Многослойные печатные платы
Требования к уменьшению объёма и веса радиоаппаратуры приводят к необходимости увеличения плотности монтажа, что ведет к необходимости улучшения как конструкции, так и функциональных соединений узлов и технологии деталей.
Самый обширно применяемым методом размещения в малом количестве солидного числа проводников, соединяющих отдельные схемы есть использование многослойных печатных плат. Многослойная печатная плата складывается из последовательности наложенных друг на друга слоев, в которых образованы соединительные проводники для передачи сигналов, проводящие поверхности для подвода питающих напряжений, прокладки заземляющих цепей и контактные площадки либо выступы Для присоединения выводов.
Довольно часто в структуру многослойной платы включают для охлаждения теплопроводящнй материал. На одном из краев платы устанавливают разъем.
О возможности размещения интегральных схем на многослойной печатной плате возможно делать выводы на основании следующего примера: на плате площадью до 900 см2 и количеством в пара десятков кубических сантиметров устанавливают много монолитных интегральных схем в плоских корпусах.
На рис. 1 продемонстрирована многослойная плата, изготовляемая последовательным наложением слоев, в том месте же продемонстрированы пайка выводов плоского корпуса с интегральной схемой внахлест к печатным проводникам, теплопроводящие полосы для улучшения охлаждения, электрические соединения между слоями платы, подвода и цепи заземления питающих напряжений.
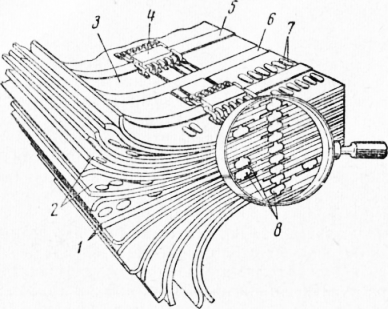
Рис. 1. Многослойная печатная плата: 1— внутренние слои с цепями подвода и заземлений питающих напряжений, 2 —внутренние слои с рисунком соединений, 5 —наружный, слой с тиной подвода и контактными площадками напряжения, 4 — интегральная схема, 6—полоса для улучшения охлаждения, 6—шина напряжения, 7 — контактная площадка, 8 — элемент межсоединений
Установилась следующая терминология в области производства и конструирования могослойных плат:
— многослойная печатная плата (МПП) — пара склеенных печатных слоев, имеющих межслойные соединения;
— печатный слой — печатный монтаж, нанесенный на изоляционное основание;
— межслойное соединение — переходное отверстие либо контактный переход;
— переходное отверстие — металлизированное отверстие, снабжающее переход печатного проводника с одного слоя МПП на другой;
— контактный переход — металлизированный участок, соединяющий печатные проводники, находящиеся в различных слоях МПП;
— технологические отверстия — отверстия в МПП, а также в отдельном печатном слое, предназначенные для обеспечения технологических требований в ходе изготовления МПГ1;
— базисные элементы— конструктивные элементы (кресты, треугольники, концентрические окружности), довольно которых координируются элементы печатного монтажа МПП;
— навесные элементы — микросхемы разных конструкций, микромодули, электро- и радиоэлементы, устанавливаемые на МПП; причем под термином микросхема подразумеваются гибридно-пленочные схемы (ГПС), твердосхемные модули (ТСМ) либо жёсткие схемы (ТС).
Многослойные печатные платы предназначены для размещения па них в основном многовыводных микросхем при, в то время, когда не представляется вероятным размещение проводников на двусторонних платах. Количество слоев МГ1П определяют при разделении электрической схемы на функциональные цепи, наряду с этим нужно, дабы любая функциональная цепь размешалась на отдельном слое (к примеру, слой с печатным монтажом цепей питания, слой с печатным монтажом нулевого потенциала, слой с печатным монтажом сигнальных цепей и др.).
Ликвидируют взаимовлияние печатных слоев и отдельных проводников рациональным размещением слоев относительно друг друга либо же введением экранирующих слоев либо проводников.
Неспециализированная толщина МПП выбирается с учетом требований механической прочности, предъявляемых к конструкции многослойного печатного узла, и обеспечивается нужным подбором толщин фольгированного и изоляциояного материалов.
Конструктивно МПП возможно делать из разных сочетаний одно- и двусторонних печатных слоев.
Ввиду малой механической прочности, сложности и коробления изготовления громадных по размерам МПП рекомендуется разрабатывать их малогабаритными. Размеры многослойных печатных плат не должны быть больше 150 X 180 мм. Рекомендуемое количество слоев 3—4.
Условно вычисляют первым слоем печатный слой со стороны установки навесных элементов.
При способе попарного прессования главными операциями технологического процесса являются:
— изготовление заготовок фольгированного стеклоткани и материала;
— изготовление печатного монтажа внутренних слоев;
— сверление переходных отверстий и их металлизация; прессование;
— нанесение картинок наружных слоев, сверление переходных отверстий;
— защита и металлизация отверстий печатного монтажа наружных слоев;
— изготовление печатного монтажа наружных слоев.
При способе металлизации сквозных отверстий главными операциями технологического процесса являются:
— изготовление заготовок фольгированного стеклоткани и материала;
— изготовление печатного монтажа внутренних слоев;
— прессование;
— нанесение картинок наружных слоев, сверление переходных отверстий;
— нанесение и металлизация отверстий защитного покрытия;
— изготовление печатного монтажа наружных слоев. При способе послойного наращивания главными операциями технологического процесса являются:
— изготовление заготовок стеклоткани, нарезка заготовок фольги;
— перфорация стеклоткани; приклеивание бронзовой фольги;
— выращивание контактных переходов и металлизация поверхности стеклоткани;
— изготовление печатного монтажа второго слоя;
— приклеивание стеклоткани второго слоя;
— выращивание контактных переходов- и металлизация поверхности стеклоткани второго слоя;
— изготовление печатного монтажа третьего слоя;
— приклеивание стеклоткани;
— изготовление печатного монтажа первого слоя.
—
Многослойная печатная плата имеет несколько слоев отдельных печатных плат, собранных в пакет и связанных между собой. Соединения между платами смогут быть сделаны разными методами, самый распространенный из которых — металлизация и сверление сквозных отверстий.
Использование многослойных плат есть действенным способом получения межсоединений для аппаратуры с высокой плотностью упаковки компонентов. Многослойная печатная плата есть носителем большого количества и печатного монтажа компонентов на данной плате.
При применении интегральных схем в плоском корпусе, пластмассовом либо в железном корпусе типа ТО многослойная плата разрешает значительно уменьшить пространство, требуемое для обеспечения межсоединений. Так, надежность плат и межсоединений обязана значительно превосходить надежность самих интегральных схем.
на данный момент прекрасно известны преимущества применения многослойных печатных плат для соединения микроэлектронных компонентов, но еще не хватает как мы знаем, что приводит к случайным отказам этих плат. Многослойные платы смогут быть сделаны достаточно надежными, в случае если при их разработке употребляется важный инженерный их изготовление и подход находится под твёрдым контролем. Чем сложнее конструкция платы, тем тверже должны быть средства контроля.
Электрические качества печатной платы должны быть выяснены перед тем, как на нее будут смонтированы другие компоненты и интегральные схемы, потому что в случае если недостаток в плате будет обнаружен по окончании монтажа и сборки, то придется вместе с платой выбрасывать и интегральные схемы. При верно организованной совокупности опробований недостатки в многослойных платах смогут быть найдены и исправлены ранее. Это прежде всего касается вероятных погрешностей в конструкции платы и в ее обработке.
В случае если нарушена главная функция платы — обеспечение электрического соединения’ Между соответствующими точками монтажа — это, в большинстве случаев, связано с тем, что одна из многих ступеней в ходе изготовления платы была совершена неправильно.
Ни один из главных процессов изготовления многослойных печатных плат не есть особенно тяжёлым и не содержит каких-либо своеобразных источников ненадежности. Процессы изготовления многослойных печатных плат были созданы пара лет назад для производства односторонних и двусторонних печатных плат, а многослойные платы являются послойную сборку нескольких таких плат. Но послойная сборка этих обеспечение и плат межсоединений между слоями, и хрупкость проводников делает более сложным поведение этих процессов.
В большинстве случаев, отдельные слои изготавливают травлением эпоксидных плат со стекловолокнистым связующим составом, каковые имеют толщину 0,05… .. .0,3 мм, в то время как простые печатные платы имеют толщину 0,7.. .1,5 мм.
Чаще всего применяемые межслойные соединения — это металлизированные сквозные отверстия. В большинстве случаев отдельные слои платы травят так, что их проводящие дорожки заканчиваются круглыми контактными площадками из меди. По окончании того как слон собраны и склеены давлением и нагревом, через эти контактные площадки просверливаются отверстия.
После этого внутреннюю часть отверстий покрывают медью методом последующей гальванизации и химического осаждения. самый опасным в таких платах есть то, что в месте соединения с контактной площадкой толщина слоя металлизации в отверстия возможно недостаточна.
Рис. 1. Виды соединений между слоями:
а — металлизированные сквозные отверстия; б — то же с выступами в — металлизация отверстий в монолитных платах.
очистка и Сверление отверстий многослойных печатных плат. При неправильном сверлении плат и очистке проводники смогут изгибаться и подвергаться износу, в случае если сверло через чур скоро вводится в отверстие либо вращается через чур медлительно. Твёрдые карбидные сверла, вращающиеся с высокой скоростью, предотвращают защемление либо скашивание контакт-пых площадок и излом слоев пластика, что приводит к образованию вакуумов и нерегуляриостей при металлизации.
В случае если с контактных площадок не удалены следы эпоксидной смолы, то проводники будут электрически изолированы от металлизации отверстий. Наилучшим методом неспециализированной очистки контактных площадок помогает химическое подтравливание, при котором не только удаляются следы эпоксидной смолы, но и выступают края проводников над слоем изоляции, что снабжает громадную контактную поверхность для металлизации отверстий.
В качестве травителя в большинстве случаев употребляется смесь серной (для растворения эпоксидной смолы) и плавиковой кислоты (для растворения стекловолокна, которое обнажается при растворении эпоксидной смолы). В растворе должно находиться около четырех частей серной кислоты на одну часть плавиковой; эта пропорция обязана в обязательном порядке сберигаться. Избыток плавиковой кислоты будет взаимодействовать с серной кислотой и наряду с этим в большинстве случаев появляются белые порошкообразные осадки.
Процессы металлизации. Критичным этапом .при металлизации отверстий есть начальное химическое (безэлектродное) осаждение меди. Кое-какие инженеры отказывались от применения многослойных плат из-за сомнений в целостности границы раздела между другими материалами и такой металлизацией.
Но шепетильно сделанные соединения выдерживают напряжения, появляющиеся при пайке, и прекрасно трудятся в разных окружающих условиях. Безэлектродное осаждение является последовательностьюхимических реакций. Эти реакции не будут закончены, в случае если металлизационные растворы не всецело смачивают внутреннюю часть отверстий.
В случае если края отверстия неровны и не хорошо очищены, то металлизация для того чтобы отверстия будет неоднородной.
На данный момент создано большое количество разных технологических способов металлизации сквозных отверстий, но предпочтительно применять трехступенчатый процесс, в котором для омеднения употребляется палладиевый активатор. В этом ходе ионы олова из раствора хлорида олова абсорбируются поверхностью эпоксидно-стеклянной изоляции и бронзовыми контактными площадками. После этого плату погружают в раствор хлорида палладия.
Узкий слой палладия осаждается посредством окислительно-восстановительной реакции, при которой ионы палладия из раствора хлорида восстанавливаются до железного палладия ионами олова, а ионы олова окисляются. На конечном этапе палладий есть катализатором при восстановлении меди из щелочного фор-мальдегидного раствора бронзовой соли. Активность каждого раствора обязана поддерживаться фактически постоянной.
Для этого нужны пополнение и периодический анализ растворов металлизационных ванн.
На последней стадии процесса образуются маленькие пузырьки газообразного водорода, каковые смогут захватываться кончиками стекловолокон, выступающими в отверстии, либо вторыми недостатками поверхности отверстия. Наличие Пузырьков кроме этого нарушает осаждение меди и может привести к вспучиванию электроосажденной меди. не сильный перемешивание либо потряхивание раствора содействует предотвращению захвата газообразных пузырьков.
На химически осажденную медь стандартным пирофосфатным гальваническим способом наносится покрытие и, в большинстве случаев, неспециализированная толщина слоя меди в сквозном отверстии приблизительно равна толщине бронзовой фольги платы. В некоторых случаях, в то время, когда требуются малые низкие уровни и контактные площадки тока, нужно применять более узкие слои металлизации. Наряду с этим внешние слои металлизируются в один момент с отверстиями, но травить малые контактные площадки тяжело, в случае если на внешний слой платы нанесен толстый слой меди, потому, что чем толще слой меди, тем посильнее, подтравливание.
Внешние слои. Наличие металла на внешних слоях многослойной печатной платы должно быть ограничено контактными площадками сквозных отверстий, и площадками для сварки и пайки. Применения проводящих дорожек на внешних слоях платы необходимо избегать, в особенности если они узкие и расположены близко друг к другу.
Проводящие дорожки в многослойных платах тонкие, и недостаток внешнего слоя готовой платы обходится через чур дорого, поскольку на изготовление платы затрачивается большое количество труда и времени. Исходя из этого травление внешних слоев — одна из последних операций изготовления многослойных плат. В большинстве случаев, внешние контактные площадки делаются большей- площади, чем внутренние.
В случае если к картинкам на внешней стороне платы предъявляются твёрдые требования, то в этом случае платы целесообразно изготавливать травлением по трафарету либо контролируемым удалением металла. Оба эти способа ликвидируют неприятности, которые связаны с гальваническим нанесением, из-за которого толщина металлизации по площади платы делается неоднородной, что усложняет процесс травления.
Время травления возрастает, возрастает возможность пробоя резиста и возрастает подтравливание меди. При металлизации по трафарету .на плату наносится негативный резист. В этом случае обрабатываются лишь контактные площадки и проводящие дорожки, причем проводящие дорожки мало увеличиваются, но бронзовое покрытие между такими линиями остается узким и его легче стравить.
Возможно кроме этого удалить металлизацию с обкладки платы перед травлением, к примеру сошлифовыванием ее на прецизионном шлифовальном станке. Сошли-фовывание направляться осуществлять контроль, дабы избежать отделения покрытий сквозных отверстий от проводящих дорожек платы. Кроме того в случае если такое отделение само по себе не вызывает отказа, то оно затрудняет очистку соединений перед покрытием меди золотом либо серебром.
В случае если золотое либо серебряное покрытие будут иметь недостатки, смогут появиться резистивные соединения, показаться коррозия и появятся трудности при пайке.
Конечная металлизация золотом либо оловянно-свинцовым (время от времени оловянно-никелевым) сплавом защищает медь от повреждений и коррозии и содействует процессу пайки.
Надежность в конструировании. Высокая совершенные методы и квалификация рабочих контроля не смогут компенсировать -неточностей в размещении печатных проводящих дорожек, контактных площадок и выборе расстояний между ними, каковые допущены проектировщиками и разработчиками. В случае если по большей части чертеже рисунка платы имеется неточность, то она возможно не найдена в течение долгого времени, охватывающего производства и цикл проектирования.
Разработчики схемы должны закладывать в собственные чертежи настоящие допуски на расстояния между проводящими дорожками, дабы обеспечить как экономичность производства, так и высокий вы-
годных многослойных плат. Время от времени проектировщики закладывают через чур твёрдые допуски на ширину проводящих дорожек и на расстояние между ними. Проектировщик, к примеру, может задать определенный диаметр отверстия по окончании металлизации, но на данной базе нельзя определить минимальный диаметр контактной площадки.
Его нужно устанавливать анализом нехорошей комбинации допусков при размещении площадок и отверстий.
Допуски. Настоящие требования к допускам, обсуждаемые ниже, говорят о том, что диаметр внутренней контактной площадки должен быть не меньше 1 мм. Площадка для того чтобы диаметра разрешает применять кольцо меди шириной не меньше 0,1 мм около металлизированного отверстия.
Кольцо должно быть тем шире, чем больше места имеется для контактных площадок, что разрешит не допустить вытекание раствора при химическом осаждении меди в последующем осаждении и отверстиях меди между проводящими дорожками.
Нужно учитывать следующие допуски, каковые смогут привести к худшей комбинации условий:
1. Допуски на подтравливание. Их нужно прибавить к диаметру контактной площадки, причем конкретная величина допуска, зависящая от удельного веса покрытия, обязана компенсировать подтравливание меди в ходе травления.
2. Допуск на отклонения от верного положения отдельных слоев платы. Чем больше плата, тем больше должен быть данный допуск. Его величина зависит кроме этого от качества обработки плат.
3. Допуск на размещение отверстий. Размещение отверстия относительно центра платы может изменяться.
4. Допуск «а толщину меди. В большинстве случаев предъявляются определенные требования к неспециализированной толщине слоя меди в сквозном отверстии. Но существует тенденция применять металлизацию меньших отвер какое количество и более узкое покрытие на внешних слоях.
5. Допуск на диаметр отверстия. Он должен быть различным в зависимости от того, покрывается ли потом медь золотом либо будет производиться лужение. Чертеж должен быть изготовлен в масштабе по крайней мере 4:1, 5:1; в нем нужно учитывать допуски на сужение проводящих дорожек в ходе контактной печати.
6. Допуск на фотолитографию. проявление и Печать фоторезиста, подтравливание в ходе обработки ведут к уменьшению толщины линии тем более значительному, чем меньше исходная ширина линии. В случае если макетный чертеж готовится посредством чертежной ленты, то в этом случае тяжело скомпенсировать сужение линии посредством повышения ширины ленты, потому, что она в большинстве случаев стандартизована.
Помимо этого, ширина линии на макете из особой ленты кроме этого изменяется, потому, что в ходе изготовления макетного чертежа лента растягивается и сжимается, помимо этого, свет может пробраться под лепту в ходе контактной печати.
Ширина линии выдерживается более шепетильно, в то время, когда употребляется техника фрезерования. Машинное фрезерование ограничивается прямыми Линиями, но наряду с этим допустима регулировка ширины линии. На макете схемы, в случае если быть может,.нужно ввести добавочное разнесение линий, что разрешит изготовителю плат мало увеличить линии в ходе производства.
Площадь контактных площадок нужно расширить за счет дополнительных участков меди в местах соединения контактных площадок и проводящих дорожек.
В случае если на контактных площадках внешних слоев предусмотрены ободки либо ребра, это предотвратит их подъем в ходе пайки и травления и улучшит образование паяных соединений. Ободки либо валики на внутренних слоях разрешают смягчить допуски на отверстия, просверленные не по центру. В макетах схем в большинстве случаев имеются контактные площадки для всех стандартных положений отверстий.
Неиспользуемые площадки не нужно удалять до тех пор, пока не будет смакетирована вся схема. Сохранение контактных площадок разрешает избежать размещения проводящих дорожек через чур близко к металлизированным сквозным отверстиям. По окончании изготовления дорожек такие площадки должны быть удалены, потому, что избыток меди ухудшает однородность распределения изоляции при сборке слоев.
Размеры сквозных отверстий. Кроме того при тщательном контроле процессов изготовления появляются металлизированные сквозные отверстия нехорошего качества. Но два чаще всего видящихся недостатка не всегда приводят к отказу платы: неполная металлизация в отверстии либо разрыв в металлизированном соединении между контактной площадкой и отверстием.
Маленькие разрывы в металлизации не приводят к отказу, в случае если площадь окружности соединения намного больше ширины проводящей линии. В этом случае маленькой разрыв металлизации не ухудшает проводимости соединения если сравнивать с самой линией. Проводимость зависит от площади поперечного сечения (рис.
14). В случае если отношение диаметра проводника в отверстии (D) к ширине линии (№) образовывает 1,5 либо больше, маленькие разрывы металлизации смогут быть допустимы. Наряду с этим нужно кроме этого учитывать отношение между толщиной платы и размером отверстия.
Не смотря на то, что в практике производства употреблялись такие значения D/W, как 10: 1, целесообразно ограничиться величиной приблизительно 3:1.
Процесс травления. Изготовление печатных плат с плотной упаковкой способом фототравления требует тщательного контроля особенностей химического травителя для бронзовой фольги и выдвигает особые требования к оборудованию. Это особенно значительно в случае если проводящие дорожки плат имеют малую ширину и мало расстояние между дорожками.
Уровень качества печатной платы, взятой процессом травления фольги, зависит кроме этого от качества нанесения и метода фоторезистов этого нанесения.
Рис. 2. Зависимость сопротивления от ширины проводящей линии
Металлизация отверстий. Использование металлизированных сквозных отверстий, просверленных в двусторонних печатных платах чтобы получить соединения, известно. Но кое-какие затруднения видятся при применении этого способа в многослойных конструкциях.
При изготовлении металлизированных сквозных отверстий в многослойных платах должно быть обеспечено хорошее электрическое и механическое присоединение контактных площадок к внутренней стенке отверстия, которое осуществляется посредством химического осаждения. Используемые для химической металлизации растворы снабжают хорошее покрытие таких изолирующих материалов, как стекловолокно с эпоксидным связующим составом. Но адгезия осажденного слоя существенно хуже если сравнивать с электролитически осажденной медью, исходя из этого хорошее соединение между слоем меди, осажденным медной фольгой и электролизным процессом, возможно взять особыми способами очистки и активирования.
Один из способов, что снабжает хорошее уровень качества металлизации — окисление меди в растворе катализатора с последующим восстановлением окисла. Выбор ванны для гальванического нанесения меди зависит от свойства металлизационных растворов попадать в маленькие отверстия.
Сборка слоев. При изготовлении и металлизации обычных способах отверстий всех плат раздельно громадна возможность появления недостатков в ходе сборки отдельных слоев. Адгезия слоев платы в целом определяется качеством материала, содержанием смолы, временем желирования и текучести материала, используемого для предварительной пропитки.
Эти характеристики полуотвержденных эпоксидных клеев конкретно связаны с способом изготовления. Процесс склеивания слоев определяется температурой пресса, величиной давления, временем выдержки и т. д., каковые употребляются для конкретного материала. При склеивании слоев конкретно по окончании подачи тепла в склеивающем прессе по-луотвержденная эпоксидная смола, применяемая для предварительной пропитки, размягчается и делается текучей, а после этого затвердевает либо желируется.
Способ подачи давления на стадиях желирования и текучести эпоксидной смолы, отвод и температура пресса тепла через многослойную структуру являются критичными параметрами цикла отверждения.
В то время, когда на материале имеется слой бронзовой фольги то тепло от пресса передается достаточно скоро. Период желирования и размягчения смолы являете весьма маленьким, исходя из этого такие платы помещаю в пресс и сразу же подается большое давление В случае если платы складываются из последовательности отдельных слоев, тепло не переносится так скоро, потому, что на поверхности плат имеются лишь узкие проводящие дорожки Исходя из этого при прессовании нужно обеспечить вы-держку в течение некоего времени, дабы теплота равномерно распределилась по всем слоям^клея между отдельными платами.
В ходе начального периода нагрева (время желирования) нужно осуществлять маленькое давление, а после этого повысить его до отметки, нужного для отверждения материала. Имеются и другие факторы, каковые значительно влияют на уровень качества многослойной структуры. К примеру, наличие жидкости в материале плат и в клее приводит к расслаиванию многослойной платы либо образование вздутий.
Перед сборкой влагу, адсорбированную в следствии прошлых операций, направляться удалить и сборку многослойных плат в единое целое проводить в поме! щении с контролируемой влажностью (относительная! влажность должна быть около 40%). Перед склеиванием слоев рекомендуется сушить их в вакууме в течение 30 мин при температуре 120 °С.
Растворы, каковые употреблялись при металлизации и травлении и следы которых остались на материале плат, смогут привести к плохой адгезии при склеивании. Для их удаления слои необходимо промыть деиони-зированной водой в вакууме. Отдельные слои платы необходимо очистить от оксидных, смазочных и других загрязнений, и при обращении с платами i(c пропиткой либо без нее) персонал должен в любой момент пользоваться перчатками.
Контроль металлизированных отверстий в многослойных платах. На каждой стадии изготовления плат крайне важен контроль качества. Нужна визуальная и электрическая проверка плат, и деструктивные опробования контрольных участков, каковые изготавливаются как часть каждой платы.
Любой отельный слой перед монтажом многослойной платы направляться осуществлять контроль методом сравнения вытравленного рисунка схемы с чертежом; помимо этого, любой слой нужно контролировать на наличие царапин, других дефектов и выбоин проводящих дорожек. По окончании склейки слоев и металлизации будут видны лишь наружные поверхности, контроль которых неимеетвозможности обеспечивать хорошую сообщение металлизации сквозных отверстий с внутренними проводниками либо того, что слои и просверленные отверстия соответствующим образом согласованы.
Пример таковой платы продемонстрирован на рис. 15.
Рис. 15. Плата для выборочных опробований
Контроль соединений между точками разрешает найти соединения и разрывы соединений с высоким сопротивлением. Измерения выполняют при низких уровнях токов, что соответствует практически всем настоящих условий применения плат. Такое опробование ча прохождение тока нужно, и соединения должны владеть свойством выдерживать 100%-ную
перегрузку если сравнивать с требованиями К плате. Рентгеновское просвечивание плат представляет собой один из немногих неразрушающих способов контроля каковые разрешают оценить их внутреннюю структуру. Рентгеновский контроль оказывает помощь проверить точность сверления отверстий перед их металлизацией либо травлением внешних слоев платы.
Уже по окончании изготовления платы этим способом возможно найти неправильное размещение слоев, возможность образования и разрывы соединений маленьких замыканий.
Испытательные площадки должны обрабатываться вместе с каждой платой. Это разрешает быть до некоей степени уверенным в объективности контроля условий процесса изготовления плат.
Металлографический контроль разрешает распознать недостатки, появляющиеся из-за нехорошего проведения технологических операций либо из-за случайных повреждений. Он разрешает кроме этого оценить типы недостатков, каковые смогут быть устранены посредством изготовления и селективного сверления проволочных перемычек.
разрывы и Короткие замыкания. Не смотря на то, что при обработке многослойных плат смогут встретиться многие виды отказов, самые серьёзными являются разрывы и короткие замыкания проводников. Разрывы соединения смогут быть позваны механическими напряжениями между слоями, существовавшими на бронзовых покрытиях до обработки, выгоранием перетравленных проводников в ходе опробования либо при работе схемы.
Громадна возможность разрыва по окончании сборки узких проводящих дорожек, каковые имели до сборки выщербины либо царапины. Разрывы смогут наблюдаться и на дорожках, каковые сдвигаются в ходе изготовления, что возможно позвано неадекватной адгезией меди к нагретому материалу платы. Вторым видом разрывов есть пропуск сквозного соединения, что случается, в случае если слои неверно идентифициро-папы либо в случае если имеются погрешности в ходе изготовления отверстий.
Маленькие замыкания вызываются следующими обстоятельствами:
— значительная неточность при проектировании внутренних слоев;
— сверленые отверстия не согласованы с контактными площадками внутренних слоев;
— конструкция схемы не снабжает достаточного расстояния между проводниками и металлизированными отверстиями;
— вероятна утечка раствора, применяемого для химического осаждения меди, в щели и отверстия между близко расположенными проводниками и отверстиями;
— вероятно попадание посторонних материалов в плату в ходе обработки.
Главные недостатки многослойных печатных плат.
Эти недостатки сводятся к следующему:
— нарушение адгезии проводника к плате, отслоение либо отклеивание проводника по длине (данный недостаток чаще всего видится на выводах и на финишах проводящих дорожек);
— наличие стекловолокон, выступающих в отверстие по окончании сверления;
— разрывы, трещины либо царапины на проводниках;
— наличие меди на поверхности по окончании нанесения верхнего слоя металлизации. Браком считается, в случае если таковой дефектный участок занимает всю ширину проводника либо имеет протяженность более чем 12,0 мм на протяжении проводника;
— сквозные отверстия, в которых площадь недостатков металлизации превышает 5% площади металлизации поверхности отверстия;
— раковины на границах раздела;
— повреждения проводящих колечек около металлизированных отверстий;
— неоднородности металлизации отверстия из-за Некачественной очистки.
Симптомы отказов по окончании сборки многослойной платы. Возможные отказы печатных плат смогут быть найдены при визуальном контроле по окончании сборки.
Их симптомы сводятся к следующему:
— вспучивания из-за недостаточного давления при склеивании либо избыточного поглощения жидкости;
— воздушная раковина — из-за неправильного проведения цикла предварительного отверждения либо недостаточной текучести смолы;
— «сыпь» из-за малого содержания смолы, применения ветхого раствора либо избыточного давления при склеивании;
— расслаивание из-за недостаточного отверждения либо неверной подготовки слоев;
— сдвиг проводящих дорожек на отдельном слое платы из-за малой силы сцепления слоев, избыточного-давления, неправильной фиксации;
— неоднородная толщина платы по причине того, что отдельные слои платы непараллельны, неоднородная конфигурация плат на отдельных слоях;
— сдвиг проводящих дорожек на поверхности из-за недостатков в предварительной обработке перед склейкой слоев, избыточного давления при склейке либо из-за старения;
— участки, запачканные смолой из-за излишней текучести смолы, позванной применением через чур больших температуры либо давления при склеивании;
— захват посторонних частиц из-за плохой погрешности и очистки в ходе сборки слоев;
— потемнение либо появление пятен на платах из-за избыточного тепла либо недостатков предварительной пропитки.