Контроль качества продукции в литейных цехах
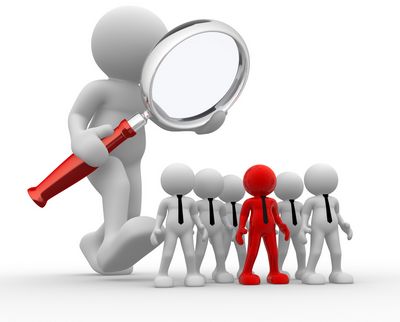
Литейное производство отличается от последовательности вторых производств многоопер а ционностью и разнообразием применяемых в технологическом ходе материалов. Отклонение от требуемого качества одного из материалов либо неправильное исполнение одной из операций может привести к несоответствию качества отливки предъявляемым требованиям. Уровень качества отливки, со своей стороны, воздействует на уровень качества последующих операций металлопокрытий.
Своеобразие литейного производства состоит еще и в том, что большинство его процессов лишена яркой наглядности и происходит при переменных физико-химических условиях. Все это затрудняет и усложняет технический контроль литейного производства.
В литейном производстве подлежат контролю: поступающие в производство главные и вспомогательные материалы; свойства взятых сплавов; модельно-опочная оснастка; формовочные и стержневые смеси; стержни; формы; отливки на разных этапах обработки и изготовления.
Главные и вспомогательные материалы поступают в литейный цех в основном через склады формовочных шихты и материалов. Кое-какие вспомогательные материалы поступают через цеховые кладовые. Задача контроля на этом месте — отбраковка поступающих некондиционных материалов.
Ниже изложены отдельные виды контроля в литейных цехах и их краткое содержание.
Контроль процесса плавки. Способы контроля плавильного процесса зависят от типа рода металла и плавильного агрегата.
Контроль качества сплавов.
Контроль режима заливки. Заливку формы осуществляют контроль по температуре заливаемого металла оптическим пирометром и по длительности заливки — секундомером. Совокупность контроля выборочная; для больших и важных отливок — целой контроль.
Контроль оснастки. Увеличение требований к точности черновых размеров отливок определяет необходимость систематического контроля состояния моделей, коробок, другой оснастки и опок. Чем выше класс точности отливок, тем меньше допускаемые отклонения на периодичность контроля и размеры оснастки.
Контроль качества смесей. Уровень качества смесей, как и исходных материалов, определяется их подготовкой, перемешиванием и шихтовкой.
Свойства смесей — влажность, прочность и газопроницаемость — подвергают систематическому контролю. Методика определения особенностей смесей установлена ГОСТ 2189—78.
Плотность литейных красок контролируют каждые 1,5—2’ч ареометром.
Контроль стержней. Контроль стержней есть предупредительным по отношению к отливкам и одновременно с этим приемочным по отношению к стержням как независимым полуфабрикатам.
Такие недостатки, как осыпаемость, трещины, пережог, определяют внешним осмотром. Влажность больших стержней возможно проконтролировать влагомером либо простукиванием. Шаблоны, используемые для контроля размеров стержней, в большинстве случаев, предельные и только в отдельных случаях, в основном для массового производства, индикаторные.
Контроль качества формы. Уровень качества изготовленной формы в большой- мере определяет уровень качества последующей отливки. равномерность и Степень уплотнения формы определяют особым твердомером, пригодным для проверки горизонтальных, вертикальных и наклонных поверхностей.
Применяя твердомер, возможно организовать действенный контроль плотности набивки форм и добиться резкого уменьшения брака по недостаткам формовки.
Контроль правильности размеров формы распространяется
главным образол на процесс установки стержней; контроль делают как правило с применением шаблонов, совмещающих производственное и контрольное назначение.
Многообразие обстоятельств, талантливых оказывать влияние на уровень качества отливок, обусловливает эффективность статистического способа контроля в литейном производстве.
Задачи контроля метода и статистического анализа в литейном производстве следующие.
1. Обнаружение самые важных технологических факторов, определяющих уровень качества продукции, и главных обстоятельств, воздействующих на эти факторы. Такими факторами при изготовлении отливок являются, к примеру, температура жидкого металла, его жидкотекучесть, газопроницаемость, влажность и прочность форм и т. д. На эти факторы соответственно воздействуют такие переменные размеры, как масса и размеры составных частей шихты, размеры кусков кокса, давление дутья, режим 136 изготовление смесей, давление сжатого воздуха в сети и др. В каждом отдельном случае факторы и воздействующие на них показатели направляться выбирать с учетом изюминок данного цеха, характера литья, основных видов брака.
2. Установление математической обработкой данных солидного числа замеров функциональной связи между технологическими факторами.
3. Установление допускаемых отклонений для контролируемых элементов технологического процесса.
4. Применение статистического способа для постоянного контроля при помощи контрольных графиков, служащих для своевременного предупреждения брака. В этом отношении особенное значение получает верная выборочность контроля, устанавливаемая матанализом.
Виды недостатков литья, обстоятельства их меры и образования предупреждения. Эффективность борьбы с браком литья определяется в значительной мере правильностью диагноза — обнаружением настоящего вида брака отливки, его виновника и причины брака. Лишь верным ответом этих вопросов, составляющих сущность контроля готовых отливок, возможно обеспечить условия для ликвидации появившегося брака и предотвратить появление его в будущем.
Главные виды недостатков литья: спай, недолив (неполная отливка), заливы, наросты, пригар, отбел (чугунное литье), раковины газовые, раковины усадочные, рыхлоты, пористость, раковины земляные, раковины шлаковые, трещины тёплые, трещины холодные, коробление, механические повреждения, пережог и окисление, несоответствие конфигураций и размеров отливок заданным (перекос, разностенность и др.), несоответствие заданным состава металла, микроструктуры и физико-механических особенностей. Более детально недостатки обрисованы в специальной литературе и соответствующих Гостах. Любой из недостатков отливок возможно следствием их комбинации и ряда причин.
самые вероятные обстоятельства происхождения того либо иного недостатка устанавливают с учетом данных приемочного контроля “(изданий шихт, смесей и т. п.), характеризующих состояние отдельных элементов технологического процесса. Меры предупреждения брака зависят от самая вероятной обстоятельства брака. Последней определяются и место происхождения брака и, в соответствии с организационным построением производства, конкретный виновник,
Для действенной борьбы с браком и надлежащего инструктажа виновников громадное значение имеет верно организованная площадка брака. Площадка должна быть местом ежедневного разбора, разъяснения и предъявления брака его виновникам, установления в присутствии виновника меры взыскания, и информации цехового коллектива о взысканиях за брак и поощрениях за его понижение. Работники технического контроля должны быть участниками работы на площадках брака, и участниками всех технологических мероприятий, приобщающих коллективы литейных цехов к самоконтролю при исполнении каждой производственной операции.
самый важным есть оснащение каждой операции нужными регулирующими и контрольно-измерительными устройствами.
Контроль по наружному виду. Контроль отливок по их наружному виду разрешает распознать литейные недостатки (недоливы, наросты, спаи, трещины, поверхностные раковины, пригар и др.), и недостатки отделки отливок (заусенцы, переточки, остатки литниковой совокупности и др.).
Осмотр отливок направляться организовать так, дабы исключить попадание дефектных отливок на последующие операции. Так, конкретно по окончании выбивки целесообразно подвергать отливки первичной разбраковке с отсортировкой явного брака и лишь затем направлять их на предстоящие отделочные операции.
Готовую отливку, предъявленную для приемки ОТК, прежде всего подвергают осмотру по наружному виду. Но во многих случаях осмотр отливок невооруженным глазом есть недостаточным. Тогда применяют лупы разного увеличе-ния.
Для обнаружения небольших внешних пороков, а также микротрещин, используют люминесцентный способ.
Гидравлическое опробование отливок. Отливки, предназначенные для работы под давлением, направляться подвергать опробованию на гидравлическую либо воздушную плотность.
Е единичном производстве для контроля плотности отливок используют отдельные пробки, заглушки, фланцы с стяжными болтами и резиновыми прокладками либо струбцинами, при помощи которых заглушают каждое отверстие в отдельности В условиях серийного либо массового производства плотность отливок контролируют с использованйем особых приспособлений — гидростанков.
По способу опробования различают гидростанки, в которых опробование выполняют при заполнении полости отливки водой (в этом случае недостатки выявляют при образовании течи либо «потении» стенок отливки), воздухом с погружением отливки в воду (о недостатках свидетельствует появление на поверхности пузырьков воздуха). Время от времени погружение испытуемой отливки в воду заменяют смачиванием контролируемой поверхности мыльным раствором.
По методу закрепления отливки станки делятся на ручные, в которых для закрывания отверстий и закрепления отливок применяют винтовые либо эксцентриковые зажимы, и механизированные, в которых для закрепления используют быстродействующие пневматические зажимы.
Конструкция гидростанка обязана снабжать надежное закрывание всех отверстий и, следовательно, возможность проведения опробования при заданном давлении, вольный доступ для осмотра всех контролируемых поверхностей отливки, достаточную производительность механизацией таких операций, как установка отливки, закрывание отверстий, выпуск и подача воды и т. д.
Контроль размеров отливок. Размеры любой отливки включают припуск на механическую обработку: допуски на размеры характеризуют точность изготовления отливки.
Припуском на обработку именуют толщину избыточного слоя металла, назначаемую в отливке в тех местах изделия, где требуется получение чистой и правильной поверхности механической обработкой. Значение припуска определяется классом точности изготовления отливки и имеет только громадное значение в машиностроении, поскольку в значительной степени определяет трудоемкость механической обработки. снижение точности объёма и Повышение заготовок механической обработки, имеющее громадное народнохозяйственное значение, обусловили ограничение допусков и припусков на литье соответствующими ГОСТами.
Чертеж отливки должен быть создан на основании чертежа готового изделия с внесением уточнений, определяемых разработкой литейного производства. Для единого приемочного документа в чертеж в большинстве случаев включают и другие эти из предусмотренных техническими условиями для полной чёрта требуемого качества отливки.
Способы контроля геометрических размеров отливок определяются только типом производства.
В условиях единичного производства главной контроль размеров отливки делают разметкой, при которой из заготовки по существу «выкраивают» годное изделие. В этом случае кроме того не в полной мере правильную заготовку (отливку) возможно применять при верном разделении имеющихся на отливке припусков.
Механическая обработка в крупносерийном и массовом производстве характеризуется применением особого оборудования, приспособлений и кондукторов, совершенно верно определяющих положение заготовки довольно режущего инструмента при механической обработке, и заблаговременно вычисленными режимами резания. В этих условиях контроль размеров отливок получает особенное значение и обусловлен следующими требованиями: контроль должен быть стремительным и правильным; проверка размеров должна быть объективной. Применение в таких условиях универсального измерительного инструмента делается затруднительным, и его все чаще заменяют особыми контрольно-приспособлениями и измерительными инструментами.
самые простые средства измерения отклонений фактических размеров от номинальных — скобы, пластины, кольца, пробки, шаблоны, т. е. твёрдый предельный измерительный инструмент. Таковой инструмент возможно обширно использовать при контроле геометрических размеров отливок, не подвергаемых механической обработке, но обусловленных определенными допусками по условиям сборки либо эксплуатации.
При контроле в отливках размеров, которые связаны с обрабатываемыми поверхностями, нужно выяснить, обеспечен ли заданный припуск на обработку в допустимых пределах (т. е. не останется ли чернота по окончании обработки), равномерно ли распределен заданный припуск по всей обрабатываемой поверхности, и нет ли чрезмерного повышения припуска на обработку, что может привести к поломке инструмента, нарушению установленного режима резания и т. п. В этих обстоятельствах использование предельного измерительного инструмента не хватает, и его приходится заменять особыми контрольными приспособлениями. Контрольные приспособления для проверки отливок должны снабжать: исполнение всех контрольных измерений от базисных мест, принятых для механической рбработки; возможность отсчета отклонения контролируемого размера либо припуска на обработку или возможность определения, находятся ли они в допустимых пределах; исполнение всех контрольных измерений с одной установки контролируемой отливки; большое упрощение процесса измерений Для применения работников низкой квалификации; достаточно высокую производительность; правильные и неизменные показания; смены и лёгкость регулирования изнашиваемых ча-§ 2. КОНТРОЛЬ КАЧЕСТВА ПРОДУКЦИИ В КУЗНЕЧНО-ШТАМПОВОЧНЫХ ЦЕХАХ
классификация и Виды брака поковок. Для кузнечно-штам-повочного производства свойственны следующие главные виды брака: от исходного материала, при резке заготовок, нагревании, штамповке, очистке окалины и термической обработке. Нижеприведенная классификация брака разрешает независимо от того, на каких стадиях брак найден, отнести его к той операции, которая явилась обстоятельством его происхождения:
— от исходного материала — риски (небольшие, открытые царапины, просматриваемые «до дна»), волосовины (узкие трещины, не просматриваемые «до дна»), заусенцы, плены (застывшие брызги жидкого металла), расслоение, шлаковые включения, несоответствие марки либо состава стали, фло-кены (скопления либо гнезда небольших трещин), несоответствующие параметры профиля материала;
— при резке заготовок — косой срез, искривление и заусенцы финиша заготовки, неотёсанный срез либо скол с вырывом металла, торцовые трещины, несоответствие заготовки по длине;
— при нагревании заготовок — перегрев, пережог, окалина; при штамповке — вмятины (следы заштампованной окалины), забоины, «неполная» фигура, недоштамповка, перекос, зажим, заусенцы, кривизна, отклонение по длине;
— при термической обработке поковок — недостаточная либо повышенная твердость, «пестрота» твердости (большое различие значений твердости на одной поковке), закалочные трещины, нехорошая обрабатываемость режущими инструментами;
— при очистке окалины — остаточная окалина, перетравлен-ность, забоины при очистке, чернота, вмятины, узкая стена.
Советуют следующие способы исправления дефектных поковок. Заусенцы, волосовины, зажимы и закаты затачивают наждачным кругом либо вырубают зубилом. «Неполную» фигуру (в случае если незаполнение незначительно) и маленькие вмятины исправляют перештамповкой в новом штампе либо заваркой. Недоштампованные заготовки целесообразно обрабатывать в механических цехах отдельными партиями с предварительной обдиркой.
Перештамповка таких заготовок нежелательна, поскольку наряду с этим возможно взять окончательный брак заштампов-кой снова появившейся окалины. В случае если поковки не подвергают последующей обработке резанием, то для неответственных подробностей недоштамповку возможно исправлять одним повторным нагревом (для перевода избытка металла в окалину).
Перекос возможно исправить перештамповкой лишь при правильной установке бабы в направляющих, причем в обязательном порядке в штампе с замками; в другом случае данный недостаток неисправим. Незначительный перекос в поковке возможно ликвидировать заточкой (выравниванием) базисных мест. Кривизну исправляют прав-142 кой в холодном состоянии в штампе (как й верном прессе) либо вручную с подгонкой по шаблону либо контрольному приспособлению.
Перегрев исправляют нормализацией, которая нужна практически для всех штампованных поковок. Повышенные и недостаточные вязкость и твёрдость поковок ликвидируют повторной термической обработкой.
Перештамповку, правку и повторную термическую обработку создают отдельными партиями на главном оборудовании цеха (в общем потоке). Недостатки исправляют в особом дефектном отделении цеха, которое должно быть изолировано от главного грузопотока поковок.
Пережог, расслоение, закалочные трещины, значительное незаполнение и торцовые трещины фигуры относятся к исправлению и окончательному браку не подлежат.
Для контроля состава стали делают анализы (химический в лаборатории,, спектральный на стилоско-пе, сравнительный по искре), определяют марку стали термоэлектрическим способом. Соответствие марки материала поковок техническим условиям чертежа осуществляют контроль проверкой накладных, сертификатов на поступившие в цех заготовки, установкой в штампах условного клейма, рассортировкой и проверкой поступающих на приемку либо механическую обработку поковок, целым контролем твердости по окончании термической обработки поковок.
Для контроля исполнения режимов термической обработки термические печи оборудованы пирометрами (либо термопарами), электрическими часами и механизмами для автоматического толкания поддонов; ведут издание термических печей для регулярной записи загружаемых режимов и изделий их обработки. Уровень качества поковок по окончании термической обработки осуществляют контроль следующими методами: опробованием на твердость по Бринеллю; металлографическим анализом поковок; механическими опробованиями; магнитными способами контроля кристаллического состояния.
Внешние недостатки осуществляют контроль визуально. Скрытые недостатки выявляют по окончании соответствующей термической обработки и очистки поверхности от окалины (а время от времени и по окончании механической обработки).
Глубину залегания недостатка осуществляют контроль: местным шлифованием недостатка на допустимую глубину с повторным осмотром; местной вырубкой недостатков зубилом; целым шлифованием недостатков наждачным камнем в пределах допустимого ослабления рабочего сечения подробности; полной вырубкой недостатка ручным либо пневматическим зубилом. Осмотр по окончании вырубки делают с применением местного травления вырубленных мест концентрированной серной кислотой. Вырубку недостатков делает производственный персонал, диагностику по окончании выруб-кн — контролер.
Для отклонений расстояния и определения зазоров от опоры либо контрольной поверхности до поверхности поковки при разметке либо проверке в несложных контрольных приспособлениях используют предельные пластины. Главные приспособления для измерения отклонений: круглый индикатор, секторный индикатор, предельный глубиномер, электрические измерительные средства.
Способы контроля размеров поковок. Новую конструкцию штампа осуществляют контроль осмотром формы заусенца на первых поковках, травлением первых поковок для обнаружения зажимов, проверкой микроструктуры по главным сечениям, подробной разметкой первых поковок.
Геометрические размеры окончательного ручья штампа контролируют (универсальным инструментом) разметкой контрольной отливки, первой и последней поковок.
Правильность установки штамповочного набора (ковочного и обрезного штампов) осуществляют контроль осмотром поковки до и по окончании обрезки заусенца, травлением первых поковок в растворе серной кислоты для обнаружения зажимов.
Перекос (смещение поковки) по линии разъема штампов осуществляют контроль осмотром поковки до обрезки заусенца, разметкой верхней половины фигуры при установке по нижней половине, проверкой боковым шаблоном, измерением на контрольных приспособлениях, измерением штангенциркулем разности диаметров по разъему.
Длину поковки осуществляют контроль прутковым шаблоном с предельной выточкой, профильным шаблоном, профильным двусторонним шаблоном, контрольным приспособлением.
Изгиб (кривизну) поковки определяют катанием на плите, и проверкой бокового смещения от установочной оси в контрольном приспособлении, биения цилиндрической поверхности при вращении подробности, биения в один момент в нескольких сечениях по длине.
Коробление плоскости измеряют глубиномерами с рычажной передачей.
Отклонение плоскостей от параллельности и перпендикулярности контролируют устройствами, включающими глубиномеры.
Угловые характеристики осуществляют контроль разметкой контрольными приспособлениями и угломером с применением вращающихся призм и качающихся коромысел.
Фактический припуск на механическую обработку контролируют измерением припусков на плоской, конической, цилиндрической, сферической и криволинейной поверхностях посредством особых приспособлений.