Станки токарной группы
В группу токарных станков входят: токарно-винторезные токарно-револьверные, многорезцовые токарные, карусельно-токарные, лобовые, токарные автоматы и полуавтоматы и особые токарные станки.
Станки токарной группы используются значительно чаще для обработки тел вращения. При исполнении работ на этих станках обеспечивается получение наружных и внутренних цилиндрических и конических поверхностей, фасонных поверхностей, торцовых плоскостей, нарезки на цилиндрической и торцовой поверхностях и др.
Главными инструментами для станков токарной группы помогают резцы разных типов. На этих станках употребляются кроме этого сверла, зенкеры, зенковки, развертки, метчики, плашки и пр.
В большинстве автомобилей и механизмов громаднейшее количество подробностей воображает тела вращения, исходя из этого конечно, что станки токарной группы на машиностроительных фабриках, в большинстве случаев, являются главным оборудованием механических цехов и составляют больше половины всех металлообрабатывающих станков.
Токарно-винторезные станки. Токарно-винторезные станки являются универсальными и используются для изготовления самых разнообразных подробностей. Эти станки активно применяются в единичном, мелкосерийном производстве и на ремонтных работах, в механических, ремонтных, инструментальных, экспериментальных цехах фабрик, а также в мастерских РТС, научно-исследовательских университетов, в учебных и мобильных мастерских.
Токарно-винторезные станки характеризуются широкими технологическими возможностями и употребляются для черновой и чистовой обработки цилиндрических, конических и фасонных поверхностей, для сверления, рассверливания, растачивания и развёртывания отверстий, нарезания резьбы разных видов и пр.
В массовом производстве универсальные токарные станки не используются, уступая место автоматам, многорезцовым и специальным станкам.
Токарно-винторезные станки бывают самых разных размеров: от настольных — для обработки подробностей часовых и других приборов и мелких механизмов, до тяжелых — для обработки разных больших подробностей.
Главными размерными чертями токарно-винторезных станков являются высота центров над станиной и громаднейшее расстояние между центрами задней бабок и передней.
На рис. 1 продемонстрирован средний токарно-винторезный станок модели 1А62 выпуска завода «Красный пролетарий». Он есть предстоящим усовершенствованием токарно-винторезного станка 1Д62 (ДИП-200).
На станке смогут обрабатываться подробности с громаднейшим диаметром 400 мм и длиной до 2000 мм.
Главные части (узлы) токарно-винторезного станка: станина, передняя бабка с коробкой скоростей, суппорт с фартуком, механизм и задняя бабка для передачи перемещения от шпинделя к суппорту, складывающийся из трензеля, сменных колес, коробки подач, ходового валика и ходового винта.
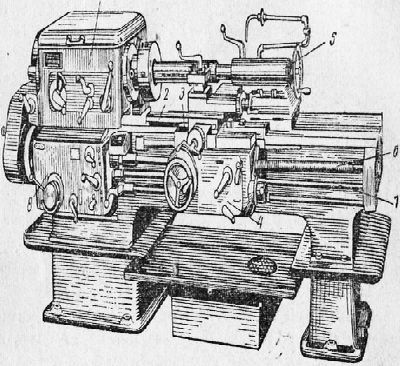
Рис. 1. Токарно-винторезный станок, модель IA62
Станина помогает для установки всех частей станка. Она отливается из чугуна и имеет коробчатую форму. Верхняя часть станины имеет направляющие (плоские и призматические) для передвижения по ним задней бабки и суппорта.
Износостойкость направляющих повышают методом закалки ацетилено-кислородным пламенем.
Передняя бабка без движений крепится к станине и снимается лишь при капитальном ремонте станка.
Шпиндель помогает для сообщения заготовке главного перемещения посредством разных приспособлений.
На правой части шпинделя нарезана резьба для навин
чивания патронов либо особых приспособлений. Внутренняя часть шпинделя с правой стороны обработана на конус для центра и установки втулки. Отверстие в шпинделе делают сквозным для возможности пропуска прутков, являющихся заготовками для подробностей.
В корпуса передней бабки токарных станков в большинстве случаев расположена коробка скоростей с зубчатыми колесами. То либо иное число оборотов шпинделя достигается при переключении рукояток коробки скоростей (рукоятками осуществляется перемещение блоков колес в коробки).
Рис. 2. Правая часть шпинделя
На рис. 3 приведена кинематическая схема коробки скоростей станка 1А62. шкив и Электродвигатель коробки скоростей соединены клиновидными ремнями, что снабжает передачу мощности главного привода до 7 кет.
На схеме римскими цифрами обозначены валы, арабскими — числа зубьев шестеренок.
При постоянном направлении вращения электродвигателя прямое вращение шпинделя достигается подключением муфты вала I к колесу 51; обратное вращение — подключением ее через колесо 50.
Рис. 3. Кинематическая схема коробки скоростей станка IA62
Предельное количество оборотов шпинделя образовывает 1200 об/мин., минимальное *— 11,5 об/мин.
Количество разных положений регулирования чисел оборотов шпинделя при прямом вращении образовывает30 (бот вала III и 24 от вала V)\ при обратном вращении — 15 (3 от вала III и 12 от вала У).
Приведенная схема коробки скоростей есть самый распространенной как у токарных станков, так и у станков других типов. Не считая этих механизмов, для регулирования скоростей используют ступенчато-шкивные приводы без переборов и с переборами, двигатели с переменным числом оборотов, гидравлические коробки скоростей, приводы В. А. Светозарова и др.
Задняя бабка (рис. 4) используется: при обработке валов — для их поддержания; для закрепления сверл, зенкеров, других инструментов и развёрток, применяемых при обработке отверстий; при обработке конусов с маленькими углами.
Нижняя поверхность основания задней бабки пришабрена по направляющим станины и скользит по ним при перемещении бабки. Планкой, гайкой и болтом производится закрепление бабки в той либо другой части станины.
Рис. 4. Задняя бабка. лов крайне важно обеспечить посто
На рис. 5 продемонстрирована задняя бабка с вращающимся пружиной и центром, снабжающей постоянство осевого упрочнения. При вращении маховичка центр войдет в центровое отверстие вала.
Рис. 5. Задняя бабка с вращающимся компенсатором и центром
Суппорт рекомендован для крепления режущих инструментов, в основном резцов, и сообщения им перемещения подачи. Посредством отдельных частей суппорта резец возможно перемещать в разных направлениях.
Самая верхняя часть суппорта — резцедержатель употребляется для закрепления резцов. Ясно, что резцедержатель (а с ним и резец) будет перемещаться при перемещении одной из частей суппорта, расположенной ниже. Токарно-винторезные станки оборудуются одноместными либо чаще четырехпозиционными поворотными резцедержателями, разрешающими в один момент закреплять до четырех резцов.
Преимуществом резцедержателей для того чтобы типа есть экономия времени на установку резцов и обеспечение возможности работы по настройке.
Рис. 6. Суппорт
Продольные (нижние) салазки при вращении маховичка перемещаются по направляющим станины. При перемещении продольных салазок вершина резца будет перемещаться по прямой, параллельной оси шпинделя.
Поперечные салазки при вращении рукоятки перемещаются по направляющим нижних салазок. При перемещении поперечных салазок вершина резца будет перемещаться по прямой, перпендикулярной к оси шпинделя.
Поворотная часть центрируется в кольцевой выточке поперечных салазок и закрепляется на поперечных салазках гайками.
Верхние салазки посредством рукоятки перемещаются по направляющим поворотной части. Установка (при необходимости) поворотной части под тем либо вторым углом производится по шкале.
Фартук крепится к продольным салазкам суппорта. На передней стенке фартука расположены рукоятки и маховички управления перемещением суппорта. Суппорт может передвигаться не только от руки, но и машинально (самоходом) от ходового валика 6 либо от ходового винта.
На задней стенке фартука смонтированы разные подробности, связывающие суппорт с зубчатой рейкой (привинченной к станине) ходовым валиком и ходовым винтом.
На рис. 7 в качестве несложной приведена часть кинематической цепи подачи — механизм фартука (вид со стороны станины станка). На ходовой валик, имеющий продольную шпоночную канавку, надет червяк . При перемещении суппорта на протяжении станины данный червяк кроме этого перемещается, увлекаемый приливами, каковые расположены на задней стенке фартука.
В отверстии червяка имеется шпонка, исходя из этого при вращении ходового валика червяк кроме этого вращается. От червяка вращение передается червячному зубчатому колесу и расположенному с ним соосно цилиндрическому зубчатому колесу; потом приводятся в перемещение шестеренки. Колесо находится в постоянном зацеплении с зубчатой рейкой (привинченной к станине) и, обкатывая ее, информирует перемещение суппорту.
выключение и Включение самохода по данной схеме осуществляется конусной муфтой (на рис. 233 отсутствует), расположенной между колесами, при помощи маховичка.
Рис. 7. Механизм самохода суппорта
На рис. 8 приведена кинематическая схема (а) и вид со стороны передней стены (б) фартука токарно-винторезного станка 1А62. Механизмы фартука снабжают продольную и поперечную подачи самоходом (каждую в обоих направлениях), и автоматическое выключение подачи при работе по упору и при перегрузках механизма подачи.
Рукоятка помогает для реверсирования и выключения станка. Маховиком производится перемещение суппорта по станине вручную через колеса г106, z40, г12 от зубчатой рейки.
Для продольной подачи суппорта самоходом рукояткой подключают колесо z2i к колесу гБ0 (положение, приведенное на схеме), а рукояткой подключают червяк к червячному колесу г30. Тогда перемещение от ходового валика к колесу z]2, связанному с зубчатой рейкой, будет передаваться по пути, продемонстрированному целыми стрелками. Дабы поменять направление подачи, достаточно рукояткой 4 передвинуть блок колес zs3 и гы так, дабы колесо z40 вошло в зацепление с колесом z40; разумеется, что направление вращения всей последующей совокупности колес наряду с этим изменится, поскольку в кинематической цепи будет одним колесом меньше.
Для поперечной подачи суппорта самоходом рукояткой подключают колесо г24 к колесу z65. Тогда перемещение будет передаваться колесу z20, насаженному на винт поперечной подачи (пунктирные линии).
Рис. 8. Кинематическая схема (а) и неспециализированный вид (б) фартука станка 1А62
Количество продольных и поперечных подач суппорта образовывает 35; пределы подач суппорта в мм на один оборот шпинделя: продольных 0,082 ч- 1,59, поперечных 0,027 f 0,52.
При повышении упрочнения подачи сверх установленного, а также в случае контакта суппорта с упором червяк машинально отключается от колена z30 и падает вниз; это обеспечивается шарнирным соединением червяка с ведущим валом, и наличием регулируемой пружины и муфты.
Автоматическое перемещение суппорта с введением в цепь ходового винта в большинстве случаев используют при нарезании резьбы. Для соединения суппорта с ходовым винтом на задней стенке фартука имеется разъемная гайка (рис. 9), а на передней — рукоятка 2 маточной гайки, при повороте которой половины гайки или хорошо охватывают ходовой винт (тогда вращательное перемещение ходового винта преобразуется в поступательное перемещение гайки и суппорта), или освобождают винт (суппорт останавливается).
Одновременное включение подач от ходового валика и ходового винта ведет к поломке и заклиниванию механизма подачи, исходя из этого современные станки снабжаются блокировочными устройствами, мешающими такому включению.
Рис. 9. Механизм маточной гайки
На рис. 10 приведена кинематическая цепь передачи перемещения от шпинделя к суппорту. Такую несложную схему имеют многие станки; она складывается из узла трензеля (реверсивного механизма), узла сменных шестеренок II, узла коробки подач III, ходового винта, узлов механизмов и ходового валика фартука IV (рассмотренных выше).
Узлы сменных колес II и коробки подач III снабжают получение разных подач (больших и небольших).
Рис. 10. Кинематическая цепь передачи от шпинделя к суппорту
При нарезании резьбы посредством сменных колес, механизма коробки ходового винта и подач обеспечивается правильное согласование поступательного движения и вращения заготовки суппорта с резцом. Наличие узла сменных колес связано с необходимостью нарезания резьб с различным шагом при ходовом винте с постоянным шагом.
Существуют станки без коробок подач. На этих станках первое сменное колесо надевается на палец трензеля (как и на станках с коробкой подач), а последнее — конкретно на ходовой винт. При передаче в одну несколько сменных колес на палец, закрепленный в прорези гитары, устанавливают промежуточное колесо znp, благодаря которому связывают колесо г1 с колесом z2. Гитара надета на ходовой винт и закрепляется в определенном по
Рис. 11. Схема установки сменных колес: а — для передачи в одну несколько; б — для передачи в две пары
Рис. 12. Кинематическая схема ^карно-винторезного станка 1А62
Заводом «Красный пролетарий» выпускается станок 1К62, что имеет верхний электродвигателя 10 предел и мощность кет чисел оборотов шпинделя 2000 об/мин. Данный станок имеет последовательность усовершенствований: ускоренное перемещение продольных и поперечных салазок суппорта от отдельного электродвигателя; механическую подачу задней бабки (вместе с суппортом) при сверлении, зенкеровании и других операциях, в то время, когда инструмент крепится в пиноли задней бабки; эргономичное управление коробкой подач и пр.
Приспособления для токарных станков. Центры помогают для установки (базировки) заготовок между пинолью и шпинделем станка задней бабки. Для установки заготовок в центрах на их торцах предварительно высверливают центровые отверстия.
Цередача крутящего момента от шпинделя при обработке в центрах в большинстве случаев осуществляется патронами либо поводковыми устройствами. На рис. 240 приведен поводковый патрон, навинчиваемый на шпиндель, ихомутик, закрепляемый на левом финише заготовки посредством болта. Не считая изогнутых хомутиков, существуют кроме этого прямые; для работы с ними используются патроны с поводковым пальцем.
При скоростной обработке валов используют задние центры, наплавленные сормайтом либо оснащенные пластинками жёстких сплавов, и вращающиеся центры.
Рис. 13. Центр и зацентрованная заготовка
Рис. 14. Установка заготовки в центрах
С целью сокращения времени на закрепление заготовки используют разные самозажимные хомутики либо самозажимные поводковые патроны. Воздействие самозажимного хомутика легко понять из рис. 15.
При вращении поводкового патрона его палец упирается в рычаг хомутика, что и зажимает обрабатываемую заготовку.
Самоцентрирующие патроны используются в большинстве случаев для закрепления цилиндрических заготовок с одновременным их центрированием. Самоцентрирующий патрон закрепляется на шпинделе станка. Существует пара конструкций центрирующих механизмов патронов: с двузначным винтом, спиральные, реечные и другие, с числом кулачков от 2 до 4. Большая экономия времени при закреплении подробностей в патронах достигается применением быстродействующих приводов.
Рис. 15. Самозажимной хомутик
Рис. 16.Самоцентрирующий патрон
Рис. 17. Четырехкулачковый патрон
Рис. 18. Крепление заготовки на планшайбе посредством угольника
Рис. 19. Пневматический трехкулачковый самоцентрирующий патрон
У четырехкулачковых патронов любой кулачок возможно перемещать раздельно, что разрешает закреплять в них некруглые и несимметричные заготовки. Выверка заготовок в четырехкулачковых патронах во многих случаях требует большое количество времени.
В то время, когда закрепление заготовок в простых патронах нереально, используют особое приспособление либо планшайбу, к которой прикрепляется угольник. На нем устанавливается и закрепляется обрабатываемая заготовка. Для уравновешивания вращающихся весов к планшайбе прикрепляется противовес.
Самоцентрирующие и четырехкулачковые патроны приведенной конструкции, и планшайба требуют ручного зажима заготовки. Это есть их неспециализированным недочётом. В массовом и серийном производстве с целью сокращения вспомогательного времени используют быстродействующие пневматические, гидравлические, электрические и другие патроны.
Рис. 20. Крепление заготовки на конусной оправке
На рис. 19 продемонстрирован трехкулачковый пневматический самоцентрирующий патрон с клиновым механизмом. Действием сжатого воздуха (под давлением 4—7 ати) винт может перемещаться в ту либо другую сторону в осевом направлении (продемонстрировано стрелками). В один момент в центральном отверстии корпуса будет передвигаться муфта с тремя наклонными пазами для связи со скошенными поверхностями кулачков.
Вместе с кулачками передвигаются сменные кулачки , которыми закрепляется заготовка. При перемещении винта 2 влево кулачки будут зажимать заготовку, при перемещении вправо — освобождать.
Для обеспечения концентричности поверхностей обрабатываемых подробностей (шестеренок, втулок, дисков и т. д.) чистовую обработку в большинстве случаев начинают с отверстия; в будущем это отверстие употребляется в качестве базы при установке подробностей на особые оправки. Имеется большое количество разных конструкций оправок: твёрдые, цанговые, плунжерные, самозажимные и др. На рис.
21 приведена несложная конусная оправка, на которой заготовка (продемонстрирована штрихпунктирными линиями) удерживается благодаря заклинивания в отверстии (Dd).
При обтачивании нежестких валов (протяженность которых на порядок и более превышает диаметр) установка их лишь на центрах, без опоры в средней части, оказывается недостаточной, поскольку под действием упрочнения резания будет происходить большой изгиб заготовки. Это затрудняет обработку и приводит к снижению точности. Предотвращение изгиба обеспечивается введением дополнительной опоры для заготовок. В качестве таковой опоры употребляются люнеты.
Любой токарный станок снабжается в большинстве случаев двумя люнетами — подвижным и неподвижным.
Рис. 21. Неподвижный люнет с подшипниками качения
Рис. 22. Подвижный люнет-виброгаситель
Неподвижный люнет устанавливается и закрепляется на станине; он имеет три кулачка, поддерживающих заготовку при обработке.
Кулачки люнета в большинстве случаев оснащаются медными подушками, заливаются баббитом либо снабжаются роликами. При высоких скоростях резания отмечается большое нагревание медных либо кроме того баббитовых кулачков и обрабатываемой заготовки, исходя из этого для скоростной обработки валов рациональнее использовать особые люнеты. На рис.
12 приведен неподвижный люнет с подшипниками качения.
Подвижный люнет устанавливается на продольных салазках суппорта; его кулачки касаются обработанной поверхности и принимают на себя то давление, которое при отсутствии их позвало бы изгиб заготовки. Рационально использовать подвижные люнеты-виброгасители (рис. 22), каковые не только предотвращают изгибы заготовок, но в один момент гасят вибрации, появляющиеся при обработке валов.
Колебания от заготовки через поршни и ролики передаются гидравлической совокупности (находящейся под давлением 1,5—2 ати) и гасятся ею.
Механизирующие и автоматизирующие устройства чтобы получить размеры. В целях повышения производительности используют разные устройства, механизирующие и автоматизирующие получение требуемых размеров подробностей. К таким устройствам относятся продольные и упоры и поперечные лимбы.
На рис. 23 приведена схема работы по упору с длино-ограничителями (мерные бруски). Упор закрепляется на станине.
Рис. 23. Схема работы по упору с длинноограничителями
Получение того либо иного из размеров подробности достигается при соприкосновении суппорта с длиноограничителем и упором.
Автоматизирующие устройства разрешают машинально приобретать заданные размеры как по длине, так и по диаметру, снабжают ускоренный подвод резца и автоматический отвод и т. д.
Револьверные станки. Токарно-револьверные станки используются в условиях серийного производства для того чтобы как из штучной, так и из прутковой заготовки.
Сущестзенным отличием этих станков от токарно-винторезных есть наличие револьверной головки вместо задней бабки. Револьверная- головка крепится на продольных салазках, она может поворачиваться около оси и фиксироваться в той либо другой позиции. Число позиций у головок с вертикальной осью в большинстве случаев равняется шести, а у головок с горизонтальной осью — до шестнадцати.
Обработка деталей на револьверном станке производится последовательно инструментами, закрепленными в разных гнездах револьверной головки.
К этим инструментам относятся: зенкеры, развертки, проходные, расточные, резьбовые резцы и пр.
На рис. 24 приведен токарно-револьверный станок с вертикальной осью револьверной головки для обработки штучных заготовок.
Рис. 24. Токарно-револьверный станок с вертикальной осью головки
Револьверная головка перемещается по станине с рабочим либо холостым (ускоренным) ходом.
За один оборот револьверной головки, при последовательном применении работы инструментов всех позиций производится целый цикл обработки заготовки — значительно чаще наружное обработка и обтачивание отверстий.
Рис. 25. Схема револьверного станка с горизонтальной осью головки
Суппорт употребляется в основном для переходов, делаемых при поперечной подаче (обтачивание торцов обдирочными и подрезными резцами, протачивание канавок, отрезание и т. д.).
На рис. 25 приведен револьверный станок с горизонтальной осью револьверной головки для обработки прутковых заготовок.
Продольная подача обеспечивается при перемещении салазок по направляющим станины. Круговое перемещение револьверной головки употребляется для отрезки и поперечной подачи, исходя из этого надобность в поперечном суппорте отпадает. Много позиций допускает крепление громадного количества инструментов, что разрешает обрабатывать подробности сложной формы.
движения главного подачи и Механизмы движения у револьверных станков подобны этим механизмам токарно-винторезных станков.
По механизации и степени автоматизации запасных перемещений револьверные станки стоят выше токарно-винторезных: поворот револьверной головки разрешает скоро перейти от обработки одним инструментом к обработке вторым, выключение подачи в конце рабочего хода производится машинально от упоров, сменяющихся при каждом повороте револьверной головки. Использование револьверных станков вместо токарно-винторезных дает большую экономию штучного времени при обработке средних и малых серий сложной конфигурации. Для обработки больших серий и в массовом производстве револьверные станки вытесняются автоматами и полуавтоматами.
Размер револьверных станков характеризуется громаднейшим диаметром (от 200 до 630 мм) изделия — при обработке штучной заготовки, либо громаднейшим диаметром (от 12 до 110 мм) прутка.
Для обработки каждой серии (партии) деталей производится настройка станка: установка инструментов, упоров, подач и скоростей.
Карусельные станки. Карусельно-токарные (карусельные) станки используются для крупных заготовок и обработки средних, диаметр которых в большинстве случаев превышает их высоту. Ось вращения заготовки при обработке на карусельно-токариом станке вертикальна (а не горизонтальна, как у всех других станков токарной группы), потому эти станки и стали называться карусельных.
На карусельных станках возможно создавать растачивания и операции обтачивания цилиндрических, конических и фасонных поверхностей, подрезания и обтачивания торцов, отрезания, резьбонареза-ния, сверления, зенкерования и развертывания отверстий (последние три вида обработки не смогут производиться на станках, не имеющих револьверной головки).
Заготовка закрепляется на планшайбе, установленной на круговых направляющих станины. На направляющих стойки имеется поперечина, несущая вертикальный суппорт с револьверной головкой. На тех же направляющих установлен боковой суппорт.
Карусельные станки разделяются на одностоечные и двухстоечные. Одностоечные станкиизготовляются с боковым суппортом либо без него. Громаднейший диаметр обработки на этих станках, в зависимости от размеров станка колеблется от 800 до 1650 мм.
Двухстоечные станки (рис. 253) являются более твёрдыми и используются для обработки больших заготовок; они имеют на поперечине два вертикальных суппорта, а на правой стойке — боковой суппорт. Кое-какие станки снабжаются еще и четвертым суппортом, устанавливаемым на левой стойке.
Эти станки изготовляются с громаднейшим диаметром обработки от 1650 до 26 000 мм.
Карусельные станки стали широко распространены на всех фабриках крупного машиностроения и среднего в связи с удобством
обработки и установки на них тяжелых и больших заготовок.
Токарные автоматы и полуавтоматы. Токарные автоматы используются для изготовления разных подробностей из прутковых, и из штучных заготовок. Работа налаженного автомата — установка, ее обработка и закрепление заготовки — выполняется без участия рабочего.
Обязанности рабочего заключаются в периодической зарядке автомата заготовками, периодическом контроле готовых подробностей, осуществляемом, в большинстве случаев, шаблонами и предельными калибрами. Настройку автоматов делают высококвалифицированные наладчики.
Токарные автоматы разделяются на одношпиндельные и многошпиндельные. На рис. 28 в качестве несложной приведена схема одношпиндельного пруткового автомата.
Управление работой автомата осуществляется распределительным валом, на котором закреплены кулачки и барабаны, приводящие в перемещение разные части автомата. Так, барабан руководит подачей прутка, барабан — зажимом прутка, кулачок — перемещением поперечного суппорта, барабан — перемещением продольного суппорта 6.
Рис. 26. Одностоечный карусельный станок
Рабочий цикл автомата соответствует одному обороту распределительного вала; это значит, что при каждом обороте вала автомат обрабатывает одну подробность.
Большая часть одношпиндельных автоматов имеет револьверную головку, и разработка обработки заготовок на них такая же, как и на револьверных станках. Различие между револьверными станками и одношпиндельными автоматами заключаете J наличии у последних узла распределительного вала, делающего те функции, каковые приходится делать рабочему у револьверного станка.
Так, программа автомата определяется звеньями узла распределительного вала.
Рис. 28. Кинематическая схема одношпинделыюго пруткового автомата.
На рис. 29 приведена схема одношпиндельного токарно-револь-верного автомата 1136 для обработки прутковой заготовки круглого и многогранного (квадратного, шестигранного и др.) сечения.
Механизм помогает для автоматической подачи заготовки; зажим заготовки осуществляется особым механизмом шпиндельного узла. Работа этих механизмов, и перемещения револьверной головки (имеющей горизонтальную ось вращения) смена ее движения и позиций поперечного суппорта управляются узлом распределительного вала 6. Привод рабочих органов станка обеспечивается механизмами и электродвигателем привода, расположенными в станине.
Многошпиндельные автоматы были следствием технического прогресса; их использование снабжает увеличение производительности. У одношпиндельных автоматов (как у револьверных станков) отдельные инструменты револьверной головки последовательно используются для обработки заготовки, и любая из позиций солидную часть времени не употребляется. Этого недочёта не имеют многошпиндельные автоматы, где пара шпинделей (четыре, пять, шесть либо восемь) соединены в блок, и инструменты всех суппортов (по числу шпинделей) трудятся в один момент.
На рис. 30 приведена рабочая территория четырехшпиндельного автомата. Шпиндели вращаются в шпиндельном блоке, и любой шпиндель несет закрепленный пруток.
По окончании каждого перехода шпиндельный блок поворачивается так, что все шпиндели последовательно становятся наоборот суппортов 6,7,8 и 9, и пруток обрабатывается инструментами, закрепленными в этих суппортах.
Рис. 29. Одношпиндельный прутковый автомат
Кроме прутковых автоматов, существуют кроме этого автоматы для обработки штучной заготовки. В этих автоматах заготовки подаются из бункера и особым устройством устанавливаются в шпинделе.
Токарным полуавтоматом именуется станок, трудящийся с автоматическим рабочим циклом, для повторения которого требуется вмешательство рабочего.
Рис. 30. Шпиндельная бабка четырех-шпиндельного автомата
По полуавтоматическому циклу трудятся многорезцовые, револьверные, карусельные, одношпиндельные и многошпиндельные станки. Как и автоматы, эти станки имеют узел распределительного вала.