Термическая обработка миниатюрных изделий
Режим термической обработки миниатюрных изделий устанавливаются каждого вида изделия раздельно, исходя из геометрических размеров, конфигурации, материала, других факторов и необходимой твёрдости. При’нагреве изделий; осей, пуансонов, игл, заготовок сверл, штифтов и т. д. имеет место опасность их сцепления, пережога и“деформации узких частей, появления пятнистой (разнотвердой) структуры при закалке и других нежелательных явлений.
Для увеличения качества термообработки нагрев и загрузку изделий нужно вести не «навалом», а бережно укладывая их на приспособлениях. Нагрев изделий реализовывают в электродных соляных вакуумных печах и в печах с защитной воздухом.
Термическая обработка миниатюрных изделий диаметром до 1 мм есть непростой технологической задачей. Незначительное отклонение от других условий и установленных режимов обработки может привести к неисправимому браку. При нагревании изделия, имеющие ограниченную жесткость в холодном состоянии, покупают повышенную склонность к деформированию под действием случайных нагрузок, из-за охлаждения и неравномерности нагрева.
При термической обработке изделий диаметром менее 0,5 мм нужно шепетильно выполнять выдержки и температуру нагрева, состав ванн закалки, установленную последовательность операций, большую осторожность в обращении с нагретыми изделиями.
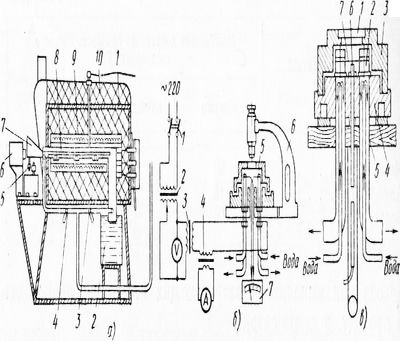
Рис. 1. Малогабаритные печи
Разглядим технологический процесс термической обработки цилиндрических изделий диаметром от 0,1 мм до 1 мм, изготовленных из быстрорежущей стали. Он есть типовым для таких изделий как оси, штифты, пуансоны, иглы, развертки. Технологический процесс включает операции предварительного подогрева заготовок, их нагрев, охлаждение, выварку, промывку, отпуск, контроль и химическую очистку.
Нагрев изделий создают в электродной соляной ванне. Изделия, имеющие температуру окружающего воздуха, загружают в особый совок и подогревают над зеркалом ванны до температуры 600—650 °С. Наряду с этим изделия, подвергаемые нагреву, укладывают последовательностями по 150—250 изделий.
Нагрев цилиндрических изделий пучками либо в особых приспособлениях в вертикальном положении открытыми создавать не рекомендуется ввиду того, что кипящая соль, омывая изделия, неизбежно их изгибает. Совок защищает изделия от потоков соли и предохраняет их от изгиба.
При предварительном подогреве исключается резкое увеличение температуры изделий от тепла, излучаемого зеркалом ванны. По окончании подогрева изделия вместе с совком погружают в расплавленную, соляную ванну и выдерживают в течение одного либо нескольких десятков секунд. Время выдержки зависит от диаметра изделий.
В табл. 28 приведены режимы термической обработки цилиндрических изделий разных диаметров.
В качестве рабочей среды для нагрева изделий применяют хлористый барий. Для исключения обезуглероживания поверхностных слоев изделий в расплавленную соль додают ферросилиций. В нижней территории ванны он разлагает сернокислые соли и образует безводную окись кремния, связывающую окислы железа (каковые играются активную роль в обезуглероживании), в прочные химические соединения, складывающиеся из окиси кремния и трехокиси железа.
В следствии образования этого соединения ванна очищается от негативных составляющих.
Для предотвращения появления на поверхности ванны жёсткой корки нужно иногда додавать буру и ферросилиций. В противном случае образующаяся жёсткая корка может стать обстоятельством изгиба тёплых изделий при извлечении их из ванны.
Электродная соляная ванна для термообработки изделий складывается из цилиндрического корпуса шамотной обмуровки, тигля и внутреннего кожуха с нагревателями. Выделяющие в ходе плавления газы удаляются вытяжной вентиляцией.
По окончании нагрева изделия извлекают из ванны и погружают в закалочную жидкость. От времени переноса из нагревательной до закалочной ванны сильно зависит итог закалки. Для узких изделий это время не должно быть более трех секунд.
В другом случае узкие изделия успевают остыть.
Охлаждение создают в нагретом до 40—50 °С веретенном масле. Не нужно погружать изделия в масло вместе с совком, поскольку от него масло скоро нагревается.
Выверку изделий создают в 10%-ном растворе каустической соды для очистки поверхности от соли. Изделия подвергают двукратному отпуску в особой отпускной печи при температуре 540—550 °С либо трехкратному отпуску в селитровой ванне при 560—580 °С.
При закалке изделий из высокоуглеродистых сталей У10А, У12А нагрев до температуры 800—820 °С создают в соляной ванне, складывающейся из 78% хлористого натрия и 22% хлористого бария. Время выдержки зависит от диаметра изделия. В крупносерийном производстве миниатюрных изделий для термообработки возможно применять индукционный нагрев в защитной среде.
Наряду с этим направляться свести к минимуму охлаждение изделий на воздухе до попадания их в масляную ванну.
Во многих случаях для нагрева употребляются простые камерные печи, оборудованные устройствами для защитной среды и особым лотком, что по окончании окончания нагрева изделий опрокидывается. Наряду с этим изделия падают в закалочную ванну. Для сцепления изделий и предотвращения сплавления в ходе нагрева целесообразно информировать им колебательное перемещение методом установки вибраторов.
Кроме инертных газов в качестве защитной среды используют газ, другие газы и пропан.
Оборудование для термообработки.
На раме печи укреплен Г-образный муфель. Финиш его вертикального ствола опущен в бак с закалочной средой и образует гидравлический затвор. В открытый финиш муфеля вставляют лоток, опирающийся на три шариковых опоры и вибрирующий в продольном направлении под действием пружинного 5 амортизатора и кулачка. К обоим финишам муфеля через краны подводится газ от сети либо баллона. Причем к открытому финишу он подается форсункой.
Муфель обкладывается нагревательными элементами — керамическими плитами с проходящей в спиралью из нихрома и теплоизолирующим материалом.
поддержание и Контроль заданной температуры производятся машинально термопарой и потенциометром. Блок управления смонтирован в виде отдельного шкафа. Перед термической обработкой подробностей (закалкой, отжигом либо отпуском) печь предварительно нагревается до определенной температуры и продувается газом.
Для этого раскрывается газ и кран, поступающий к открытому финишу муфеля через форсунку, поджигается. Газовое пламя регулируют краном так, дабы факел был минимальный, но перекрывал все сечение муфеля. После этого всецело открывают муфель и кран продувают газом в течение 1,5—2 мин, вытесняя воздушное пространство. По окончании продувки кран закрывают.
В следствии внутреннее пространство муфеля заполнено газом и изолировано от попадания воздуха с одной стороны гидравлическим затвором — закалочной средой, а с другой — факелом пламени. Затем печь готова к работе.
Включив вибратор и подобрав нужную скорость перемещения по лотку изделий (т. е. время выдержки), загружают на последний изделия, подлежащие обработке. Пройдя муфель, нагретые до требуемой температуры изделия попадают в закалочную среду. При отжига бак с закалочной средой заменяют коробкой с песком.
Поверхность подробностей до и по окончании термической обработки получается чистая без следов заметного окисления.
В тех случаях, в то время, когда изделия нужно очистить от окалины, их закладывают в древесный коробку, наполненный порошком пемзы и крупными опилками. Ящик хорошо закрывают и устанавливают на приспособление, которое создаёт возвратно-поступательное перемещение со скоростью 800—900 ходов в 60 секунд. Время очистки образовывает 15—30 мин.
В следствии наполнителей и относительного движения изделий производится очистка их поверхности от окалины, окисных плёнок и остатков солей.
Для нагрева, определения и расплавления температуры плавления микродоз разных материалов помогает малогабаритная электропечь, которая складывается из нагревательной печи, микроскопа для наблюдения за процессом, регулирующего трансформатора, приобретающего питание из сети, и понижающего трансформатора.
Сечение катушки низкого напряжения образовывает 450— 500 мм2. Нагревателем фактически печи есть платиновая пластинка толщиной 0,3 мм, зажатая с обеих кондов двумя водоохлаждаемыми токоподводами, изолированными от водоохлаждаемого корпуса втулками из миканита. Печь завинчивают крышкой с окном из молибденового стекла.
Для правильного определения температуры плавления микродозы применяют термопару. Выводы термопары приваривают точечной сваркой к пластинке. Нагреваемую микродозу (пара миллиграммов) кладут на платиновый нагреватель.
Печь закрывают и включают воду для охлаждения корпуса и токоподводов. Посредством трансформатора медлено поднимают температуру, замечая за микродозой через микроскоп. Температуру нагрева микродозы определяют по микровольтметру.
По окончании каждого расплавления микродозы нагреватель очищают. Для очистки от силикатных совокупностей применяют плавиковую кислоту. Потребляемая мощность микропечи 0,5 кВт; время нагрева— 1—2 мин.
При необходимости миниатюрные изделия подвергают цементации как в газовом, так и в жёстком карбюризаторе и в пастах.
Обработка холодом. В производственной практике часто появляется необходимость в проведении работ с обработкой изделий малых размеров глубоким холодом (температурой —60 °С и ниже). Существующие для данной цели установки, применяемые для громадных изделий, очень громоздки и дороги.
Исходя из этого для обработки холодом изделий малых размеров используют малогабаритную холодильную камеру, схема которой приведена на рис. 2. Она складывается из пенопластового контейнера с крышкой, расположенного на столе. В стола размещают 15-литровый сосуд Дюара с жидким азотом.
В сосуд Дюара помещают железную трубку, на финише которой размещена нихромовая спираль, применяемая в качестве подогревателя. В верхней части трубки имеется уплотняющая фторопластовая втулка. Жидкий азот в рабочую камеру поступает через теплоизолирующий поролоновый стакан. На подогреватель подают регулируемое напряжение от автотрансформатора.
Рассеиваемая на подогревателе мощность расходуется на испарение жидкого азота, над поверхностью которого создается давление, выжимающее жидкий азот в рабочую камеру. В последнюю укладывают обрабатываемые изделия. В центре трубки имеются отверстия диаметром 1—1,5 мм, через каковые в трубку попадает газообразный азот.
Необходимость в этом позвана тем событием, что при поддержания в камере температуры порядка —60 °С резкая подача жидкого азота в рабочий количество ведет к большому градиенту температур по высоте камеры и к нежелательному скоплению жидкого азота в ее нижней части. Указанные отверстия содействуют подаче в камеру не жидкого азота, а парожидкостной смеси, что облегчает возможность регулирования температуры в рабочем количестве с точностью ±3 °С.
Рис. 2. Малогабаритная камера для обработки холодом
Изготовление миниатюрных шлифов. В экспериментальной работе часто необходимо изготавливать шлифы из миниатюрных подробностей. Но изготавливать шлифы из них достаточно сложно: их тяжело зажать и удерживать при шлифовании, других видах и полировании обработки.
В большинстве случаев изделие, из которого нужно изготовить шлиф, запрессовывают в легкоплавкий материал, к примеру полистирол.
Запрессовку реализовывают следующим образом. На дно матрицы кладут изделие, из которого нужно изготовить шлиф.
Сверху засыпают полистироловой крошкой с таким расчетом, дабы высота уже готового кубика равнялась 20—25 мм. После этого матрицу устанавливают в нагреватель и в нее вводят термометр до соприкосновения с полистиролом. Нагреватель включают через трансформатор в сеть. Полистирол нагревают до температуры плавления. Затем термометр извлекают, а в матрицу вводят пуансон.
Потом матрицу и пуансон устанавливают под пресс, развивающий давление 60—70 кГс/см2. При таком давлении пресс-форму выдерживают в течение трех мин., по окончании чего упрочнение снимают. Отформованный цилиндр либо кубик с запрессованным изделием извлекают из матрицы.
Потом направляться обработка на шлифовальных и полировальных кругах, травление. Толщина шлифа при таком методе обработки может составлять 0,1 мм.
Имеются установки для изготовления сферических и цилиндрических шлифов из полупроводниковых материалов.
Рис. 3. Приспособление для изготовления миниатюрных шлифов