Cущность основных видов неразрушающего контроля качества сварки
Контроль внешним осмотром. Внешним осмотром выявляются:
несоответствие геометрических размеров швов проектным (размеры швов определяются особыми шаблонами); подрезы; непровар в корне соединения (ориентировочно); поверхностные трещины (продольные либо поперечные); наружные раковины и газовые поры; неравномерность шва и крупная чешуйчатость; незаплавленные кратеры; коробление изделия либо отдельных его элементов.
Контролю внешним осмотром подвергаются все сварные конструкции независимо от их ответственности и назначения. Внешний осмотр сварных подробностей действен лишь тогда, в то время, когда он производится квалифицированным и умелым контролером.
Радиационные виды контроля. Надежным и обширно используемым на данный момент есть радиационный контроль просвечиванием сварных соединений рентгеновским и гамма-излучением.
Обнаружение недостатков металла обеспечивается свойством рентгеновского излучения попадать через жёсткие материалы; среди них и металлы. При прохождении через металл рентгеновское излучение понижает собственную интенсивность благодаря поглощения его ядерной решеткой металла. Лучи ослабляются тем посильнее, чем больше атомов встречают они на своем пути. Исходя из этого степень ослабления рентгеновского излучения зависит от физических и химических особенностей материала, его массы и количества.
Неодинаковая интенсивность лучей, прошедших через просвечиваемый объект, фиксируется с противоположной стороны исследуемого участка на фотопленке (рис. 1). Излучение оказывает на вещество пленки химическое действие, которое выражается в почернении фотопленки.
Недостатки выявляются в виде тёмных пятен на ярком фоне хорошего шва.
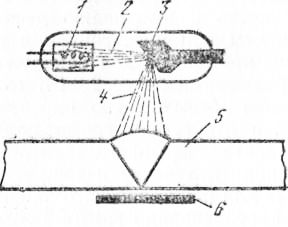
Рис. 1. Схема рентгеновского просвечивания: 1 — катод, 2 — пучок электронов, 3 — анод (мишейь), 4 — рентгеновское излучение, S — просвечиваемы)! металл, 6 — кассета с пленкой
Рис. 2. Рентгеновские снимки: 1 — газовые включения, 2 — шлаки, 3 – трещины, 4 — непровары
Рентгеновское излучение вызывает световозбуждающее воздействие некоторых веществ: это воздействие пребывает в том, что эти вещества (к примеру, платиносинеродистый барий, сернистый цинк и др.) при действии на них рентгеновского излучения флюоресцируют, т. е. дают свечение. Это свойство рентгеновского излучения употребляется при экспозиции не на пленку, а на экран при просвечивании металлов.
Используется контроль рентгеновским излучением с применением экранов в сочетании с телевизионным устройством, преобразующими рентгеновское изображение в видимое (установка типа РИ — рентгенотелевизионный интроскоп). Чувствительность этого контроля не уступает чувствительности фотоконтроля (1% и более), а производительность контроля довольно большая.
Скорость передвижения контролируемого изделия образовывает у рентгенотелевизионного интроскопа «РИ-10 Т» 0,5 м/мин..
Интроскопы смогут трудиться с разными рентгеновскими аппаратами, к примеру типа РУП-150-10.
Для контроля в условиях монтажа выпускаются портативные импульсные рентгеновские аппараты «РИНА-1Д», «ИРА-1Д» и другие с большой толщиной стали, дешёвой для рентгеногра-фирования, до 25 мм.
Гамма-излучение, имеющее те же свойства, отличается от рентгеновского более высокой жесткостью и довольно малой длиной волны; следовательно, оно может попадать в металл глубже, чем рентгеновское излучение. Оно разрешает просвечивать металл толщиной до 300 мм. Чувствительность к обнаружению недостатков гамма-излучением немного ниже, чем при просвечивании рентгеновским.
Исходя из этого гамма-излучение используют для обнаружения довольно больших недостатков с размерами более 2—4% толщины просвечиваемого металла. Громадное преимущество просвечивания гамма-излучением содержится в отсутствии громоздкой аппаратуры, которая связана с подводкой электричества и охлаждающей воды, и возможность источника просвечивания и портативность излучения в местах, недоступных для рентгеновского аппарата.
Но большим недочётом при просвечивании гамма-излучени-ем есть невозможность регулирования интенсивности излучения, которая в рентгеновской трубке регулируется подводимым к ней напряжением. Также, работа с гамма-аппаратами более страшна для операторов, чем работа с рентгеновскими. Гамма-излучение, имеющее громадную жесткость, при неосторожном обращении с гамма-аппаратом, может позвать сильное и страшное облучение.
Расшифровка рентгенограмм. На негативе рентгенограммы (рис. 2) недостатки изобразятся в виде тёмных точек (газовые поры), неправильной формы пятен (шлаковые включения), в виде прямой тёмной линии и полос (непровар, трещина).
Газовая пористость выявляется на пленке в виде округлых изображений плотности и различного размера, каковые находятся изолированно, группами либо разбросаны непоследовательно по полю шва.
Шлаковые включения проявляются на пленке как теневые изображения удлиненной неправильной формы, находятся изолированно в одном направлении либо разбросаны в беспорядке по полю шва.
Непровар представляется чёрной тенью, которая в большинстве случаев имеет вытянутую форму. Непровар в корне соединения виден как прямая чёрная целая либо прерывающаяся линия; довольно часто имеет форму прямой, идущей по оси шва.
Трещины проявляются на пленке в виде четких чёрных изгибающихся линий. Подрез виден на пленке как чёрная линия рядом с главным металлом.
Особенности просвечивания сварных швов рентгеновским и гамма-излучением. Потому, что о недостатке в шее делают выводы только по отраженному изображению, то просвечивание лишь с одной позиции не дает возможности выяснить глубину залегания недостатка. Глубину недостатка предположительно определяют по расстоянию между изображениями, взятыми на рентгеновских пленках при просвечивании под двумя разными взаимно пересекающимися углами.
Схема размещения дефектометра и крепления кассеты с пленкой продемонстрирована на рис. 3.
Толщину недостатка определяют сравнением плотностей изображения на пленке недостатка со особым эталоном. Наряду с этим методе на плотность изображения недостатка воздействует не считая толщины кроме этого и его ширина. При маленькой ширины недостатка смогут иметь место большие погрешности.
Все это формирует сложность расшифровки узких их глубины и дефектов залегания.
Оценка качества сварного шва по рентгеновскому либо гамма-снимку производится по трехбалльной совокупности. Сварные швы, оцененные баллом 1, подлежат исправлению.
Ультразвуковой контроль сварных швов. Ультразвуковой метод обнаружения недостатков сварки основан на отражении направленного импульса высокочастотной звуковой волны.
В большинстве случаев частоты ультразвуковых колебаний превышают 20 000 Гц и находятся выше звукового диапазона, принимаемого обычным людской ухом. Эти волны распространяются в однородных материалах по относительно прямым линиям и при достижении границы раздела двух сред (к примеру, однородный внутренний порок и металл шва) преломляются и отражаются.
Отраженный пучок улучшается, преобразуется в переменный ток и подается на экран электроннолучевой трубки, на которой изображается соответствующей формы импульс ультразвуковой волны. Расшифровка этого импульса разрешает выяснить наличие в шве недостатка.
Ультразвуковой контроль имеет следующие главные преимущества:
– высокая чувствительность (1—2%), разрешающая обнаруживать, определять местонахождение и измерять маленькие недостатки (площадью более 2 мм2);
– громадная проникающая свойство звуковых волн, разрешающая осуществлять контроль толстые материалы (для стали До двух метров);
– возможность контроля лишь с одной поверхности сварного соединения.
Но ультразвуковой контроль имеет кроме этого и значительный недочёт, ограничивающий его использование либо затрудняющий диагностику качества сварных швов; он выражается в сложности расшифровки недостатков шва из-за влияния внутренней структуры (большое зерно, тонкодисперсные включения); сложной конфигурации и сложного вида и ориентации дефекта сварного изделия
Рис. 3. Схема размещения дефектометра и крепления кассеты с пленкой: 1 — сварное соединение, 2 — де-фектометр, 3 — кассета с пленкой, 4 — магнит
При прозвучивании неоднородного металла, каким есть ме талл практически каждого сварного соединения, происходит громадное рас сеива[ние энергии ультразвуковых волн, которое ведет к слож нечёткому изображению и ному импульса недостатка на экране элек троннолучевой трубки. Чрезмерное рассеивание энергии колеба ний может привести к дефициту ее для обнаружения недостатка.
Исходя из этого ультразвуковой контроль довольно часто используют как предварительный в сочетании с последующим просвечиванием швов рентгенов’ ским либо гамма-излучением При всех случаях ультразвуковой контроль швов обязан выполняться высококвалифицированными и умелыми операторами.
обнаружение и Получение ультразвуковых волн. В дефектоскопии используется пьезоэлектрический метод получения ультразвуковых волн, при которых электрические колебания преобразовываются в механические.
Выходной сигнал от импульсного генератора (рис. 4) проходит через датчик (щуп) к сварному соединению. Датчик является пластинкойиз пьезоэлектрического материала, которая вибрирует, преобразуя переменный электрический ток в механические колебания.
В качестве пьезоэлектрических материалов могут служить кварц, сульфат лития, титанат бария и др.
Частота импульса регулируется толщиной пьезоэлектрической пластинки. Щуп с пьезоэлектрической пластинкой прижимается к поверхности сварного соединения через звуковую (контактную) среду (слой воды, машинного масла, глицерина и др.), так как воздушное пространство есть нехорошим проводником ультразвуковых волн и мешает их прохождению. Узкий слой жидкости облегчает кроме этого перемещение датчика по поверхности сварного соединения.
Звуковой контакт возможно кроме этого достигнут погружением сварного изделия с щупом в водяную ванну.
Упругие колебания достигают большого значения тогда, в то время, когда частота электрических колебаний сходится с колебаниями пластины. Исходя из этого ультразвуковой дефектоскоп обязан с определенной скоростью генерировать (производить) ультразвуковые волны требуемой частоты.
Требуемая частота зависит от размера контролируемого недостатка и требуемой глубины проникновения. К примеру, чем выше частота, тем на большей глубине выявляется недостаток и тем меньше недостаток, что возможно обнаружен.
Рис. 4. Схема ультразвукового контроля металла: 1 и 2 — датчики (щупы) с пьезоэлектрическим материалом, 3 — звуковая среда, 4— недостаток
Для контроля качества сварных швов целесообразно применять импульсные ультразвуковые дефектоскопы. В данной совокупности дефектоскопа генератор высокой частоты подает короткий импульс тока на датчик из пьезоэлектрического материала, после этого наступает пауза, по окончании чего опять направляться очередной импульс и т. д.
Ультразвуковой пучок, достигший недостатка в шве, отражается и принимается или вторым щупом (приемным при двухщуповой схемы), или тем же (подающим — однощуповая схема) на протяжении паузы между импульсами.
Исполнение контроля сварного шва и манипуляция щупом иллюстрируются рис. 5. Щупдолжен перемещаться параллельно сварному шву зигзагами, как продемонстрировано на рис. 5.
При перемещении щупа 1 контролируется лишь часть шва (на рис. заштрихована). Для обследования всего поперечного сечения шва щупом делают зигзагообразные перемещения, медлительно удаляясь от шва на расстояние, достаточное для обследования всего шва (щуп 2 на рис. 162).
Области применения ультразвукового контроля. При контроле ультразвуковым дефектоскопом УЗД-7 смогут быть распознаны трещины и непровары глубиной более 0,15—0,2 мм при их длине не меньше 5 мм; шлаковые включения и газовые поры диаметром 1 — 1,5 мм и более при толщине сваренной стали более чем 5 мм.
Фактически минимальная толщина контролируемых дефектоскопом УЗД-7 сварных швов образовывает 8—10 мм; при меньшей толщине недостатки выявляются нечетко.
Па стройках громаднейшее использование находят устройства типа УДМ-1М, ДУК-13ИМ, ДУК-ВИМ (батарейное питание).
Индустрией выпускаются кроме этого ультразвуковые дефектоскопы УЗД-НИИМ-5, ДУК-11ИМ, ДУК-66П, УДМ-3. Питание дефектоскопов производится от сети напряжением 12, 36, 127 либо 220 В; в некоторых типах дефектоскопов предусмотрено кроме этого питание от аккумуляторных батарей напряжением 12 В. Дефектоскопы снабжают глубину прозвучивания до 700 мм (УДМ-3 — до 2000 мм), обнаружение недостатков в стали площадью 2—3 мм2 на глубине до 100 мм.
Ультразвуковой вид контроля применим для прозвучивания труб со стенкой толщиной более 8 мм.
Магнитные виды контроля. Магнитный вид контроля металла основан на том, что при прохождении магнитных силовых линий по испытуемому материалу в местах недостатков появляются поля рассеяния. В случае если на поверхности металла нанести ферромагнитный порошок, то над местом размещения недостатка создадутся скопления порошка в виде верно ориентированного магнитного спектра.
Рис. 5. Контроль сварного шва и манипуляция щупом
Намагничивание осуществляется пропусканием тока по подробности, созданием магнитного поля около подробности действием природного магнита либо электромагнита. Неравномерность поля определяется искателем, в частности магнитным порошком, что и показывает протяжённость и местоположение недостатка в подробности.
Эргономичным методом создания магнитного потока есть пропускание тока плотностью 15—20 А/мм2 по виткам сварочного провода, наматываемого тремя — шестью витками на подробность. Для намагничивания лучше использовать постоянный ток.
Посредством магнитного порошка возможно выявлять каждые внутренние недостатки. На данный момент данный вид контроля используют для обнаружения:
поверхностных трещин, невидимых невооруженным глазом;
трещин, находящихся в металла на глубине не более 15 мм (чем больше ширина трещины, тем легче ее распознать);
расслоение металла. Возможно обнаруживать кроме этого большие газовые раковины, поры и шлаковые включения, расположенные на глубине не более 3—5 мм.
Существует два метода контроля посредством магнитного порошка: сухой и мокрый. В первом случае магнитный порошок (охра, сурик, металлические опилки, окалина и т. д.) находится в сухом виде; во втором случае магнитный порошок находится во взвешенном состоянии в жидкости (керосине, мыльном растворе, воде). Сухим методом возможно найти как поверхностные, так и глубинные недостатки; мокрым методом лучше обнаруживаются поверхностные недостатки.
В производстве сварных трубопроводов для контроля качества швов применяется магнитографический метод контроля посредством магнитной ленты. Он основан на записи полей рассеяния, появляющихся над недостатками, на ферромагнитную ленту и последующим воспроизведении их магнитографическим магнито-скопом. В следствии сравнения контролируемого стыка с эталоном контролер делает вывод о пригодности стыка и характере дефектов.
В соответствии с методике ВНИИСТ магнитографическому контролю возможно подвергать стыковые швы и стыки трубопроводов листовых металлоконструкций с толщинами стенок от 2 до 16 мм.
Рис. 6. Прохождение магнитного потока по подробности при наличии недостатка в металле
Рис. 7. Схема намагничивания изделия пропусканием тока: 1 — подробность, 2 — витки провода, 3 — трещина
Магнитографический метод более чувствителен к наружным недопустимым недостаткам швов — резким переходам по усилению, большой чешуйчатости шва, гребенчатому усилению и подрезам. Но довольно часто данный вид негоден для обнаружения внутренних недостатков. К примеру, стыки трубопроводов диаметром менее 114 мм с толщиной стены 4 мм смогут иметь усиления шва высотой более 40% толщины стены трубы. При магнитографировании запись от недостатка сливается с записью от усиления.
В следствии этого контроль таких соединений делается неосуществимым.
Надежность магнитографического контроля возрастает с уменьшением отношения усиления шва к толщине стены трубы.
В некоторых случаях магнитографический метод контроля может заменить контроль просвечиванием.
Для очень важных сварных конструкций с высокими требованиями к качеству сварных соединений целесообразнее использовать оба вида контроля. Наряду с этим возможно рентгенопросвечивание использовать только для расшифровки недостатков, распознанных магнитографическим контролем.
Используются дефектоскопы МД-9, МДУ, МГК-1, ВУМД-7 и др.
Контроль непроницаемости швов. Контроль, основанный на проницаемости газов (воздуха, смеси воздуха с другими индикаторами и аммиаком) и жидкостей (воды, керосина), обширно употребляется для трубопроводов герметичности и проверки сосудов.
Гидравлическое опробование. Гидравлическому опробованию подвергаются разные сосуды, трубопроводы и котлы, трудящиеся под давлением. Гидравлическим опробованием контролируется не только плотность сварных соединений, вместе с тем относительная прочность всей сварной конструкции. При гидравлическом опробовании сосуд наполняется водой; для выхода воздуха в верхней части одно отверстие оставляют открытым. Это отверстие закрывается только по окончании наполнения водой всего сосуда.
После этого в сосуде гидравлическим прессом создается давление, равное рабочему давлению. В случае если недостатков не обнаруживается, давление возрастает ДО Рпсп == 1,25 ЯраС ДЛЯ сосудов И Яисп = 1,5 Рраб ДЛЯ трубопроводов. Под этим давлением сосуд либо трубопровод выдерживают 5 мин, после этого давление снижают до- Рраб и обстукивают соединения молотком со сферической головкой на расстоянии 15— 20 мм от кромки’ шва.
По окончании, этого швы осматривают. При опробовании на морозе вместо воды используют антифриз.
Пневматическое опробование. Пневматическое опробование выполняют с целью контроля плотности сварных соединений. Для этого в замкнутый сосуд нагнетают воздушное пространство до рабочего давления. Снаружи все швы смачиваются мыльным раствором. Сжатый воздушное пространство в местах неплотностей образует мыльные пузыри.
В зависимости от интенсивности и количества выделения мыльных пузырей возможно делать выводы о величине и характере недостатка. Пневматический вид контроля сварных соединений взял широкое использование при опробовании сосудов малой емкости, как самый удобный и дешёвый в заводских условиях с массовым производством. В этом случае испытуемый сосуд погружается в ванну с водой и неплотности определяются выделением пузырьков воздуха.
Для сосудов громадного количества использовать опробование сжатым воздухом направляться крайне осторожно, поскольку при наличии недостатков в швах может случиться разрыв всего сосуда.
Химическое опробование. Данный вид опробования сварных соединений, предложенный С. Т. Назаровым, применим для опробования на плотность замкнутых сварных сосудов. В испытуемый сосуд подается под давлением до 2 ат смесь воздуха с аммиаком (1%). С внешней стороны сосуда на сварные соединения хорошо укладывается (приклеивается) бумага (либо марлевый бинт), пропитанная 5%-ным водным раствором азотнокислой ртути.
В случае если в сварном соединении имеются неплотности, то аммиак, владея высокой проницаемостью, пройдет через них и в этих местах бумага потемнеет. В зависимости от скорости появления на бумаге пятен, их размеров и формы возможно делать выводы о размерах и характере недостатка. В большинстве случаев время проникания аммиака через неплотности сварного соединения образовывает от 10 до 30 мин.
Данный вид опробования сварных соединений взял на производстве относительно малое использование.
Опробование керосином. Керосин владеет свойством попадать через малые неплотности: трещины, поры и сквозные непровары металла. Для контроля швы со стороны раскрытия окрашивают мелом, разведенным на воде с добавлением клея, а со стороны корня соединения смачивают керосином.
Керосин, проходя через неплотности, образует ,на высохшей меловой краске чёрные пятна, по которым возможно делать выводы о месте и характере неплотности ее размещения. В случае если в течение 30—60 мин такие пятна не покажутся, то швы считаются удовлетворительными. Скорость прохождения керосина через металл будет определяться толщиной сварного соединения и характером размещения недостатков в металле.
Для важных изделий время выдержки под керосином устанавливают до 12 ч при температуре окружающего воздуха выше 0° и до 24 ч при температуре ниже 0°.
Керосиновая проба эквивалентна 3—4 ат гидравлического давления, используемого для сварных сосудов закрытого типа.