Паркетные полы
Громадное использование в современном постройке имеют паркетные полы. Настилка паркета, что есть одним из основных элементов архитектурно-художественного оформления помещений, относится к отделочным работам. Художественная обработка пола как части интерьера имеет собственную давешнюю историю.
Из всех материалов, употребляемых для настилки полов, древесина занимала одно из первых мест. До XVI в. пол настилали из досок, пригнанных хорошо друг к другу, в XVI в. в связи с возникновением нового инструмента существенно усовершенствуются методы обработки дерева. Из древесины жёстких пород — дуба, бука, граба — стали выделывать дощечки однообразной величины и укладывать их на особую базу, придавая тот либо другой несложный рисунок.
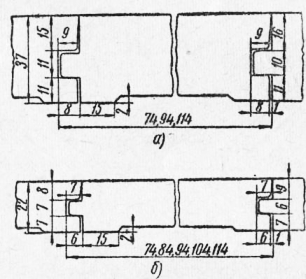
Рис. 1. Доски для настила чистого пола:
а — однослойного, б — двухслойного
С XVIII в. паркетные полы стали делать сложного рисунка. Для украшения таких паркетных полов использовались разные породы древесины: дуб, бук, граб, орех, сосна, береза, груша, мореный дуб, ясень, клен, красное дерево, палисандр, лимонное дерево, атласное, тисс, туя, самшит, амарант и эбеновое дерево.
Рис. 2. Фрагменты паркета
Самым распространенным видом рисунка паркета был сетчатый орнамент из геометрических форм.
Громадным разнообразием отличаются паркеты Останкинского дворца в Москве. В каждом комнате и зале соответственно их оформлению и назначению дано то либо подбор древесины и иное решение рисунка. Паркет концертного зала этого дворца по сложности собственной композиции, по разнообразию геометрических форм представляет собой редкий пример в практике художественной обработки пола.
Паркетные полы бывают трех видов: из штучного, паркетных досок и наборного паркета.
Штучный паркет
Заготовка паркета. Для настилки полов по древесному основанию на мастике используют паркетные планки-клепки с пазом и гребнем, которыми эти планки соединяются между собой. Данный штучный паркет, предусмотренный ГОСТ 862—60.
При изготовлении паркета для полов в жилищном постройке в большинстве случаев используется древесина жёстких пород — дуба, ясеня, граба, бука. В соответствии с ГОСТ 862—60 для того чтобы возможно использовать и древесину березы, сосны, лиственницы. Но березовый паркет имеет серьёзной недочёт — коробится, что ведет к понижению срока и качества работы полов.
Рис. 3. Штучный паркет
Испытания обработки березовой клепки в петролатуме—маслянистой жидкости, приобретаемой при переработке нефти, — продемонстрировали очень хорошие результаты, поскольку береза получает новые весьма полезные особенности: быстро изменяется ее влагоем-кость и увеличивается сопротивление истиранию. Для данной цели обрабатывать древесину березы нужно в два приема. Сначала пиломатериал, предназначенный для того чтобы, сушится в петролатуме.
После этого паркетная дощечка пропитывается петролатумом еще раз, поскольку в ходе изготовления паркета часть пропитанного слоя снимается. Производство паркета из березовой древесины, пропитанной в петролатуме, не Уступает по качеству дубовой и одновременно с этим практически вдвое Дешевле. Наровне с этим наличие некоего количества петро-латума в поверхностных слоях древесины разрешает поддерживать хороший вид и чистоту пола, протирая его сухой щеткой без применения мастики.
Для изготовления паркета используют паркетно-строгальный станок ПАРК-1, что рекомендован для четырехстороннего строгания паркетных дощечек. Станок имеет две горизонтальные и две вертикальные головки. Подача материала производится цепным конвейером. Ножевые головки насажены конкретно на валы особых электродвигателей, установленных на мобильных суппортах. Закрыты головки кожухами, в один момент являющимися приемниками эксгаустерной сети.
Устанавливается цепной конвейер на нужную высоту вручную. Имеет станок четыре скорости подачи.
Паркетные дощечки в большинстве случаев обрабатываются на станках ПАРК-1 металлическим инструментом. Инструмент складывается из двух шестизубых дисковой пилы и фрез, расположенной между ними. Каждые 8 час. нужно было создавать наладку станка и переточку инструмента. А на наладку станка ПАРК-1 время от времени тратилось до 25% рабочего времени. Низкой стойкостью владели и вставные ножи горизонтальных фрезерных головок, которыми обрабатывалась плоскость паркетной дощечки.
На Ростовском-на-Дону домостроительном комбинате металлическая фреза была заменена паркетной фрезой новой конструкции со сменными вставными ножами, армированными жёстким сплавом марки IBK15. Представляет собой фреза металлической диск диаметром 185 мм, на котором расположены сменные ножи, формирующие боковые плоскости паркетной дощечки, и сменные ножи-пилочки, формирующие шпунт. Ножи крепятся клиньями, каковые затягиваются винтами, а ножи-пилочки крепятся болтами № 8 посредством упругих шайб.
Вставные ножи горизонтальных фрезерных головок кроме этого заменены на твердосплавные.
Рис. 4. Паркетно-строгальный станок ПАРК-1
Опробование продемонстрировало, что стойкость этих фрез в 100 раз выше, чем металлических.
Для оторцовки с двух сторон паркетных дощечек с одновременной выборкой в них пазов используется паркетный концеравнитель ПАРК-2.
Материал загружают в особый бункер, откуда он поступает на цепи конвейера и проходит мимо двух торцующих выпивал, насаженных на валы электродвигателей, и после этого мимо горизонтально расположенных выпивал, выбирающих пазы. Станок имеет четыре скорости подачи.
При изготовлении паркетных дощечек главным видом брака есть непрострожка базисной (боковых) кромок и лицевой поверхности, вырывы на кромках и лицевой поверхности, и неточности линейных размеров. Брак лицевой плоскости и кромок разъясняется тем, что дощечки, поступающие в обработку, имеют большие отклонения по толщине, Длине и ширине, и громадное коробление.
На данный момент в большинстве случаев недостатки обработки определяются контролерами-сортировщиками визуально, а отклонения линейных размеров микрометром и штангенциркулем. Лабораторией средств автоматизации укрНИИМОД создано автоматическое контрольно-сортировочное устройство АКУ-38. Предназначено устройство ^КУ-38 для контроля линейных качества и размеров обработки паркетных дощечек.
Устройство должно быть установлено На автоматической линии для изготовления паркетных дощечек по окончании станка ПАРК-1 (ПАРК-5). При прохождении бракованной подробности импульс о наличии брака подается через блок уси-Ления на сортировочное устройство и на световое табло. Сортировочное устройство удаляет бракованные подробности из потока. Годная подробность поступает на перекладчик для предстоящей обработки либо в бункер готовых подробностей.
Для отвода бракованных подробностей имеется особый лоток из листовой стали толщиной 1 мм. Это автоматическое контрольно-сортировочное устройство АКУ-38 в один момент помогает и для передачи паркетных дощечек со станка ПАРК.-1 в питатель станка ПАРК-2.
Рис. 5. Неспециализированный вид автоматического контрольного устройства АКУ-38:
1 — контрольный стол, 2 — пульт управления, 3 — электромагнит, 4 — шток, 5 — конические шестерни, 6 — блок-контакт, 7 — стойки, 8 — ходовые винты, 9, 12 — датчики, 10 — ролики, 11 — балка, 13, 14 — направляющие линейки, 15 — прижимные ролики, 16, 17 — ручки, 18 — контактный стержень
Станок, продемонстрированный на рис. 6, торцует и перерезает паркетную клепку по любому размеру. Станок имеет поворотную станину, исходя из этого на нем возможно срезать клепку на ус.
Группой работников стройуправления № 47 треста «Мосотдел-строй» № 4 создан особый станок для обрезки паркетной дощечки под прямым и вторым заданным углом. На ставке в один момент обрабатываются две дощечки.
Станок имеет стол, электродвигатель и укрепленные на валу фрезу и дисковую пилу. Механизм станка смонтирован на двух площадках из угловой стали, находящихся одна над второй и приваренных к столу.
Станок позволяет механизировать ручные работы, создаваемые при подгонке паркетных дощечек. Производительность станка при обрезке торцов дощечек образовывает 100 резов в 60 секунд, а при выборке пазов — 25 пог. м в час.
Для обработки в размер паркетной дощечки и для выборки пазов на продольных боковых стенках дощечек либо брусков используют новейшие станки ПАРК-5 и ПАРК-6.
Четырехсторонний строгальный станок,для паркета ПАРК-5 (рис. 388) имеет чугунную литую станину, на которой смонтирован стол, суппорты нижней и верхней ножевых головок, привод и механизм подачи, суппорт вертикальных головок и редуктор привода подачи. Привод подачи встроенный.
Электрошкаф, в котором имеется преобразователь частоты и пусковая аппаратура, устанавливают раздельно от станка. Стружка удаляется отсосом с патрубками, присоединенными к цеховой экс-гаустерной установке. Конвейерная цепь механизма подачи приводится в перемещение через двухскоростной редуктор от электродвигателя.
Рис. 6. Станок для оторцовки и перерезания паркетной клепки
Рис. 7. Четырехсторонний строгальный станок для паркета ПАРК-5
Рис. 8. Подающее устройство П1-ПАРК
Для автоматической подачи заготовок в станок имеется подающее устройство П1-ПАРК (рис. 389). Оно складывается из литой чугунной станины, на которой смонтированы магазин, питатель, основной приводной вал, подвижная каретка, зубчатый кулачок и привод.
Для привода подающего устройства П1-ПАРК на выходном валу шестеренчатого редуктора имеется звездочка.
Пакет заготовок числом 20—25 шт. загружают в магазин подающего устройства. Заготовки подаются для обработки при вращении зубчатого кулачка и перемещении приводной цепи.
По окончании выхода нижней дощечки пакет с заготовками опускается и последующая заготовка попадает в промежуток между приводной цепью и зубчатым кулачком. Для регулировки обрабатываемых заготовок по ширине зубчатый кулачок перемещается в поперечном направлении. Подающие упоры конвейерной цепи станка захватывают заготовку и протаскивают ее через режущие головки. В местах резания заготовка поджимается особыми прижимами.
После этого обработанная паркетная дощечка подается со станка на транспортер либо в особую тару. При применении подающего устройства производительность станка увеличивается на 25—30%.
Производительность станка ПАРК-5 выше производительности станка ПАРК-1 в 1,5 раза.
Двухсторонний паркетный концеравнитель ПАРК-6 рекомендован для оторцовки паркетных дощечек с двух сторон с одновременной выборкой гребня и паза. Станок имеет литую чугунную станину, где смонтированы подвижная и неподвижная бабки с суппортами, конвейер с загрузочным магазином, редуктор и механизм прижима.
Обе бабки станка имеют направляющие типа ласточкина хвоста для крепления фрезерного и пильных суппортов, а подвижная бабка — механизированное перемещение маховик и колонки для ручной доводки при наладке станка на длину заготовки. Для удаления отходов от станка в бабках и станине имеются особые лотки.
Рис. 9. Двухсторонний паркетный концеравнитель ПАРК-6
Правым пильным суппортом производится подрезка верхней части паркетной дощечки, а горизонтальными — торцовка ее с двух сторон. На правом шпинделе установлена вторая дополнительная выпивала для подрезки нижней части гребня и дощечки. Фрезерный суппорт создаёт выборку гребня и паза.
Наладку суппортов делают посредством регулировочных винтов.
Подающие цепи конвейера, что помогает для перемещения и базирования изделия, имеют особые упоры. Осуществляется переключение и подача скорости электродвигателя через редуктор одной рукояткой. Механизм прижима складывается из особенной части, в которой находятся подпружиненные звенья.
Шкаф с электроаппаратурой и преобразователь частоты устанавливают раздельно от станка.
Для безопасности работы все режущие инстументы станка ограждены. Эти ограждения являются одновременно и пыле-отсасывающими устройствами; присоединяются они к цеховой эксгаустерной совокупности.
При наличии пяти режущих головок — трех пильных и двух фрезерных — на станке возможно обрабатывать паркет всех размеров.
Станок ПАРК-6 требует для установки меньшей производственной площади, чем станок ПАРК-2, и снабжает громадную производительность труда.
Влажность древесины, из которой изготовляют паркетную клепку, должна быть не более 9%. Влажность паркета определяют в лабораториях электровлагомером. Паркет влажностью более 9% нельзя применять для укладки.
Перевозить паркет следует в крытых автомашинах и вагонах. Необходимо особенно аккуратно обращаться с буковым паркетом, поскольку он увлажняется посильнее дубового и. скоро коробится.
ГОСТ 862—60 установлены по длине пять размеров штучного паркета — от 150 до 400 мм и по ширине пять размеров — от 30 до 60 мм, с градацией в 5 мм.
Паркет сортируют и упаковывают в пачки на заводе. Пачки укладывают в штабеля и прикрепляют к ним ярлыки с указанием количества и размера клепок. Древесина паркета не Должна иметь пороков: сучков, трещин, синевы и др.
На стройку паркет доставляют в пачках. В тех случаях, в то время, когда его завозят россыпью, паркет сортируют по длине и ширине на особом верстаке. Поступающий на строительную площадку паркет время от времени требует дополнительной обработки (прифуговки) кромок.
Станок для прифуговки клепки изображен на рис. 391. Станок имеет легкий железный каркас из уголков.
На каркасе смонтированы фуговальные (верхний и нижний) ножевые валы, закрытые кожухом, предназначенные для двухсторонней прифуговки кромок паркета; нож для зарезки паркетных реек; наждачное точило для заточки фуговальных ручного инструмента и ножей, используемого при настилке паркетных полов. Вместо точила на станке возможно установить дисковую электропилу и создавать приторцовку паркетной клепки. Механизмы приводятся в перемещение электродвигателем, станок перемещается посредством ручек, шарнирно укрепленных на раме.
Для прифуговки паркетную клепку устанавливают на ребро в стусло и зажимают рукояткой. После этого каретку с установленной в ней клепкой передвигают в направлении фуговальных ножей, где и производится двухсторонняя, прифуговка кромок.
Рис. 10. Комбинированный станок для прифуговки клепкн и нарезки паркетных реек:
1 — каретка, 2 — электродвигатель, 3 — рама, 4 — нож, 5 — кожух, 6 — стусло, 7 — точило, 8 — рукоятка, 9 — ручки
Следующей по окончании фугования операцией подготовки паркета к укладке есть торцовка. Дабы выяснить, необходимо ли подрезать торцовые кромки, берут из нескольких пачек на выбор по 8—10 паркетных планок и контролируют их. В случае если выявляют недостатки, то всю партию паркета сортируют, откладывая клепки, подлежащие торцовке, в отдельный штабель.
Торцовку паркетной клепки делают на верстаке дисковой электропилой. Весьма удобен для этого несложный переносный станок, предложенный слесарем Шапроновым. Данный станок разрешает не только создавать торцовку, но и обрезать клепку на ус под любым углом.
Для обрезки паркета (по длине и под углом), для фугования его торцов и исполнения последовательности вторых операций конкретно на рабочем месте паркетчика используется небольшой станок паркетчика. Станок изготовлен на ремонтно-механическом заводе треста «Таллинстрой». Механизм его снабжен набором сменных рабочих органов— дисковой пилой, рубанком и фрезой.
Производительность станка 500 операций в час; окружная скорость в м/сек: пилы 37,5, рубанка и фрезы.
Рис. 11. Станок для торцовки и обрезки на ус клепки
Рис. 12. Небольшой станок паркетчика:
1 — опорная плита, 2 — дисковая выпивала
Переносный станок паркетчика ОЛ-124 рекомендован для обрезки паркета, выборки в нем пазов и фугования боковых кромок. Производительность станка 500 шт. паркета в час, число оборотов рабочего вала в 60 секунд 3450, диаметр пилы — 200 мм, фрезы—117 мм, ножевого барабана—102 мм-, мощность электродвигателя— 0,6 кет, напряжение 200 в, вес — 26 кг.
Настилка паркета. Паркетные полы гигиеничны, легко ремонтируются, владеют малой незначительной звукопроницаемостью и теплопроводностью. Одновременно с этим устройство паркетных полов есть очень трудоемкой операцией, исходя из этого громадное значение имеет верная организация работы по настилке паркета и наличие приспособлений, улучшающих уровень качества паркетных работ.
Устройство паркетных полов складывается из подготовки поверхности перекрытия, отделки и настилки паркета.
Паркет настилают по доскам древесного тёмного пола, по цементной либо асфальтовой стяжке, покрывающей конкретно бетонное междуэтажное перекрытие либо уложенной на звукоизоляционный слой из асбестоцементных, торфяных, шлаковатных либо древесно-волокнистых плит либо по шлакобетонному и ячеистому слою бетона.
Стяжки из асфальта используют в тех случаях, в то время, когда паркетные работы нужно выполнить в очень маленькие сроки либо в то время, когда паркет настилают зимний период при низкой температуре воздуха, при которой нельзя укладывать стяжки из бетона либо раствора. В этом случае раствор обязан содержать битума не меньше 10% от собственного неспециализированного веса и иметь температуру не меньше 150° С.
Лучшее уровень качества асфальта обеспечивается приготовлением его на фабриках.
При малых количествах паркетных работ асфальтовую смесь возможно приготовлять на стройке в асфальто-варочных котлах емкостью 0,6—0,75 м3. Асфальт, так же как раствор и бетон, укладывают в полосы. По окончании заполнения асфальтом нечетных полос снимают маячные рейки и заполняют четные полосы. За укладкой асфальт разравнивают сперва лопатой, а после этого правйлом, не вдавливая излишков, а лишь срезая и сдвигая их по ходу укладки вперед.
Не допускается охлаждение асфальта ниже 120 °С, исходя из этого асфальт необходимо скоро уплотнять ручным катком, дабы он опоздал остыть.
По древесному основанию паркет укладывают на тёмный пол, настланный из неостроганных сосновых либо еловых досок толщиной не меньше 35 мм и шириной не более 120 мм, влажностью не выше 18%. Доски укладывают по лагам с маленьким (до 5 мм) зазором вразбежку. Пол должен быть твёрдым, иметь горизонтальную поверхность.
Уровень паркетного пола во всей квартире определяют уровнем площадки лестничной клетки. Так как входная дверь раскрывается в большинстве случаев вовнутрь, пол передней делают на 15—20 мм ниже лестничной площадки, а остальные помещения подгоняют под уровень передней.
Для проветривания пространства под паркетным полом предусматривают вентиляционные устройства (решетки, дырчатые плинтусы и др.).
Дабы на протяжении ходьбы паркетный пол не скрипел, на основание настилают два слоя бумаги либо картон. Настилку полов создают поточно-расчлененным способом — звеном. В звено входят мастер-паркетчик (звеньевой), паркетчик 4-го разряда и двое подсобных рабочих.
Обязанности между рабочими распределены соответственно их квалификации.
Перед настилкой паркета мастер контролирует горизонтальность чистого пола и разбивает площадь пола для определения
его середины — оси помещения. Затем по противоположным сторонам помещения забивают гвозди, между которыми натягивают шнур, являющийся осью маячной елки. Эту работу делает мастер и первый подсобный рабочий.
Заготовленную паркетную клепку второй подсобный рабочий разносит и раскладывает на рабочем месте.
Паркет обязан пребывать под рукой паркетчика. Для этого раскладывают пачки клепки по направлению настилаемого последовательности по 4—6 шт. в каждой пачке наклонно, лицевой плоскостью в сторону паркетчика. Расстояние между пачками должно быть таким, дабы паркетчик, протянув руку, имел возможность дотянуться их, а количество выставленного паркета должно обеспечить настилку многих.
В этом случае паркетчик одним перемещением подвигает из пачки к себе клепку и укладывает на место, что повышает производительность труда и снабжает своевременный контроль за качеством.
Рис. 13. Настилка маячной рейки
В ходе укладки паркета паркетчик 4-го разряда забивает гвозди в торце уложенных клепок; один подсобный рабочий сортирует рейки, а второй подсобный рабочий продолжает подносить паркетную клепку к рабочему месту паркетчиков. Свободное время они применяют для настилки фризовых последовательностей. Подготовительную работу — сортировку клепки по оттенкам и размерам — создают в отдельном помещении, неподалеку от места работы.
Рис. 14. Приемы раскладки паркета;
а – вставными рейками вверх, б – вставными рейками вниз
Рис. 15. Неспециализированный вид рабочего места паркетчика
После этого мастер укладывает паркетную клепку гребнем в паз хорошо одну к второй и подшивает гвоздями. Сейчас паркетчик стоит на правом колене, дабы дать свободу перемещений правой руке,; левая нога является опорой корпуса. За ним подсобный рабочий добивает гвоздь в паз каждой уложенной клеткй, держа в левой руке добойник, а в правой молоток.
Для предохранения кромки паркета от повреждения при забивке гвоздей используют Г-образный шаблон из листовой стали с вырезом в средней части.
Рис. 16. Работа подсобного рабочего и мастера (а); забивка гвоздя в паз посредством добойника (б) и посредством шаблона (е)
Для пришивки паркета к тёмному полу гвозди загоняют в паз наискось, но так как молотком возможно забить гвоздь лишь До паза, то дальше его добивают добойником Вугина.
В свободное время подсобный рабочий набирает предфризовые углы паркетных последовательностей и при настилке пола с фризом обрезает дисковой пилой финиши клепки, примыкающей к фризу. Дабы дисковые электроцилы были пригодны для обрезки настланных последовательностей паркета, П. К- Точилкин снабдил их опорной площадкой громадного размера и двумя дополнительными рукоятками. Для передвижения пилы по краю паркетной настилки (параллельно стенке) укладывают линейку.
По окончании настилки рядового паркета и обрезки крайних последовательностей укладывают фризовые клепки. Укладку фриза начинают с угла и ведут так, дабы стенки пребывала слева от паркетчика. В свободное от заготовки и подноски клепки время подсобные рабочие настилают фризовые последовательности.
Рис. 17. Приемы работы молотком конструкции Вугина:
а — повертывание молотка, б — положение молотка при забивке гвоздей
Рис. 18. Работа добойником при забивке гвоздя в паз, при посадке паркета на приёмы и шипы укладки фриза
При настилке паркета направляться экономно расходовать клепку, укладывая ее с минимальным числом обрезков, а неизбежные обрезки применять для заполнения предфризовых уголков. Настилка «в елку» возможно выполнена и без фриза. В небольших помещениях и узких коридорах паркет укладывают прямым рисунком либо «в ковер».
Главной причиной образования отходов при настилке паркета есть необходимость опиливания примыкающих к фризу последовательностей клепки. Одним из нужных условий для настилки пола без отходов есть четность числа полных последовательностей клепок по ширине помещения (полагая два последовательности из половинок клепок за один полный последовательность). Это возможно обеспечено лишь предварительным подбором клепок по длине.
Основанием для укладки паркета по асфальту помогает цементная либо бетонная плита. Поверхность основания не должна иметь впадин, бугров и раковин.
К цементной либо асфальтовой стяжке паркет крепят мастикой. Мастика является смесьюбитума с волокнистым либо волокнисто-пылевидным наполнителем, что придает мастике упругость, мешающую отслоению паркета. Волокнистым наполнителем есть асбест, пылевидными — тальк, трепел, доломитовая либо древесная мука, измельченные опилки, торфяная крошка, гипс, шлаковая пыль, молотый известняк.
Выпускается мастика фабриками в виде плит весом 30—32 кг.
Доставленные на стройку плиты мастики разогревают в электрокотелках КРМ-2, каковые складываются из двух котелков емкостью по 50 л с электрическим обогревом стенок и днища. Мастика перемешивается поочередно в каждом котелке мешалкой-гребенкой, действующей от электродвигателя. Котелки подвешены к тележке так, что их возможно наклонять, наливая мастику в ведро.
Сейчас стройки снабжают тёплой мастикой, которую транспортируют в утепленной автоцистерне с керосиновыми форсунками, действующими на ходу цистерны. Доставленная на стройку мастика должна иметь температуру 170—180 °С, а при розливе под паркет — не ниже 150 °С, поскольку пониженная температура мастики сокращает прочность приклейки и затрудняет укладку паркета.
Набор оборудования для паркетных работ изображен на рис. 400. Состоит он из железного бака емкостью 40 л, снабженного шарнирно укрепленной крышкой.
Бак устанавливают на электронагреватель, складывающийся из железного коробки, в котором размещены две электроспирали, смонтированные на подставке. Входящий в набор электротермос емкостью 8 л складывается из засунутых один в второй двух железных бачков, между которыми находится термоизоляционная асбестовая прокладка.
На дне наружного бачка установлена электрическая плитка, а на крышке — асбестовая прокладка. На ручке электротермоса смонтированы штепсельная розетка и кнопочный выключатель для подключения термоса к электросети. Из бака разо-
Рис. 19. Набор оборудования для паркетных работ:
1 — железный бак, 2 — электронагреватель, 3 — ведрд с крыщкой, 4 — электро-термос, 5 — гребенка, 6 — проволочные носилки, 7 — кельма
гретый тёплый битум разносят по рабочим местам в ведрах о крышками 3. На рабочем месте битум переливают в электротермос 4, а из него разливают битум под настилаемый паркет. В случае если в ходе работы битум остыл, его подогревают в электротермосе.
Рационализаторы Управления строительства г. Тюмени для нанесения битума на вертикальные поверхности внесли предложение особый ковш. Корпус ковша изготовляется из кровельной стали, к бокам прикрепляют древесные державки, а к корпусу— хлопчатобумажную ткань — полотенце. Сейчас возможно наносить тёплую битумную мастику на поверхность ровным слоем, без разбрызгивания.
Для разогрева битума удачно используется действенная установкана основе агрегата для обогрева и сушки строения. Состоит установка из компрессора, тепловой трубы с форсункой, бака для обычного котла и горючего емкостью 0,7 м3 для разогрева битума. Вставляется тепловая труба в топку котла. ДТ из бака подается самотеком к форсунке, где распыляется и сгорает в тепловой трубе. Дымовые газы омывают дне котла и разогревают битум.
Пламя же конкретно не соприкасается со стенками котла, что предохраняет их от прогорания. Происходит разогрев битума в 15— 25 мин., и расходуется около 6 л ДТ.
Для разравнивания мастики на основании используются гребенки шириной 120 и 400 мм. Гребенка шириной 120 мм предназначена для разравнивания мастики в отдельных малодоступных местах, к примеру под радиатора-,ми. Полотна гребенок изготовляются • из листовой стали марбк У7, У8.
На рабочей грани полотна гребенки нарезают зубцы высотой 3 мм (вершина зубца шириной 1,5 мм, основание 7,5мм). Разравниваемая гребенкой мастика распределяется на основании ровным слоем, толщина которого равна половине высоты треугольного зубца гребенки, т. е. не более 1,5 мм.
Перед укладкой паркета поверхность стяжки должна быть проверена двухметровой рейкой и для хорошего сцепления с мастикой шепетильно прогрунтована битумом, растворенным в зеленом масле, лакойле либо в каком-либо втором растворителе. К настилке паркета возможно приступать лишь тогда, в то время, когда из грунтовки улетучится растворитель и она не будет липкой.
До настилки паркета нужно помещение очистить от мусора и подмести. Для переноски паркетной клепки пользуются проволочными носилками.
Работу рекомендуется организовать так, дабы на одной захватке производилась настилка паркета, а на другой шла сейчас подготовка площади под настилку.
Рис. 20. Схема установки:
1 — котел из листовой стали толщиной 6—8 мм, 2 — бак для битума, 3 — тепловая труба диаметром 120 мм со стенками толщиной 5—6 мм, 4 — форсунка от двигателя трактора С-80, 5 — шланг диаметром 9 мм для подачи сжато-го воздуха, 6 — бронзовая трубка диаметром 6 мм для подачи горючего, 7 — компрессор производительностью 0,5 м3/мин, 8 — бак для жидкого горючего емкостью 30 л
При настилке маячной елки (первых двух последовательностей) паркет выставляют парами, против укладываемых последовательностей. При настилке последующих последовательностей (рядового настила) паркет раскладывают в один последовательность, наискось от направления последовательности.
Паркет «в елку» с фризом настилает паркетчик с подсобным рабочим. Работу начинают с линейки и укладки фриза на протяжении стенку, перпендикулярных последовательностям «елки». Чтобы получить верную линию фриза, нужно натянуть шнур на расстоянии от стенки, равном длине фризовой клепки и ширине линейки.
Так как вбить гвоздь в цементную либо асфальтовую стяжку запрещено, то шнур закрепляют за гвоздь, вбитый в маячную клепку, либо наматывают на нее, а клепку удерживают на месте, укладывая на нее 2—3 кирпича.
Фризовый последовательность и линейку настилают в один момент, но фриз до углов не доводят. По окончании того как фризы на протяжении всех стен настланы, закрывают углы. Дабы вся поверхность настила пребывала на одном уровне, паркетчик обязан контролировать расстояние от настила до нанесенного на стену репера. По окончании настила фризов у первых двух стен наверстывают около линейки насухо, ближе к одному из углов, 3—6 шт. паркета крайнего последовательности настила, распиленных пополам.
После этого укладывают к ним паркет для маячной елки, определяя этим ее положение, обозначаемое натянутым шнуром.
Маячную елку настилают около стенки, противоположной входной двери, а не по оси перемещения, дабы подсобные рабочие не ходили по свеженастланному паркету.
По окончании укладки маячной елки подсобный рабочий готовит паркет и доставляет тёплую мастику. Доставленную мастику в ведре либо электротермосе ставят у рабочего места и черпаком разливают ее слоем в 2—3 мм на участок, опережающий паркетчика на 3—4 клепки, с тем дабы мастика не успевала остыть.
Паркетные клепки при укладке сплачивают ударами молотка со скошенным обушком либо через древесную прокладку, с тем дабы не повредить верхнюю кромку клепки.
Рис. 21. Разбивка для настилки фризового последовательности:
1 — шнур, 2 — маячная дощечка, 3 — кирпич
По окончании рядового настила укладывают последовательности, примыкающие к фризам: один, складывающийся из половинок, второй — из намерено нарезанных косяков.
Последний к фризу последовательность елки прибивают гвоздями лишь в продольных пазах; в торцы гвозди не забивают, дабы при обрезке не повредить пилы. Линию обреза отбивают шнуром, натянутым на расстоянии от стенки, равном ширине фриза с жилкой и линейкой плюс зазор в 15—20 мм. Обрезку клепок создают электропилой, смотря за тем, дабы не пропилить тёмный пол.
Обрезанные части клепок переносят и укладывают в соответствующем порядке в конечный последовательность с противоположной стороны помещения.
Паркет без фриза настилают следующим образом. Около одного из углов помещения укладывают два-три косяка, к ним прикладывают насухо пара штук клепки для определения положения маячной елки. Замерив расстояние от стенки до маячной елки, переносят его на противоположную сторону помещения.
Рис. 22. Обрезка электропилой финишей крайнего последовательности паркета
Рис. 23. Разбивка для настилки на мастике без фриза:
1 — косяки, 2 — наверстка насухо паркета, обозначающего маячную елку, 3 — расстояние от стенки до маячной елки, 4 — маячные клепки, 5 — кирпичи, 6 — шнур
Уровень пола определяют по реперу, отмеченному на стене. По этому уровню укладывают две маячные клепки, удерживая их на месте кирпичами. Затем в маячные клепки забивают гвозди и натягивают шнур.
Паркет укладывают равно как и при настилке пола с фризом. Схема раскладки паркета на рабочем месте паркетчика приведена на рис. 24.
Используемая при наклейке паркета тёплая битумная мастика не удовлетворяет требованиям современного индустриального строительства. Паркет, уложенный на таковой мастике, имеет большое количество недочётов (битум довольно часто на протяжении эксплуатации выступает из щелей между паркетными клепками, неосуществима укладка паркета на жёсткую рейку, и имеются случаи ожогов и травм). Сейчас для наклейки паркета используют холодную мастику.
Это позволяет удешевить работы по отделке, существенно расширить производительность труда и обеспечить требуемое уровень качества полов.
Настилка паркета на холодной мастике производится конкретно по стяжке из цементно-песчаного раствора либо по жёстким древесно-волокнистым плитам, наклеенным на стяжку из асфальтобетона. Холодную мастику наносят на подготовленное основание слоем толщиной 1 мм и укладывают паркет с таким расчетом, дабы отличие в уровне лицевых плоскостей паркета до острожки не превышала 1 мм. Острожку пола создают не ранее чем через 5 дней по окончании укладки паркета.
Мастику разливают на основание на всей протяженности помещения и древесным движком разравнивают слоем толщиной 1 —1,5 мм.
Паркетчик берет из ближайшей пачки паркет и укладывает его на место, после этого он сглаживает и прижимает клепку к ранее уложенной так, дабы мастика не выходила через швы. Ребром укладываемой клепки паркетчик удаляет излишки мастики.
Холодная мастика густеет в течение 3—4 час., а через 12 час. клепка всецело приклеивается к основанию. Холодные мастики используют двух видов: одним видом являются битумные мастики, разжиженные при помощи летучих растворителей (бензина, керосина, толуола, масел и бензола); вторым видом — водные битумные эмульсии с разными заполнителями. Эти мастики владеют достаточной клеящей свойством и снабжают надежное сцепление паркетной клепки либо линолеума с основанием.
На битумной эмульсионной базе делают два состава мастики: известково-битумную и глино-битумную. Известково-битумная мастика складывается из 1 весовой части битума, 0,8 части известкового теста и 0,6 части воды. Уровень качества известково-битум-ной мастики высокое.
Но водоразбавимые глино-битумные мастики для наклейки паркета владеют более большой прочностью, влагостойкостью, эластичностью, температуроустойчивостыо, а приготовление их несложное. Состав мастики следующий: 1 весовая часть битума марки 111, 0,7—0,8 весовой части жирной глины и 1 весовая часть воды. Сперва перемешивают глину с водой и полученное глиняное молоко, имеющее густоту сметаны, нагревают до 70—80 °С.
После этого в него вливают расплавленный при температуре 120—160 °С битум, непрерывно перемешивая массу механической мешалкой. Такую мастику возможно приготовлять за ранее и хранить в течение нескольких месяцев. Летом ее направляться заливать сверху слоем воды, а в зимнее — предохранять от замерзания.
Склеивание наступает через 2—5 дней, а процесс твердения мастики заканчивается всецело через 2—3 семь дней.
Рис. 24. Раскладка паркета на рабочем месте:
а — для укладки маячной плиты; б — для нечетных последовательностей; в — для четных последовательностей; 1 — маячная елка, 2 — нечетный последовательность, 3 — четный последовательность, 4 — стопки паркета, 5 — ящик с шипами и гвоздями, 6 — шнур
Использование водоразбавимых глино-битумных мастик повышает производительность труда рабочих и снижает цена 1 м2 настила паркета.
Время от времени паркет укладывают вместо мастики на тёплом асфальте. Паркет прикрепляют к основанию асфальтовой массой, пробравшейся в тёплом состоянии в пазы по периметру клепки.
После этого асфальт остывает, твердеет и прочно держит паркет. Толщина асфальтового слоя в этом случае должна быть 19—25 мм.
Асфальт варят рабочие-асфальтировщики в котле при температуре до 160— 180 °С. Варку асфальта необходимо затевать за 3 часа до начала укладки паркета. Асфальт должен быть песчаным, а не зернистым.
Состав асфальтовой смеси для настилки паркета определяет лаборатория. Асфальтовая масса при укладке должна иметь температуру не меньше 130—150 °С. Транспортируют тёплую асфальтовую массу в посуде, исключающей возможность расплескивания.
Температура окружающей среды при укладке асфальтового слоя должна быть не ниже 5 °С.
Организация рабочего места паркетчика при настилке по асфальту такая же, как и при укладке паркета на рейку. По окончании работ по подготовке подсобные рабочие приносят тёплую асфальтовую массу и выливают при помощи ковша на место, указанное мастером-паркетчиком. Тёплую асфальтовую массу подливают за один раз под 6—8 клепок. Уложенную на основании асфальтовую массу паркетчик разравнивает кельмой.
После этого, забрав из ближайшей пачки паркет, укладывает его левой рукой на асфальт, хорошо прижимает молотком и рукой осаживает до заданной отметки. Осадив паркет, паркетчик кельмой снимает асфальт, что выдавливается прижатой клепкой. Кельму необходимо использовать с малым полотном, поскольку при громадном полотне асфальтовая масса благодаря собственной вязкости разравнивается тяжелее.
Остатки асфальтовой массы подсобный рабочий обязан собирать в ведро и отправлять для переварки.
Для выравнивания плоскости пола подсобный рабочий на уложенные клепки по линии стыка последовательностей кладет рейку длиной около 1,5 м либо легко отдельные клепки и устанавливает на них груз из 2—3 кирпичей. Паркетчик неспешно передвигает рейку с грузом. Дабы уложенная под грузом клепка не отходила от ранее уложенной, у торцов ставят на ребро рейку и подпирают ее кирпичами.
Чтобы не было остывания асфальтовой массы, уложенной на пол, нужно настилку пола делать в один прием. Застывшую до укладки паркета асфальтовую массу вырубают и удаляют, поскольку нехорошая сообщение ветхой и свежей массы осложняет работу и ухудшает ее уровень качества.
Для настилки паркета по асфальту используют маячную раму, применение которой дает экономию асфальтовой массы и снабжает высокий уровень качества работы. Такая рама складывается из двух рамок: верхней 11, изготовленной из угловой стали 35X35 мм, и нижней 2, изготовленной из намерено обрезанных уголков 35X15 мм. Рама является параллелограммомс острыми углами 45°.
Паркетную клепку закладывают между рамками и зажимают винтами 3, 4. Раму устанавливают на основание паркетного пола по шнуру в соответствии с рисунком паркета и при помощи винтов 5 и 6 приводят в горизонтальное положение. Высота винтов от основания до низа паркетной клепки определяет заданную в проекте толщину слоя асфальта. Рядом с маячной рамой на основании укладывают слой асфальта и на него настилают паркет впритык к клепке, зажатой в раме.
Перемещая раму на протяжении помещения, настилают маячный последовательность паркета, а после этого настилают паркет простым порядком.
Рис. 25. Настилка паркета:
Рис. 26. Маячная рама для настилки паркета по асфальту:
1 — верхняя рамка, 2 — нижняя рамка, 3 и 4 — винты с гайками для зажима паркетной клепки между рамками, 5 и 6 — винты с гайками для выверки рамы при установке
Укладка паркета по не в полной мере затвердевшей цементной стяжке производится на холодной битумной мастике, с дополнительным креплением паркета гвоздями. Специальными звеньями производится укладка цементно-песчаной стяжки, приготовление битумной мастики, забивка и сортировка паркета шипов-реек в пазы, укладка паркета, натирка и циклёвка готового покрытия.
Цементный раствор расстилается по шлаковой подсыпке растворонасосом и разравнивается долгой малкой по съемным маячным рейкам. Через 1—2 дней на стяжку (влажностью не меньше 30%) наносят слой холодной битумной мастики. Настилка паркета производится так же, как по дощатому настилу. Паркет укладывают хорошо на основание и крепят гвоздями длиной 45—50 мм.
Забивают гвозди в пазы под углом 45° и втапливают их шляпки добойником.
Укладка паркета таким способом уменьшает технологический разрыв между началом укладки и устройством стяжки паркета в 8—10 раз если сравнивать с настилкой паркета по затвердевшей и просушенной стяжке. Это дает сокращение сроков исполнения ремонта и снабжает надежное скрепление паркета с основанием.
Наборный паркет
Индустриализация паркетных работ достигается методом укрупнения подробностей пола в виде более либо менее большого наборного паркета, изготовленного заводским методом.
Наборный паркет складывается из планок с прямыми кромками, наклеенными лицевой пластью на бумагу, снимаемую вместе с клеем по окончании настилки паркета на основание.
Допускается изготовление наборного паркета из планок шириной 15 мм, взятых в следствии переработки и отбраковки штучного паркета.
Новым ГОСТ 862—60 щитовой паркет не предусмотрен, но, учитывая, что он в свое время на постройке использовался и громадные площади полов настланы им, знать его нужно, поскольку это пригодится при ремонте строений.
Паркетные щиты изготовлялись на деревообрабатывающих фирмах и доставлялись на строительные объекты в готовом виде. Такими щитами заполнялись каждые площади без доборов и обрезков.
Щиты маленького размера именуются тафельными. Щит складывается из брусков обвязки, соединенных со средником шипами на клею. Обвязку заполняют профугованным паркетом и склеивают под линейку и угольник.
С средником и обвязкой паркет скрепляется вставными шипами. Для изготовления та-фельного паркета употреблялись отходы и нестандартные до-Щечки.
Тафельный паркет настилают по древесному и цементному основанию. Тафели прикрепляют к основанию мастикой и гвоздями, либо лишь мастикой.
Рис. 27. Наборный паркет
Для основания паркетного щита употреблялись пиломатериалы низших сортов и отходы производства.
Предварительно набирали паркетными дощечками рисунок и наклеивали их на основание.
Рис. 28. Тафели:
а — из паркета с пазами; б — из паркета на мастику; в — из паркета с фальцем: 1 — фанера либо сухая штукатурка, 2 — слой мастики, 3 — вставные шипы
Рис. 29. Настилка паркетных плит
Щиты с наклеенными паркетными дощечками укладывались в пакеты, запрессовывались и подвергались нагреву в камере при температуре 40—60 °С. После этого щиты выдерживались в помещении. На четырехстороннем станке на боковых кромках щитов выбирали пазы.
При настилке полов щиты укладывали на лаги и прибивали гвоздями. В стыки щитов закладывали планки твердолист-венной породы. Щиты кроме этого укладывали по сглаживающему перекрытие слою и скрепляли между собой рейками, закладываемыми в паз рамок обрамления.
Барановичский завод строительных л подробностей освоил производство нового вида паркета. Из отходов — обрезков дуба, ясеня, сосны, клена, бука — отбирают бруски и заготовляют клепку. После этого готовую клепку собирают в паркетные плиты размером 325X325 мм. Любая такая плита складывается из девяти квадратов, каковые со своей стороны составляются из четырех клепок.
Клепки приклеивают казеиновым клеем на бумагу так, дабы между каждой клепкой оставалось пространство шириной 0,5 см. Для удобства и ускорения вязки применяют особый шаблон, воображающий собой железную форму с гнездами. На уложенные в шаблон клепки наклеивают плотную оберточную бумагу.
Укладывали паркетные плиты на известково-битумной мастике на основание в основном из теплого бетона. Толщина слоя известково-битумной мастики 1 —1,5 мм. По окончании укладки плит безлюдные пространства между клепками заливали магнезиальным цементом (ксилолитом). Для уменьшения осадки ксилолита при перемешивании в него додают небольшую древесную муку и любой сухой краситель, подобранный по цвету пола.
Излишки ксилолита снимают с клепок резиновым шпателем длиной 25 см. Ксилолит при схватывании расширяется, что увеличивает прочность пола и исключает происхождение трещин.
Паркетные доски
Паркетные доски — самый дешёвый и экономичный материал для полов, приобретающий все большее распространение. Размеры паркетных досок продемонстрированы на рис. 411. Паркетные доски складываются из нижнего реечного основания и верхнего лицевого покрытия — паркетных планок с прямыми кромками, наклеенных на основание.
Ширина реек основания должна быть не меньше 20 мм.
Рис. 28. Паркетные доски
Кромки паркетных досок имеют гребень и паз, служащие Для их соединения между собой. Рейки основания при ширине
их более чем 30 мм должны иметь продольные пропилы. Допускается поставка укороченных паркетных досок длиной от 600 до 1200 мм, взятых в следствии переработки отбракованных стандартных досок. Общее число укороченных досок не должно быть больше 15% от размера поставки.
Варианты размещения планок на паркетных досках продемонстрированы на рис. 29. При настилке пола из паркетных досок производительность труда вдесятеро выше, чем при настилке штучного паркета, и практически в пять раз выше, чем при настилке простых досок.
Помимо этого, паркетные доски являются самым недорогим материалом из всех используемых для настилки пола. Полезные породы древесины (дуб, бук), используемые для лицевого покрытия, возможно заменить березовой древесиной зимней заготовки либо лиственницей, и сосной. Имея пресс для тёплого склеивания, любое деревообрабатывающее предприятие в состоянии организовать выпуск паркетных досок.
Технологический процесс производства их складывается из изготовления основания паркетной доски, изготовления покрытия (лицевой стороны) паркетной доски, склеивания основания с покрытием, окончательной обработки, упаковки и отделки.
Основание доски в виде реек (брусков) изготовляют из отходов лесопиления и низкосортных пиломатериалов и деревообработки. Покрытие набирают в форме квадратов («корзинка»), у которых любая сторона не должна быть больше 175 мм, либо с одним поперечным размещением планок. Основание склеивают с покрытием при помощи гидравлического пресса.
После этого паркетную доску совсем обрабатывают по толщине, отбирают гребень и шпунт.
На изготовление паркетных досок затрачивается намного меньше труда, чем на производство паркетных штучного паркета и щитов, а расход древесины уменьшается в 1,5—2 раза.
На деревообрабатывающем комбинате № 13 Главмоспром-стройматериалов организован автоматизированный цех по производству паркетных досок с тремя полуавтоматическими действующими линиями производительностью 550,0 тыс. м2 в год.
Рис. 29. Варианты размещения планок на паркетных досках
На стройках Киева создают укладку полов из паркетных досок по песчаному основанию и из штучного паркета по не в полной мере затвердевшей цементной стяжке. Для соединения между собой доски по краям снабжены гребнем и пазом. Полы из таких досок делают по лагам, укладываемым по слою песка на перекрытии.
Используемый песок не должен содержать органических примесей и иметь влажность не более 8—10%. Для данной цели его прокаливают в переоборудованной известегасилке, где он, поступая через загрузочный люк во поворачивающийся барабан, подвергается прокалке пламенем от форсунки, трудящейся на дизельном горючем. Прокаленный песок расстилают по бетонному перекрытию слоем толщиной 40 мм.
Рис. 30. Прибивка паркетных досок к лагам:
1 — лаги, 2 — паркетные доски
По подготовленной песчаной насыпке укладываются с шагом 0,5—0,6 м антисептированные лаги сечением 50X75 мм, длиной на 25—30 мм меньше помещения. После этого уровнем и рейкой лаги сглаживают, а промежутки между ними заполняют песком заподлицо. По такому основанию поперек лаг раскладывают паркетные доски, тыльная сторона которых в обязательном порядке антисептируется. Доски хорошо сжимаются и крепятся к лагам гвоздями 70 мм.
Их забивают в пазы под углом, шляпки втап-ливают добойником. Между настланными стеной и досками оставляют зазор шириной 8—10 мм, где укладываются полосы из мягких древесно-волокнистых плит или других звукоизоляционных материалов. Таковой метод укладки паркетных Досок повышает производительность труда и снижает затраты тРУда на устройство пола вместе с основанием.
Планки для всех видов паркета изготовляются из древесины дуба, бука, березы, сосны, лиственницы, ясеня, клена, береста (карагач), вяза, ильма, граба, акации и каштана. Буковую древесину пропаривают.
лиственницы и Древесина сосны, из которой изготовляются планки, должна быть радиальной распиловки, угол наклона годовых слоев к лицевой пласти составлять не меньше 45°.
Основание для паркетных досок изготовляют из древесины сосны, ели, лиственницы, пихты и кедра, и из антисепти-рованной древесины березы, ольхи, тополя и осины.
Древесина реек основания паркетных досок должна быть здоровой и подбираться одной породы.
Влажность древесины готовых паркетных досок, штучного паркета, реек основания и наборного паркета паркетных досок должна быть 8% абс. с допускаемым отклонением ±2%.
Рейки смогут быть по длине цельными либо составными. В составных рейках стыки должны размешаться вразбежку.
В штучном паркете и паркетных досках размеры пазов и гребней должны быть однообразными на всем протяжении и пребывать на одном расстоянии от пластей. Допускается в пазах и гребнях паркетных досок и планок закругление углов. Лицевые поверхности всех изделий должны быть ровными и ровными.
При укладке планки паркетных наборного паркета и досок направляться подбирать по цвету древесины.
Планки лицевого покрытия паркетных досок склеиваются с основанием водостойкими синтетическими фенолформальдегид-ными клеями СП-3 и КБ-2, меламиновыми ММФ, резорциновыми ФР-12. Склейка должна быть прочной и плотной.
В наборном паркете для наклейки планок используется крафт-бумага либо вторая бумага, соответствующая ей по качеству, и клей типа декстринового, что легко снимается вместе с бумагой и не требует промывки поверхности паркета водой.