностей производится через профильные бруски при помощи струбцины либо наложением сыпучего груза в виде мешков с песком.
При пользовании реечными цулагами направляться в обязательном порядке использовать резиновые либо железные прокладки, содействующие равномерному распределению давления.
Сыпучие цулаги являются мешки, до половины наполненные промытым, просеянным и нагретым до 50—60 °С небольшим песком. Размеры мешков зависят от размеров фанеруемых подробностей. Мешок прижимают к фанеруемой поверхности струбцинами через продольные рейки и надавливают сперва на серединную часть наклеенной фанеры.
Рис. 22. Схемы действия резиновых камер для фанерования профильных подробностей:
а — нагнетательная камера, б — вакуумная камера
При фанеровании маленьких подробностей возможно применять сухие подогретые опилки древесины лиственных пород. Для этого фанеруемые подробности укладывают в горизонтальный последовательность на дно коробки, засыпают опилками и сверху покрывают щит.ком. На щиток накладывают груз — кирпич, камни, кусок рельса, маленькие цементные подробности и т. п.
Эластичные цулаги используются при фанеровании круглых подробностей и складываются из металлических и прочных пеньковых лент. Финиши лент вправлены в железные угольники, каковые стягивают винтами по окончании охвата по периметру фанеруемой подробности.
Резиновые камеры используются при фанеровании профильных подробностей. Сделаны камеры в виде мешков из листовой резины и помещаются в предохранительные чехлы из брезента либо прорезиненной ткани. Камеру помещают в намерено устроенную коробку, а на нее профильной поверхностью вниз укладывают и закрепляют подробность. Затем через шланг камеру наполняют сжатым воздухом либо водой.
Рекомендуется как воздушное пространство, так и воду подогревать до 50—60 °С.
Используются кроме этого вакуумные резиновые камеры-мешки, из которых насосом выкачивают воздушное пространство до сильного разрежения. Подробность с наложенной на клей фанерой помещают вовнутрь камеры, которую герметически закрывают. После этого из камеры через шланг выкачивают стенки и воздух камеры силой давления обжимают подробность со всех сторон. При фанеровании в вакуумной камере для увеличения давления на фанеру используется автоклав.
Автоклав представляет собой герметически закрывающийся полый железный цилиндр. В автоклав возможно накачивать воздушное пространство либо жидкость давлением до нескольких воздухов и выкачивать из него воздушное пространство, образуя вакуум. Вакуумную камеру с запрессованной в ней подробностью помещают в автоклав, после этого накачивают воздушное пространство либо воду и создают давление до 3 атм и больше.
Воздушное пространство либо воду полезно подогревать.
При фанеровании профильных подробностей наклеенную фанеру в обязательном порядке необходимо сверху увлажнить. Это даёт предупреждение продольный ее излом, образование на ней трещин. Чем радиус кривизны профиля меньше, тем больше направляться увлажнять фанеру.
Фанерование направляться вести при следующих режимах. В помещении для фанерования температура окружающего воздуха должна быть 20—30°С, густота клея — средняя, его расход 0,3 кг на 1 м2, длительность смазки клеем и закладывания в пресс — не более 30 мин. Запрессованные подробности выдерживаются в течение 3—3,5 час. в помещении с температурой не ниже 18 °С.
Обработка фанерованных подробностей обязана производиться не ранее чем через 2—4 дней по окончании освобождения от запрессовки.
Устранение недостатков фанерования
Уровень качества фанерования направляться определять внешним осмотром, простукиванием поверхности пальцем либо особым прибором (вибратором), созданным проф. Соколовым. Прибор снабжен телефонными наушниками, при помощи которых дефектные места выявляются на слух.
Помимо этого, подробности контролируют на отгиб фанеры и пробным заламыванием ее на кромках.
На исправление недостатков фанерования затрачивается большое количество времени и не всегда удается устранить их бесследно. Исходя из этого Недостатки при фанеровании существенно легче не допускать, чем их исправлять.
К обстоятельствам, вызывающим недостатки фанерования, относятся:
1. Высокая влажность либо неравномерное распределение влажности по сечению подробности благодаря неудовлетворительной просушки материала.
2. Шероховатая поверхность распиливания, зачистка древесины и неудовлетворительная обработка склеиваемой поверхности.
3. Неодинаковая толщина фанеры либо неровная поверхность прокладок и цулаг.
4. Густой (застуденевший) либо через чур жидкий клей.
5. Неравномерное либо недостаточное нанесение клея.
6. Неправильное размещение пакета в прессе.
7. Неверный режим прессования — недостаточное либо через чур большое давление, неправильно установленная температура, недостаточная выдержка под прессом.
8. Сильное просачивание (пробитие) клея либо приклеивание фанеры к прокладке.
9. Неравномерная толщина фанеруемых заготовок, незаде-ланные сучки и неудаленные смоляные места.
10. Попадание между прокладкой и фанерой больших стружек, щепочек или других посторонних тел.
11. расхождение и Сдвиг страниц фанеры.
Исправление недостатков фанерования должно соответствовать техническим условиям на изделия. Вставки направляться делать из кусков фанеры, подобранных по цвету и текстуре. Вставкам необходимо придать ромбическую форму для совпадения линий швов с направлением волокон. Неровности, выступы, смятия на фанере размачивают тёплой водой и сушат под цулагой и прессом.
Прекрасный результат получается, в случае если смачивать клеевой водой.
При больших недостатках необходимо снять фанеру методом строгания. В случае если при фанеровании применен глютиновый клей, то поверхность необходимо предварительно намочить водой и гладить горячим утюгом до отставания фанеры.
Прослойка между наклеенной основой и фанерой необратимого клея (казеинового либо синтетического) при нагревании не плавится. Вклеивать вставки фанеры на необратимых клеях вероятно лишь с запрессовкой, а не впритирку.