Ультразвуковая и абразивоструйная обработка
Ультразвуковая обработка содержится в том, что рисунок либо профиль отверстия приобретают в следствии действия абразивного материала на поверхность стекла за счет многократных колебаний рабочего элемента ультразвуковой установки с частотой 20… 25 кГц. Рабочий элемент головки, совершая маленькое по амплитуде перемещение (доли миллиметра) с высокой частотой, ударяет по поверхности стекла, вызывая как бы выкрашивание стекла в обрабатываемой территории.
Основной элемент ультразвуковой установки — вибратор, помещенный в кожух, по которому пропускают проточную воду для охлаждения вибратора. В вибраторе появляются ультразвуковые колебания, каковые передаются механическому трансформатору. На финише трансформатора закреплен рабочий элемент.
Упорный винт как бы регулирует амплитуду колебаний рабочего элемента. Ультразвуковую головку монтируют на механическом направляющем устройстве, которое напоминает сверлильный «танок.
Работа ультразвуковой головки содержится в следящем. Абразивная суспензия подается в промежуток между Рабочим изделием и элементом из стекла. Рабочий элемент вовлекает в возвратно-поступательное перемещение частички абразива, каковые собственными острыми гранями истирают стекло. В следствии скорость продавливания рабочего элемента возрастает. Рабочий элемент действует по принципу пробивания, перемещаясь лишь в вертикальном направлении.
Наряду с этим на поверхности изделия остается след, повторяющий конфигурацию рабочего элемента.
Лучшим абразивным материалом для ультразвуковой обработки есть карбид бора либо алмазный порошок. Абразивный материал используют в виде водной суспензии. Вода содействует обработке ультразвуком, поскольку охлаждает рабочий элемент, что разогревается на протяжении работы.
Установлено, что при ультразвуковой обработке электроэнергия лишь на 70% преобразовывается в ультразвуковую, а на 30%—в тепловую, исходя из этого понижение затрат на тепловые утраты приводит к повышению мощности ультразвуковых колебаний.
Рис. 1. Изображения, наносимые ультразвуковой установкой
Рис. 2. Схема ультразвуковой головки: 1 — упорный винт, 2 — толкающая пластинка, 3 — кожух водяного охлаждения, 4 — вибратор, 5 — трансформатор, 6 — рабочий элемент
Съем материала при ультразвуковой обработке зависит от амплитуды и возрастает с ее возрастанием, но амплитуда колебаний должна быть не меньше 0,02 мм (в большинстве случаев 0,04… 0,10 мм). Этим разъясняется выбор относительно низких частот (17… 50 кГц), что разрешает при меньших мощностях генератора взять достаточную амплитуду колебаний. При тех же параметрах генератора возможно расширить амплитуду колебании, применив концентраторы, финиши которых делают в виде инструментов нужной формы.
Посредством ультразвуковой установки на стекле делают тонкие рисунки и рельефы, подобные чеканным рельефам медалей. Картинки наносят как на плоскую, так и на закругленную поверхность, чем и определяется выбор формы наконечника концентратора. В большинстве случаев размер гравируемого на стекле рельефа не превышает 100 мм.
Особенно действенно использование ультразвука при массовом производстве изделий со сложным рельефным рисунком, к примеру портретными изображениями.
Ультразвуковым методом приобретают такие декоративные украшения, как «стекло в стекле». Для этого в стекле высверливают отверстия и параллельно с этим изготовляют столбики соответствующего диаметра из стекла различных цветов. Столбики вставляются в отверстия и приклеивают бесцветным клеем, к примеру эпоксидной смолой.
После этого изделие обрабатывают разными методами, среди них и абразивными кругами.
Чаще всего ультразвуковые установки применяют при сверлении стекла — отверстие диаметром 14 мм в стекле толщиной 3 мм просверливают за 40 с. Самый целесообразно этим методом сверлить отверстия малых диаметров (десятых и сотых долей миллиметра).
Готовое отверстие имеет легко коническую форму. При сверлении по большей части участвуют абразивные зерна, каковые находятся под передней стенкой сверла. Зерна, находящиеся конкретно около сверла, сглаживают материал и отверстие стенок изделия срабатывается.
Дабы выровнять отверстие, его обрабатывают последовательно набором сверл, незначительно отличающихся друг от друга диаметрами.
Абразивоструйная обработка содержится в том, что слой стекла снимается струей свободного абразивного материала, что подается самотеком либо лопатками вращающегося колеса (в механических установках), потоком жидкости под давлением (в гидравлических) либо газовым потоком (в пневматических). Значительно чаще используют пневматические установки, в которых абразивный материал выбрасывается через сопло сжатым воздухом либо вакуумом.
Абразивоструйную обработку применяли сперва для получения матовой поверхности на плоском листовом стекле, позднее данный вид обработки стали применять при декорировании изделий из стекла: нанесении разных украшений и узоров, надписей знаков, глубинных и рельефных изображений отверстий.
Рис. 3. Схема работы ультразвуковой головки: 1 — рабочий элемент, 2 — абразивная суспензия, 3 — изделие
При абразивоструйной обработке небольшие острограненые час-тицы абразивного материала ударяются с громадной скоростью о поверхность стекла. В месте удара частиц образуются раковино-образные трещины, поверхность стекла разрушается, выкрашиваются осколки. В следствии стекло делается шероховатым матовым, интенсивно рассеивает свет.
На уровень качества абразивоструйной обработки воздействуют вид абразивного материала, скорость струи абразива, ее удаленность от поверхности изделия, количество зерен абразивного материала, падающего на единицу обрабатываемой поверхности, и время обработки. Громадное значение имеют твердость, хрупкость, величина и форма зерна абразивного материала.
Первоначально в качестве абразивного материала применяли кварцевый песок, исходя из этого и обработка именовалась пескоструйной. на данный момент используют карбид и корунд кремния. Корунд жёстче (твердость по шкале Мооса 9) и износоустойчивее, чем песок (твердость 6). Карбид кремния имеет твердость между 9 и 10.
Недочёт этого материала в том, что при сильном ударе его пластинчатые зерна не только очень сильно разрушают поверхность стекла, но и ломаются сами из-за хрупкости. Исходя из этого скоро значительно уменьшается их величина. К тому же остроугольные пластинки карбида кремния легко забивают трубопровод и очень сильно разрушают стены оборудования.
Большая величина зерен абразивного материала не должна быть больше 1 мм. Зерна громадных размеров в потоке абразива имеют соответственно громадную скорость если сравнивать с зернами меньших размеров. В струе абразивного материала меньшие по размерам зерна тормозят громадные и они сталкиваются между собой. Исходя из этого много зерен малого размера замедляет скорость зерен обычной величины, в следствии понижается производительность потока.
Иначе, зерна малых размеров разрушают поверхность стекла стремительнее, чем зерна громадных размеров. Исходя из этого они самый пригодны для матирования стекла, поскольку в этом случае за одно да и то же время у зерен меньшего размера происходит большее число соударений. Для глубинной абразивоструйной обработки, напротив, удачнее трудиться с зернами большего размера, они не смотря на то, что и создают за то же время меньшее число ударов по поверхности стекла, но разрушают его на громадную глубину.
Рис. 4. Схема абразивоструйной обработки поверхности изделия с применением шаблона: 1 — шаблон, 2 — стекло, 3, 5, 6 — зерна летящего абразива, 4 — «мертвая» территория
В случае если часть ровной поверхности стекла прикрыть шаблоном / (рис 100), а открытую часть поверхности обработать струей абразивного материала, то по окончании удаления шаблона на поверхности рисунка образуется матовый рисунок, повторяющий очертания шаблона. Наряду с этим громадное значение имеет размер падающих зерен. Зерно громадного размера соударяется с поверхностью стекла у края шаблона, оставляя наряду с этим через чур громадную по размеру «мертвую» территорию, куда не попадает абразивный материал.
Второе зерно для того чтобы же размера может удариться о край шаблона и отскочить от него на большое расстояние. Все это ведет к тому, что рисунок имеет нечеткие очертания. При применении небольших зерен контрастность изображения увеличивается, поскольку значительно уменьшается размер «мертвой территории».
Для того чтобы получить прекрасно обработанную поверхность с четким рисунком, необходимо применять классифицированный по фракциям абразивный материал.
Энергия перемещения зерен определяется величиной давления либо вакуума и размерами зерен. При повышении скорости потока абразивного материала за единицу времени на одну и ту же площадь попадает большее число зерен. Следовательно, с повышением скорости потока производительность обработки возрастает.
Но скорость не должна увеличиваться так, дабы существенно снизить срок работы применяемого шаблонов и оборудования.
С удалением распыляющего сопла от поверхности изделия конечная скорость потока абразивных частиц быстро понижается, но в этом случае увеличивается однородность обрабатываемой поверхности. Расстояние сопла от обрабатываемой поверхности не должно быть больше 200 мм. При повышении расстояния выше 200 мм уменьшаются утраты стекла при обработке, но однородность обработки поверхности увеличивается.
Исходя из этого при матировании громадных плоскостей рекомендуется пара повышать расстояние между соплом и поверхностью изделия, при глубинной же обработке, напротив, нужно приблизить сопло к поверхности стекла.
Время абразивоструйной обработки выбирают в зависимости от требований, предъявляемых к обрабатываемой поверхности: чтобы получить матовое стекло достаточно пара секунд, глубинная обработка стекла может длиться пара часов.
Пневматические установки для абразивоструйной обработки бывают инжекционные, градиентные и вакуумные.
Инжекционная установка трудится так. Сжатый воздушное пространство по трубопроводу проходит через инжектор, в следствии в смесительной камере создается разрежение. Абразивный материал засасывается по подающему трубопроводу из сборника в смесительную камеру, а после этого сжатым воздухом через сопло направляется на изделие.
Изделие обрабатывают в герметизированной рабочей камере, внутренние стены которой локрыты упругим материалом. Дабы прекратить подачу абразивного материала, трубопровод перекрывают заслонкой. При поступлении многочисленной партии изделий устанавливают две рабочие камеры: до тех пор пока в одной меняют изделие, в второй — обрабатывают.
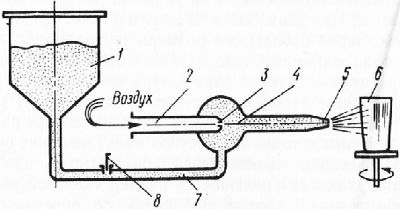
Рис. 5. Схема работы инжекционной абразивоструйной установки: 1 — сборник, 2, 7 — трубопроводы, 3 — инжектор, 4 — смесительная камера, 5 —сопло, 6 — изделие, 8 — заслонка
Рис. 6. Схема работы градиентной абразивоструйной установки: 1 — сито, 2,4 — камеры, 3 — закрывающий вентиль, 5 — регулировочный вентиль, 6 — сопло, 7 — инжектор, 8 — трубы
Градиентная установка (трудящаяся под давлением) (рис. 6) трудится так. Абразивный порошок, загруженный в камеру, давит на закрывающий вентиль.
Вентиль снабжен тужиной и регулирует давление в камере. Воздушное пространство под давлением проходит через трубу, которая поделена на две ветви: первая в камеру, вторая —через инжектор под камеру для транспортирования абразива к соплу. При заполнении камеры абразивным порошком заканчивается доступ сжатого воздуха.
При давлении абразива в сборнике вентиль раскрывается и абразив подает в камеру. Под действием пружины, а после этого избытка давления воздуха в камере вентиль опять закрывается.
К недочётам данной схемы относится цикличность технологического процесса и проникновение части песка из камеры опять в сборник. Чтобы сделать работу установки постоянной, увеличивают число камер, устанавливают переходные трубопроводы и дополнительные вентили.
Вакуумные установки самый обширно применяют для обработки изделий массового производства. Установка монтируется на железном столе, в котором сделаны прорези для движения дозаторов, и прорези для прохода отводов вакуумных головок. В большинстве случаев, на столе устанавливают три вакуумные головки, каковые по направляющим смогут выполнять возвратно-поступательное перемещение при смене изделия.
По салазкам перемещаются направляющие втулки, Все это облегчает перемещение вакуумных головок по окружности.
В вакуумной головке дозатор с абразивным материалом прикреплен к горловине в форме раструба. Вакуумная камера соединена гайкой с вакуумным насосом. При открывании вакуумного клапана в камере создается абразив и разрежение из дозатора по направляющей магистрали устремляется к соплу.
Крышка снабжает плотное прилегание вакуумной головки к изделию и полную герметизацию рабочего пространства.
Установка трудится следующим образом. Изделие устанавливают в центрующее гнездо. При слабом нажатии на изделие планка гнезда включает электродвигатель, что подводит головки к изделию. В то время, когда головки подходят к изделию, электродвигатель отключается и одновременно с этим включается реле времени. Сейчас абразивный порошок начинает подаваться самотеком из дозатора через совмещенные перфорированные решетки в направляющую решетку.
Тут же приводится в воздействие совокупность, управляющая вакуумным клапаном. Наряду с этим в камере создается разрежение и в направляющие поступает воздушное пространство. Поток воздуха подхватывает частицы абразива, что, вырываясь из сопла, причиняет рисунок на изделие в соответствии с приложенным шаблоном.
Потом частицы абразива уносятся через вакуумные отводы в камеры для очистки воздуха. Длительность обработки регулируется реле времени. По окончании обработки реле срабатывает и закрывает вакуумный клапан.
Сейчас электродвигатель отводит головки в крайнее положение, перфорированные решетки перекрывают подача песка и друг друга заканчивается. Рабочий меняет изделие, и цикл обработки повторяется.
Рис. 7. Вакуумная абразиво-струйная установка (а) и вакуумная головка (б): 1 — дозатор, 2 — направляющая головки, 3, 4 — прорези, 5 — салазки, 6 — изделие, 7 — вакуумная головка, 8 — стол, 9 — направляющие втулки, 10 — камера, 11— крышка, 12 — сопло, 13 — клапан, 14 — соединительная гайка
Рис. 8. Организация рабочего места при абразивоструйной обработке изделий: 1 — воздушная магистраль, 2 — бункер с песком, 3 — распыляющее сопло, 4 —вытяжная вентиляция, 5 — рабочая камера, 6 — обрабатываемое изделие, 7— вращающаяся подставка, 8 — сборник отработанного песка
В большинстве случаев при абразивоструйной обработке в пневматических установках создают рабочее давление воздуха 0,2 …0,4 МПа либо разрежение 0,08… 0,09 МПа.
Абразивный материал, подаваемый пневматической установкой, распыляется соплом 3. Сопло изготовляют из жёстких износостойких материалов. В качестве сопл применяют кроме этого сменные вкладыши из победита, карбида бора либо карбида вольфрама. Срок работы вкладыша из карбида вольфрама в 200…250 раза больше, чем сопл из жёсткого чугуна.
Диаметр и длину сопла выбирают в зависимости от характера обработки (нанесение рисунка, целое матирование), раз-iepa обрабатываемого изделия, используемого абразива, давления под которым воздушное пространство поступает в абразивоструйный аппарат. В большинстве случаев для нанесения рисунка применяют круглые сопла диаметром 6… 15, длиной 100… 120 мм, для целого матирования щелевидные.
При обработке щелевидными соплами всей поверхности изделия его закрепляют на резиновом конусе и надевают на вал, на котором оно вращается около собственной оси перед соплом. Со своей стороны, сопло перемещается вверх и вниз так что изделие равномерно обрабатывается по всей поверхности.
На протяжении обработки сопло располагают перпендикулярно стенке обрабатываемого изделия.
Шаблоны для нанесения картинок изготовляют из эластичных, упругих абразивостойких материалов, таких, как мягкие металлы, каучук, резина, пластмасса, клеевые мастики, проклеенная бумага.
Для защитного материала и шаблонов приготовляют клеевую мастику следующего состава (мае. ч.): столярный клей—2,5; глицерин (плотностью 1,2 г/см) — 1,35; молотый мел—1,05.
Перед нанесением мастики изделие протирают, сушат. Мастику наносят широкой кистью в одном направлении. По окончании застывания первого слоя накладывают второй и третий слои; толщина покрытия зависит от глубины делаемого рисунка.
Главным условием, которое нужно выполнять при нанесении покрытия, пребывает в том, что слой мастики не должен содержать пузырьков воздуха.
По окончании того как все слои мастики совсем остановятся, на ее поверхность мягким карандашом либо пером наносят рисунок, что после этого вырезают острым ножом, и удаляют те участки мастики, под которыми стекло должно быть подвергнуто обработке. Дабы поверхность оставшейся мастики не была липкой, ее припудривают мелом, тальком либо магнезией.