Приготовление формовочных и стержневых смесей
Приготовление формовочных смесей складывается из трех этапов:
1 — подготовки свежих формовочных материалов; 2 — подготовки отработанных смесей; 3 — изготовление смеси из предварительно подготовленных материалов.
Пески, поступающие на склад формовочных материалов, смогут иметь самую разную влажность, исходя из этого они подвергаются сушке при температуре ~250 °С, что позволяет обеспечить заданную влажность формовочных смесей. Пески сушат в печах барабанного типа, аппаратах кипящего слоя и в установках, трудящихся по принципу пневмопотока.
Аппарат кипящего слоя есть одним из современных сушильных агрегатов. Перед началом сушки песок находится на решетке с отверстиями диаметром 4 мм. Площадь отверстий образовывает 10% площади решетки. Толщина слоя песка около 400-450 мм.
Топку делают герметически закрытой так, дабы продукты сгорания имели возможность двигаться лишь по направлению к песку. Дымовые газы при температуре около 1000 °С, направляющиеся под решетку под давлением 400 мм вод. ст., поднимают песок с решетки, отдельные песчинки совершают стремительное хаотичное перемещение.
Расширение конического резервуара содействует понижению скорости перемещения песчинок и оседанию их. В трубу в потоке газов выносятся частицы пыли. Высушенный песок непрерывно вытекает через желоб 6, а мокрый песок непрерывно поступает по транспортеру через воронку.
Производительность этих установок до 10 т/ч.
По окончании сушки песок охлаждается до обычной температуры и просеивается (с целью отделения комьев, гальки и разных посторонних включений) через сита с плоским полотном либо барабанные и конические сита с размером ячеек 3-5 мм.
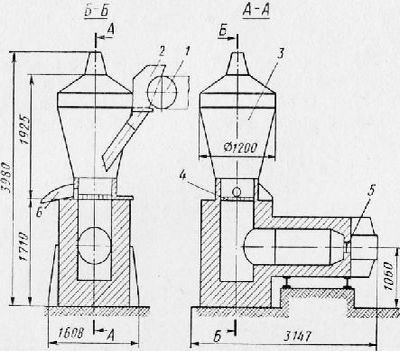
Рис. 1. Аппарат кипящего слоя: 1 — транспортер для сырого песка; 2 — приемная воронка с рукавом; 3 — конический резервуар; 4 — решетка; 5-топка; 6 — рукав для сухого песка
Глину предварительно сушат и размельчают. Монтморилло-нитовые глины сушат при 120 °С, а остальные — при 200-250 °С. В большинстве случаев сушат в барабанных печах.
Высушенную глину размельчают в два приема: сперва реализовывают неотёсанное разделение на куски размером 15-25 мм в ще-ковых, вальцовых и молотковых дробилках, после этого глину размалывают до размера менее 0,1 мм в шаровых, молотковых, крестовых мельницах, а кроме этого в мельницах типа бегунов. Затем глину просеивают через сита, подобные ситам, применяемым для просева песков.
Целесообразно в формовочные смеси вводить не порошковую глину, а суспензию. На 45-60 в. ч. воды берется 35-40 в. ч. сухой глины. Суспензию приготовляют смешением глины с водой в бегунах, лопастных смесителях либо в шаровых мельницах.
Готовая суспензия подается по трубопроводу либо в особых баках к местам изготовление формовочных смесей.
По сравнению со методом, предусматривающим применение порошковой глины, данный метод имеет следующие преимущества:
1. Расход глины значительно уменьшается приблизительно на 30% благодаря увеличения связующей свойстве глины.
2. Исключение дробильно-размольного, сушильного и просеивающего оборудования и обслуживающих их транспортных средств.
3. Не нужно горючее для сушки глины.
Использование суспензии глины ограничивается тем, что при введении в смесь 1% глины в один момент вводится 1,5% воды. При повышенной влажности вторых компонентов смеси это может оказаться недопустимым.
Угольный порошок приготовляют на том же дробильно-размольном оборудовании, что и порошковую глину.
Остальные свежие материалы (связующие, пылевидный кварц и др.) поступают в литейные цехи в готовом виде и не требуют особой подготовки.
Отработанную смесь, выбитую из опок, предварительно перерабатывают и после этого подают в смесеприготовительное отделение. Отработанная смесь, приобретаемая по окончании выбивки сухих форм, содержит жёсткие комья, каковые разминают в ровных валках. Отработанная смесь, приобретаемая по окончании выбивки мокрых форм, легко рассыпается и обработки в валках не требует.
Для удаления из смеси железных включений (брызг металла, каркасов стержней) используют магнитный сепаратор. В ведущем шкиве 1 ленточного конвейера 3, подающего отработанную смесь от выбивной решетки, находится многополюсный электромагнит. Железные частицы, притягиваясь к магниту, прижимаются к ленте конвейера и падают лишь тогда, в то время, когда лента сходит со шкива. Немагнитный материал — отработанная смесь ссыпается с ленты отдельным потоком раньше железных частиц.
Железные частицы планируют в емкости 2, а отработанная смесь передается ленточным конвейером на последующую переработку.
По окончании магнитной сепарации отработанная смесь просеивается через цилиндрические либо конические сита с размерами ячеек 6-10 мм для отделения немагнитных включений. Смесь, охлажденная до 50 °С, направляется в смесеприготовительное отделение.
Отработанные стержневые смеси, которые содержат пленки затвердевших связующих, подвергают особой переработке, именуемой регенерацией. Целью регенерации есть получение продукта (дегенерата), что снова возможно использован, как заменитель свежего формовочного песка, входящего в состав стержневых смесей.
Рис. 2. Схема магнитного сепаратора
Отработанная стержневая смесь разминается. Комья распадаются на отдельные зерна песка и на пылевидные частицы, образованные растрескавшимися остатками плёнок и зёрнами песка связующих. По окончании смесь классифицируют по размеру зерен или в воздушном потоке, неспешно изменяющем скорость собственного перемещения (сухая регенерация), или по окончании смешения с водой — в особых отстойных чанах (мокрая регенерация).
Процесс регенерации требует больших производственных площадей и связан с громадными затратами, исходя из этого он используется лишь на фабриках, каковые находятся на громадном расстоянии от месторождения отличного кварцевого песка.
Приготовление формовочных смесей включает следующие операции: перемешивание ранее подготовленных составляющих смеси, увлажнения, разрыхления и вылёживания смеси.
Сущность процесса перемешивания пребывает в том, дабы из песка, связующего и воды взять однородную смесь, все зерна песка которой были бы покрыты узким, равномерным слоем увлажненной глины либо другого связующего. Это снабжает получение газопроницаемости смесей и высокой прочности,
Формовочные и стержневые смеси перемешивают в особых смесителях. Самый распространены смесители типа бегунов. Бегуны делают с вертикальными и горизонтальными катками.
На рис. 3 приведена схема автоматизированных бегунов с горизонтальными катками. На траверсе, укрепленной на вертикальном валу, находятся маятники, на которых подвешены катки. Маятники шарниром соединены с траверсой, которая связана с вертикальным валом. При вращении вала катки под действием центробежных сил отклоняются к борту чаши.
Смесь поднимается со дна чаши вращающимися вместе с траверсой плужками и подается под катки, каковые разминают комья.
Перемешивание смеси обеспечивается совместным действием катков и плужков. По окончании окончания перемешивания смесь удаляют из чаши через люк.
Производительность бегунов до двадцати метров31ч мовочной смеси. Длительность изготовление одного замеса 1,5-2,0 мин.
Рис. 3. Смешивающие бегуны с горизонтально расположенными катками
Автоматические бегуны смогут последовательно делать шесть операций: подачу в пустую чашу заданного количества воды, загрузку песка либо отработанной смеси, удаление пыли отсосем воздуха из чаши бегунов, загрузку связующих из особого лотка, смешивание смеси, выгрузку из чаши готовой смеси. Любая из шести операций выполняется в течение заданного промежутка времени.
Автоматизация работы смесителей снабжает более правильное дозирование составляющих смеси и исполнение всех операций по заданному режиму. стабильность и Качество особенностей форм, изготовляемых из этих смесей и приобретаемых отливок, существенно выше, чем при ручном (кнопочном) методе управления операциями. По окончании переработки в бегунах формовочные и стержневые смеси, связующим в которых есть глина, поступают на 2-6 ч в бункеры-отстойники.
Это время нужно для образования водных оболочек около устранения неравномерности и глинистых частиц распределения жидкости в отдельных конгломератов зерен.
Для смесей с довольно низким содержанием глины (мокрые формы) время вылеживания образовывает 2-4 ч. Для смесей с высоким содержанием глины (сухие формы) это время возрастает до 5 ч и более. По окончании бункеров-отстойников смесь подвергается разрыхлению в разрыхлителях, дезинтеграторах и аэраторах, что снабжает громадную однородность степени уплотнения смеси при изготовлении форм и высокую газопроницаемость.
В аэраторе вращающиеся на валу лопатки подхватывают непрерывно поступающую в загрузочную воронку смесь и бросают ее на решетку, складывающуюся из вольно подвешенных прутьев либо цепей, с которых она падает уже разрыхленной. Производительность аэраторов достигает 80 м31ч. Дезинтеграторы рассчитывают на меньшую производительность.
По окончании разрыхления формовочная смесь совокупностью ленточных конвейеров подается в бункеры над формовочными автомобилями. В большинстве случаев один ленточный конвейер устанавливают над несколькими бункерами, расположенными над рядом формовочных автомобилей. При ручном управлении процессом рабочий опускает на ленту сгребающий формовочная смесь и плужок ссыпается в бункер, по окончании заполнения которого тот же рабочий поднимает плужок, и смесь транспортируется к следующей машине.
В большинстве случаев один рабочий обслуживает 6-8 формовочных автомобилей.
Рис. 4. Схема аэратора
Автоматизация распределения смеси по бункерам снабжает бесперебойное снабжение автомобилей смесью. При неавтоматизированном распределении емкость бункеров должна быть большой (до десяти метров3 и более), дабы рабочий успевал вовремя опускать и поднимать плужки. При автоматизации процесса эти операции осуществляются довольно часто, исходя из этого емкость бункеров возможно в пара раз уменьшить (до 1 м3), что существенно усиливает свойства смесей.
В случае если смесь была предварительно аэрировала, то в громадном бункере она слеживается, спрессовывается и эффект аэрации исчезает. При автоматизированной раздаче смесь в бункерах малого количества будет в разрыхленном состоянии, легко высыпается из бункера.
В современном смесеприготовительном отделении литейного цеха оборудование располагают в последовательности, приведенной на схеме 3.
Схема 3. Приготовление формовочной смеси
На данный момент созданы конструкции всецело системы и автоматизированных смесителей автоматической раздачи смесей к формовочным автомобилям. Так, смесеприготовительное отделение современного литейного цеха может трудиться всецело в автоматическом режиме без яркого вмешательства со стороны персонала . В случае если смесеприготовительная совокупность обслуживает целый литейный цех, то ее именуют центральной смесеприготовительной совокупностью’.
Довольно часто строят независимые смесеприготовительные совокупности, любая из которых обслуживает одну автоматическую линию. В цехе возможно пара независимых независимых смесеприготовительных совокупностей, трудящихся независимо друг от друга. Последовательность технологических операций и расстановка оборудования и в этом случае сохраняются.
Для обеспечения обычных условий работы персоналав смесеприготовительном отделении на всех участках, которые связаны с переработкой и транспортировкой пыле-выделяющих смесей и материалов (песка, глины, отработанных смесей, пылевидного кварца и др.), должна быть установлена замечательная и действенно трудящаяся приточно-вытяжная вентиляция.