Электродуговая сварка и резка
Метод Бенардоса. На рис. 1 приведена схема сварки по методу Бенардоса.
Электрическая дуга возбуждается между свариваемой графитовым электродом и деталью. Электрод закрепляется в держателе, что эластичным кабелем присоединяется к одному из полюсов источника тока, в большинстве случаев, к катоду (отрицательному полюсу). Свариваемая подробность помещается на железной плйте, соединенной со вторым полюсом источника тока.
Зажигание дуги создают краткосрочным соприкосновением электрода со свариваемой подробностью и последующим их разъединением. Установившаяся электрическая дуга поддерживается при неизменном расстоянии между электродом и основным металлом. Это расстояние определяет длину дуги и примерно равняется диаметру электрода. Дуга, имеющая температуру более чем 5000°, расплавляет кромки свариваемых частей, и металл кромок сливается в неспециализированную ванночку.
При передвижении дуги на протяжении свариваемых кромок нагреваются и плавятся новые частицы металла, ванночка перемещается, а остающийся сзади металл затвердевает, остывает и образует шов, соединяющий свариваемые части в одно целое. Довольно часто ванночка пополняется за счет присадочного металла, вносимого в пламя дуги в виде круглых прутков. Время от времени присадочный металл укладывают в разделку шва заблаговременно.
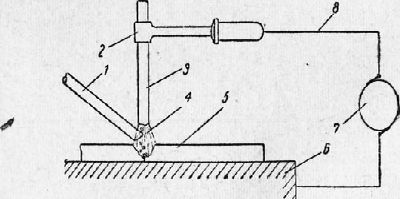
Рис. 1. Схема сварки по методу Бенардоса
Сварка по методу Бенардоса имеет ограниченное использование в индустрии. Она употребляется для получения бортовых соединений тонкостенных металлических подробностей, где не нужно присадочный металл для чугуна и цветных металлов, и для наплавки порошкообразных жёстких сплавов. Наряду с этим методе сварки в большинстве случаев используют постоянный ток, причем в целях обеспечения устойчивой меньшего расхода и дуги электродов, и для лучшего прогрева подробности при сварке пользуются прямой полярностью: подробность делают анодом (+), а электрод — катодом (—).
Рис. 2. Схема сварки по методу Славянова (я); сварка покрытым электродом (б): 1 — электрод; 2 — направленный металл; 3 — корка затвердевшего шлака; 4 н? — свариваемые части; 6 — ванночка жидкого металла
Метод Славянова. По методу Славянова (рис. 2, а) используется железный электрод 1 в виде проволоки. Дуга, возбуждаемая между основным металлом и электродом, плавит как главный металл, так и электрод, причем образуется неспециализированная ванночка, где перемешивается целый расплавленный металл. Так, электрод тут есть одновременно и присадочным металлом. Электродная проволока выпускается диаметром от 1 до 10 мм.
Для сварки стали значительно чаще используют мягкую металлическую проволоку, содержащую 0,1—0,18% углерода. Для сварки легированной стали используют проволоку из стали марок Св-ЮГС, Св-ЮГСМ, Св-20ХГСА, Св-15др и М.
При ручной дуговой сварке по методу Славянова пользуются практически только покрытыми электродами (рис. 2, б), поверхность которых обмазана особым составом. Покрытия электродов бывают узкие (ионизирующие) и толстые (качественные).
Узкие покрытия наносятся для увеличения устойчивости горения электрической дуги; они в большинстве случаев складываются из мела с жидким стеклом. Находящиеся в составе мела соединения кальция легко ионизируются (выделяются в виде электропроводных частиц) и, заполняя газовый промежуток дуги, облегчают ее горение. Вес ионизирующего покрытия образовывает 1—2% от веса электрода, а толщина слоя обмазки колеблется в пределах 0,1—0,25 мм.
Толстые (качественные) покрытия должны не только снабжать устойчивость дуги, но удовлетворять кроме этого последовательности вторых требований. Составы обмазок для толстых покрытий подбираются так, дабы около дуги создавалась газовая защитная воздух, дабы изолировать металл электрода, стекающий вдуге, и металл ванночки от растворения и окисления в нем газов (к примеру, азота). По мере плавления электродов обмазка переходит в шлак, равномерно покрывающий шов.
Шлак защищает металл от поглощения и окисления азота, помимо этого, он замедляет охлаждение металла, что содействует более полному выделению растворенных газов и увеличению плотности шва. При необходимости легирования шва металла в состав обмазки вводят ферросплавы, которые содержат необходимые легирующие элементы.
Так, в состав толстых покрытий входят ионизирующие (к примеру, мел), газообразующие (к примеру, мука), шлакообразующие (полевой шпат) материалы, и раскислители (к примеру, ферромарганец) и легирующие вещества. Вес качественного покрытия образовывает 20—35% от веса электрода, а толщина слоя обмазки колеблется в пределах 0,25—0,35 d, где d — диаметр электрода.
Электроды без обмазки, в отличие от покрытых электродов, именуют обнажёнными.
При сварке обнажёнными электродами металл шва не защищен от действия газов, исходя из этого он содержит увеличенное количество азота и кислорода, а благодаря стремительного застывания из металла шва не успевают выделяться газовые пузыри и неметаллические включения. Такие швы владеют пониженными качествами.
В любых ситуациях в то время, когда шов обязан удовлетворять повышенным требованиям (громадные нагрузки, давление газа либо жидкости и пр.), используют толстопокрытые электроды, каковые снабжают получение шва, по пластичности и прочности не уступающего главному металлу.
Обычными пороками швов являются: непровар — местное отсутствие сплавления между наваренным и главным металлом; пористость металла швов; трещины и шлаковые включения; пережог — окисление металла шва и прилегающего к нему главного металла (появление пленок окиси по границам зерен). Эти пороки вызываются неправильной разработкой сварки, применением несоответствующих электродов и другими обстоятельствами.
В зоне шва структура металла и его механические особенности поменяны благодаря на-грева при сварке и последующего охлаждения, исходя из этого в сварном шве имеются остаточные напряжения. Для выравнивания структуры и устранения напряжений создают отжиг сварных подробностей.
Аппаратура для сварки. Для горения электрической дуги нужно напряжение 18—25 в — при железном электроде (напряжение холостого хода 55—65 в) и 35—40 в — при угольном электроде (напряжение холостого хода 60—80 в). В момент возбуждения дуги электрод касается изделия (замыкание), сила тока растет, а напряжение падает практически до нуля; при удлинении дуги напряжение возрастает.
Дуговую сварку возможно вести на постоянном либо на переменном токе. Дуга на постоянном токе горит устойчивее, но стоимость сварки и расход электроэнергии выше, чем при применении переменного тока.
Для питания дуги постоянным током используют генераторы; для сварки переменным током применяют сетевой ток стандартного напряжения (127, 220, 380, 500 в), что пропускают через сварочный аппарат, складывающийся из понижающего регулятора и трансформатора тока.
генераторы и Сварочные аппараты делятся на однопостовые — для питания одной дуги и многопостовые — для питания нескольких дуг. Многопостовая сварочная аппаратура используется в громадных сварочных цехах.
На рис. 3 приведена схема включения сварочного аппарата переменного тока типа СТЭ завода «Электрик».
Первичная обмотка П трансформатора подключается к сети; к вторичной обмотке В низкого напряжения (55—65 в) подключается регулятор тока (реактор), регулирующий ток в сварочной цепи.
Ток регулируется методом трансформации индуктивного сопротивления реактора. Часть сердечника может перемещаться посредством винта при вращении рукоятки наряду с этим будут изменяться воздушный зазор а и, следовательно, индуктивность обмотки реактора. При повышении зазора магнитное сопротивление сердечника возрастает, индуктивность обмотки реактора значительно уменьшается и сварочный ток возрастает; при уменьшении зазора сварочный ток значительно уменьшается.
Сварочные генераторы постоянного тока приводятся в воздействие электродвигателем либо двигателем внутреннего сгорания. Они должны выдерживать громадные токи (до 300 а и более), каковые появляются при возбуждении дуги.
Рис. 3. Схема включения сварочного аппарата типа СТЭ
Для лица сварщика и защиты глаз от действия лучей дуги используют шлемы и щитки с чёрными стеклами.
Дуговая сварка в воздухе защитного газа. В современной промышленной практике используется сварка электрической дугой в воздухе защитного газа. Сущность этого метода сварки сводится к тому, что в зону дуги подводится защитный газ, благодаря чего дуга горит не в воздухе воздуха, а в воздухе газа (в большинстве случаев водорода либо аргона), защищающего расплавленный металл от поглощения и окисления азота из воздуха.
Атомно-водородная сварка производится свободной (горящей между двумя электродами независимо от наличия свариваемого предмета) дугой, возбуждаемой между вольфрамовыми электродами; в зону горения дуги подается водород (Нг), диссоциирующий по реакции Н2 —»2Нс поглощением громадного количества теплоты. Соприкасаясь с металлом, атомарный водород переходит в молекулярное состояние (2Н—Н2),.выделяет наряду с этим ранее поглощенное тепло дуги, которое употребляется для сварки. Атомно-водородная сварка используется при изготовлении очень важных тонкостенных конструкций из высокоуглеродистой и легированной стали и из алюминиевых сплавов.
Аргонно-дуговая сварка производится зависимой дугой, т. е. горящей между обнажённым электродом и свариваемым предметом в воздухе аргона, не участвующего в химических реакциях, а служащего только газовой защитой, мешающей проникновению кислорода и азота в зону электрической дуги. Аргонно-дуговая сварка употребляется для соединения подробностей из магниевых, алюминиевых сплавов, нержавеющей стали, меди и других металлов и сплавов.
Более недорогим газом, используемым для данной же цели, есть углекислый газ. Сварка в воздухе углекислого газа в большинстве случаев используется для исправления пороков отливок из углеродистой и легированной стали.
Аргонно-сварка и дуговая сварка в воздухе углекислого газа значительно чаще производятся с автоматической подачей сварочной проволоки.
Автоматизация электродуговой сварки. При ручной сварке сварщик обязан поддерживать дугу, подавать электрод в зону дуги по мере его расходования и передвигать дугу на протяжении шва. Механизация этих главных операций сварки разрешает осуществлять полуавтоматическую и автоматическую сварку.
Рис. 4. Схема автоматической сварки под слоем флюса
Незадолго до ВОВ в СССР был создан и внедрен в производство метод скоростной электродуговой сварки под слоем флюса, предложенный акад. Е. О. Патоном.
Сущность метода автоматической электродуговой сварки пребывает в следующем. Сварочная головка (рис. 4) подает в зону дуги электродную проволоку из магазина.
Для питания дуги, образующейся между электродной проволокой и основным металлом, возможно использовать переменный либо постоянный ток. В заводских условиях в большинстве случаев пользуются переменным током; сварка на постоянном токе используется в поле, где для привода сварочного генератора постоянного тока употребляется двигатель внутреннего сгорания. По мере образе-вания шва головка (а с ней и дуга) машинально перемещается на протяжении разделки.
Вместе с головкой перемещается бункер, из которого в разделку шва перед дугой засыпается гранулированный (сыпучий) флюс. Так, сварка протекает под слоем флюса, защищающего навариваемый металл от воздуха. Часть флюса расплавляется от соприкосновения с дугой и при остывании образует корку, покрывающую шов и замедляющую охлаждение металла.
Сыпучий флюс, оставшийся поверх корки, засасывается в бункер через шланг и сопло.
Скоростная автоматическая сварка по методу Е. О. Патона имеет следующие преимущества:
а) резкое увеличение производительности;
б) улучшение качества шва благодаря глубокому провару, замедленному полному выделению и охлаждению металла из него газов и шлака;
в) экономия проволоки в связи с уменьшением сечения швов на 20—40% (благодаря улучшению качества шва по сравнению
с ручной сваркой) и отсутствием остатков (огарков) электродов;
г) экономия до 50% электричества благодаря меньшего количества расплавляемого металла, увеличения коэффициента нужного действия до 0,65 (если сравнивать с 0,35 при ручной сварке) за счет концентрированного нагрева металла, отсутствия утрат на лучеиспускание;
д) удешевление за счет применения обнажённой проволоки вместо дорогих толстообмазанндох электродов.
К недочётам этого метода относится невозможность производства «потолочной» сварки (сварки над электродом); помимо этого, он применим только при поточном производстве однотипных подробностей.
Электродуговая резка. При электродуговой резке металлов заготовка разделяется на части расплавлением в зоне реза, а не благодаря сгорания металла, исходя из этого электродуговая резка применима как для стали, так и для цветных металлов и чугуна.
Дуговая резка может осуществляться графитовым либо угольным электродом. Резка графитовым электродом дает лучшую чистоту реза.
Резка железным электродом менее экономична, поскольку для этого смогут использоваться лишь электроды с толстой обмазкой, нужной для обильного шлакообразования.
Электродуговая резка не дает ровной поверхности реза и исходя из этого используется по большей части для разделки лома, литников и отделения прибылей у отливок из высоколегированной стали, не поддающейся газовой резке, и т. п.; производительность ее низкая.
Сейчас начали использовать более производительные способы воздушно-дуговой резки, при которой расплав, ленный металл выдувается струей сжатого воздуха.
Подводная сварка металлов и электродуговая резка созданы настоящим участником Академии наук Украинской ССР К. К. Хреновым.
Рис. 5. Схема горения электрической дуги под водой:
Для работы под водой (рис. 5) используют обмазку, плавящуюся пара медленнее электродной проволоки, в следствии чего на финише электрода образуется чашеобразный козырек. Окружающая дугу вода под действием теплоты испаряется и разлагается с образованием газового пузыря, в котором дуга горит практически так же нормально и устойчиво, как на воздухе.
Избыточные газы поднимаются на поверхность воды; газовый пузырь непрерывно возобновляется за счет испарения и разложения окружающей воды.