Литейное производство
В литейном производстве исходные железные материалы расплавляют, перегревают и заливают в формы. В течение определенного времени теплота отводится в вохдух. В следствии этих процессов формируется отливка, которая, но, редко есть независимым конечным изделием. Чаще отливки входят составными частями в изделия практически всех отраслей металлообрабатывающей индустрии.
Литые подробности имеются чуть ли не во всех автомобилях.
Как и всякое производство, производство отливок осуществляется в качествах количества и качества.
В соответствии с назначением отливки к ее форме и качеству предъявляются определенные требования. Исходя из этого форма отливки может входить в понятие качества. Назначение отливки разрешает кроме этого приближенно оценить количество.
В конструкторских бюро каждый день проектируют новые отливки. Уже пара лет назад в ГДР было зарегистрировано около 1 млн. разных отливок. Это число показывает, насколько велико их разнообразие.
Все отливки проходят через жидкое состояние. Но область применения каждой из них определяется ее служебными особенностями, каковые смогут быть очень разными. Помимо этого, отливка обязана владеть еще технологическими особенностями как для собственного изготовления, так и для обработки, к примеру резанием, определенной поверхностной обработкой И т. д.
Служебные особенности интересуют потребителей отливок, технологические — изготовителей. Обе группы требований не всегда возможно привести к неспециализированному знаменателю, к примеру кое-какие отливки приходится изготовлять со стенками большей толщины, чем предусмотрел конструктор, поскольку заполняемость форм жидким сплавом может оказаться недостаточной. Компромиссы довольно часто неизбежны.
Дабы удовлетворить потребителя и требования изготовителя, нужно знать и учитывать влияние бессчётных факторов. Литейщик требует от конструктора технологичной конструкции. В последней должны быть гарантированы определенные служебные особенности.
Служебные особенности ориентировочно возможно поделить на следующие группы:
физические — механические, электрические, звуковые, термодинамические, кристаллографические, размерная и массовая (весовая) точность, точность состава;
химические — поведение по отношению к вторым материалам;
эстетические — красота формы, точность контуров, звуковое поведение.
Эти особенности смогут требоваться независимо друг от друга, накладываться друг на друга либо взаимно обусловливаться. К примеру, определенное строение структуры возможно предпосылкой для механических либо электрических особенностей.
Многообразие разных литых изделий разглядим подробнее на отливках, продемонстрированных на рис. 1.
В техническом смысле чугунная чушка (рис. 1, а) есть отливкой, не смотря на то, что ее изготовляют в основном на металлургических фирмах, а в литейных цехах весьма редко. Наровне с низкой размерной и массовой (весовой) точностью чушка но должна иметь определенный состав.
Довольно вторых отливок требования к качеству чушек относительно низкие. Нужное и изготовляемое количество их весьма громадно. Многие доменные фирмы с каждым годом создают чугун в виде чушек.
К судовому гребному винту (рис. 1, б) в соответствии с его назначением предъявляют высокие требования. Он обязан владеть коррозионной стойкостью, и, помимо этого, удовлетворять солидному числу требований по физическим особенностям. Наиболее значимыми из них являются механическая прочность, кавитационная стойкость и высокая размерная точность при хорошем качестве поверхности. Размеры винта оказывают дополнительное влияние на особенности.
Гребных винтов требуется намного меньше, чем чугунных чушек. Нужные служебные особенности не связывают отливку с определенным химическим составом. Гребные винты возможно изготовлять из многих железных и неметаллических материалов.
На рис. 1, в продемонстрирован колокол, установленный на одном из высотных домов на площади Карла Маркса в Лейпциге. Состав материала колокола возможно подобен составу материала гребного винта. Но служебные особенности их совсем разны.
Не считая коррозионной стойкости колокол обязан владеть достаточной чистотой звона и другими эстетическими особенностями. На поверхности большинства колоколов имеются надписи либо украшающие элементы. Последние нужно делать с четкими контурами, а поверхность колокола чистой и ровной. Не считая сигнальных, большая часть колоколов, имеющих художественное значение, отливают единицами.
Серии бывают редко.
И, наконец, электрический элемент сопротивления (рис. 1, г), применяемый, к примеру, в электровозах. Предпосылками для определенного электрического сопротивления являются высокая размерная точность, определенные строение структуры и химический состав.
Механические особенности в этом случае имеют подчиненное значение. Отливка не испытывает динамические напряжения, да и статические напряжения в ней малы. Нужное количество отливок громадно, исходя из этого их изготовляют громадными сериями.
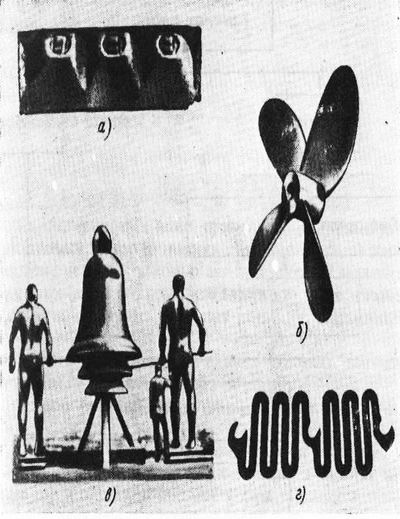
Рис. 1. Отливки: а — чугунная чушка; б — гребной винт; в — колокол механизма боя; г — элемент сопротивления
Круг служебных особенностей и предъявляемых требований не исчерпывается рассмотренными на этих отливках. От отливок для энергетического машиностроения, кстати развивающегося в ГДР прежде всего, требуются собственные особенные особенности кроме этого, как и от отливок для химических установок и т. д. Отливки смогут быть массой от 5 г до 300 ООО кг и самых разных размеров.
Задача литейщиков — изготовлять отливки качественными и в нужном количестве — не легка и требует глубоких научных знаний, среди них и технологии. Итог научных изысканий не имеет значения для улучшения качества отливок, пока он не стал технологическим рецептом.
Рис. 2. Схема выбора процесса
Производство отливок требует самой тесной конструкторов и совместной работы литейщиков. Последние должны кроме этого знать процесс формирования отливок и осознавать трудности, обусловленные влиянием бессчётных взаимодействующих факторов.
количество и Качество определяют способ изготовления. Разработка изготовления отливки кроме этого подчиняется качественному и количественному нюансам. К примеру, изготовление чугунных чушек требует на большое количество меньше операций, чем изготовление гребного винта.
Однообразные операции различаются требуемым качеством их выполнения.
Обеспечить количество и качество— первая и основная задача литейщика; выполнить ее при благоприятном соотношении затрат и взятой прибыли — вторая. Производственная программа определяет выбор метода изготовления отливок (рис. 2).
Литейщикам известно большое количество способов. Дабы отыскать верный, требуются глубокие знания процесса формирования отливок.
—
Задачей литейного производства есть изготовление из металлических сплавов и металлов изделий — отливок, имеющих разнообразные очертания и предназначенных для применения в разных целях.
Отливки по окончании механической обработки составляют практически половину массы подробностей всех автомобилей, механизмов, аппаратов и приборов, производимых различными отраслями машино- и приборостроения. Литьем изготовляют кроме этого отдельные части строительных сооружений, транспортных устройств и т. п.
Сущность литейного производства сводится к получению жидкого, т.е. нагретого выше температуры плавления, сплава необходимого качества и нужного состава и заливке его в заблаговременно приготовленную форму. При охлаждении металл затвердевает и в жёстком состоянии сохраняет конфигурацию той полости, в которую он был залит. В ходе охлаждения и кристаллизации сплава формируются главные механические и эксплуатационные особенности отливки, определяемые макро- и микроструктурой сплава, его плотностью, расположением и наличием в нем неметаллических включений, развитием в отливке внутренних напряжений, вызванных неодновременным охлаждением ее частей, и др.
Масса отливок колеблется в весьма широких пределах: от нескольких граммов до нескольких сотен тысячь киллограм.
Конфигурация отливок возможно любой, она определяется возможностью изготовления технологической формы и оснастки, минимальной толщиной полости, которую способен заполнить металл и эконономическими расчетами, разрешающими сравнить условия эксплуатации и стоимость изготовления отливки, с одной стороны, и подобного изделия, взятого вторым методом либо составленного из отдельных литых частей, с второй (к примеру, сварнолитые изделия).
Как уже указывалось, отливки приобретают в особых формах. Формы возможно изготовлять разными методами и из различных материалов. Размеры рабочей полости формы пара превышают размеры отливки, поскольку металл, залитый в форму, при затвердевании охлаждении уменьшается в количестве. Формы в большинстве случаев изготовляют раздельно для каждой отливки из особой, поддающейся уплотнению формовочной смеси, пребывающей в главном из глины и песка.
Формовочные смеси приготовляют в особом отделении литейного цеха, оборудованном смесительными и вторыми автомобилями.
Как пример на рис. 1 представлена разрез литейной и стальная отливка формы той конструкции, которая, употребляется чаще всего. Форма изготовлена из формовочной смеси по модели. Значительно чаще модель дробят на две части, по которым делают раздельно полуформы. Полуформы изготовляют в формовочном отделении литейного цеха.
Часть модели плоскостью, которая соответствует плоскости разъема формы, устанавливают на плите. На данной же плите устанавливают литую либо сварную рамку, именуемую опокой. В опоку насыпают формовочную смесь и уплотняют ее.
Рис. 3. Литейная форма (а) и отливка (б)
Из каждой полуформы по окончании ее изготовления удаляют часть модели. Появившиеся полости по окончании соединения (сборки) полуформ соответствуют внешним очертаниям отливки. В форме, не считая рабочей полости, делают каналы, по которым поступает жидкий металл («литниковые каналы»), а кроме этого каналы, по которым из формы по мере ее заполнения вытесняется воздушное пространство (вентиляционные каналы, выпоры).
До сборки в нижнюю полуформу устанавливают раздельно изготовленные части, именуемые стержнями. Места, занимаемые стержнями, не заполняются металлом, что разрешает оформить полости, углубления либо придать другие особенности конструкции отливки.
Стержни изготовляют в железных иди древесных коробках из смесей, отличающихся от формовочных содержанием связующих, увеличивающих прочность стержня.
Стержни устанавливают в нижней полуформе на месте либо вблизи места формовки, довольно часто это делают на конвейере, по которому движутся полуформы, высвобожденные от моделей.
По окончании установки стержней полуформы соединяют и скрепляют. В случае если крепление не есть твёрдым, то на собранную форму укладывают груз, мешающий поднятию верхней полуформы заливаемым металлом. Собранная форма по конвейеру либо иным методом подается на заливку.
В форме довольно часто делают дополнительную полость — прибыль с таким расчетом, дабы металл в ней затвердевал последним. Металл, поступая из прибыли в рабочую полость, компенсирует усадку металла во внутренних частях отливки, что исключает образование в отливки вакуумов (усадочных усадочных пор и раковин).
Прибыль образует на отливке время от времени большую по размерам выступающую часть. По окончании извлечения и охлаждения отливки из формы прибыль отрезают и подают на переплав.
В современных литейных цехах многие операции формовки осуществляются на автомобилях, к примеру уплотнение формовочной смеси, извлечение модели из готовой полуформы и т. д.
Для изготовление расплавленного металла в литейных цехах используют самые разные печи (электрические, пламенные, шахтные, тигельные). Выбор типа печи зависит от особенностей приготовляемого сплава и в первую очередь от температуры его плавления. В большинстве случаев жидкий металл заливают в форму из ковша. В некоторых случаях заполнение формы металлом происходит под давлением воздуха, поршня, центробежной силы, появляющейся при вращении формы и т. п.
По окончании затвердевания отливки песчано-глинистую форму подают на выбивку, где её разрушают и извлекают отливку. После этого из отливок удаляют стержни, отрезают прибыли, литники, выпоры. Поверхность отливки очищают от всякого рода загрязнений (пригоревшей формовочной смеси, «заусенцев», образованных металлом и т. д.).
Готовую отливку время от времени подвергают термической обработке. По окончании окраски и очистки отливки подают на склад либо в механический цех.
Около 80% общего числа отливок изготовляют в песчано-глинистых формах. Но чистота и точность поверхности этих отливок во многих случаях не удовлетворяют требованиям современного машиностроения. В связи с этим стали обширно применять особые методы литья: по выплавляемым моделям, в оболочковые формы, в железные формы (кокили), под давлением, центробежное и др., разрешающие приобретать отливки повышенной точности, с минимальным объёмом и чистой поверхностью механической обработки.
В литейном производстве применяют множество сплавов, самый активно используются сплавы на базе железа — сталь и чугун. Кроме этого используются сплавы на базе алюминия, меди, магния, цинка, никеля, кобальта, других металлов и титана. Литейные сплавы в зависимости от состава отличаются по температуре плавления (она колеблется от нескольких сотен градусов до 2000° С и выше), химической активности, вязкости в жидком состоянии, пластичности и прочности конкретно по окончании затвердевания и по окончании полного охлаждения и по весьма многим вторым особенностям.
Литые подробности многих автомобилей при работе испытывают большие нагрузки, каковые смогут быть статическими, динамическими и знакопеременными. В некоторых случаях отливки должны сохранять прочность при высокой либо низкой температуре, быть коррозионностойкими при работе с кислотами, растворами солей и вторыми агрессивными средами. Литьем изготовляют подробности, имеющие свойства и специальные назначения, к примеру магниты.
Многие художественные произведения монументальной скульптуры, требующие высокой точности воспроизведения заблаговременно приготовленной модели, кроме этого являются отливками.
Изготовление отливок различного размера, разной степени сложности из сплавов, отличающихся по многим особенностям, нельзя осуществлять одними и теми же производственными методами. В связи с этим взяли распространение многие технологические процессы, любой из которых, сохраняя в базе сущность литья, отличается своеобразными производственными приемами.
В литейном производстве употребляется много разных автомобилей и механизмов, разрешающих механизировать, а в некоторых случаях и автоматизировать технологические процессы изготовления отливок.
—
Литейное производство имеется процесс получения фасонных отливок методом заполнения жидким металлом заблаговременно приготовленных форм, в которых металл затвердевает.
Отливки смогут быть либо в полной мере готовыми подробностями, либо заготовками, подвергающимися в механических цехах окончательной обработке, которая произвздитсл с целью получения правильных размеров и требуемой чистоты всех либо некоторых поверхностей. В последнем случае на отливках предусматривается припуск на механическую обработку.
Отливки изготовляются из чугуна, сплавов и стали цветных металлов.
Литые подробности активно используются в станках, механизмах и различных машинах и составляют от 50 до 85% их веса. Методом литья смогут изготовляться подробности, различные по размерам и форме, а также сверхсложной конфигурации. Во многих случаях цена отливок намного меньше стоимости подробностей, изготовленных вторым методом.
Удачи в области улучшения структуры отливок, качества формовки и формовочных материалов стали причиной большому увеличению механических особенностей фасонного литья. Это разрешило возможность изготовлять литыми очень важные Подробности, к примеру: коленчатые валы двигателей, траки гусениц тракторов, рамы паровозов вместе с цилиндрами и др.
Существует пара способов заливки форм, а также:
а) простая заливка, в то время, когда металл заполняет форму вольно, под действием силы тяжести;
б) центробежное литье, в то время, когда металл заливают во вращающуюся форму и он распределяется в ней под влиянием центробежной силы;
в) литье под воздушным либо поршневым давлением с применением особых автомобилей.
Формы для заливки металла смогут быть разовыми либо постоянными. Разовые формы изготовляются из формовочной смеси и годны для получения Лишь одной отливки. Постоянные формы (железные) Еыдерживают много заливок.
По семилетнему замыслу 1959—1965 гг. в литейном производстве обширно внедряется автоматизация и механизация. Будет выстроено 75—80 больших заводов и специализированных цехов по производству литья, штамповок и поковок, и совершена специализация и реконструкция действующих фирм. В 1965 г. мощность специальных фирм составит по чугуну до 14,7 млн. т., по стали — до 4 млн. т. Мощность специальных фабрик по производству литейного оборудования будет увеличена более чем в 4 раза.