Контроль качества поверхностной закалки
Высокочастотная закалка подробностей отличается, в первую очередь, тем, что как правило закалке подвергается лишь поверхностный слой заданной толщины. Это ведет к необычному распределению внутренних механических напряжений, хорошему от такового при закалке с нагревом в ваннах и печах. Наличие поверхностного закаленного слоя заставляет пересмотреть последовательность вопросов, которые связаны с прочностью изделий; значительно изменяются по сравнению со сквозной закалкой их усталостная прочность, ударная вязкость.
Второй изюминкой высокочастотной закалки есть возможность очень эластичного регулирования процесса нагрева. Но не обращая внимания на такую гибкость регулирования, осуществление яркого контроля температур связано с целым рядом трудностей. Исходя из этого для проверки правильности выбранного режима термической обработки приходится прибегать к металлографическому анализу, разрешающему изучать структуру металла, и на базе взятых результатов корректировать электрический режим нагрева.
направляться различать три характерных случая контроля результатов высокочастотной закалки:
1. Проверка результатов на протяжении налаживания процесса закалки подробностей нового типа.
В этом случае по окончании закалки одной подробности ее подвергают подробному, время от времени всестороннему изучению. Результаты изучения применяют для установления ориентировочного режима, после этого снова закаливают подробность и опять ее исследуют. Данный процесс продолжают до тех пор, пока не будут совсем установлены электрический режим нагрева, технология и оптимальная конфигурация индуктора фактически закалки, пригодные для серийного либо массового производства.
2. Проверка результатов закалки при серийном либо массовом производстве однотипных подробностей.
Такая проверка производится на подробностях, отбираемых от партии по определенной совокупности, которую время от времени показывают в технологических картах.
3. Отыскание обстоятельства брака.
В этом случае рассмотрению подвергаются подробности, вышедшие из строя в ходе производства либо на протяжении эксплуатации.
Во всех приведенных случаях контроль результатов высокочастотной закалки может осуществляться разными способами, причем кое-какие из них приводят к разрушению подробности. Полезно в один момент применять пара способов контроля.
Любой способ владеет собственными изюминками и помогает в основном для определенных целей. Так, к примеру, изучение поверхности в большинстве случаев предшествует всем вторым изучениям и содержится во травлении поверхности и внешнем осмотре детали. Это разрешает ориентировочно делать выводы о использовавшейся в ходе обработки температуре нагрева.
Травление поверхности разрешает четко распознать закаленную территорию и найти последовательность недостатков, к примеру, микротрещины, незакаленные участки. Серьёзным преимуществом способа изучения поверхности есть то, что его возможно применять в серийном производстве, поскольку он не ведет к повреждению подробности
Наблюдение излома подробности разрешает приближенно, но скоро распознать конфигурацию, качество и глубину закаленного слоя. Конечно, что подробность наряду с этим приходится разрушать, но чрезвычайная быстрота этого способа делает его весьма эргономичным, в особенности при наладке технологического процесса закалки массовых однотипных подробностей.
Изучение разреза подробности методом изготовление макрошлифа разрешает делать выводы о конфигурации закаленного слоя.
Макрошлифом именуют шлифованное и травленное сечение подробности, при котором невооруженным глазом возможно видеть закаленный слой. Для изготовление макрошлифа подробность разрезают по определенным плоскостям. Ровную поверхность разреза обрабатывают одним из особых реактивов — травителей, в следствии чего закаленные участки металла покупают более чёрную окраску.
Макрошлиф позволяет проверить по конфигурации закаленного слоя, верна ли конструкция индуктора и какова полученная глубина закалки. Как будет продемонстрировано дальше, глубина закаленного слоя, отысканная этим способом, не есть подлинной и носит особое наименование «глубина слоя по макро». Недочётом этого способа есть кроме этого необходимость разрушения подробности, но он более точен и идеален, чем контроль по излому.
Способ контроля результатов закалки по твердости есть одним из самые удобных и распространенных. Твердость замеряют как на поверхности, так и в сечении подробности. Это разрешает объективно выяснить территорию закаленного слоя.
Измерение твердости ро глубине большей частью создают на макрошлифах, что разрешает определить подлинную глубину закаленного слоя, и ширину переходной территории. Распределение твердости по глубине в большинстве случаев изображают графиком, что именуют кривой твердости. Измерение твердости по глубине закаленной подробности связано с необходимостью
рушения подробности и исходя из этого чаще используется в ходе наладки. При текущем контроле закаленных подробностей в большинстве случаев ограниваются измерением твердости на поверхности.
Микроисследование полированной и протравленной поверхности боазца, вырезанного из подробности, содержится в рассмотрении ее священик микроскопом при повышении от 100 до 2000 раз. Таковой пример именуют микрошлифом. Микроструктурный анализ есть самоё детальным, но одновременно с этим и самые трудоёмким и требует от лица, создающего наблюдение, достаточной квалификации.
Микроструктурный анализ разрешает еще более совершенно верно и объективно, чем по кривым твердости, выяснить подлинную глубину закаленного слоя, т. е. слоя со структурой мартенсита.
Мартенситом именуют структуру, соответствующую громаднейшей твердости закаленного металла. По виду различают игольчатый и безыгольчатый мартенсит. Последний характерен для высокочастотной закалки.
Как и при макроисследовании, при изучении микроструктуры подробность, в большинстве случаев, приходится разрушать.
Довольно часто закалка подробностей сопровождается их деформациями, появляющимися благодаря действия внутренних механических напряжений. Измерив величину деформаций, возможно делать выводы о качестве закалки, в особенности в массовом производстве. Величина деформаций при высокочастотной закалке во многих случаях меньше, чем при простой, и имеет закономерный и однообразный темперамент.
Измерение деформаций создают общепринятым измерительным инструментом. Таковой метод контроля высокочастотной закалки не дает исчерпывающего представления о ее качестве, но сами по себе замеры деформаций имеют довольно часто первостепенную важность для механической обработки подробностей.
В массовом либо серийном производстве крайне важно верно выбрать совокупность отбора подробностей для контроля. Как правило практики прибегают к выборочному контролю, контролируя отдельные образцы, от определенной партии. Процент подробностей, отбираемых для изучения, зависит от условий производства.
Так, в случае если изменяются состав стали, условия обработки, напряжение сети и т. п., в случае если закалочный станок не автоматизирован либо изношен, — нужно от каждой партии для опробований отбирать большее число подробностей. В случае если же условия технологического процесса и уровень качества сырья неизменны и нет оснований ожидать больших отклонений качества закалки, то возможно осуществлять контроль лишь небольшой процент от дневной продукции. Так, постоянство и автоматизация производства самого технологического процесса разрешают снизить количество контролируемых подробностей, К примеру, внешнему осмотру подвергаются все 100% подробностей, а травление с поверхности, как процесс более трудоемкий, рекомендуется создавать для одной из 20—50 подробностей, причем последняя Цифра относится к закалке на станках-автоматах.
Контролю твердости на поверхности при важных изделиях нужно подвергать все 100% закаленных подробностей. Наряду с этим для каждой подробности для контроля равномерности закалки нужно создавать не меньше 3—5 измерений в различных точках поверхности.
Для полного металлографического анализа довольно часто берут одну подробность от партии в 200—300 шт., в случае если средняя дневная производительность образовывает приблизительно 100 шт. В случае если же производство более массового характера, а подробности имеют несложную конфигурацию то возможно изучить одну подробность из 1000 шт.
В некоторых же случаях при прекрасно налаженном ходе закалки для серийных малогабаритных подробностей несложной формы используют контроль лишь по излому. Для этого разламывают одну из каждых 20—30 тыс. подробностей. Действительно, данный способ пригоден для подробностей, на которых легко взять излом в нужном сечении и где возможно ограничиться приближенным определением глубины слоя.
В целях упорядочения ведения контроля подробностей, закаленных высокочастотным методом, возможно советовать для участков контроля групповые карты.
В картах имеет суть отразить следующие элементы:
1) марка стали;
2) глубина закаленного слоя по чертежу;
3) глубина закаленного слоя с учетом припуска на шлифование;
4) твердость закаленного слоя с поверхности и на определенной глубине;
5) характер и твёрдость сердцевины предварительной термической обработки;
6) место закалки (и особенные условия распределения закаленного слоя);
7) место контроля;
8) виды массового контроля (твердость, уровень качества поверхности, деформации, наличие микротрещин и т. д.);
9) процент подробностей, подвергающихся контролю на глубину, и микроструктуру закаленного слоя.
Такая карта разрешила бы сконцентрировать в одном месте все технические данные, относящиеся к подробностям, подвергающимся высокочастотной закалке.
ляемые намерено, но повторяющие форму соответствующего участка целой подробности, мы будем именовать моделями. Использование моделей приводит не только к экономии металла, но и формирует удобства при контроле качества закалки. При помощи моделей подбирают форму индуктора, охлаждения и режим нагрева.
В случае если материалом подробности есть дорогостоящая легированная сталь, то первоначально модели изготовляют из недорогой стали и на них подбирают форму индуктора. Затем уже на моделях из заданного сорта стали подбирают электрический и термический режимы, нужные для получения нужной конфигурации и глубины закаленного слоя и его микроструктуры.
В тех случаях, в то время, когда требуется выяснить свойства данной марки стали при закалке, к примеру — закаливаемость, структурные превращения и т. п., закалке подвергаются образцы несложной формы, в большинстве случаев цилиндрической.
Подготовка объекта изучения зависит от того, в чем будет заключаться само изучение.
При изучении поверхности большей частью ограничиваются ручной зачисткой поверхности небольшой корундовой и карборундовой шкуркой.
Для измерения твердости, в особенности при пользовании склероскопом Шора, на измеряемом участке нужно удалить следы механической обработки; в большинстве случаев это делают вручную при помощи наждачного камня.
При подготовке образцов с целью проведения изучения на макро- либо микро шлифах крайне важно верно выбрать плоскость сечения, в которой будут производиться изучения. В большинстве случаев при закалке нужно взять закаленный слой равномерной глубины. Исходя из этого в случае если имеется опасение, что слой по глубине окажется неравномерным, плоскость сечения необходимо выбрать так, дабы эта неравномерность была распознана.
Неравномерность закаленного слоя может иметь место, к примеру, при наличии у подробности галтелей, выступов, вырезов, отверстий, других усложнений и кромок формы. В районе размещения перечисленных элементов, изменяющих дороги прохождения индуктированных токов в подробности, вероятны перегревы и местные нагревы. Для более тщательного изучения через такие места подробности необходимо проводить как минимум несколько взаимно перпендикулярных плоскостей сечения (рис. 1).
Последовательность подробностей сложной конфигурации, к примеру, шестерни, приходится изучить по весьма громадному количеству плоскостей, дабы вое-произвести сложную картину пространственного распределения закаленного слоя.
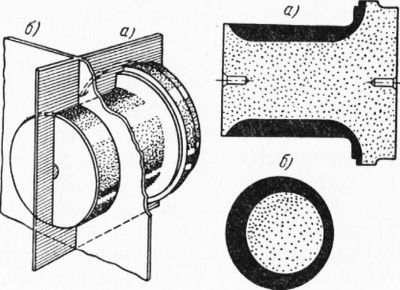
Рис. 1. Выбор плоскости разреза
Для микроисследований из подробности вырезают маленькой количество наряду с этим выбор участка подробности эргономичнее всего проводить по предварительно изготовленному макрошлифу. Особенную важность воображают микрошлифы участков, где возможно беспокоиться перегрева либо недогрева.
Чтобы получить макрошлиф, подробность в первую очередь нужно разрезать. Практически во всех случаях макрошлиф приходится изготовлять как раз по разрезу, а не по излому. При поломке подробности плоскость излома находится произвольно, в то время как при высокочастотной закалке для определения конфигурации закаленного слоя необходимо, дабы плоскость проходила в полной мере в некотором роде.
Сочетание закаленных и незакаленных участков на одной подробности вызывает особенно прихотливую форму излома.
Резка закаленных подробностей может осуществляться разными методами, в зависимости от наличного оборудования и твёрдости материала. Самый обширно используют резку на шлифовальных станках либо на станках особой конструкции при помощи узкого абразивного диска, и на анодно-механических станках. Последний способ есть самый совершенным.
В некоторых случаях, в особенности при больших подробностях, сперва подробность режут автогеном, а после этого на станке срезают некий слой по сечению, отпущенный при нагреве пламенем автогена.
При резке подробностей необходимо заботиться о том, дабы не нарушить структуру металла, взятую в ходе закалки, т. е. дабы при резке температура не превышала 200 °С и не создались громадные упрочнения, содействующие появлению трещин. Следовательно, резку подробности нужно вести при малых скоростях подачи и при интенсивном охлаждении.
Большое значение имеет размер зерна резательного круга. К примеру, круги марки Э60, благодаря весьма небольшого зерна, дают прижоги более сильные, чем круги марки Э46 с более большим зерном. Имеет значение кроме этого и твердость круга.
В большинстве случаев используют круги средней твердости типа С1 и С2, что в марке круга кроме этого указывается.
При несоблюдении этих правил на практике получаются ошибочные результаты. За недостатки закалки принимают трещины и микротрещины, появившиеся в ходе резки, и отпуск и подкалку. Исходя из этого нужно шепетильно инструктировать персонал, осуществляющий резку.
В случае если поверхность разреза подверглась отпуску, а отпуск время от времени происходит на глубину до 2—3 мм, то она покрывается цветами побежалости в зависимости от температуры нагрева; по наличию этих цветов возможно делать выводы о неправильности режима резки (рис. 2).
В случае если нагрев в плоскости реза случился до температуры, превышающей 200 °С, то микроструктура металла уже претерпевает большие трансформации, так что разобраться в итогах закалки делается неосуществимым. Есть вероятность развития и более больших температур, впредь до закалочной. В последнем случае на поверхности реза цвета побежалости неразличимы, поскольку серый цвет, соответствующий температуре выше 500 °С, очень похож на цвет исходного металла.
При травлении для того чтобы макрошлифа получаются тёмные участки, фиксирующие места прижогов (рис. 3).
Рис. 2. Микрошлифы колец шарикоподшипников. Чёрные участки результат отпуска при резке.
Трещины кроме этого позваны неправильным режимом резки.
Во всех тех случаях, в то время, когда поверхность разреза оказалась недоброкачественной (неровной, с уступами, прижогами, трещинами и т. д.) либо оплавленной по окончании анодно-механической резки, ее нужно отшлифовать на плоскошлифовальном станке. К такому же шлифованию прибегают, в то время, когда необходимо приготовить качественный макрошлиф для фотографирования и в то время, когда Для измерения твердости по глубине закаленного слоя нужно обеспечить строгую параллельность верхней и нижней плоскостей шлифа.
При шлифовании направляться выполнять те же предосторожности, что и при резке, чтобы не было прижогов, других дефектов и трещин. Трещины, появляющиеся при шлифовании, имеют основной вид узкой сетки, а прижоги, появляющиеся благодаря биения камня, Дают на макрошлифе пунктир (рис. 4).
Для устранения таких прижогов необходимо обеспечить систематическую правку шлифовального круга.
Рис. 3. Макрошлиф части коленчатой оси: 1 — подкаленный при резке участок; б — закаленный слой; в — исходный материал.
Рис. 4. Недостатки, появляющиеся от станочного шлифования: а — «пунктир»; б — сетка трещин.
В некоторых случаях на поверхности возможно найти местные оплавления либо участки с узким розоватым налетом. Эти показатели означают, что в ходе нагрева в этих местах случился пробой между деталью и индуктором. Розовый налет является слоем , появившийся благодаря конденсации паров меди на поверхности подробности.
Ясно, что в этом случае нужно отрегулировать зазор между деталью и индуктором.
При контроле закаленных подробностей возможно обширно использовать способ травления поверхности. Сущность его содержится в том, что наружная поверхность подробности по окончании обезжиривания и шлифования смачивается особым раствором — реактивом, в следствии чего на поверхности появляется рисунок. Данный рисунок разрешает делать выводы о поверхностной макроструктуре и недостатках закалки.
Обезжиривание возможно создавать любым из известных способов, к примеру, обмывая поверхность спиртом,ацетоном, чистым бензином и др.
Громаднейшее распространение взяли следующие методы травления:
1. Травление персульфатом аммония. Данный реактив используется для обнаружения небольших трещин. Его химическая формула: (NH4)2S208.
Подготовленную поверхность подробности при помощи ваты смачивают 15-процентным водным раствором персульфата в течение 10 мин. После этого обрабатывают 10-процентным водным раствором азотной кислоты и промывают водой. Дабы обезопасисть руки от действия реактивов, вату направляться брать щипцами.
По окончании просушивания фильтровальной бумагой и горячим воздухом выжидают 10—15 мин. и обследуют поверхность при помощи лупы. Трещины выступают в виде тёмных линий. Попутно на ярком фоне незакаленного металла выявляется закаленная территория, имеющая темно-серую окраску.
2. Травление 25-процентным водным раствором азотной кислоты Используется для обнаружения макроструктуры. Поверхность металла смачивается кислотой до потемнения закаленных участков. После этого, как в большинстве случаев, производится промывка и визуальное обследование и сушка поверхности.
Данный реактив кроме этого выявляет трещины.
3. Травление 3-процентным водным раствором азотной кислоты. Используется для обнаружения обезуглероженных участков, и трооститных пятен (рис. 5), каковые образуются при не хватает резком охлаждении в ходе закалки и владеют пониженной твердостью.
Для травления поверхность, подготовленная как в большинстве случаев, смачивается раствором в течение нескольких мин.. На мокрой поверхности трооститные пятна выглядят чёрными, а обезуглероженные участки — белыми на светло-сером фоне закаленной поверхности На сухой поверхности эти пятна мало заметны.
Рис. 5. Трооститные пятна на закаленной поверхности, распознанные методом травления 3-процентным водным раствором азотной кислоты (на рисунке отмечены стрелками).
Как уже было отмечено, цель травления первым и вторым реактивами пребывает в обнаружении на поверхности трещин, каковые смогут появиться либо в ходе закалки либо в ходе последующей механической обработки. Помимо этого, эти реактивы нужны тем, что, выявляя на поверхности территорию закалки, они разрешают осуществлять контроль соответствие ее техническим требованиям.
К примеру, при закалке шейки коленчатого вала, в то время, когда строго заданы расположение и ширина закаленного участка, их возможно скоро выяснить при помощи травления (рис. 6).
Pиc. 6. Картинки, распознанные на поверхности травлением и появившиеся благодаря охлаждения струями закалочной воды: а — пятна, появляющиеся при одновременной закалке без вращения подробности, расположены кроме этого в шахматном порядке, как и отверстия в индукторе; б — рисунок в виде спирали; получается при последовательной закалке с вращением подробности
В некоторых случаях, в то время, когда одна закаливаемая территория находит на другую, закаленную ранее, в зоне смыкания образуется так называемая отпускная полоса, снижающая прочность подробности. Она кроме этого прекрасно выявляется травлением.
Довольно часто на поверхности, протравленной первым либо вторым реактивами, выявляются разного вида картинки (рис. 6). Так, при закалке с одновременным нагревом всей закаливаемой поверхности без вращения подробности время от времени на протравленной поверхности ‘весьма быстро выступают пятна в виде очерченных кружков.
Эти кружки находятся в определенном порядке, в таком же, как и отверстия на внутренней поверхности индуктора, и образуются от остро направленных струй закалочной воды, попадающих на раскаленную поверхность металла.
Рисунок сам по себе не есть, отрицательным показателем, но довольно часто в центре этих пятен выявляются микротрещины (рис. 7). Не смотря на то, что эти микротрещины имеют глубину и незначительную протяжённость, так что при последующем шлифовании подробности на 0,1—0,2 мм они всецело снимаются, все же в таких случаях нужно принимать меры для их устранения, к примеру, снизить давление воды в случае если это не отражается на твердости; возможно кроме этого подогревать закалочную воду. Избежать образования указанных микротрещин возможно и методом применения индуктора соответствующей конструкции
При последовательной закалке с вращением подробности на поверхности время от времени выявляется рисунок в виде перемежающихся весьма узких ярких и чёрных полос, идущих по спирали, каковые появляются благодаря неравномерного попадания водяного душа на раскаленную поверхность металла. Эта неравномерность обусловлена отсутствием водяных струй в месте разреза кольца индуктора, и малой скоростью вращения подробности. В большинстве случаев данный рисунок не связан с какими-либо недостатками в закаленном слое.
Рис. 7. Микротрещины на шейке коленчатого вала, распознанные при травлении персульфатом аммония. Появились в местах падения струй закалочной воды (кружком обведено место, представленное справа в увеличенном масштабе).