От ока до изотопа и эвм
В базе литейного производства лежит тяжёлая задача укрощения капризного, талантливого всегда изменять собственные свойства литого получения и металла из него качественной фасонной отливки.
Трудности ответа данной задачи обусловливаются двумя главными факторами. Во-первых, разными условиями формирования отливок. Они зависят от неизменно изменяющихся технологических условий (режимы и составы плавки шихты, условия и уровень качества обработки выплавленного расплава, скорость его кристаллизации в форме и т. д.). Вследствие этого механические и другие свойства подробностей, взятых из одной и той же плавки, сплошь и рядом быстро разняться между собой.
Во-вторых, отсутствием яркой наглядности большинства литейных процессов (плавка, графитизация чугуна, модифицирование расплавов, формирование отливки в форме).
Предки — ветхие русские мастера-литейщики укрощали литой металл своим мастерством, основанным на личном опыте. Не было у них ассистентов-устройств, а потому осуществлялся единственный способ визуального контроля отливок. Пользуясь собственными глазами — «окулярами», контролер дробил создаваемые в цехе отливки на годные и брак.
На данный момент уровень развития науки, технологии и техники литейного производства достиг невиданных высот. Сейчас литейщики обязаны заботиться не только о получении литых заготовок, но и о качестве изготовленных из них подробностей, т. е. отливок, прошедших механическую обработку. Исходя из этого контролю в современных литейных цехах уделяется огромное и всевозрастающее внимание.
В отечественных литейных цехах используют две совокупности контроля — профилактический и аккуратный. Профилактический контроль осуществляется конкретно на производственных участках цеха. В лаборатории формовочных материалов смесепри-готовительного участка особая аппаратура оказывает помощь осуществлять контроль свойства составов формовочных и стержневых смесей; на участке формовки устройствами-твердомерами реализовывают контроль степени уплотнения смеси в формах, а особыми шаблонами — правильность установки стержней в форму; в экспресс-лаборатории плавильного участка устанавливают состав приготавливаемых расплавов; на площадке технологических проб определяют температуру, другие свойства и жидкотекучесть литейных расплавов.
Аккуратный контроль осуществляется на намерено выделенных участках цеха. На площадках наружного осмотра отливок визуальному (невооруженным глазом либо посредством лупы, дающей 30-кратное повышение) контролю подвергается вся продукция литейного цеха с целью обнаружения брака либо отливок, подлежащих исправлению. На контрольных плитах методом разметки контролируют правильность геометрии отливок.
На стендах гидравлических опробований плотность металла отливок контролируют методом введения в полость отливок воды под высоким (до 200 ат) давлением.
Для контроля свежих формовочных и шихтовых материалов, всесторонней проверки качества взятых отливок, обнаружения обстоятельств найденных в них недостатков, и с целью проведения анализов по заданию исследовательских бригад, осуществляющих мероприятия по борьбе с браком и увеличению качества отливок, в современных литейных цехах созданы особые лаборатории (химическая, металлографическая, рентгеновская и др.).
Действенность цехового контроля обусловливается тем, что его функции реализовывают работники отдела технического контроля (ОТК), входящего в состав работ предприятия и не подчиняющегося главе литейного цеха.
Последние годы свойственны все громадным применением в литейном производстве особых способов контроля, основанных на применении радиоактивных изотопов, современной аппаратуры и новейших приборов, впредь до электронно-вычислительных автомобилей (ЭВМ).
Невидимые невооруженным глазом небольшие трещины, залегающие на малом (0,4 ч- 0,6 мм) глубине либо частично выходящие на поверхность отливок, значительно чаще выявляются способом магнитной дефектоскопии. Способ основан на свойстве потока магнитных силовых линий, проходящих через намагниченную отливку, поменять собственный направление либо рассеиваться около неметаллических включений и трещин.
В месте размещения скрытого недостатка рассеявшийся по его очертаниям поток магнитных силовых линий образует дополнительные полюсы S и N. В случае если загрузить отливку в бак с растворителем (минеральное масло, керосин, бензин), где во взвешенном состоянии находится магнитный порошок окиси железа, то порошок соберется у дополнительных магнитных полюсов и, так, распознает границы недостатка. Намагничивание отливок производится особым прибором — дефектоскопом. Магнитный способ на данный момент используется как для обнаружения небольших трещин в отливках из серого чугуна и стали, так и трещин в отливках из ковкого чугуна, формирующихся в литейной форме.
На рис. 2 продемонстрирована современная установка для скоростного флуоресцентно-магнитного контроля металлических литых колес ЖД транспорта. Особенность способа содержится в том, что в жидкость с магнитным порошком окиси железа вводит флуоресцирующее вещество (люминофор, дефектоль), талантливое светиться при облучении его ультрафиолетовыми лучами.
Установка складывается из катушки дефектоскопа, которая подвешивается к перемещающемуся брусу, электрического агрегата для ее питания током низкого напряжения, бака с флуоресцирующей жидкостью и двух ламп ультрафиолетового света мощностью по 400 вт.
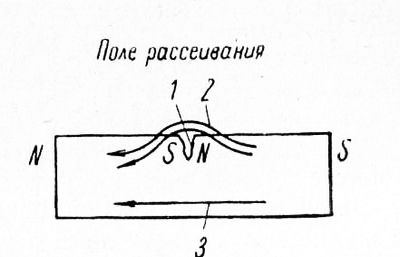
Рис. 1. Изменение потока магнитных силовых линий в металлическом изделии при наличии недостатка: 1 — трещина; 2 — магнитный поток в дефектной части отливки; 3 — магнитный поток в здоровой части отливки.
Рис. 2. Установка для скоростного флуоресцентно-магнитно:. го способа контроля металлических литых колес.
При наличии недостатка капиллярные силы удерживают флуоресцирующую жидкость в трещины, границы которой под действием ультрафиолетовых лучей будут светиться красным, голубоватым либо зеленоватым светом.
Производительность контрольной установки достигает 55—60 колес в час.
Как посмотреть вовнутрь отливки? Так как есть вероятность происхождения в ней внутренних усадочных раковин, других дефектов и газовой пористости. При массовом выпуске их наличие весьма легко устанавливается взвешиванием отливок: в случае если масса отливки если сравнивать с контрольной занижена, значит, отливка с внутренним недостатком. Но для успешной борьбы с внутренними пороками отливок этого мало.
Нужно знать еще их размеры, место и форму размещения. В этом случае прибегают к рентгенодефектоскопии — просвечиванию отливок посредством рентгеновских лучей, талантливых попадать через толщу металла. Внутренний порок отливки четко фиксируется на находящейся в кассете фотопленке, по причине того, что в месте его размещения отправляемые рентгеновской трубкой лучи легче попадают через металл, а следовательно, в основном воздействуют на эмульсию, оставляя на ней (по окончании проявления пленки) чёрные пятна.
Сейчас рентгеновские лучи в сочетании с телевизионными установками и кинокамерами стали использоваться для постоянного изучения процессов литья. Наряду с этим замечательная рентгеновская трубка устанавливается по одну сторону от формы, в которую из ковша заливают расплав. По другую сторону формы устанавливают флуоресцирующий экран.
Изображение с экрана передается оптической совокупностью на светочувствительную поверхность телевизионной трубки, электрические сигналы которой усиливаются в блоке и регистрируются на магнитной пленке видеорекордера. Параллельно сигналы поступают к телевизору. С его экрана изображение снимается кинокамерой (со скоростью до 50 кадров в секунду) либо фотоаппаратом.
Изображение может в один момент передаваться и на другие телевизионные приемники.
Рис. 3. Схема просвечивания отливки рентгеновскими лучами.
Рис. 4. Схема изучения процесса литья способом рентгено-кинематографии.
Использование рентгенокинематографии разрешает изучать особенности процессов заливки форм в зависимости от состава плотности и формовочной смеси ее набивки, других условий и перегрева расплава литья для того, чтобы на базе взятых разрешённых разработать советы для проектирования литниковых совокупностей, размещения в форме доходов, других элементов и холодильников, снабжающих получение качественных отливок при большом выходе годного литья.
При разбраковке отливок (с делением на годные, дефектные и бракованные), в то время, когда контроль нужен для оценки приблизительных положения и размеров недостатка, используют способ ультразвуковой дефектоскопии. В отличие от рентгеновского способа всецело автоматизированные ультразвуковые опробования смогут производиться менее квалифицированным персоналом. Малые размеры дефектоскопов допускают их установку в любом месте.
Ультразвуком возможно осуществлять контроль отливки толщиной более чем 1 м. Способ основан на способности ультразвуковых (частота от 500 тыс. до 10 млн. периодов в секунду) волн проходить через плотные однородные тела и задерживаться при встрече с раковиной, трещиной либо вторым каким-либо препятствием.
Ультразвуковой дефектоскоп складывается из лампового генератора (формирует переменное электрическое напряжение высокой частоты), излучателя с пластинкой из кварца, титанита либо бария (преобразует электрические колебания в ультразвуковые), приемника с такой же пластинкой (преобразует ультразвуковые колебания обратно в электрические) и осциллоскопа, на экране которого получается условное световое изображение внутренних пороков отливки. При контроле излучатель хорошо прикладывается к исследуемой отливке.
Генератор отправляет порцию электрических колебаний, а излучатель — луч в отливку, благодаря которому приводятся в колебание частицы отливки, расположенные по одной прямой. Достигнув противоположной стороны отливки, ультразвуковые колебания отразятся и направятся вверх. В случае если в этом месте поставить приемник с кварцевой пластинкой, то она преобразует ультразвуковые колебания в электрические. В следствии на волнистой световой линии экрана осциллоскопа покажется пик (всплеск).
Значит, ультразвуковой луч свободно прошел через толщу отливки и, следовательно, внутренние недостатки в металле отсутствуют. При наличии в металле отливки внутреннего порока на экране осциллоскопа покажутся два пика: конечный правый, являющийся, как и в прошлом случае, донным знаком, а второй — в средней части экрана, соответствующий недостатку. В следствии совершённых у нас изучений заключили, что ультразвуковой контроль может использоваться для неразрушающего (без вырезания образцов из отливки) термической предела выносливости и определения прочности отливок из обычного либо малолегированного серого чугуна.
Рис. 5. Распространение ультразвуковых волн при контроле здоровой (а) и дефектной (б) отливок.
Для обнаружения внутренних пороков отливок литейщики используют кроме этого и радиоактивные изотопы. Изотоп — разновидность химического элемента, весьма сходная по практически всем особенностей с главным элементом, которая отличается от него лишь строением ядра атома. Если сравнивать с рентгеновским способом гамма-дефектоскопия имеет последовательность преимуществ: отсутствие громоздкой аппаратуры, свойство просвечивать отливки большей толщины, поскольку гамма-лучи являются более твёрдыми (отличаются меньшей длиной волны), возможность обнаружения внутренних пороков в металле больших отливок и в труднодоступных их местах.
На данный момент, с учетом толщины стенок контролируемых металлических отливок, используют не-VoTbKO радиоактивных изотопов: кобальт-60 с,с,‘45-=-274,8 мм), иридий-192 (17,8-50,8 мм), туллий-170 (5,1-4-30,5 мм), натрий-24 (101,6-5-304,8 мм), цезий-137 (38 ь 101,6 мм) , тантал-182 (25,4:- 174,8 мм).
Изотопы приобретают облучением природных нера-диоактивных элементов разными ядерными частицами (тепловыми нейтронами в ядерном реакторе), выделением продуктов распада ядерного топлива по окончании его применения в ядерном реакторе и бомбардировкой природных элементов в разных ускорителях. Если сравнивать с естественными (радий, актиний, полоний, уран и др.), и искусственно создаваемыми (нептуний, плутоний и др.) радиоактивными элементами изотопы нерадиоактивкых элементов значительно дешевле. С учетом этого на данный момент для просвечивания гамма-лучами используют практически только радиоактивнее изотопы и в основном лучший из них — кобальт-60.
При подготовке к гаммаграфированию маленькое количество радиоактивного изотопа помещают в особую ампулу. После этого ампулу вводят в свинцовый контейнер, где ее держат перед контролем в положении хранения. На протяжении контроля отливки ампула продвигается до рабочего окна контейнера и облучает отливку направленным пучком лучей.
Полное выдвижение заряженной ампулы из контейнера недопустимо, поскольку может привести к облучению персонала .
При радиографии пользуются несколькими приемами: группу отливок располагают около одного источника гамма-лучей с получением в один момент гаммаграмм всех отливок; источник гамма-лучей помещают в центр цилиндрической отливки, а серию фотопленок — на его наружной поверхности; источник помещают на некоем расстоянии от отливки, в то время, когда направление гамма-лучей перпендикулярно ее плоскости.
Наровне с контролем отливок на данный момент радиоактивные изотопы используются при отработке литейной разработки, для изучения действия доходов при формировании отливок, проверки работы графитовых пробок стопорных сталеразливочных ковшей и в других случаях практики литейного производства.
Аппаратура гамма-дефектоскопии, предназначенная для проверки экспериментальных отливок перед началом их отработки и серийного производства литниковых совокупностей литейного цеха ковкого чугуна, складывается из пушки с зарядом кобальта-60. Заряд, имеющий размеры карандашной резинки, заложен в капсюль из нержавеющей стали и помещен в центре свинцового контейнера.
Пушка находится в помещения без окон, со стенками из литого бетона толщиной 0,9 м и для удобства радиографирования снабжена совокупностью передвижения. В помещении установлен прибор автоматической регистрации уровня гамма-излучения в миллирентгенах. Радиографирова-ние разрешило отработать литниковые совокупности для последовательности сложных автомобильных отливок (картер дифференциала, картер руля, соединительная вилка, шатун и др.).
Рис. 6. Ампула естественного радиоактивного элемента радия:
1 — радий; 2 — ампула стеклянная; 3 — чехол латунный; 4 — амортизаторы резиновые; 5 — пломба.
Рис. 7. Контейнер для гаммаграфирования изотопом кобальт-60:
а) — ампула в положении хранения; б) — ампула светит направленным пучком; в) — ампула вне защитного кожуха; 1 — наружный защитный кожух; 2 — выемной кожух; 3 — ампула.
В СССР создан прибор для измерения стержней литейных и плотности форм радиоизотопным способом, конструкция которого была создана отделом радиоактивных изучений Университета неприятностей литья Академии наук УССР. Прибор универсален, поскольку разрешает измерять плотность набивки литейных форм, изготовленных по любой технологии и из разных формовочных смесей. На протяжении опробования в литейных цехах последовательности отечественных фабрик он разрешил уменьшить брак отливок, который связан с недоуплотнением либо переуплотнением смеси в формах, приобретаемых из песчано-глинистых, жидких самотвердеющих и графитовых смесей.
Многообразие проявлений разных литейных недостатков время от времени затрудняет их распознавание кроме того умелыми экспертами, а следовательно, тормозит принятие мер для их стремительного предотвращения. В этом случае для определения характера литейных пороков (небольшие поры, тёплые и холодные трещины и др.) рекомендуется использовать растровый электронный микроскоп.
Он отличается от простого электронного микроскопа тем, что разрешает приобретать увеличенное изображение различных материалов и поверхности отливок с громадной разрешающей свойством. Посредством растрового микроскопа возможно, к примеру, изучить структуру графита в чугуне.
Последние годы свойственны интенсивным оснащением литейных цехов, исследовательских организаций и лабораторий, изучающих литейные процессы, всевозможными устройствами и электронно-счётными автомобилями. В чугунолитейном производстве ЭВМ удачно оказывает помощь в выборе шихтовых материалов; координирует параметры работы вагранок.
В ряде фасонно-сталелитейных цехов ЭВМ всегда информируют литейщиков о температуре ванны, выполняют спектрографический анализ проб стали, осуществляют контроль процесс ее плавки в дуговых электрических печах. Наряду с этим ЭВМ выдает оператору инструкцию по корректировке режима плавки. Инструкция содержит указания о количестве нужных добавок компонентов, временя подачи кислорода и т. п. В один момент ЭВМ разбирает составы шлака и металла чтобы как следует обрисовать процессы дефосфорации и десульфурации (освобождения стали от серы и фосфора), регистрирует фактический расход кислорода и осуществляет по особой программе оптимизацию потребления энергии в ходе плавки.
Постоянное увеличение требований к качеству создаваемых отливок приводит к необходимости совершенствования методов и организации контроля в литейных цехах. Неизменно повышают собственную квалификацию работники ОТК, улучшается профилактический контроль методом внедрения и создания в производство более идеальной приспособлений и контрольной аппаратуры.
С той же целью на последовательности отечественных фирм сейчас были созданы отделы по качеству. Отделы решают громадной круг задач. Главными из них являются: организация совокупности опробований взятых отливок и сделанных из них подробностей, технико-экономическое обоснование производства отдельных наиболее значимых методов и отливок литья, планирование и организация работ по увеличению качества отливок и другое.
Помимо этого, в их функции входит устранение причин и рассмотрение рекламаций появления брака, создание и планирование контрольных и испытательных устройств, и распределение их по рабочим местам и включение в ходе контроля.