Оборудование и способы получения колотых балансов
Одним из действенных способов применения низкокачественных (дровяных) и, частично, низкосортных лесоматериалов есть изготовление балансов. Балансы из для того чтобы сырья изготовляются по окончании его раскряжевки на мерные отрезки (чу-раки) и расколки их на поленья. Исходя из этого оборудование для получения балансов из колотых дров устанавливают, в большинстве случаев, вблизи от дроворазделочной площадки.
По окончании раскряжевки дровяные чураки раскалывают на поленья на цепном одноклиновом дровокольном станке КЦ-7 (КЦ-5), на двухклиновом станке КЦ-6М (КЦ-6) либо на гидравлическом колуне ГК-2.
Время от времени для повышения производительности раскряжевочных площадок либо агрегатов сырье на дровяной узел подают не только в коротье, но и в долготье. В таких случаях долготье раскряжевывают на нужную длину ручными электропилами (либо бензопилами), или на балансировочных станках типа ЦБ-4, либо установках типа АЦ-1.
направляться подчернуть, что такая двухступенчатая разделка производится лишь на складах с громадным грузооборотом и при большом количестве дров.
Для таких складов в ЦНИИМЭ создана и Свердловским механическим заводом Министерства строительного и дорожного машиностроения серийно выпускается линия ЛД-2. В линию входят : механизм для раскряжевки дровяного долготья — АЦ-2М, колун для расколки чураков на четыре части — ГК-2 и набор околостаночного оборудования: поперечный цепной транспортер ТС-9 — буферная горка, подающий цепной транспортер ТС-8, подающий и приемный роликовые столы, ленточный транспортер 8063-100 для выноса готовой продукции, цепной скребковый транспортер для отходов ЗТ, кассетоукладчик КУ-2М, и малогабаритный аккумуляторный погрузчик 4004М с устройством УП для погрузки коротья.
По окончании расколки поленья сортируются. Часть поленьев идет на получение балансов, а имеющие недостатки поступают на отгрузку в качестве дров. По ленточному транспортеру дрова подаются к кассетоукладчику.
Главными узлами кассетоуклад-чика являются: рольганг, транспортер и кантователь со щитом. Руководит работой кассетоукладчика оператор с пульта.
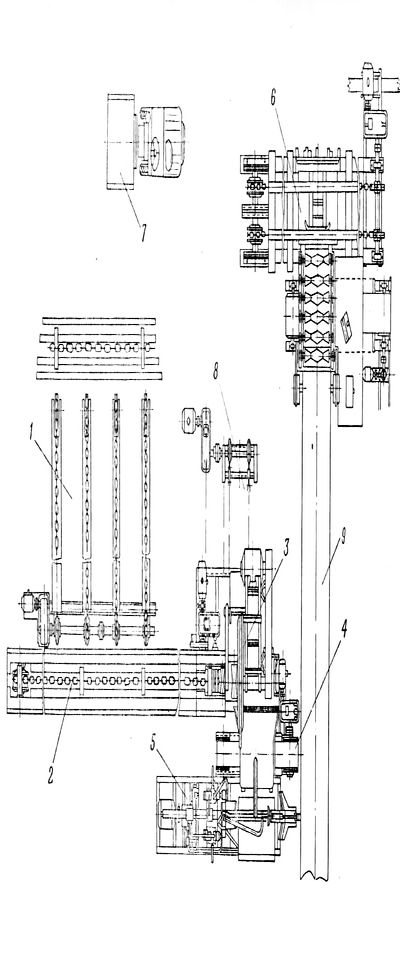
Рис. 1. Механизированная линия для раскряжевки дровяного дол-готья, расколки погрузки и чураков поленьев в кассеты ЛД-2:
1 — поперечный цепной транспортер ТС-9 — буферная горка; 2 — подающий продольный транспортер ТС-8; 3 — выпивала АЦ-2М; 4 — ленточный транспортер T4M для выноса поленьев малого диаметра; 5 — гидроколун ГК-2: 6 — кассетоукладчик КУ-2М; 7 — малогабаритный электропогрузчик 4004М с устройством УП ЦНИИМЭ; 8 — цепной скребковый транспортер ЗТ для отходов; 9 — ленточный конвейер 8063—100
В зависимости от породной и размерно-качественной чёрта поступающего на склад сырья количество перерабатываемых на балайсы дров от общего объема дровяного сырья колеблется в пределах от 30 до 80%.
В большинстве леспромхозов удаление из колотых поленьев гнили и их окорка осуществлялась до последнего времени вручную. Сменная норма выработки колотых балансов из дров устанавливалась, исходя из местных условий. К примеру, в Тоснен-ском леспромхозе треста «Ленлес» сменная норма на одного рабочего, занятого выколкой гнили из поленьев и их окоркой вручную, составляла 2 скл. м3.
Для леспромхозов Западного Урала в 1963 г. были созданы временные нормы выработки балансов вручную из дровяной древесины при длине поленьев 1-М,25 м и чистой окорке: зимний период—1,8 скл. м3, летом — 2,3 скл. м3. В переводе на плотные кубометры (переводной коэффициент 0,7) это образовывает соответственно 1,26 и 1,61 м3. В этом случае, не считая окорки и удаления гнили, рабочие должны подносить поленья к рабочему месту на расстоянии до десяти метров, относить готовые балансы на такое же расстояние, укладывать их в поленницы и убирать рабочее место.
В Монзенском леспромхозе комбината «Вологдалес» норма получения балансов из колотых дров при окорке и ручном удалении гнили равна 1,69 м3 в 7-часовую смену. оборудование и Технология при получении балансов из колотых дров вручную очень несложны.
В Удимском леспромхозе Вологодской области в 1964 г. была организована поточная линия с ручной выработкой балансов из дров. Переработка 1 м3 осиновых дров давала леспромхозу прибыль 2 р. 29 к.
В некоторых леспромхозах Пермлеспрома при переработке елово-пихтовых дров на линиях с ручной выработкой балансов прибыльна 1 м3 балансов составила 2 р. 70 к. Нужный выход наряду с этим колебался в пределах от 55 до 62%, т. е. на про-„зводство 1 м3 балансов расходовали от 1,6 до 1,8 м3 дров. Однако, не обращая внимания на явную рентабельность процесса изготов-тения балансов из колотых дров вручную, советовать данный процесс к широкому внедрению запрещено и в первую очередь вследствие того что наряду с этим через чур громадны затраты тяжелого физического труда и не хорошо соблюдаются правила техники безопасности.
‘ Разные организации предпринимают попытки механизировать данный процесс. Для этого они проектируют, изготовляют и частично применяют механизмы и специальные станки. Не обращая внимания на различия в конструктивном выполнении этих механизмов, в их базу положены четыре метода удаления гнили: скалывание; скалывание с последующим выфрезерованием; выфрезерование; выпиливание.
Окорка колотых поленьев проводится на особых создаваемых для этого станках, или методом встраивания в станки для удаления гнили особых фрезерных головок, имеющих профильные ножи. Помимо этого, в некоторых случаях окорка чураков производится на окорочных станках типа ОК либо ОД еще до их расколки.
Схематическое изображение разных способов удаления гнили из их окорки и дров для получения балансов даны на рис. 26. Очевидно,- что при механизации получения балансов из колотых дров пропускная свойство этого участка, а следовательно, и количество перерабатываемой древесины, приходящейся на одного рабочего в единицу времени, существенно возрастает.
Наряду с этим возрастает и количество отходов, каковые должны быть убраны от рабочего места; тем более, что при механизации процесса отходы достигают 50% количества сырья, отобранного для получения балансов. Исходя из этого принципиально важно при создании механизированных станков, участков либо поточных линий для получения колотых балансов из дров предусмотреть надежно действующую совокупность уборки отходов.
Одной из первых организаций, которая спроектировала, изготовила и внедрила станок для получения балансов из колотых дров был Тосненский (сейчас Дубовицкий) леспромхоз треста «Ленлес». В этом леспромхозе с конца 1962 г. начал работату станок, что в будущем был пара поменян и улучшен Гипролестрансом. По окончании реконструкции данный станок под маркой АБС-1 был выпущен маленькой партией Ленинградским умело-экспериментальным механическим заводом треста «Ленлес».
Станок АБС-1 довольно несложен по устройству. В базу его работы заложена окорки удаления и схема гнили, изображенная на рис. 26, II.
При нужном выходе продукции в 50—60% это снабжает пропуск через него 28—30 пл. м3, либо 40—43 скл. м3 исходного сырья в смену.
Но при лучшей организации производства данный станок может обеспечить производительность до 20—25 пл. м3 в смену.
Станок вычислен для работы на средних и малых складах, где количество заготавливаемого в смену дровяного сырья не превышает 100 м3. Но с неменьшим успехом он бывает использован и на больших складах.
Рис. 2. Схематическое изображение разных окорки удаления дров и способов гнили для получения балансов
Для больших складов и ЦБК Уралгипролесбумпромом спроектирована на Пермском заводе «Коммунар», изготовлена и передана для эксплуатации на Камский ЦБК поточная линия для получения балансов из дров с годовой производительностью 60 тыс. м3, трудящаяся по схеме Па, указанной на рис. 2. Окорка древесины, поступающей на линию, производится на простых окорочных станках типа ОК либо на особом оборудовании.
В состав операций, делаемых на линии, кроме окорки, включена расколка на четыре части на колуне КЦК- окоренных и разделанных по длине чураков. В первом варианте линии в операцию входилоудаление остатков гнили на особом станке СФГ-1 комплектом дисковых фрез.
Но опробования в производственных условиях, в ходе которых станки и сама линия, входящие в нее, подверглись большой модернизации, продемонстрировали, что по окончании выколки гнили удалять остатки фрезерованием нет необходимости, поскольку их остается всего около 1,7%. Это количество гнили возможно для выработки сульфитной целлюлозы. Следовательно, в состав линии, кроме набора вспомогательно-транспортного оборудования, входят три станка: окорочный, станок и колун для скалывания гнили.
Компоновка станков и их количество в линиях смогут быть разными и зависят от количества древесины, пропускаемой через линию, от требований, предъявляемых к приобретаемым балансам, и т. д. В том случае, если в изготавливаемых балансах не должно быть кроме того остатков гнили, к примеру при получении балансов для вискозного производ?тва либо при поставке их на экспорт, в состав линии должен быть дополнительно включен станок для их удаления.
Большая сменная производительность линии, складывающейся из одного колуна КЦК-1М и четырех станков для скалывания гнили ССГ-1М, достигает, согласно данным ее авторов, 260 м3 по сырью [13]. Необходимо заметить, что, во-первых, на расколку подаются уже окоренные чураки и, во-вторых, средний их диаметр при таковой производительности должен быть не меньше 45-^ 50 см, что вряд ли вероятно взять в простых производственных условиях.
В том случае, если окорка древесины производится на окорочных станках, то далеко не каждый дровяной кряж возможно пропущен через эти станки. Следовательно, в этом случае для подачи на линию отбирается фактически лучшая часть Дров, т. е. технологические дрова.
В случае если кора удаляется с расколотых поленьев на особых устройствах с окорочными головками фрезерного типа, то и в этом случае, как показывает стаж работы аналогичных станков, для обычной эксплуатации оборудования нужно подавать в него отобранные, т. е. опять-таки технологические, дрова. Количество отобранных дров в большинстве случаев не превышает 35% их общего объема, что со своей стороны образовывает 20—30% всего количества сырья, вывозимого па склад. Так, в том случае, если средняя пропускная свойство линии образовывает хотя бы 80—100 м3 в смену, то для обычной ее работы она должна быть установлена на складе с годовым грузооборотом при двухсменной работе не меньше, чем 350 тыс. м3 либо, что значительно лучше, на бирже ЦБК.
этих случаях довольно громадная цена набора главного и запасного оборудования, входящего в состав линии, в полной мере окупается ее большой пропускной свойством.
В ходе опробований данной линии распознаны кое-какие недоработки в части межстаночного и вспомогательно-транспортного оборудования и самих станков. Эти недочёты в ходе доводки полностью устранены.
Кроме обрисованных станков, чисто историческое значение имеет набор фрезерных станков СО-1М и СВГ-1М [14], изготовленных Ленинградским умело-экспериментальным заводом по чертежам, созданным особым проектно-конструк-торским бюро (СПКБ) мебельной и деревообрабатывающей индустрии бывшего Ленгорсовнархоза. Первый из названных станков предназначался для окорки колотых поленьев, второй для выфрезерования из них гнили.
В наборе, совместно с околостаночным вспомогательно-транспортным оборудованием, эти станки составляли линию для получения балансов. Опробования этих станков в производственных условиях Оленинского леспромхоза продемонстрировали их нетехнологичность, последовательность конструктивных недочётов и в итоге их неприемлемость для предстоящей эксплуатации. Исходя из этого они не были рекомендованы для изготовления.
То же самое возможно сообщить и о комплекте станков, входившем в линию для получения балансов из дров на Сухонской перевалочной лесобазе Сокольского сплавучастка, и о линии для получения балансов и попутной продукции способом выпиливания, смонтированной в Гремяченском леспромхозе комбината «Чусовлес». Станки, трудящиеся по схемам Ша — Па, и 1а, рис. 2, были спроектированы в Гипролесмаше, но не изготовлены.
На основании изучения опыта работы разных механизмов, линий и станков для получения балансов из дров, данных исследований, и конструкторских и натурных проработок Гипролесмаша в ЦНИИМЭ в 1965—1966 гг. был создан и изготовлен экспериментальный пример станка, взявший кроме этого, как и экспериментальный пример Гипролесмаша, шифр Н8.
Данный станок в 1966 г. был установлен в Каменском лесопункте Монзенского леспромхоза с целью проведения широких производственных опробований. окорка поленьев и Удаление гнили секторной формы осуществляется на этом станке по схеме, указанной на рис. 2, I.
Ввиду того, что в станке Н8 подача полена под режущие органы осуществляется так лее, как и в станке АБС, цепью с упорами, его производительность значительно не отличается от производительности, достигнутой на станке типа АБС. В зависимости от организационных обстоятельств она колеблется в пределах от 15 до 25 пл. м3 балансов в смену.
Для эксплуатации на ЦБК и фирмах, изготовляющих разного рода древесные плиты, по заданию Гипробума Вологодским головным конструкторским бюро по проектированию деревообрабатывающего оборудования был создан, а после этого изготовлен на заводе «Северный коммунар» станок ДСГ-1, предназначенный лишь для удаления гнили из колотых поленьев по схеме, указанной на рис. 2, Па.
Данный станок не снабжает законченный цикл операций по изготовлению балансов из расколотых, но неокоренных чураков и рекомендован для работы лишь в наборе с окорочным станком. Таковой набор оборудования характерен для линий с довольно определёнными требованиями и большой производительностью к качеству исходного сырья. Следовательно, обеспечить экономически удачную эксплуатацию аналогичных линий возможно лишь при их установке на ЦБК либо, в виде исключения, на наибольших нижних складах.
Один из способов получения балансов из колотых, но неокоренных дров с сердцевинной гнилью обрисован в литературе и используется на некоторых фирмах Японии. Недочёт сырья для целлюлозно-бумажной индустрии вынудил промышленников Японии применять для изготовления технологической щепы всю низкосортную и низкокачественную древесину.
Сырье, доставленное на предприятие, разделывается по длине, раскалывается на колуне, довольно часто вертикальном, либо распиливается на ленточном станке. Полученные поленья подаются во поворачивающийся барабан. Число оборотов барабана возможно разным.
В зависимости от конструкции и размеров оно колеблется от 6 до 16 об/мин. Вращаясь вместе с барабаном, поленья, попавшие в него, ударяются приятель о приятеля и о особые ножи на его внутренней поверхности. Наряду с этим за счет сухого трения они теряют гниль и кору.
В барабанах, производимых некоторыми компаниями, имеются дополнительные ножи, укрепленные на центральном вращающемся валу. Число его оборотов возможно разным и достигает 900 об/мин. Наличие этих валов с ножами, по утверждению компаний, усиливает и активизирует отделение и окорку гнили. Ножи на внутренней поверхности барабанов находятся в шахматном порядке по длине барабана через 250—300 мм и по диаметру через 300— 350 мм.
Изготовляются ножи из углеродистой стали и в ходе эксплуатации практически не требуют ухода. Кое-какие компании устанавливают фигурные ножи. удаление гнили и Успешная окорка из поленьев зависит от эксплуатации ножей и правильной установки. Благодаря ножам в барабанах сухого трения возможно достигнута 100%-ная окорка.
Помимо этого, наличие ножей на внутренней поверхности барабана разрешает создавать удаление и окорку гнили и в зимнее воемя при температуре до —25°.
Но качество и удаления гнили и продолжительность окорки методом сухого трения по большому счету, а зимой в особенности, нуждаются в экспериментальной проверке, тем более в условиях нашей страны.
В зависимости от требующейся производительности в Японии выпускается много типоразмеров барабанов сухого трения. Их диаметры колеблются от 1800 до 3000 мм, а протяженность от 1800 до 15 000 мм. В соответствии с этим вес барабанов колеблется от 8700 до 26 100 кг.
Производительность барабанов зависит от их размеров, ряда и гидротермического состояния древесины вторых факторов и колеблется в пределах от 20 до 100 пл. м3 и более готовой продукции в смену, что соответствует 36—180 м3 исходного сырья. Конечно, чем больше производительность, тем ниже себестоимость 1 м3 продукции.
Согласно данным японских экспертов, барабанный (групповой) способ получения балансов из колотых дров снабжает более большой процент нужного выхода если сравнивать с личным способом на станках проходного типа. Одновременно с этим направляться очень выделить, что приобретаемые в барабанах сухого трения балансы не предназначаются для продажи в Японии.
Тут же на предприятии, значительно чаще в составе той же линии, эти балансы преобразовываются в щепу, которая сортируется и лишь затем возможно реализована потребителю. Это показывает, что балансы, полученные так, не имеют товарного вида. Помимо этого, металлоемкость, энергоемкость, прочие данные и производительность этого способа применения низкокачественного и низкосортного сырья говорят о возможности его применения или лишь на ЦБК, или, в виде исключения, на наибольших нижних складах в наборе с оборудованием чтобы получить щепу.
Анализ разных способов получения балансов из низкосортного н опыта работы и низкокачественного сырья станков и линий, предназначенных для этих целей, но различных по конструкции, исполнению и составу, разрешает утверждать, что для леспромхозов, где в смену вывозится в среднем около 100 м3 дров, направляться применять такие механизмы, у которых окорки удаления и процесс гнили объединены в одном станке. Приобретаемая наряду с этим продукция имеет хороший товарный вид и не обязательно тут же должна быть перевоплощена в щепу. Готовая продукция с таких фирм с успехом возможно реализована в виде отличных балансов, а также для получения сульфитной целлюлозы вискозного производства и на экспорт.
Для фирм с громадным числом дровяной древесины, предназначенной для изготовления из нее балансов, а также прежде всего для ЦБК, смогут быть рекомендованы два главных метода их получения:
1. Удаление коры на окорочном станке, раскряжевка, расколка, выколка гнили на особых станках.
2. Раскряжевка, расколка (распиливание), удаление коры и гнили групповым методом, способом сухого трения в барабанах.
Рис. 3. Неспециализированный вид станка модели Н8 для получения балансов из колотых дров
Серийно производимый станок модели Н8 имеет сварную, коробчатой формы станину, на которой смонтированы главные механизмы:
— двухцепной подающий транспортер с профильными толкающими траверсами, приводной и натяжной станциями;
— фрезерная, шестиножевая, окорочная головка с электроприводом;
— устройство для срезания гнили, транспортирования срезанных прижимания и кусков фрезеруемого полена к столу.
Устройство складывается из кольцевого ножа и соединенного с ним желоба. Перемещение его на высоту срезаемой гнили осуществляется посредством рычажной совокупности, приводимой в перемещение гидроцилиндром. Величину перемещения задает станочник, определяющий ее по копиру-флажку, дублирующему положение кольцевого ножа.
Финиш этого флажка, совмещенный с нижней границей гнили в полене, определяет высоту размещения кольцевого ножа. Режущие органы, как и все движущиеся части станка, закрыты ограждениями и специальным кожухом, снабжающими безопасность трудящихся.
В зависимости от технологических изюминок привязки станка к остальным сооружениям нижнего склада подача поленьев на транспортер станка может производиться с его торца, т. е. в продольном направлении, по оси станка, либо сбоку.
Расколотые поленья, независимо от направления их перемещения по отношению к продольной оси станка подаются к нему ленточным транспортером. Данный транспортер равно как и транспортер уборки отходов, проходящий на протяжении станка под полом, входит в набор оборудования, поставляемого со станком, и совместно составляют механизированную линию ЛО-12 для получения балансов из колотых дров.
Последовательность срабатывания механизмов станка приведена на кинематической схеме. При боковой подаче поленьев на станок срабатывание механизма поштучной выдачи поленьев происходит при повороте вала, на котором укреплены рычаги отсекателя. Данный поворот осуществляется зацеплением цевки приводного устройства с прорезью мальтийского креста.
Привод диска с цевкой производится от ведомого (натяжного) вала подающего транспортера. Передаточное отношение приводной совокупности мальтийского креста подобрано так, дабы он совершал поворот на 90° и выдачу очередного полена за время прохождения очередной траверсой пути, равного расстоянию между двумя смежными траверсами. Всего на цепях три траверсы.
При подаче сырья с торца станка механизм боковой поштучной отсекания и выдачи поленьев отключается и заменяется на механизм торцовой поштучной подачи поленьев на цепи транспортера станка.
Комплектование станка тем либо иным механизмом подачи поленьев на обработку производится по требованию клиента. Регулировка фрезерной головки на величину снимаемого слоя равно как и регулировка приемного стола станка, производится особыми гайками-стяжками.
Из кинематической схемы станка направляться, что время прохождения поленом пути, равного расстоянию между траверсами, при большой скорости цепи подающего транспортера 0,6 м/сек, равняется 5,41 сек. Протяженность полена колеблется около 1000 мм. Вследствие этого на его обработку, с учетом времени выхода и входа ножа в древесину, требуется не меньше 2 сек.
За оставшиеся 3—4 сек оператор обязан оценить уровень качества поданного на станок полена, в случае если необходимо, исправить его положение и поворотом штурвала совместить нижний край флажка—указателя с границей размещения гнили в полене, задавая тем самым величину перемещения кольцевого ножа по высоте. При помощи рычагов штанга с флажком-указателем связана с сектором, на котором укреплены микропереключатели.
Рис. 5. Кинематическая схема станка модели Н8 для получения балансов из колотых дров:
1 — фрезерная головка; 2 — кольцевой нож; 3 — подающий двухцепной транспортер с траверсами; 4 — механизм заказа величины скалываемой гнили; 5 — опускания и гидроцилиндр подъёма жёлоба и кольцевого ножа; 6 — натяжное устройство подающего транспортера; 7 — лоток для удаления кусковых отходов; 8 — следящий аккуратный механизм установки размера скалываемой гнили; 9 — механизм отсекания и поштучной боковой подачи поленьев на станок; 10 — кулачок командного устройства
Один из них ВКВ, будучи включенным, дает команду на перемещение кольцевого ножа вверх, второй ВКЦ вниз. Разумеется, что срабатывание того либо иного микропереключателя определяется направлением поворота сектора. Но в момент настройки на величину перемещения ножа по высоте микропереключатели обесточены и не срабатывают , пока из-под кольцевого ножа и прижимающего желоба не выйдет прошлое полено.
В момент его выхода из-под падения и жёлоба в лоток к очередному полену подходит следующая траверса и подхватывает его. Лишь сейчас в совокупности кулачков, установленных на секторе, появляется ток.
Команду на включение тока подает второй кулачок, связанный зубчатой передачей с приводным валом подающего транспортера. Передаточное отношение подобрано так, дабы кулачок, включающий ток в совокупности управления, делал бы один оборот за время прохождения расстояния между траверсами. Подходя в момент падения готового баланса в лоток к микропереключателю В К, у которого на схеме указано «пуск», данный кулачок включает ток и начинается перемещение ножа.
Совокупностью тяг, делающих функцию обратной связи, нож связан с кулачком совокупности управления. Вращаясь при перемещении ножа, данный кулачок выходит из контакта с микропереключателем, укрепленным на секторе. Когда кулачок выходит из контакта с микропереключателем, совокупность обесточивается и перемещение ножа, достигшего заданного положения, заканчивается.
При предстоящем вращении кулачок, который связан с подающим транспортером, подходит к микропереключателю ВКП, у которого на схеме указано «поджим». Соприкасаясь с ним, кулачок дает команду для включения электромагнитов золотника. Обрабатываемое полено нижней частью желоба прижимается к рифленым направляющим станка и, основное, к ножам фрезерной головки, срезающим кору. Цикл обработки кончается когда полено выходит из-под прижимающего его желоба и падает в лоток.
Цикл обработки следующего полена начинается когда кулачок снова замкнет микропереключатель ВК «пуск». За это время оператор уже установил направление перемещения и нужную величину ножей для обработки очередного полена и по окончании прохождения кулачком микропереключателя «пуск» цикл обработки повторяется.
Если оператор опоздал уложить полено либо дать приказ на перемещение ножа, цикл повторяется при сохранении заданного по прошлому полену положению ножа.
Характеристика серийно производимого станка Н8 приведена ниже.
Станок АБС-2 кроме этого имеет сварную, коробчатого сечения станину. Вместо двух фрезерных окорочных головок, как было на станке АБС-1, у новой модели покинута одна. Снята фрезерная головка, которая выфрезеровывала остатки гнили по окончании срезания главной ее части плоским ножом. Так, станок АБС-2 в принципе повторяет конструкцию станка Н8.
Но наряду с этим между ними остается значительная отличие, пребывающая в том, что подающий транспортер у станка АБС-2 одноцепной, почему он в отличие от транспортера у станка Н8 не проталкивает полено через целый станок, а доводит его лишь до фрезерной головки. Дофрезеровывание и выталкивание застрявшего на фрезерной головке полена производится очередным поленом, поступающим на обработку.
Срезание гнили, как и у станка АБС-1, осуществляется плоским ножом, что в отличие от кольцевого ножа ведет к излишним утратам здоровой древесины. Плита, на которой закреплен плоский нож, перемещается по высоте по двум колоннам-направляющим вручную при зубчатого зацепления и помощи рычага.
Рис. 6. Неспециализированный вид станка модели АБС-2 для получения балансов из кололотых дров
Гниль сталкивается особым механизмом в боковом направлении, сразу же по окончании ее срезания. программирования и Элементы автоматизации в совокупности управления, имеющиеся в станке Н8 и существенно облегчающие труд рабочего, в этом станке отсутствуют.
Процесс замены режущего инструмента, снятие фрезерной головки, на станке АБС-2 пара сложнее, чем у станка Н8. В остальном их обслуживание и эксплуатация аналогичны.
Станки типа АБС, Н8 и им подобные являются проходными. Их сменная производительность (по сырью) возможно выяснена по формуле для проходных станков, приведенной в прошлой главе.