Основы резания металлов
Неспециализированные понятия о токарной обработке металлов. Токарная обработка — это технологическая операция обработки тел вращения заданной размеров и формы при помощи снятия стружки режущим инструментом при вращении заготовки (рис. 1) на токарном станке.
самоё широкое распространение взяли следующие виды работ: обработка наружных цилиндрических (рис. 2, а), конических (рис. 2, б) и фасонных (рис.
2, в) поверхностей; обработка внутренних цилиндрических (рис. 3, а),.конических (рис. 3, б) и фасонных (рис. 3, в) поверхностей;
подрезание торцов (рис. 4, а);протачивание наружных (рис. 4, б) и внутренних (рис. 4,в) канавок; нарезание наружных (рис. 5, б, в) и внутренних (рис. 5, а, г) резьб и образование рифленой поверхности (рис.
6).
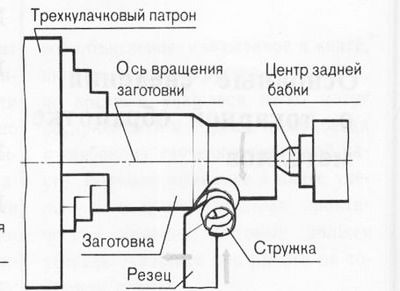
Рис. 1. Схема получения тел вращения при помощи снятия стружки
Рис. 2. Обработна наружных поверхностей
Рис. 3. Обработка внутренних поверхностей
Рис. 4. 0бработна торцов и канавон
Рис. 5. Нарезание резьбы резцом (а, б), плашной (в) и метчиком (г)
Рис. 6. Накатка
Для исполнения токарных работ используют следующие виды режущего инструмента: резцы (рис. 7, а), сверла (рис. 7,6), развертки (рис.
7, в), зенкеры (рис. 7,г), зенковки (рис. 7, д), метчики (рис. 8, а) и плашки (рис. 8, б).
Рис. 7. Виды режущего инструмента
Рис. 8. Метчини и плашки
Рис. 9. Методы измерения линейкой (а), нронцирнулем (б) и нутромером (в)
Для деталей и измерения заготовок применяют металлические линейки, кронциркули, нутромеры (рис. 9), штангенциркули (рис. 10, а), глубиномеры (рис. 10,6), микрометры (рис.
11), шаблоны, скобы и калибры (рис. 12).
Рис. 10.Методы измерения: штангенциркулем (а) и глубиномером (б): Dh— наружный диаметр; Рв-внутренний диаметр; Н-глубина отверстия
Рис. 11. Микрометр
Рис. 13.Крепление заготовок на тонарном станне
Рис. 14. Резцедержатель
Заготовки на токарном станке крепят з патроне, центрах, в люнете и на планшайбе (рис. 13). Режущий инструмент крепят в резцедержателе (рис.
14), в пиноли задней бабки (рис. 15, а), плашкодержателях (рис. 15,6) и воротках (рис. 15, в).
Токарные станки производят разными по назначению, размерам и техническим возможностям. То-карно-винторезные станки (рис. 16)—это универсальные станки, предназначенные для исполнения разнообразных токарных работ.
Передняя бабка станка является опорой для шпинделя, передающего вращение заготовке либо инструменту, задняя бабка — для устройства, поддерживающего заготовку.
Суппорт — главной рабочий орган станка, предназначенный для перемещения и закрепления при обработке режущих инструментов либо заготовки.
Рис. 15. Крепление режущего инструмента
Рис. 17. Токарно-револьверный станок 1А341: 1—станина; 2 — коробка подач; 3 — рукоятки переключения; 4 — передняя бабка; 5—револьверная головка; 6—суппорт; 7—упор; 8—маховичок поворота револьверной головки; 9 — штурвал перемещения суппорта; 10 — цанга
Токарно-револьверные станки (рис. 17) снабжены многорезцовыми головками. Головки по размещению бывают горизонтальными и вертикальными и помогают для установки режущего инструмента.
Токарно-револьверные станки предназначены для обработки однотипных подробностей в условиях массового производства.
Рис. 19. Токарно-затыловочныи станок
Рис. 20. Токарно-карусельный станок
Коробка подач станка — многозвенный механизм, предназначенный для направления подачи и изменения скорости.
Многорезцовые токарные станки (рис. 18) предназначены для высокопроизводительной обработки подробностей в условиях серийного и массового производства. Это достигается применением в один момент нескольких резцов, закрепленных в резцедержателе суппорта.
Токарно-затыловочный станок (рис. 19, а) рекомендован для обработки задних поверхностей зубьев зуборезного и резьбонарезного инструмента. Изюминкой станка есть наличие передачи (рис. 19, б) от распределительного вала станка на кулачок и вертикальный вал, расположенный в центре основания суппорта.
Поворотная плита возможно установлена под углом довольно нижней части суппорта. Эта поворотная часть соединена с плитой, в которую запрессован палец, при помощи которого плита совершает возвратно-поступательные перемещения.
Токарно-карусельный станок (рис. 20) рекомендован для обработки заготовок диаметром до 1500 мм, имеет одну вертикальную стойку несущую на себе траверсу (поперечину), на протяжении которой может перемещаться каретка с поворотным резцедержателем (револьверной головкой). По вертикальным направляющим стойки может перемещаться боковой суппорт с резцедержателем.
Заготовку устанавливают на горизонтальной планшайбе.
Двухстоечный токарно-карусель-ный станок (рис. 21) используют при обработке заготовок диаметром более чем 1500 мм. Главные узлы: планшайба и станина, две стойки, скрепленные между собой балкой. По вертикальным направляющим стоек посредством вертикальных ходовых винтов, перемещающихся от электродвигателя, может перемещаться траверса. По ее горизонтальным направляющим перемещаются два вертикальных суппорта.
Пульт рекомендован для дистанционного управления станком. Револьверная головка перемещается маховичками.
Лобовые станки (рис. 22) помогают для обработки заготовок громадных малых и диаметров длин. На передней бабке лобового станка закреплена планшайба, на которой устанавливают заготовку. Задняя бабка у лобовых станков отсутствует. Поперечная станина с двумя суппортами расположена на отдельной плите.
Средняя часть суппорта установлена параллельно либо под углом к оси шпинделя и к верхней части с резцедержателем.
Рис. 21. Двухстоечный тонарно-нарусельный станок
По управлению крепления и способу заготовок токарные станки подразделяют на станки с ручным управлением, полуавтоматы и автоматы. Станки с ручным управлением (рис. 23)— это простые универсальные станки, на которых снятие и установку заготовки, отвод и подвод резца 2 реализовывают вручную.
В случае если снятие и установку заготовки 3 (рис. 24) создают вручную, а целый цикл обработки (отвод и подвод резцов 1 и 2, установка на размер и т. д.) производится в автоматическом цикле, то такие станки именуют полуавтоматическими.
Рис. 23.Схема обработки на токарном станне с ручным управлением
Рис. 25. Схема обработни на автомате: а — положение резцовой головки и зажимного устройства при подаче прутна; б — положение резцовой головки и зажимного устройства в ходе точения
В случае если станок трудится по заданной программе без яркого участия человека, т. е. снятие и загрузка заготовки (рис. 25), отвод и подвод резцов, установка на контроль и размер производятся машинально, то такие станки именуют автоматами.
Применяют кроме этого особые агрегатные станки, каковые складываются из унифицированных, кинематически не связанных между собой агрегатов. Их используют в крупносерийном и массовом производствах.
Рис. 24. Схема обработни на токарном полуавтомате
Сущность процесса резания. Для осуществления процесса резания нужно сотрудничество двух перемещений — главного Ог и перемещения подачи Ds (рис. 26). Основное перемещение в токарных станках — вращательное, определяющее скорость резания и информируемое, в большинстве случаев, заготовке.
Перемещением подачи именуют перемещение, создаваемое механизмом подачи и информируемое инструменту. Снятие стружки осуществляется при вращательном главном перемещении, информируемом заготовке, и прямолинейном перемещении резца.
Рис. 26. Элементы перемещений в ходе резания при обтачивании: 1 — направление скорости результирующего перемещения; 2 — направление скорости главного перемещения резания; 3 — рабочая плоскость Ps; 4 — разглядываемая точка режущей кромки; 5 — направление скорости перемещения подачи; V-скорость главного перемещения резания; ve —скорость результирующего перемещения резания; vs— скорость перемещения подачи;
Рис. 27. Сотрудничество обрабатываемой поверхности с резцом
Рис. 28. Виды поверхностей на обрабатываемой заготовке
Сотрудничество обрабатываемой поверхности с резцом продемонстрировано на рис. 27. Плоскость, совершённую касательно к режущей кромке, перпендикулярную к главной плоскости, именуют плоскостью резания.
Плоскость, проведенная через разглядываемую точку режущей кромки перпендикулярно к скорости главного перемещения, именуют главной плоскостью.
Различают три вида поверхностей (рис. 28): 1 —обрабатываемую (поверхность заготовки до обработки), 2 — обработанную (поверхность по окончании обработки) и поверхность резания R, образуемая режущей кромкой в результирующем перемещении резания.
Процесс резания подобен процессу раскалывания и вероятен лишь при приложении к режущему клину силы Р, которая больше сил сопротивления материала заготовки (рис. 29).
Главные элементы резца. Резец (рис. 30) есть режущим инструментом и складывается из державки и головки.
Головка резца есть его режущей частью. Крепят резец за державку. Головка резца имеет форму клина и имеет несколько кромок и поверхностей. Передней поверхностью именуют поверхность лезвия инструмента, контактирующую в ходе резания со срезаемым стружкой и слоем.
Основная задняя поверхность — поверхность лезвия, примыкающая к основной режущей кромке. Основная режущая кромка лезвия образуется пересечением передней и основной задней поверхностей; — запасной режущая кромка. Вершиной лезвия именуют участок режущей кромки в месте пересечения двух задних (основной и вспомогательной) поверхностей.
кромки и Плоскости резца расположены под следующими углами: (рис. 31). Основной передний угол 7 — угол в секущей плоскости N — N между передней основной плоскостью и поверхностью лезвия; основной задний угол а — угол между главной плоскостью резания и задней поверхностью резца; основной угол заострения (3 — угол в секущей плоскости между передней и задней поверхностями лезвия; угол в плане Ф — угол в главной плоскости между рабочей плоскостью и плоскостью резания; вспомогательный угол ф1 — угол между проекцией запасном режущей кромки на главную плоскость и направлением подачи; угол при вершине в плане е образуется проекциями основной и запасном режущих кромок на главную плоскость; угол наклона кромки К — угол в плоскости резания между режущей основной плоскостью и кромкой.
Рис. 29. Схема работы резца
Рис. 30. Геометрические элементы токаоного резца
Рис. 31. Углы резца
Рис. 32. Основной передний угол
Рис. 33. Угол нанлона режущей нромни
Рис. 34. Угол в плане
Рис. 35. Установка вершины резца относительно оси заготовки
Рис. 36. Стружнообразование
Рис. 37. Виды стружек
Углы у (рис. 32) и А, (рис. 33) смогут быть хорошими, отрицательными и равными нулю. Угол в плане ф в зависимости от вида обработки изменяется от 30 до 90° (рис.
34). задние углы и Передние изменяются в зависимости от установки резца по оси (рис. 35, а), выше оси (рис. 35, б) и ниже оси (рис. 35, в) заготовки.
При установке резца выше оси заготовки передний угол возрастает, при установке ниже — значительно уменьшается.
Рис. 38. Направление схода стружни
Рис. 39. Параметры резания при протачивании (а),растачивании (б) и прорезании (в)
Рис. 40. Подача Sq проходного (а), расточного (б) и подрезного (в) резца, соответствующая одному обороту заготовки
Стружкообразование. При постоянном действии силы Р на резец (рис. 36) режущая кромка врезается в материал заготовки, уплотняя его передней поверхностью и отделяя в виде стружки. В зависимости от условий резания и материала заготовки в ходе обработки срезается разная по виду стружка: сливная (рис.
37, а)—при обработке вязких материалов, скалывания (рис. 37,6)—при обработке жёстких материалов, надлома (рис. 37, в)—при обработке хрупких материалов.
Направление схода стружки зависит от угла наклона основной режущей кромки X (рис. 38). При А = 0 стружка отводится в направлении, перпендикулярном к режущей кромке.
При хорошем К стружка сходит в направлении обработанной поверхности, при отрицательном — по направлению перемещения резца.
Режимы резания. При работе на токарных станках задают следующие параметры: глубину резания t, мм; подачу S, мм/об; скорость резания v, м/мин (рис. 39).
Глубиной резания именуют толщину срезаемого слоя металла за один рабочий движение инструмента, измеряют как расстояние между обработанной и обрабатываемой поверхностями заготовки. При точении t — (D — d)/2.
При точении, фрезеровании и сверлении применяют понятие подача на оборот S0, мм/об, т. е. перемещение режущего инструмента довольно обрабатываемой поверхности за один оборот заготовки (рис. 40).
Рис. 41. Формирование площади сечения срезаемого слоя в ходе протачивания (а), растачивания (б) и прорезания (в)
Рис. 42. Определение снорости резания
Рис. 43. Силы, действующие в ходе резания
Разглядим понятие скорости резания (рис. 42). Точка А, находящаяся на окружности диаметром D, за один оборот заготовки проходит путь, равный длине окружности. Протяженность окружности в 3,14 раза больше ее диаметра.
Следовательно, точка А за один оборот совершит путь 3,14 либо nD. Заготовка за 1 мин совершит п оборотов. Путь, что пройдет точка А, равен произведению длины окружности на число оборотов в 60 секунд: nDn, мм/мин. Путь, пройденный точкой А за 1 мин, именуют ее окружной скоростью.
Точки А и Б, лежащие на окружностях различных диаметров Dud заготовки, при вращении пройдут за один оборот пути различной длины: точка А пройдет путь, равный яД а точка Б — путь nd. За время полного оборота заготовки точка А, лежащая на большей окружности диаметром D, обязана пройти больший путь, чем точка Б, лежащая на меньшей окружности диаметром d, т. е. она обязана двигаться стремительнее и иметь, следовательно, громадную окружную скорость.
В случае если основное перемещение резания есть вращательным, то скорость резания и = л?)«/1000, м/мин, где D — громаднейший диаметр заготовки; п — частота вращения инструмента, мин-1. Скоростью резания возможно именовать путь, проходимый режущей кромкой инструмента в 60 секунд относительно поверхности заготовки. Следовательно, скорость резания имеется не что иное, как окружная скорость заготовки.
Рис. 44. Влияние угла в плане на силы Pz(1) и Ру(2)
Рис. 45. Изменение силы Pz от napaMeTpoet mS0
Рис. 46. Изменение сил Р, Р ,Р отснорости резания v
Сила резания. При точении силу резания Р раскладывают на три составляющие (рис. 43).
Основная составляющая Рг сходится по направлению со скоростью главного перемещения резания. С учетом силы Рг рассчитывают на прочность резца и детали. Осевая составляющая Рх действует параллельно оси главного вращательного перемещения резания. По данной силе рассчитывают механизм продольной подачи станка и изгибающий момент, действующий на резец.
Радиальная составляющая Ру направлена по радиусу главного перемещения резания, отжимает резец от заготовки и прогибает заготовку. При обычных условиях резания сила Pz в 4—8 раза больше осевой силы Р, ив 2—3 раза больше силы Ру.
С повышением угла в плане (р составляющие Ру и Рг уменьшаются (рис. 44). При увеличении твердости обрабатываемого материала, глубины резания t и подачи S0 составляющая Рг возрастает (рис.
45). С повышением скорости резания составляющие силы резания изменяются незначительно (рис. 46).
Рис. 47. Распределение теплоты в зоне резания
Рис. 48. Подача СОЖ в зону резания
Рис. 49. Виды передач в тонарных станках
Тепловыделение в зоне резания и СОЖ. В ходе обработки в зоне резания выделяется много теплоты, под действием которой режущий инструмент нагревается (рис. 47). Для уменьшения нагрева заготовки (рис.
48) при обработке используют смазочно-охлаж-дающую жидкость (СОЖ). Под смазочным действием знают свойство СОЖ образовывать на контактных поверхностях инструмента, детали и стружке прочные пленки, всецело либо частично предотвращающие соприкосновение передней поверхности резца со стружкой и задних поверхностей резца с поверхностью резания.