Уводы при глубоком сверлении
Уводы либо отклонения осей отверстий от требуемого направления во многих случаях приводят к браку обрабатываемых заготовок. От величины нормируемых уводов при сверлении зависят размеры припусков на обработку подробностей типа пустотелых валов и труб. Потому, что подробности с глубокими отверстиями достигают больших размеров, брак от уводов может привести к громадным утратам в производстве.
Обнаружением обстоятельств происхождения уводов занимались многие исследователи.
Согласно точки зрения этих исследователей происхождение уводов разъясняется следующими обстоятельствами:
1) несовершенством конструкции инструмента, его режущих и направляющих элементов;
2) несоответствием оборудования обрабатываемым заготовкам;
3) неправильным направлением инструмента в начале сверления;
4) неоднородностью материала обрабатываемого изделия;
5) трудностью удаления стружки из территории резания;
6) неудачно выбранными режимами резания при сверлении;
7) продольной неустойчивостью стебля в ходе сверления;
8) неудовлетворительным качеством заточки сверл;
9) нерациональной разработкой глубокого сверления и др.
Ни одна из перечисленных выше обстоятельств уводов не была достаточно теоретически обоснована и экспериментально подтверждена, а отсутствие повторяемости экспериментальных результатов заставляло настороженно доходить к бессчётным рекомендациям по борьбе с уводами.
Из всех перечисленных выше обстоятельств самые вероятными представлялись следующие из них.
Эта формула есть, по-видимому, пока единственной, показывающей на влияение одной из черт обрабатываемого материала на увод оси отверстия при глубоком сверлении. Но и она не согласуется с практикой сверления. Так, к примеру, увидено, что при сверлении термически обработанных заготовок, имеющих повышенную твердость, уводы меньше, чем у отожженных либо нормализованных заготовок.
Остальные вышеприведенные обстоятельства уводов являются неопределяющими, поскольку при неизменности этих обстоятельств величина уводов осей отверстий колеблется в широких пределах. Вместе с тем ознакомление с ними давало основание предполагать, что уводы зависят от каких-то случайных обстоятельств, или не всегда проявляющихся, или не неизменно существующих.
Анализ обстоятельств уводов. Разработке методики изучения обстоятельств уводов предшествовал анализ случаев брака по уводам на производстве. Ознакомление с браком проводилось конкретно на рабочих местах, что давало возможность детально выяснять условия обработки. Заготовки измерялись, определялась твердость материала в нескольких местах по длине и в разных сечениях. Твердость определялась посредством прибора Польди.
Но случаи брака по уводам были нечасты и, в большинстве случаев, единичны. Появлявшиеся при сверлении уводы не превышали в большинстве случаев величины равной 2/3 допуска. Прободение (выход инструмента при громадном уводе не в выходной торец, а в бок заготовки) заготовок за всю собственную практику автору встретилось лишь четыре раза.
Уводы определялись у трех подробностей, вышедших в брак по уводам на одном из фабрик. Заготовки имели громадную относительную длину (6Z = 84) и круговую цилиндрическую форму. На наружных поверхностях заготовок было нанесено по одной контрольной риске параллельно образующим.
После этого они были размечены и разрезаны на 10 частей любая. Измеренные размеры уводов их расположение и Ус по сечениям заготовок (
Из графиков, приведенных на рисунке, возможно сделать следующие выводы.
1. У всех трех заготовок (штоки 1, 2, 3) самоё интенсивное смещение плоскости громаднейшего увода отмечается на входных частях; в будущем это смещение (приращение ср) заметно сни-жается.
2. Приращение величины уводов АУ не остается постоянным (особенно в начальной стадии сверления); на отдельных участках это приращение равняется нулю.
3. Настоящие оси отверстий не прямые линии, а пространственные кривые (ф = const).
4. Нет строгой закономерности в трансформации размеров уводов и в их пространственном размещении, а следовательно, не существует однозначной зависимости уводов от начального направления сверла, поскольку не соблюдаются условия: ф = const.
Так, разглядываемые случаи уводов у трех просверленных подробностей не подтвердили положения, выдвинутого И. С. Веремейчуком.
Все эти сведенья показывают на то, что обстоятельство, которая отклоняет сверло на разных участках сверления, существует. Так, к примеру, из графика видно, что приращение увода на всем пути инструмента было неравномерным. Сначала увод скоро возрастал (1-2-й участки пути), после этого его величина стабилизовалась (3-4-й участки), после этого снова росла (5-6-й участки) и, наконец, на 7-9-м участках стала постоянной.
Наряду с этим увод, не меняя величины, менял собственный относительное положение по отношению к принятой нами начальной плоскости, совершённой через ось заготовки. Создавалось чувство, что при глубоком сверлении сверло, не имея твёрдого крепления, все время испытывает действия сил, талантливых поменять направление его пути. Раскрыть эти силы и их природу означало отыскать главную причину, вызывающую явление увода осей просверленных отверстий.
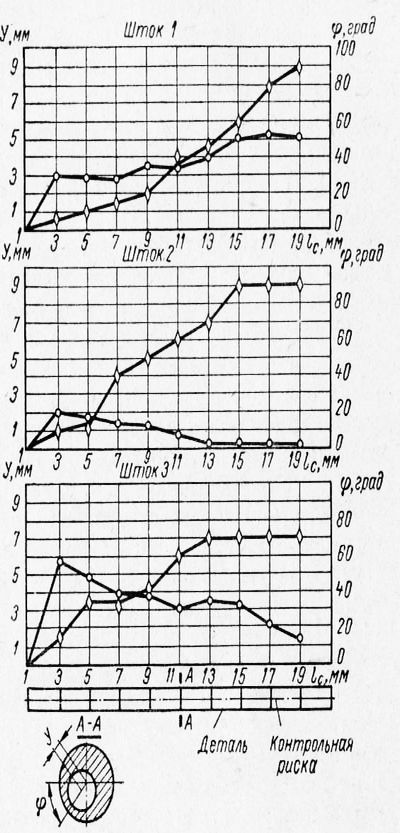
Рис. 1. их расположение и Уводы по сечениям заготовки при сверлении штоков
Из практики сверления прекрасно известен факт трансформации характера стружкообразования на отдельных участках пути сверла в заготовке. Не редкость так, что в начальной стадии сверления образуется небольшая стружка, прекрасно вымываемая охлаждающей жидкостью из территории резания, а после этого наступает момент, в то время, когда стружка начинает виться. В этом случае может случиться нарушение стружкоотвода и поломка инструмента. Но еще перед тем, как оператор примет меры, стружка снова начинает прекрасно дробиться.
Обстоятельством трансформации характера стружкообразования, в большинстве случаев, есть неравномерность особенностей материала по длине заготовки.
Кроме этого прекрасно известен факт, в то время, когда при обточке разные части заготовки обрабатываются неодинаково: одна сторона получается ровной и блестящей, вторая — матовой с повышенной шероховатостью. В этом случае стружка на отдельных участках длины имеет разные оттенки. Проверка твердости таковой заготовки подтверждает тот факт, что она неодинакова, т.е. заготовка имеет «поперечную раз-нотвердость».
Наконец, существуют определенные соотношения между их пределами и твёрдостью материалов прочности по длине заготовки, и как мы знаем, что чем больше предел прочности на твёрдость и растяжение ав НИ, тем больше должны быть силы резания.
Из заготовки каждого штока было произведено по 11 шлифов. Рассмотрение микрошлифов поперечных сечений подтвердило существование структурной неоднородности материала. Эта структурная неоднородность зависела от характера формирования заготовок и их тепловой обработки. Поперечная разнотвердость, например, имела возможность происходить и из-за неодинаковой по сечению прокаливае-мости заготовок.
Прокалимаемость — глубина проникновения закалки — зависит от легирующих элементов сплава, величины зерна, температуры закалки и размеров детали и др. К примеру, простые углеродистые стали, обширно используемые в машиностроении, не всегда дают прекрасные результаты при термообработке как по особенностям, так и по однородности.
Распределение твердости материала по сечению в большинстве случаев симметрично относительно оси заготовки. Представим себе, что сверло любой конструкции образует отверстие симметричное относительно оси заготовки. В этом случае режущие кромки и направляющие сверла, вращаясь относительно заготовки, будут встречать сопротивление срезаемого материала, свойства которого симметричны относительно оси сверла.
Разумеется, что в этом случае не будет существовать обстоятельств (сил), каковые имели возможность бы отклонить сверло от принятого им направления. Но кроме того при самой тщательной термической обработке совершенной симметрии особенностей взять запрещено.
Исходя из этого возможно высказать предположение, что кривые распределения твердости материала заготовки смогут быть расположены асимметрично и иметь в качестве оси не прямую, а пространственно расположенную кривую. Возможно кроме этого высказать предположение, что сверло при врезании в заготовку не всегда направлено по оси симметрии особенностей материала.
На рис. 2 представлены варианты разных положений сверла в заготовке при наличии поперечной различно-твердости.
Из рис. 2, а видно, что обе кромки сверла испытывают при сверлении симметричную относительно оси инструмента нагрузку Р. Сил, побуждающих сверло поменять собственный направление, в этом случае, разумеется, нет.
На рис. 2, б ось сверла не сходится с осью симметрии разнотвердости заготовки. Смещение е приводит к загрузке левой режущей кромки громадными силами сопротивления при сверлении, чем загружена сейчас правая кромка сверла.
В этом случае составляющие поперечных сил Р” не равны и разность между ними ДРу, разумеется, и будет той силой (обстоятельством), которая может побудить сверло поменять собственный направление в заготовке.
На рис. 2, в продемонстрирован один из вероятных вариантов сверления, в то время, когда сверло направлено под углом а к оси заготовки, имеющей поперечную разнотвердость, расположенную симметрично довольно геометрической оси. В этом случае, как видно из рисунка, кроме этого существует сила, которая обязана поменять направление сверла.
Причем это изменение направлено на совмещении осей сверла с заготовкой (с осью симметрии разнотвердости).
Это случай ставит под сомнение утверждение И. С. Веремейчука о том, что при наличии в начальный момент сверления угла между осями инструмента и заготовки увод будет возрастать. В разглядываемом случае, напротив, существование поперечной разнотвердости должно привести к уменьшению увода и к совмещению заготовки и осей сверла. Так делается светло, из-за чего сверло, просверливая во многих случаях весьма глубокое (6/100), отверстие в заготовке, имеет очень незначительный увод.
Рис. 2. Варианты разных положений сверла в заготовке при наличии поперечной разнотвердости: а — ось сверла сходится с осью симметрии разнотвердости; б — ось сверла не сходится с осью симметрии разнотвердости; в-ось сверла направлена под углом к оси симметрии поперечной разнотвердости
Из рассмотренных вариантов сверления возможно сделать вывод, что не всегда существуют обстоятельства увода осей отверстия. К примеру, при, приведенном на рис. 2, а, при существовании поперечной разнотвердости нет условий для увода сверла, поскольку ось симметрии и ось сверла разнотвердости заготовок совпадают.
Возможно допустить, что в случае если диаметр термообработанной заготовки равен либо меньше критического диаметра DKpx, то кроме этого не будет существовать сила АРу, которая может поменять направление инструмента относительно заготовки, в случае если ось сверла сейчас сходится с осью вращения подробности. Возможно высказать предположение, что наличие продольной разнотвердости, т.е. распределения твердости материала в сечениях на различных участках длины заготовки, не будет приводить к силы АРу, в случае если поперечная разнотвердость наряду с этим будет размешаться симметрично оси сверла. В этом случае отсутствие силы АРу не приведёт к сверла от принятого направления.
Самым серьёзным выводом из рассмотренных вариантов распределения разнотвердости относительно осей заготовок и инструмента есть обнаружение настоящей силы, талантливой изменять направление пути сверла в заготовке. направляться иметь в виду, что наряду с этим нужно иметь упругие сверла либо упругие обрабатываемые материалы, поскольку существование одной поперечной силы еще не обусловливает происхождение уводов.
Поперечная сила, в большинстве случаев, неизменно обязана уравновешиваться реакциями базисных направляющих инструмента. Ниже эта идея будет детально проиллюстрирована примером построения элементарного увода.
Без громадной погрешности возможно разглядывать варианты относительного размещения сверла и поперечной разнообрабатывае-мости, пренебрегая законом загрузки режущих кромок сверл, зависящих от скорости резания.
Для облегчения анализа механизма происхождения уводов совершим графическое построение величины элементарного увода. Допустим, что сверление производится однокромочным сверлом, продемонстрированным на рис. 65, а.
Суммарные отклонения калибрующей оси и кромки сверла представлены на рис. 3, г.
Рис. 3. Анализ происхождения увода: а — однорезцовое сверло; б, в, г. — схемы построения соответственно деформации сверла, деформации материала, суммарных деформаций
Из рисунка видно, что отклонение оси инструмента под действием сил резания происходит благодаря податливости как сверла, так и обрабатываемого материала. Причем, в последнем случае внедрение направляющих элементов сверла (alt а2 и blt b2), разумеется, будет зависеть не только от действующих на инструмент сил Рг и Ру, но и от величины площади рабочих поверхностей направляющих (Fu F2) и твердости обрабатываемого материала.
Для упрощения построения величины элементарного увода примем три случая распределения твердости материала в поперечных сечениях заготовки:
1) заготовка имеет однообразную твердость (вариант I);
2) добрая половина заготовки имеет высокую твердость, а вторая добрая половина — низкую (вариант II);
3) распределение твердости по сечению подчиняется закону эксцентриситета (вариант III).
Будем кроме этого считать, что силы сопротивления давлению Р, действующие на сверло, пропорциональны твердости Н обрабатываемого материала, а глубина вдавливания направляющих сверла в деформации и заготовку инструмента пропорциональны действию сил.
Задаваясь масштабами деформаций и сил инструмента и обрабатываемого материала заготовок, выстроим для 16 положений (точки 1 -16) инструмента (довольно обрабатываемой заготовки) элементарные уводы осей отверстий при упругом инструменте, упругом обрабатываемом материале заготовок и суммарные элементарные уводы.
Графическое построение элементарных уводов разрешает сделать следующие выводы.
1. При отсутствии в зоне резания в поперечном сечении заготовки асимметрично расположенных по отношению оси сверла поперечной разнообрабатываемости и поперечной разнотвердости обрабатываемого материала элементарных уводов не образуется.
2. При наличии поперечной разнообрабатываемости и разнотвердости, асимметрично расположенных относительно оси сверла, элементарные уводы образуются.
3. Направление элементарных уводов идет в сторону лучшей обрабатываемости (меньшей твердости).
4. Большой элементарный увод расположен под некоторым углом к оси симметрии размещения твердости в поперечном сечении заготовки. Направление большого увода (ф) зависит кроме этого от упругости инструмента. Так, к примеру, при полностью твёрдом инструменте большой элементарный увод при закономерности распределения АРу по варианту II находится слева, а при упругом — справа от оси симметрии. Следовательно, направление и величина уводов смогут зависеть и от жесткости корпусов инструментов;
5. При уводе должно быть искажение макроформы поперечных сечений отверстий (рис. 66, г. варианты II и III). Это есть подтверждением необычного копирования разнотвердости (и разнообрабатываемости), не обращая внимания на то, что при операции сверления расчетная величина припуска, срезаемого инструментом, сохраняется постоянной.
Рис. 4. Распределение поперечной разнообрабатываемости (а) и построение элементарных уводов отверстий при упругом обрабатываемом материале (б), при упругом инструменте (в) и суммарные деформации при инструменте и упругом материале (г)
Методика проведения опытов. Изучение работ разных исследователей, накопление опыта по глубокому сверлению и совершённый анализ обстоятельств увода осей отверстий говорят о том, что получение надежных результатов при проведении опытов сильно зависит от выбранной методики изучения. Основной вопрос методики: как обеспечить контроль материала заготовок, поступающих на сверление.
В предшествующих работах по уводам этому вопросу не было уделено достаточного внимания, что стало причиной громадному рассеиванию умелых данных, а во многих случаях и к ошибочным выводам. Большую сложность воображает в этом отношении выбор опытных образцов для глубокого сверления. До сих пор не существует несложного и надежного способа определения механических особенностей материала в образцов без их разрушения.
Попытки изготовить опытные образцы для сверления с получением в поперечных сечениях требуемой поперечной разнотвердости (и разнообрабатываемости) посредством термообработки не дали желаемых результатов. Резать заготовки по окончании сверления и измерять их твердость либо обрабатываемость не только тяжело, но и не совсем верно, поскольку материал заготовок, что влияет на поведение инструмента, высверливается в ходе сверления, преобразовываясь в стружку.
Измерять обрабатываемость и твёрдость материала на наружной поверхности, в особенности при сверлении заготовок из углеродных и низколегированных сталей диаметром выше 50 мм, было бы неправильно. Исходя из этого было нужно пойти по пути созадния составных образцов, каковые воображали полосовой материал, стыкуемых по диаметральной плоскости. Такие образцы позволили осуществлять контроль твердость внутренней части заготовки до сверления.
Имея маленькое сечение (толщину), они снабжали кроме этого удовлетворительную однородность материала. По окончании контроля твердости материала образцы соединялись попарно сваркой, центрировались по стыку, обтачивались с финишей и проходили заправку до диаметра da под заход инструмента.
Принятые с целью проведения опытов образцы владели следующими преимуществами:
1) разрешали осуществлять разные комбинации материалов заготовки впредь до сопряжений материалов с разным трансформацией особенностей;
2) чтобы получить уводы большой величины не требовалось создавать сверления весьма долгих, а следовательно, и весьма дорогих образцов (заготовок); в отечественных опытах протяженность заготовок равнялась приблизительно 164, а испытания проводились в основном при сверлении отверстий диаметром dc = 80 мм;
3) работа инструмента проходила в определенной среде, что принципиально важно для раскрытия влияния материала заготовки на уводы;
4) содействующая уводам среда создавала условия минимального разброса умелых данных.
На первый взгляд может показаться, что составные образцы использовать не нужно, поскольку на практике аналогичных случаев не видится. Но в опытах по обнаружению обстоятельств уводов и, например, по обнаружению влияния поперечной разнотвердости и разнообрабатываемости, нужно быть не только уверенным, но иметь неизменно возможность проверить, какой материал подвергается обработке. Помимо этого, при этих примерах возможно обеспечить широкий диапазон трансформаций изучаемой величины.
В этом отношении составные образцы позволяют совершить широкий круг работ при относительно маленьких затратах и основное с получением надежных и легко повторимых результатов.
Проверив эту методику в работе, мы взяли уверенность в том, что она возможно применена и для других изучений в области резания и технологии материалов. Так, к примеру, ее возможно советовать при изучении обрабатываемости разных материалов. В случае если составить заготовку из разных (двух, трех и т. п.) материалов и совершить динамометрирование, то осциллограмма даст ответ, какой из материалов и при какой геометрии инструмента обрабатывается хуже либо лучше.
Причем сокровище этих опытов содержится в том, что тут все факторы, каковые смогут оказывать влияние на изучаемое явление, остаются постоянными, не считая одного, в этом случае материала. Фактор времени, время от времени вносящий громадные погрешности в опыты, тут устранен.
Испытания по уводам. Сперва были совершены пробные испытания сверления составных заготовок с разными разнотвердостью и различно-обрабатываемостью на одном режиме обработки.
На рис. 5 продемонстрированы примеры уводов отверстий у двух опытных образцов с разными разнотвердостями, каковые условно представлены пропорциональными толщинам стенок заготовок (00 — линия вращения разъёма и ось детали заготовки). Как видно из рисунка, разнотвердость АН и увод УС1 и примера 1 больше, чем у примера 2 ( УС2).
В этом случае величины уводов не являются большими, поскольку промеры уводов производились не в плоскости, задаваемой углом ф (плоскость больших уводов см. на рис. 4), а по верхней и нижней образующим просверленного отверстия. Уводы направлены в сторону меньшей твердости материала образцов, что подтверждает выводы, сделанные при анализе построения и причин уводов элементарных уводов. Характерным тут есть кроме этого некое уширение входного отверстия у опытного образца.
В будущем это уширение провалилось сквозь землю, но диаметр просверленного отверстия имел на всей протяженности колебания в малых пределах.
Рис. 5. Примеры уводов отверстий при наличии поперечной разнообрабатываемости:
Приведенные мысли потребовали проверки, поскольку при их справедливости возможно было бы вычислять доказанным, что метод сверления воздействует на увоДы и существует влияние гироскопиЧё-ского результата на направление инструмента при сверлении. Последнее предположение было заманчиво тем, что если бы имело место при сверлении правило Фуко, то в возможности было бы возможно безуводное сверление с применением заготовки и попутного вращения инструмента для одноименного параллелизма.
Как видно из таблицы, испытания не подтвердили заметного влияния на уводы трансформации соотношений угловых скоростей и инструмента вращений и направления заготовок. При существующих режимах обработки не найдено кроме этого влияние одноименного параллелизма, а некое понижение размеров уводов возможно растолковано меньшей в этих обстоятельствах поперечной разнотвердостью (04,5/5 вместо 0 4,2/5 мм).
Сверление неподвижных составных заготовок (сталь 40Х + сталь 25) было совершено на следующем режиме: vc = 44 м/мин; dc = 80 мм; по = 175 об/мин; п3 = 0; s0 = 0,17 мм!об. Наряду с этим взяты уводы, равные 6,48 и 6,76 мм. Эти величины уводов, как будет продемонстрировано дальше (см. рис.
70), являются обычными для данной скорости сверления.
Так, и эти испытания говорят о отсутствии заметного (определяющего) влияния на уводы соотношения угловых инструмента вращения и скоростей изделия. Полученные результаты согласуются с отечественной и зарубежной [50] практикой сверления без движений закрепленных заготовок.
Из взятых выше разрешённых можно сделать вывод о том, что величина увода не зависит от того, будет либо нет вращаться заготовка при сверлении. Исходя из этого разглядим работу вращающегося сверла при врезании его во входной торец неподвижной заготовки. Наряду с этим сверло будет перемещаться в направлении, задаваемом ему направляющей втулкой.
В случае если поперечная разнотвердость материала заготовки отсутствует, то сил, каковые имели возможность корректировать направление инструмента, по всей видимости, не будет. Разглядим потом случай врезания вращающегося (без дисбаланса) либо невра-щающегося сверла во вращающуюся заготовку при наличии несовпадения сверла вращения и осей заготовки. В принятых условиях получается, строго говоря, не сверление, а растачивание в целом материале на маленькую глубину.
Наряду с этим растачивании между заготовкой и инструментом постоянно будет образовываться зазор. Образующаяся сила сопротивления резанию, среди них и радиальная ее составляющая Ру, может в этих условиях восприниматься лишь стеблем, а не направляющими сверла. Сила Ру будет стремиться совместить ось сверла с осью вращения заготовки, а жесткость стебля благодаря повышения его выдвижения быстро значительно уменьшается.
В то время, когда ось инструмента совместится с осью вращающейся заготовки, вступят в работу направляющие сверла.
Из этого примера делается ясно, что вращение заготовки может корректировать начальное направление инструмента, которое он имеет при врезании. Частичное уширение отверстий, приобретаемое при врезании инструмента в заготовку, кроме этого подтверждает данный вывод.
При сверлении заготовок громадной относительной длины бывают случаи, в то время, когда они имеют громадное провисание. Промежуточные люнеты не всегда выбирают стрелу изгиба, а в некоторых случаях создают дополнительные перегибы оси обрабатываемой подробности. Но стрелы прогиба fm заготовок в этом случае становятся существенно меньшими.
Из рисунка видно, что если бы сверло перемещалосьна протяжении линии центров станка, то в этом случае оно перешло бы от режима сверления на режим растачивания. Выше было обнаружено, что при вращении заготовки радиальная составляющая силы сопротивления резанию откорректирует направление сверла и совместит его ось с настоящей осью вращения заготовки. В случае если заготовка при сверлении не вращается, то, разумеется, сверло сохранит собственный начальное направление (при АН = 0), так как появляющаяся сила ру будет уравновешиваться направляющими инструмента и на протяжении полного оборота сверла постоянна.
В конечном итоге, при громадных уводах отверстий (АН0) сверло отходит от оси вращения заготовки. Это делается вероятным благодаря малой жесткости стебля и большего, чем корректирующая свойство вращения заготовки, влияния разнотвердости (наряду с этим стебель начинает заметно «водить»).
Рис. 6. Установка долгой заготовки для сверления: а — без промежуточного люнета; б — с промежуточным люнетом; в — сверла и продольное сечение заготовки
Рассмотрение двух случаев работы сверл как при врезании инструмента, так и при наличии непрямолинейной оси вращения заготовки показывает следующее:
1) условия работы сверла при вращающейся и неподвижной заготовках неодинаковы;
2) при происхождении рассогласования в направлении сверла и осей заготовки при вращающейся заготовке происходит автоматическая коррекция направления сверла; в случае если заготовка не вращается, то у нее настоящая ось вращения отсутствует и никакой коррекции не происходит;
3) минимальный увод отмечается при симметричной относительно оси вращения заготовки поперечной разнотвердости и разнообрабатываемости и при вращении заготовки.
Практика сверления говорит о том, что наиболее способна изменять направление инструмента поперечная разнотвердость (разнообрабатываемость) но не всегда в желаемом направлении. В этом случае получается не корректировка, а увод.
Контроль кривизны, совершённый посредством нивелира и оптической марки, продемонстрировал, что у составных образцов большие уводы в отдельных поперечных сечениях находятся в узком секторе. Существование малых отклонений в размещении больших уводов возможно растолковать некоей неизбежной неоднородностью материала кроме того у составных заготовок. Результаты опытов дают основание вычислять, что большие уводы в сечениях заготовок находятся фактически в одной плоскости.
При определении влияния на уводы начальной угловой погрешности в направлении сверла составные образцы имели заправочные отверстия на входных финишах, расположенные под разными углами а, — к теоретическим осям заготовок. Были опробованы два варианта направления заправки: на жёсткий и на мягкий материалы составных образцов. При проведении этих опытов наблюдались случаи исправления заданного направления оси заправочного отверстия сначала сверления.
Исходя из этого громадного угла наклона а0 не было возможности взять. Итог сверления составных образцов при направлении оси заправочного отверстия на жёсткий материал приведен на рис. 7.
Испытания продемонстрировали следующее:
1) при наличии поперечной разнотвердости сверло значительно изменяет собственный направление, не обращая внимания на придание ему в начале сверления противоположного действию силы Ру направления;
2) при сверлении разнотвердых образцов с заправочным отверстием, направленным на мягкий материал, уводы по величине получаются больше простых.
Для обнаружения влияния скорости резания на уводы были просверлены составные заготовки из сталей 40Х, 25, 50 и 20 при разных скоростях резания. Скорость сверла изменилась от 5 до 210 м/мин при постоянной подаче s0 = = 0,17 мм/об. В опытах использовались однокромочные сверла диаметром dc — 80 мм.
До скоростей резания из “ 50 м/мин — твеолый сплав маоки Т15К6.
На рис. 8 продемонстрированы величины уводов, полученные при сверлении составной заготовки из сталей 40Х и 25, при разных скоростях (кривая 2) и подачах (кривая /).
Как видно из рисунка, скорость резания значительно влияет на уводы: при повышении скорости резания уводы быстро снижаются.
Рис. 7. Результаты сверления заготовки с поперечной разнообра-батываемостью и начальной угловой погрешностью направления инструмента: а — кривизна по вертикали; б-кривизна по горизонтали; в — суммарная кривизна
Это событие очень весьма интересно вследствие того что возможно применено как главная совет борьбы с уводами. Сокровище ее содержится и в том, что при увеличении скорости резания не только уменьшаются уводы, но и обязана расти производительность сверления. До этого, трудясь на скоростных режимах, мы предполагали, что приобретаемые незначительные уводы определяются по большей части не скоростью резания, а качеством используемых инструментов.
Оставалась неясной обстоятельство падения уводов с возрастанием скорости резания при сверлении заготовок с поперечной разнотвердостью, тем более что в прошлых опытах не удалось распознать заметного влияния на уводы гироскопического результата. Для установления обстоятельства понижения размеров уводов при возрастании скорости резания было совершено динамометрирование.
Для этого на токарном станке были обточены составные заготовки, каковые до этого сверлились в опытах по обнаружению влияния скорости резания на уводы. Резец, использовавшийся при обточке, был закреплен в токарном динамометре с проволочными датчиками сопротивления. Тангенциальные силы резания Рг замерялись и записывались посредством тензостанции (35 кгц) и осциллографа МПО-2.
Рис. 8. Зависимость уводов оси сверла от скорости резания и вели чины подачи при сверлении:
Рис. 9. Заготовки с разиообрабатываемостью, просверленные при разных скоростях резания
Обработка составных образцов дает наглядное представление 0 том, что по мере возрастания скорости резания быстро снижается разность между обрабатываемостью стали 50 и стали 20. Подобная нивелировка обрабатываемости разных материалов наблюдалась нами и раньше при сверлении составных заготовок из сталей 35 и ОХИЗМА при скоростях сверления vc 5» 150 м/мин.
Факт уменьшения поперечной разнообрабатываемости (нивелирования обрабатываемости, но не твердости) дает основание сделать
Рис. 10. Осциллограммы и графики трансформации сил, замеренных при разных скоростях резания на протяжении обточки заготовки из составного примера
следующий ответственный вывод. В случае если главной причиной уводов есть наличие поперечной разнообрабатываемости заготовок, а поперечная разнообрабатываемость значительно уменьшается с возрастанием скорости резания, то возможно высказать предположение, что на высоких скоростях резания возможно проводить глубокое сверление фактически без уводов:
Опытами установлено кроме этого, что при повышении подачи на протяжении сверления величина уводов имеет тенденцию к возрастанию. Это положение возможно растолковать повышением отклонения инструментов при наличии и увеличении подачи поперечной разнообрабатываемости. Но чем больше подача, тем меньше число отжимов инструмента.
Были совершены испытания, определяющие влияние конструктивной схемы сверл на уводы при сверлении. Конструирование сверл,
Пригодных для производительного сверления, упорно приводило к мысли применять инструмент, трудящийся способом деления подачи. Для осуществления этого нужно было проверить, как эти сверла будут вести себя в отношении уводов. Существовало очень сильно укоренившееся в практику вывод о склонности сверл аналогичного типа к уводам.
Рис. 11. Уводы при сверлении однотипных заготовок двумя типами сверл:
Средний увод оси отверстий при сверлении однокромочными скоростными сверлами составлял УС1 – 1,5 мм, в то время как средний увод при сверлении быстрорежущими сверлами равнялся УС2 = == 4,5 мм, т.е. был в три раза выше, чем у скоростных однокромочных сверл. В то время такую громадную отличие в качестве просверленных заготовок растолковывали высоким качеством однокромочных сверл. Испытания, обрисованные выше, вносят ясность в разглядываемый вопрос, но не освобождают от умелой проверки сверл, трудящихся способом деления подачи.
Испытания были совершены с тремя типами сверл, охватывающими фактически все вероятные комбинации сверл: от сверл с безотносительной определенностью базирования (однокромочные сверла) до сверл без определенности базирования (двухкромочные сверла, трудящиеся способами деления подачи). Хотя проверить специфичность отдельных типов инструментов и в отношении скорости резания, сверление проводилось как на высоких, так и на низких скоростях.
На рис. 12 продемонстрированы уводы, полученные при опробовании сверл на двух режимах резания. Из рисунка видно, что конструкции сверл не оказывают значительного влияния на уводы.
При скоростном и нескоростном режимах разные типы инструментов просверлили отверстия практически с равными размерами уводов. Так определили, что нет особенных оснований проигнорировать способ деления поцачи и инструменты, трудящиеся этим способом. Это тем более направляться подчернуть, что эта несколько инструментов владеет более высокой производительностью.
Результаты опытов послужили основанием для разработки новой конструкции скоростного сверла для глубокого сверления, трудящегося способом деления подачи.
Неспециализированные выводы. Проведенные иследования уводов при глубоком сверлении разрешают сделать следующие выводы.
Главной причиной увода есть поперечная разнообраба-тываемость материала заготовки, которая практически в любое время существует у заготовок. Но условия, при которых происходит увод сверла, не всегда существуют. Увод может происходить лишь при условиях несовпадения сейчас оси сверла с осью симметрии разнообрабатываемости и при наличии податливости (упругости) инструмента (либо обрабатываемого материала).
Скорость резания, какой бы величины она ни была, не есть обстоятельством увода сверла, но данный фактор может нивелировать поперечную разнообрабатываемость и этим заметно сократить увод.
Вторыми факторами, воздействующими на увод не как следует (как воздействует обстоятельство), а лишь количественно, являются упругость инструмента, угол между режущей перпендикуляром и кромкой к оси сверла
При сверлении с вращением заготовки угол между осью вращения сверла и осью заготовки а0 оказывает определенное влияние на увод, но намного меньшее, чем при неподвижной заготовке. Это несовпадение легко корректируется при сверлении вращающейся заготовки. Сам процесс сверления, так, проходит при постоянном трансформации условий резания, поскольку на своем пути сверло испытывает воздействие как корректирующих, так и усугубляющих увод факторов.
Главная причина увода — поперечная разнообрабатываемость — способна не только отклонять сверло от оси вращения заготовки, но при определенных событиях деятельно совмещает его ось с осью вращения заготовки.
Рис. 12. Уводы, полученные при опробованиях разных типов сверл на двух режимах резания
На данный момент величина допустимого увода принимается равной 0,5 мм на 1 м длины сверления.
Так, дабы сверлить с малыми уводами, нужно следующее:
1) трудиться на высоких скоростях резания;
2) использовать в качестве материалов заготовок по возможности высоколегированные, прекрасно прокаливающиеся стали;
3) шепетильно проводить операции термообработки заготовок перед сверлением, не допуская громадной поперечной разнотвердости (раз-нообрабатываемости);
4) создавать сверление по возможности с вращением заготовок;
5) использовать более твёрдые сверла;
6) при наружной обработке перед сверлением заготовок типа тел вращения снабжать по возможности съем равномерного припуска;
7) совершенно верно центровать заготовки и заправлять отверстия под заход инструмента и др.
Так, внедрение скоростного сверления глубоких отверстий перспективно не только с позиций увеличения производительности, но и с позиций уменьшения уводов, увеличения чистоты образуемых поверхностей, а следовательно, увеличения качества обработки.