Отливки из углеродистой стали
Из углеродистой стали изготовляют около 2/3 металлических отливок. По технологическим (литейным) особенностям углеродистая сталь уступает чугуну; тем не меньше из нее возможно приобретать сложные отливки, разнообразные по конструкции, размерам, массе, толщине стенок для самых разных отраслей народного хозяйства. Литая углеродистая сталь по окончании термической обработки владеет высокими механическими особенностями.
В зависимости от содержания углерода сталь дробят на низкоуглеродистую (до 0,20% С), средне-углеродистую (от 0,20% до 0,45% С), высокоуглеродистую (более 0,45% С).
Углерод есть главным элементом, определяющим механические особенности углеродистых сталей. Повышение содержания углерода повышает прочность и снижает пластичность (рис. 110).
1акое изменение особенностей связано с тем, что по мере повышения концентрации углерода в структуре возрастает количество перли I а более прочной, но менее пластичной, чем феррит, составляющей.
Исходя из этого в конструкциях взяли громаднейшее распространение отливки из среднеуглеродистой стали (0,25-0,35% С). Как правило повышают содержание углерода более 0,45% с целью обеспечения особых особенностей отливок. Стали с высоким содержанием углерода относят время от времени к группе особых высокоуглеродистых сталей.
Низкое содержание углерода (менее 0,10-0,08%) требуется кроме этого при необходимости получения отливок со особыми особенностями.
По ГОСТу 977-65 в зависимости от содержания углерода (от 0,12% до 0,60%) сталь делится на 9 марок. Марки стали обозначают цифрами, соответствующими среднему содержанию углерода (указывается количество сотых долей процента), и буквой Л (литая). К примеру, сталь, содержащую 0,15% С, обозначают 15Л.
По качественным показателям, устанавливаемым в зависимости от назначения и предъявляемых требований, отливки разделяются на три группы:
I — простого назначения;
II — важного назначения;
III — очень важного назначения.
Углеродистая сталь всех марок содержит 0,20-0,42% Si, сталь 15Л, 20Л и 25Л — 0,30-0,75% Мп, а остальных марок — 0,40-0,90% Мп. Как кремний, так и марганец вводят в сталь в основном для раскисления (а марганец и для нейтрализации вредного действия серы), они значительного влияния на механические особенности не оказывают.
Содержание фосфора и серы в главной мартеновской и электростали допускается до 0,05%, в кислой стали до 0,06%. В бессемеровской стали большое содержание фосфора и серы может быть около 0,06 и 0,08% соответственно. Количество фосфора и серы в любых ситуациях нужно иметь минимальным.
Сера усиливает красноломкость стали, склонность ее к образованию тёплых трещин. Для отливок, испытывающих сильное торможение протекающей усадки (отливки сложной конфигурации), а кроме этого для толстостенных отливок, где благодаря ликвации вероятна местная концентрация серы, целесообразно ограничивать содержание ее до 0,03-0,035%.
Механические особенности металлических отливок, самая узкая стена которых имеет толщину более 100 мм, устанавливаются особенными техническими условиями.
Сталь для отливок II группы качества осуществляют контроль по относительному удлинению и пределу текучести, сталь для отливок III группы качества — по пределу текучести, ударной вязкости и относительному удлинению.
Особенности изготовления отливок из углеродистой стали
Металлические отливки изготовлять более сложно и трудоемко если сравнивать с изготовлением отливок из серого чугуна. Своеобразные условия сталелитейного производства обусловлены литейными и способами выплавки особенностями стали..
Жидкотекучесть углеродистой стали в среднем в два раза меньше жидкотекучести серых чугунов. Пределы дешёвого регулирования жидкотекучести более узки, и осуществить это регулирование более сложно. Низкая жидкотекучесть стали разъясняется довольно высокими значениями поверхностного натяжения и вязкости при температурах разливки.
Динамическая вязкость среднеуглеродистой стали (0,3% С) при 1555° С образовывает 0,026 из против 0,0210 из для серого чугуна при 1250° С, а поверхностное натяжение углеродистой стали превышает поверхностное натяжение серого чугуна более, чем в 1,3 раза.
Жидкотекучесть углеродистой стали в большой мере определяется содержанием в ней углерода. По мере увеличения содержания углерода практическая жидкотекучесть возрастает. Это позвано в первую очередь повышением относительного перегрева над температурой ликвидуса.
Расширение же промежутка кристаллизации с повышением содержания углерода оказывает менее сильное противоположное влияние.
кремний и Марганец (в пределах простого содержания их в углеродистых сталях) не оказывают заметного влияния на промежуток кристаллизации, другие свойства и вязкость стали, а исходя из этого их влияние на жидкотекучесть углеродистой стали несущественно. направляться подчернуть, что жидкотекучесть стали будет тем выше, чем полнее сталь раскислена. Сера, присутствуя в стали в виде тугоплавких, фактически нерастворимых мелкодисперсных включений MnS, A12S3, сокращает жидкотекучесть.
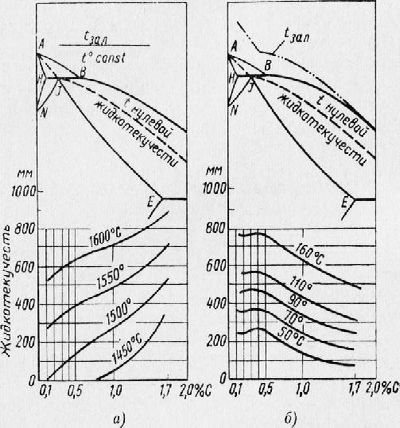
Рис. 1. Влияние углерода на жидкотекучесть стали: а — практическую (при постоянной температуре заливки); б — подлинную (при постоянном перегреве над температурой нулевой жидкотекучести)
Жидкотекучесть стали увеличивается при содержании более 0,05% Р. Как мы знаем, концентрацию фосфора и серы в углеродистой стали для получения пластичности и высокой прочности нужно иметь минимальной, а в допустимых пределах их практического влияния на жидкотекучесть не обнаруживается.
Отрицательное влияние оказывает на жидкотекучесть присутствие в стали тугоплавких неметаллических включений, попавших в нее в период выплавки, а особенно раскисления.
Первичная кристаллизация, обуславливая структуру отливки, во многом определяет ее свойства. Темперамент первичной кристаллизации определяется рядом факторов, связанных со особенностями сплава и с условиями производства отливки. Значительное влияние на первичную кристаллизацию углеродистых сталей оказывает концентрация углерода.
Громаднейшей склонностью к образованию широкой территории столбчатых кристаллов владеют стали, которые содержат -0,2% С. По мере повышения концентрации углерода (до 0,6-0,8% С) значительно уменьшается территория транскристаллизации, что разъясняется в основном влиянием углерода на промежуток кристаллизации сплава и его теплофизические особенности. Влияние углерода на ширину двухфазной территории при затвердевании отливки видно на рис. 2. Трансформацией перегрева стали, температуры заливаемого сплава, модифицированием, трансформацией скорости охлаждения возможно регулировать первичную структуру металлических отливок.
Рис. 2. Влияние углерода на ширину двухфазной территории затвердевания в металлических отливках, изготовленных в сырых песчано-глинистых формах (3, 4) и железных (1, 2): а — сталь с 0,10% С; б — сталь с 0,6% С
Рис. 3. Усадка углеродистой стали (0,35% С)
Литейная усадка тонкостенных отливок сложной конфигурации образовывает 1,25-1,5%, толстостенных — 2,0-2,3%. Литейная усадка кроме того в условиях торможения в большинстве случаев не не редкость меньше 10-1,25%, в противном случае образуются трещины.
Особенности литейных особенностей углеродистой стали приводят к необходимости разработки и применения своеобразных приемов разработки производства фасонных отливок.
Сталь выплавляют в агрегатах периодического действия, т.е. металл выдается через определенные промежутки времени. Емкость плавильных агрегатов для этих условий выбирают с учетом допустимых длительности разливки всей плавки и предельного количества открытий стопора ковша при разливке металла по формам. Число открытий стопора, изготовленного из шамотного припаса, согласно данным практики, образовывает в среднем ~ 120. В сталелитейных цехах самый распространены печи емкостью в 3; 5 и 10 т.
В фасонно-сталелитейных цехах громадной мощности, изготовляющих небольшие и средние отливки, при выборе емкости плавильного агрегата учитывают постоянную заливку на конвейере. В этих обстоятельствах устанавливают много печей малой ем- кости, что снабжает выдачу металла из различных печей через маленькие промежутки времени (не реже 2-3 раз в час).
Крановый стопорный ковш довольно часто есть промежуточным, из него сталь распределяется по раздаточным ковшам. Заливка движущихся на конвейере форм из кранового стопорного ковша неосуществима, поскольку тяжело добиться синхронизации перемещения конвейера и мостового крана.
Формы заливают сталью значительно чаще при 1600-1550 °С. В связи с этим к формовочным и стержневым смесям предъявляют более высокие требования по огнеупорности. Исходными материалами для смесей являются более чистые огнеупорные глины и кварцевые пески.
Глинистые пески, в большинстве случаев, в сталелитейных цехах не используют.
Заливка из стопорного ковша обусловливает большое воздействие струи металла на форму, исходя из этого их нужно изготовлять прочными, с большей степенью уплотнения смеси. Нехорошая если сравнивать с вторыми сплавами жидкотекучесть стали, меньший относительный перегрев требуют повышения размеров каналов литниковой совокупности, сокращения ее протяженности.
Дабы исключить механическое разрушение стенок литниковых каналов в больших формах, их изготавливают из огнеупорного сифонного припаса. Конструкции литниковых совокупностей определяются в основном массой и конфигурацией отливки, а кроме этого самоё рациональным местом подвода металла. Для отливок массой до 100 кг в основном используют литниковые совокупности с боковым подводом металла по разъему формы; для отливок массой 100-500 кг — с боковым и нижним подводом.
Формы тяжелых отливок (500 кг и выше) заливают, в большинстве случаев, через сифонные либо ярусные литниковые совокупности.
В зависимости от конфигурации отливки, ее ответственности и назначения металл подводится:
а) в толстые стены (лучше в прибыли) для направленного затвердевания, снабжающего получение плотной отливки (подвод металла к прибыли повышает коэффициент применения металла прибыли);
б) рассредоточение через много литников, дабы добиться одновременного равномерного охлаждения и, следовательно, меньших напряжений, что целесообразно при изготовлении тонкостенных протяженных отливок;
в) к узким частям, дабы по возможности выравнять скорости охлаждения отливок, склонных к образованию трещин. Питание массивных частей в этом случае целесообразно осуществлять из доходов, трудящихся под избыточным газовым либо воздушным давлением.
Усадка стали в жидком состоянии и в период кристаллизации, если не приять особых мер, приводит к образованию усадочных пористости и раковин. Получение плотных отливок обеспечивается созданием и установкой прибылей направленного, последовательного затвердевания. Без доходов возможно изготовлять из стали лишь малоответственные, тонкостенные отливки.
Типы доходов, способы определения их размеров, выбор места установки, а кроме этого методы регулирования охлаждения отливки рассмотрены в прошлых разделах.
Усадка стали в жёстком состоянии может привести к образованию тёплых и холодных трещин, коробление отливок, высокие изменение и внутренние напряжения линейных размеров. Тёплые трещины в отливках из углеродистой стали являются следствием сильного торможения (в основном, со стороны формы) доперлитной усадки. Трещины находятся в самые слабых местах, какими являются разогретые участки.
Повышение содержания углерода снижает линейную усадку (особенно доперлитную), что сокращает опасность образования тёплых трещин. Иначе, низкоуглеродистые стали стремительнее увеличивают прочность при охлаждении. Отливки, испытывающие громадное механическое торможение усадки, рекомендуется изготовлять из углеродистой стали с повышенным либо низким содержанием углерода.
Разностенные отливки со большим термическим торможением усадки целесообразнее изготовлять из низкоуглеродистой стали. Отрицательное влияние на трещиноустойчивость оказывает неметаллические включения и сера (особенно легкоплавкие). Отмечается громадная склонность к образованию трещин кислых сталей.
Главные мероприятия по предотвращению тёплых трещин заключаются в улучшении разработки изготовления форм, обеспечении хорошей их податливости, выборе конструкции отливки, литниковой совокупности, в рациональном режиме охлаждения и заливки.
Не считая уменьшения упрочнений, затрудняющих усадку, образование тёплых трещин дают предупреждение упрочнением не сильный мест отливки установкой холодильников и усадочными рёбрами. Усадочные ребра принимают часть усилий, тем самым «разгружая» не сильный (горячее) место отливки. Холодильники (наружные либо внутренние) содействуют более стремительному охлаждению и, следовательно, упрочнению страшного участка отливки.
В области температур ниже 650 °С под действием внутренних напряжений либо внешних нагрузок в углеродистой стали появляются упругие деформации (в основном).
Громаднейшей склонностью к образованию холодных трещин владеют отливки из высокоуглеродистых сталей. Увеличение содержания углерода приводит к увеличению среднего коэффициента термического сжатия (14,5- 10“е для стали с 0,14% С и 16,1-Ю“6 для стали с 0,45% С). Высокоуглеродистые стали менее теплопроводны, чем низкоуглеродистые, что вызывает громадной перепад температур по сечению отливки и между отдельными ее частями.
1аким образом, за счет повышения термических напряжений с увеличением содержания углерода возрастает опасность образования холодных трещин.