Контроль суспензии
Изменение качества керамических форм (их прочности, газопроницаемости либо теплового расширения) сигнализирует в большинстве случаев о нарушениях технологического процесса. Исходя из этого нужно прекрасно знать влияние факторов, каковые приводят к нарушению четкости разработки, в особенности при массовом выпуске продукции.
Потому, что в ЧССР для производства оболочковых форм применяют в основном пылевидный кварц, кварцевый песок
И ЗТиЛсиЛиКаТ, то контроль суспензии направлен на изучение особенностей этих исходных материалов.
На прочность керамических форм воздействуют следующие параметры:
– величина и форма зерен огнеупорного порошка в суспензии и обсыпочного материала;
– концентрация условной двуокиси кремния в суспензии;
– количество связующего в суспензии;
– их нанесения сушка и технология слоёв.
Информацию о влиянии величины зерен пылевидных огнеупоров на особенности керамических форм рассмотрены весьма детально в технической литературе. Наряду с этим указывается, что верный промежуток зернистости пылевидного огнеупора относится к главным факторам, определяющим его прочность, и что на прочность керамических форм воздействует не только величина, но и форма частиц.
В большинстве случаев считается, что при крупнодисперсном пылевидном ог-неупоре керамические формы имеют меньшую прочность при изгибе, чем при мелкодисперсном. С уменьшением величины зерна и с повышением его удельной поверхности растет прочность керамических форм, но до определенной величины, а после этого снова понижается. Это обосновывают данные исследований, совершённых на заводе ZPS г. Готвальдов.
При постоянных рабочих условиях (постоянной вязкости суспензии, зернистости обсыпочного материала, концентрации условной двуокиси кремния в связующем, при постоянной технологии нанесения слоев, сушке и прокаливании керамических форм) испытывали на прочность при изгибе керамические формы, изготовленные из пылевидного кварца с разным распределением зернистости и с разной удельной поверхностью. Из результатов видно, что большая прочность керамических форм достигается при удельной поверхности от 5000 до 8000 см2/г.
Пылевидный кварц изготовляют методом размола кварцевого-песка. При размоле происходит постепенное измельчение зерен песка (в следствии их истирания и раскалывания). При долгом размалывании частицы становятся весьма небольшими, кроме того практически коллоидными.
В зависимости от метода и времени размола образуется разное количество коллоидных частиц. Такие частицы имеют весьма громадную поверхность, которая владеет так называемой механической активацией. Так как методы размалывания поставляемого пылевидного кварца разны (влажные либо сухие), то количество коллоидных частиц будет различным. Влияние коллоидных частиц пылевидного кварца на прочность керамических форм при изгибе было изучено на умелых примерах.
Наносили слои из смеси пылевидного кварца пыли и известной зернистости с высоким содержанием коллоидного кварца. Связующим был гидролизованный раствор этилсиликата с содержанием 115 г/л условной двуокиси кремния.
Опытные образцы изготовляли в постоянных условиях (нанесение слоев, прокаливание и сушка). Пыль представляла собой практически коллоидный кремнезем — отход при производстве кристаллического кремнезема с величиной частиц до 1 мкм.
Данные исследований продемонстрировали, что с повышением доли коллоидного кремнезема в суспензии до 5% прочность оболочек на изгиб понижается медлительно, после этого стремительнее, а при 15% образцы фактически не имели прочности.
В соответствии с литературным данным прочность на изгиб мало зависит от обсыпочного материала с малым разбросом зернистости. Но в случае если разброс зернистости велик, то влияние на прочность больше. Отмечается кроме этого, что на прочность керамических форм воздействует и форма зерен.
Практический опыт продемонстрировал, что зернистость кварцевого песка для обсыпки в пределах 0,06—0,5 мм не воздействует на прочность оболочковой формы в тех случаях, в то время, когда величина зерна более либо менее постоянна. С повышением в песке весьма небольших частиц прочность формы увеличивается.
Соотношение между величиной зерна и качеством суспензии обсыпочного материала определяется вязкостью суспензии. Керамическая форма из суспензии с большой вязкостью, обсыпанная небольшим песком, будет иметь большое содержание суспензии если сравнивать с формой, изготовленной из суспензии с низкой вязкостью, но обсыпанной большим песком.
Суспензия для этих образцов имела вязкость 40 ± 2 с (при 24 °С) по воронке Форда (диаметр отверстия 6 мм). При весьма густой суспензии (65—70 с), т. е. при высоком соотношении суспензии к массе обсыпочного материала, образуется форма с низкой прочностью. Это, возможно, возможно растолковать тем, что при гелеобразо-вании суспензии, в которой довольно мало песка, происходит ее растрескивание. Сетка трещин есть обстоятельством понижения прочности керамических форм.
Прочность на изгиб керамических форм, изготовленных обсыпкой кварцевым песком с величиной зерна 0,2—0,4 мм с возрастающей вязкостью обмазки, приведена в табл. 79.
Обсыпочный небольшой кварцевый песок кроме этого воздействует на прочность керамических форм при изгибе. Для густой суспензии не пригоден небольшой обсыпочный песок, поскольку на слоях керамической формы таковой песок не хорошо держится и не снабжает хорошую сообщение отдельных слоев. Керамические формы из таких слоев имеют низкую прочность.
Вязкость суспензии составляла 70 ± 2 с по воронке Форда диаметром 6 мм.
Значительное влияние на прочность при изгибе керамических форм оказывает концентрация условной двуокиси кремния в связующем. В работе указывается, что прочность силли-манитовых керамических форм увеличивается с повышением в гидро-лизованном растворе этилсиликата содержания условной двуокиси
кремния. Это же относится и к керамическим формам из кремнеземистых материалов.
Вязкость суспензии при всех концентрациях условной Si02 однообразна и образовывает 30 ± 2 с при 22—24 °С.
Зернистость обсыпочного песка была в пределах 0,1—0,3 мм (опробования проводили на заводе ZPS г. Готвальдов).
На газопроницаемость керамических форм воздействуют следующие факторы: форма и величина зерна пылевидного огнеупора и обсыпочного материала; тип и концентрация жидкого связующего; время и температура прокаливания керамических форм.
Газопроницаемость понижается с увеличением дисперсности пылевидного огнеупора (это относится к пылевидным огнеупорам по большому счету). Подтверждением этого являются результаты опробований корундовых форм, изготовленных из суспензии, жёсткой фазой которой являлся неестественный пылевидный корунд разной зернистости. Концентрация условной SiO, в связующем составляла 20% (ZPS г. Готвальдов).
Вязкость суспензии при 20—24° С была 18—20 с (по воронке Форда). Для опытов применяли огнеупорный порошок корунда В К 280-320 и М32. В качестве обсыпочного материала использовали корундовый песок ВК 36.
Критерием газопроницаемости являлась пропитываемость прокаленных керамических форм по CSN 726010. Результаты измерений представлены в табл. 83.
Величины пропитываемости не отражают газопроницаемость, определенную соответствующим измерением количества воздуха, проходящего через материал в единицу времени под постоянным давлением. Пропитываемость характеризует лишь открытые поры (связанные с поверхностью), в каковые может пробраться жидкость. По размерам пропитываемости возможно делать выводы только о качественном трансформации газопроницаемости.
Влияние зернистости обсыпочного материала на газопроницаемость керамической формы из молохита обрисовано в работе. В соответствии с сообщениям авторов данной работы газопроницаемость керамических форм возрастает с повышением величины зерна обсыпочного материала лишь до определенной величины, а после этого с повышением крупности зерна опять понижается, в особенности при суспензиях с высокой вязкостью.
Понижение газопроницаемости керамических форм с неотёсанным обсыпочным материалом разъясняется тем, что между его частицами имеются свободные пространства, в каковые при повторном погружении легко пробралась суспензия. Особенно это проявляется в тех случаях, в то время, когда суспензия весьма вязкая, не вытекает из зазоров и они всецело ею заполняются. Подобные опробования были совершены на ZPS г. Готвальдов и с кварцевыми керамическими формами.
Вязкость суспензии с пылевидным кварцем составляла 30 ± 2 с при 22—24° С по воронке Форда.
О влиянии качества связующего на газопроницаемость керамических форм сообщается в работе. Газопроницаемость керамических форм из суспензии на гидрозолях меньше, чем газопроницаемость форм, изготовленных на этилсиликатных связующих с органическими растворителями.
Опробования с гидрозолем Si02 на заводе ZPS г. Готвальдов продемонстрировали, что пористость керамических форм, определяемая пропи-тываемостью, существенно выше, чем пористость керамических форм из алкозолей. Из этого направляться, что газопроницаемость форм с гидрозольными связующими должна быть не ниже газопроницаемости формы с этилсиликатными связующими. Такая несогласованность с литературными разрешёнными может быть растолкована разным характером связующей пленки.
Связующим при этих опробованиях был Ludox SM40 с весьма небольшой коллоидной дисперсией Si02 (мельче, чем имеет связующее Syton 2). Наполнитель суспензии — пылевидный кварц, обсыпочный материал — кварцевый песок. Согласно данным работы, огнеупорным материалом был молохит.
Изучения продемонстрировали, что газопроницаемость, определенная по пропитываемости, увеличивается, в случае если смешиваются два огнеупорных материала с разной формой зерна, причем прочность на изгиб керамических форм не понижается. Пропитываемость керамических форм, изготовленных из смеси пылевидного кварца и молотого корунда зернистостью 280/380 с алкогольным связующим, содержащим 118 r/л условной двуокиси кремния, по окончании прокаливания была более высокая.
Увеличение газопроницаемости керамических форм подтвердилось и при практическом опробовании на отливках.
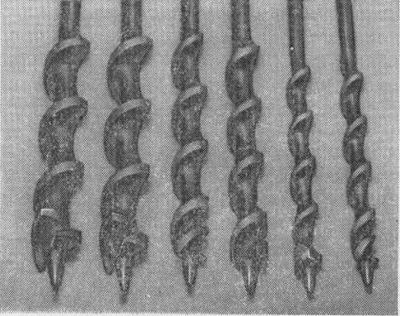
Рис. 1. Сверла для дерева, отлитые в формах из кварца рундом
При длительности прокаливания и повышении температуры прочность керамических форм увеличивается. Газопроницаемость увеличивается лишь в том случае, если в суспензии нет веществ, снижающих температуру плавления огнеупорных материалов. В другом случае происходит понижение газопроницаемости керамических форм.
В изучениях, совершённых на заводе ZPS г. Готвальдов, изучали влияние разработки на наиболее значимые особенности, такие, как прочность на газопроницаемость и изгиб. При простом изготовлении керамических форм для первых слоев применяли более жидкую суспензию, а для более густую. Для жидкой суспензии использовали небольшой обсыпочной материал, для густой — большой.
Керамические формы возможно изготовить кроме этого погружением блока сперва в жидкую, а по окончании стекания избытка — в густую суспензию. Цель опробований — проверить, воздействует ли значительно такая разработка на газопроницаемость и прочность керамических форм.
Из суспензии, складывающейся из пылевидного кварца и гидролизо-ванного раствора этилсиликата с концентрацией 115 г/л условной кварцевого песка и двуокиси кремния в качестве простого материала, изготовляли опытные образцы четырьмя разными методами при нанесении слоев:
1) первый слой — жидкая суспензия, обсыпка небольшим песком. Остальные слои — густая суспензия, обсыпка большим песком;
2) первый слой — жидкая суспензия, обсыпка небольшим песком. Второй слой — густая суспензия, обсыпка большим песком. Остальные слои — так же, как первый слой;
3) первый слой — густая суспензия, обсыпка [крупным песком. Остальные слои—жидкая суспензия, обсыпка весьма небольшим песком;
4) все опытные образцы сперва погружали в жидкую суспензию, а по окончании стекания ее избытка — в более густую; обсыпка большим песком. Вязкость суспензии определяли по вороке Форда с отверстием диаметром 6 мм при 21—23° С.
В второй серии опытов контролировали влияние выдержки модельного блока в суспензии и времени стекания ее избытка перед обсыпкой на те же свойства керамических форм. Из данных табл. 87 направляться, что трансформации в технологии не воздействуют значительно на особенности керамических форм.
Изучили кроме этого влияние вязкости суспензии при постоянных условиях на газопроницаемость керамических форм при разных температурах (табл. 88). Из этих данных видно, что с увеличением вязкости суспензии газопроницаемость оболочки значительно снижается при всех вариантах сушки форм.
Толщина керамических оболочек была постоянной, равной 4,5 мм (±5%).
Газопроницаемость оценивали по прохождению количества газов (в см3) через 1 см2 поверхности керамической формы за 1 мин.
Вторыми технологическими факторами, каковые воздействуют на фундаментальные особенности керамических форм, являются сушка слоев, температура и продолжительность прокаливания. Прочность керамических форм с наполнителем—пылевидным кварцем при сушке на воздухе образовывает 3,1—3,3 МПа; по окончании отверждения аммиаком — лишь 1,48—1,56 МПа. В качестве связующего применяли гидролизованный раствор этилсиликата с разбавителем — спиртом.
У керамических форм, изготовленных из суспензии с гидрозолем кремнезема, кроме этого происходит изменение прочности, в случае если их отверждают химическим методом вместо спокойной сушки на воздухе. В табл. 89, согласно данным британской литературы [16], даны для сравнения свойства керамических форм из молохита и гидрозоля (SYNTON 2х) с 30% Si02, высушенных на воздухе и отвержденных химическим методом.
Громаднейшую прочность имели керамические формы с гидрозолем Si02, каковые высушивались нормально на воздухе.
Контроль суспензии ограничивается измерением вязкости. В большинстве государств вязкость суспензии определяют по времени истечения суспензии из воронки Форда типа В либо из вискозиметра Zahn . Крайне редко (в соответствии с литературным данным) измеряется динамическая вязкость
в сантипуазах на вращающемся вискозиметре Брукфильда.
В ЧССР применяют воронку Форда. размеры и Форма таковой способ и воронки измерения в ЧССР, как и в некоторых вторых государствах, нормализованы.
Рис. 2. Схема усовершенствованного вискозиметра Zahn
Замеренные размеры вязкости должны быть неизменно дополнены данными о величине отверстия температуры и воронки при определении вязкости.
В Англии диаметр отверстия воронки обозначается цифрой, которая ставится у буквенного обозначения типа воронки Форда — воронки В2, В3, В4, Въ.
Вискозиметр Zahn имеет сменные втулки с пятью разными диаметрами. При определении вязкости по воронке Форда за финиш измерения принимают момент, в то время, когда струя суспензии прерывается, переходя в отдельные капли; при измерении вязкости вискозиметром Zahn окончанием измерения вычисляют момент времени, в то время, когда на понижающемся уровне суспензии показывается острие стержня, установленного на дне воронки.
Ответственным причиной при измерении времени истечения суспензии есть температура, поскольку с ее трансформацией изменяется и время истечения. По данным работы время истечения существенно уменьшается при увеличении температуры. Так, в случае если время истечения суспензии из воронки Форда В4 при 26° С образовывает 130 с, то вязкость понижается при увеличении температуры до 36° С до 96 с.
Время истечения суспензии имеет, конечно, объективное значение лишь при условии, что состав связующего и зернистость пылевидного огнеупора не изменяются. В другом случае суспензия при однообразном времени истечения будет иметь разные соотношения между пылевидным огнеупором и связующим и изготовленные керамические формы будут иметь разные особенности. Исходя из этого информацию о вязкости суспензии должны в любой момент сопровождаться сведениями о концентрации условной Si02 в связующем, и о зернистости и составе пылевидного огнеупора либо о его величине удельной поверхности.
С повышением концентрации условной Si02 в жидком связующем и величины поверхности пылевидного огнеупора при постоянном отношении связующего и пылевидного огнеупора время истечения суспензии будет возрастать.
Из анализа всех этих условий, воздействующих на вязкость суспензии, направляться, что вязкость не может быть определяющим причиной для оценки качества керамической формы. Исходя из этого изыскивают методики, каковые разрешили бы определить зависимость качества керамических форм от их газопроницаемости и прочности.
Контроль исходных материалов для того чтобы. В предыдущей главе был рассмотрен последовательность факторов, каковые влияют на уровень качества керамических форм. Установлено, что уровень качества керамических форм зависит в первую очередь от стандартного качества применяемых исходных материалов.
Значит, одним из наиболее значимых этапов входного контроля есть контроль всех исходных материалов. Исходя из этого исследователи всех государств стремятся создать производственные методы опробования исходных материалов для осуществления стремительного и правильного контроля производства керамических форм.
Контроль пылевидного кварца пребывает в определении влажности, количества примесей, зернистости и щёлочности. Громаднейшая допускаемая влажность 1% (если она выше, нужно пылевидный кварц сушить). Содержание примесей в пылевидном кварце должно быть минимальным; по данным работы молотый p-кварц, применяемый в Соединенных Штатах, складывается из 99,8% Si02 и примесей: 0,11% А1203, 0,033% Fe203, 0,022% ТЮ2 и СаО и MgO (следы).
Кварцевые порошки, применяемые в ЧССР, не отличаются таковой чистотой. Содержание в них А1203 и Fe203 не редкость выше. Так как эвтектика с низкой температурой плавления в совокупности Si02—А1203 образуется при 5% А1203, то при нагреве кварца до 1300° С фактически не образуется соединений с низкой температурой плавления, а лишь жёсткие растворы [20]; это не воздействует на огнеупорность и на газопроницаемость керамических форм, содержащих 0,25—0,30% А1203 либо Fe203.
Но это может сказаться на хрупкости керамических форм, поскольку Fe203 при температуре 575—900° С диффундирует в кристаллическую решетку Si02. Содержание магния и окислов кальция в пылевидном кварце ЧССР не редкость больше указанного.
Совсем не допускается содержание элементарного железа которое окисляется в кислой среде жидкого связующего и сдвигает рН до неустойчивой области, чем приводит к преждевременному гелеобразованию связующего. Живучесть суспензии наряду с этим уменьшается. При прокаливании керамических форм железо окисляется, а его соединения с кислородом (FeO, Fe203) образуют с Si02 соединения с низкой температурой плавления.
Это сопровождается возникновением недостатков на поверхности отливок.
Количество щелочных примесей в наполнителе должно быть минимальным. Высокая щелочность уменьшает живучесть суспензии. Щелочность возможно снизить увеличением содержания кислоты в суспензии по эквиваленту, соответствующему количеству, потребному для связывания ионов Са++ или других веществ, повышающих концентрацию ионов ОН”.
Опыт продемонстрировал, что щелочность, вызываемая СаО при его содержании до 0,035%, не сокращает живучесть суспензии. Щелочность определяют кипячением навески пылевидного кварца в определенном количестве кислоты децинормальной концентрации. Неизрасходованную кислоту оттитровывают децинормальным раствором едкого натра.
Кислоту, израсходованную для нейтрализации растворенных щелочей, пересчитывают на содержание СаО (в %).
По CSN 721531 зернистость пылевидного огнеупора определяют просеиванием на ситах по CSN 721263; небольшие частички (до 0,06 мм) определяются седиментационными опробованиями по Andreasen либо Casagrand (CSN 721127). Эти методы простые, но требуется долгое время опробования для того, чтобы получить верные и воспроизводимые результаты.
Долю небольших частиц возможно выяснить и другими методами. Имеются сообщения о проведении ситового анализа и весьма небольших огнеупорных порошков — до величины зерна около 2 мкм; наряду с этим используют железные плетеные сетки. Ситовой анализ выполняют мокрым методом и результаты сравнивают с результатами вторых способов.
самые простым есть метод определения посредством седиментационных весов; на них определяют количество частиц, осадившихся за определенное время. Особые компании изготовляют седиментационные весы с автоматическим регистрированием результатов взвешивания, как, к примеру, седиментационные весы компании Sartorius-Werke G. М. В. Н. (Геттинген, ФРГ).
Долю небольших частиц в пылевидном огнеупоре возможно выяснить и турбидиметрическим методом, основанным на измерении интенсивности света при прохождении его через дисперсионную среду с частицами пылевидного огнеупора. Анализ проводится при помощи фотоэлектрического турбидиметра Вагнера. Преимущество турбидиметрического метода если сравнивать с остальными седиментационными методами пребывает в значительном сокращении времени анализа.
Для получения правильных кривых крупных величины частиц и распределения зерна рекомендуется комбинировать турбидиметри-ческий метод с седиментационным взвешиванием. Седиментационные способы в большинстве случаев не разрешают совершенно верно определять частицы менее 2 мкм. Седиментация таких небольших частиц продолжается продолжительное время, и определенные размеры не правильны благодаря броуновского перемещения молекул.
Величину зерна возможно определять и при помощи вычислительных автомобилей, к примеру прибором Coulter-Counter. К суспензии разбираемого порошка додают электролит (NaCl), дабы она была электропроводна, и измеряют сопротивление между двумя сосудами, поделёнными капиллярной стенкой. По этому капилляру проходит суспензия. При проходе каждой частицы возрастает сопротивление, изменение которого регистрирует электронный прибор.
Большое повышение сопротивления характеризует величину зерна. В случае если известна величина зерна, то возможно выяснить величину удельной поверхности, и напротив.
Чаще всего для измерения удельной поверхности частиц используют методы, основанные на адсорбции мономолекулярных слоев. Самым простым есть определение удельной поверхности частицы адсорбцией азота в соответствующих устройствах.
Метод BET применяют лишь для частиц с довольно громадной удельной поверхностью. Для кремнезема, к примеру, таковой поверхностью владеют частицы размером менее 20 мкм.
Не считая ранееприведенных устройств для измерения величины зерна зарубежные компании предлагают большое количество разных устройств. Кое-какие из них трудятся в автоматическом режиме, такие, как гранулометр TURZ62 производства VEB Transformatoren und Rontgenwerke (Дрезден, ГДР); седиграф — модель 5000 производства Micromeritics Corp. (США); фотоседиментометр производства Microscal ЛТД. (Лондон, Англия); турбидиметр производства Evans Electro Scienium ЛТД. (США); непроизвольный анализатор величины зерна SF 82, ASTMD-422 производства Matodo Testing Machine Co. (Токио, Япония).
Дабы контроль зернистости пылевидного кварца был целесообразным, требуется знать допускаемые отклонения в размерах зерен. По опыту ZPS г. Готвальдов выяснилось удачнейшим следующее распределение величины зерна в пылевидном кварцевом порошке:
Контроль этилсиликата и спирта. В большинстве случаев контроль этилсиликата 40 ограничивают определением плотности пикнометром, которая характеризует содержание условной двуокиси кремния,и определением концентрации соляной кислоты способом титрования. Рекомендуется кроме этого определять содержание фракции с температурой кипения до 110 °С и содержание низкомолекулярных веществ.
Для этилсиликата 40 производства ГДР (завода VEB Chemie-Werk Niinch-ritz) по стандарту TGL 21405 свойственны следующие размеры: плотность при 20° С 1,04—1,06 г/л, температура воспламенения 60° С, содержание Si02 38—42%, НС1 не более 0,1%, низкомолекулярных веществ не бол ее 15%. Это чистая несмешиваемая с водой и смешиваемая со спиртом в любом соотношении жидкость, смесь этокси-полисилоксанов (в основном додекаэтоксиполисилоксанов).
Согласно данным завода ZPS г. Готвальдов в этилсиликате 40 возможно до 8% фракции с температурой кипения до 110 °С.
Изготовители советуют оценивать пригодность этилсиликата для изготовление связующего определением времени геле-образования. Данный параметр определяют следующим образом. В пробирке смешивают последовательно 10 мл пробы этилсиликата с 2 мл этилового спирта и 4 мл концентрированной соляной кислоты.
Раствор в пробирке шепетильно перемешивают, дабы он стал гомогенным, и после этого пробирку с раствором устанавливают в термостат, где выдерживают при 20 ± 0,5° С. Начало гелеобра-зования определяют по моменту весьма медленного течения раствора при наклоне пробирки. Время гелеобразования — это промежуток от начала опробования до полного гелеобразования (прекращение перемещения раствора при наклоне пробирки).
В безводном этиловом спирте (CSN 660835), денатурированным добавкой 2% технического бензина, определяют содержание спирта спиртометром. При производственных опробованиях рекомендуется определять пригодность спирта для изготовление связующего следующим образом: 200 мл этилсиликата разбавляют 100 мл’ испытываемого этилсиликата спирта, додают 20 мл воды и 1 мл концентрированной соляной кислоты. Всю смесь прекрасно перемешивают интенсивным встряхиванием колбы, в которой находится жидкость.
В случае если температура раствора начинает существенно увеличиваться (40—45° С), то это говорит о прохождении гидролиза. В один момент подобно определяют пригодность этилсиликата для изготовление связующего.
Все опробования исходных материалов детально обрисованы в особой литературе.
Рис. 4. Оптимальный гранулометрический состав пылевидного кварца