Инструментальные материалы
В творческой деятельности изобретателей и рационализаторов, в какой бы отрасли промышленности они ни трудились, инструменты всегда являются очень важным объектом приложения их усилий. Качество инструментов оказывает влияние на производительность труда, стоимость изделий: на возможности механизации и автоматизации технологических процессов.
Определяется качество инструмента прежде всего материалом, из которого он изготовлен. За последние годы произошли существенные изменения в разработке и применении инструментальных материалов. Изменились составы и свойства сплавов, утвердились новые критерии оценки качества инструментальных материалов. Например, широко известная быстрорежущая сталь Р18 во многих случаях успешно заменяется сталью Р12 с меньшим содержанием вольфрама. Эта замена обоснована не только экономически.
Исследованиями в СССР и зарубежных странах (США, ФРГ, Швеция, Япония) установлено, что стойкость инструментов из стали, содержащей 12% вольфрама (Р12), выше, чем из стали, содержащей 18% вольфрама (Р18), благодаря меньшему размеру зерен карбидов вольфрама. Если раньше главное значение придавалось равномерному распределению карбидов, то в настоящее время доказано, что на стойкость инструмента решающее влияние оказывают размеры карбидов.
В связи с этим разработаны и внедряются новые способы производства быстрорежущей стали с карбидами малого размера (2—5 мкм). Прочность стали Р12 на 50—70% выше прочности стали Р18, и шлифуемость ее лучше.
Созданы новые, более износостойкие марки быстрорежущих сталей с повышенным содержанием углерода, с частичным замещением вольфрама молибденом (Р6М5) и кобальтом (Р6М5К5). Вольфрамомолибденовая сталь Р6М5 не только на 30% дешевле, но и обладает хорошей теплопроводностью, мало склонна к трещинообразованию.
Анализ зарубежного опыта показывает, что иностранные фирмы поставляют на рынок большую номенклатуру быстрорежущих сталей, однако практически до 90% инструмента изготовляется из вольфрамомолибденовой стали марки М2 (Р6М5). В нашей промышленности основной маркой быстрорежущей стали является Р6М5.
Разработана технология производства металлокерамической быстрорежущей стали методом горячего прессования порошков, полученных восстановлением окислов. Эта сталь обладает монолитностью, беспористостью, мелкозернистостью, высокой прочностью и вязкостью, не имеет анизотропии механических свойств, не деформируется.
Совершенствование твердых сплавов идет в основном в направлении улучшения их механических свойств, химического состава, структуры, а также технологии изготовления. Как правило, высокое качество сплавов зарубежных фирм определяется регламентируемой величиной зерна и отсутствием пористости. Представляют большой практический интерес данные по применению инструмента из твердых сплавов группы РЗО (Т5К10) с покрытием тонким слоем карбида титана.
Фирма «Керомант» (Швеция) рекомендует такой инструмент под названием «Гамма коатинг». Процессу покрытия подвергаются только твердосплавные пластинки группы ТЗО (Т5КЮ) после их окончательного изготовления, включая заточку и доводку. Толщина слоя покрытия —от 0,01 до 0,05 мм.
Такое покрытие повышает износостойкость твердосплавных пластинок в 2—5 раз, а прочность и вязкость сплава сохраняются.
Внедряются новые металлокерамические материалы, которые содержат карбид титана и цементирующую стальную связку. Эти материалы обладают уникальными свойствами — они допускают возможность термической обработки (отжиг, закалка, отпуск), благодаря чему могут быть подвергнуты механической обработке в отожженном состоянии и приобрести высокую твердость и износостойкость путем закалки. По механическим свойствам эти материалы не уступают твердым сплавам.
В нашей стране разработана технология и организовано промышленное производство новых сверхтвердых синтетических материалов. С каждым годом возрастает число станков, работающих абразивными инструментами. Наряду с количественным ростом парка подобных станков непрерывно повышается эффективность абразивной обработки. В значительной мере это связано с созданием новых абразивных материалов и инструментов.
Так, разработана технология и создано промышленное производство нового абразивного материала — эль-бора и инструментов из него. Эльбор, по твердости и абразивной способности близкий к алмазу, значительно превосходит его по термостойкости. Промышленность производит инструмент из эльбора диаметром от 4 до 350 мм на органической, керамической и металлической связках; помимо кругов, изготовляются бруски, шлифовальные шкурки и пасты.
Для повышения прочности крепления зерен в мягкой органической связке, а также увеличения прочности самих зерен разработан способ получения агрегированных металлизированных алмазных порошков со специальной формой частиц. При этом алмазно-абразивные частицы представляют собой укрупненные агрегаты, состоящие из нескольких алмазных зерен, покрытых и прочно спаянных между собой металлическим сплавом. Под действием капиллярных сил металлический расплав заполняет мельчайшие поры, трещины и другие дефекты на поверхности алмазных и абразивных зерен и после отвердевания оказывает цементирующее действие, повышая в 1,5—3 раза стойкость абразивных зерен.
Специально для металлизированных агрегированных алмазных порошков разработана новая органическая связка марки 01. Каждый карат алмазов в круге на связке 01 дает значительную экономию и снижает затраты на шлифовальный алмазный инструмент в 3—4 раза. Круги с металлизированными агрегированными алмазно-абразивными порошками на связке 01 выпускаются с концентрацией алмазов 50 и 100% и зернистостью от 50/40 до 160/125.
В настоящее время применяются абразивные инструменты, пропитанные серой, парафином и другими импрегнаторами. Стойкость таких инструментов повышается в 2 раза по сравнению с непропитанными брусками. Это объясняется защитным действием импрегнатора, предохраняющего связку от разрушения.
Появились разнообразные тканевые круги для полирования. В зависимости от назначения применяются различные виды тканей, в том числе сисаль. Ткани пропитываются разными импрегнаторами, что повышает срок их службы более чем на 50%.
Созданы также новые разновидности шлифовальной шкурки, в том числе водостойкие шлифовальные шкурки на синтетических клеях. Выпускается шлифовальная шкурка на рулонной фибре из абразивов Э, ЭБ, КЗ зернистостью 80, 50, 40, 25 и 16 на синтетических клеях марок ФМ-4 и ФМ-3.
ВНИИАШ разработал и завод «Ильич» освоил производство шлифовальной шкурки из эльбора зернистостью М40, 5, 8 с применением синтетических клеев. Применение такой шкурки дает повышение производительности и стойкости по сравнению с алмазной в два—три раза. При этом чистота поверхности соответствует 11-му классу.
Находят довольно широкое применение в качестве инструментального материала пластмассы. В современной номенклатуре инструмента и технологической оснастки 25—30% может быть изготовлено из пластмасс. Их используют при производстве приспособлений, штампов, литейных моделей, копиров, полировального и доводочного инструмента, при контроле и сборке пресс-форм и штампов.
Этот краткий обзор показывает, что в Советском Союзе и в других промышленно развитых странах ведутся значительные работы по изысканию и применению новых инструментальных материалов. При этом характерно все расширяющееся применение более экономичных инструментальных материалов для высокопроизводительного резания труднообрабатываемых сплавов.
—
К материалу, из которого изготовляют резцы, предъявляют особые требования. Чтобы режущая часть резца могла врезаться в поверхность заготовки, твердость режущей части должна быть выше твердости обрабатываемого металла.
Металл или сплав, сопротивляясь внедрению режущей части инструмента в срезаемый слой, давит на переднюю поверхность резца; эта сила давления стремится изогнуть, сломать резец, поэтому материал, из которого сделан резец, должен обладать достаточной прочностью.
Режущая кромка резца, испытывающая при работе ударные нагрузки, не должна выкрашиваться, поэтому материал режущей части должен быть достаточно вязким.
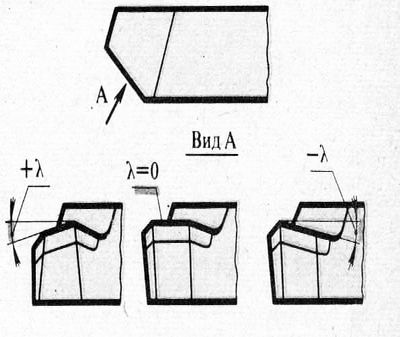
1. УГОЛ НАКЛОНА РЕЖУЩЕЙ КРОМКИ
Передняя и задняя поверхности резца, соприкасающиеся при резании с обрабатываемым металлом, подвергаются истиранию и нагреву до высокой температуры. Следовательно, инструментальные материалы должны быть износостойкими при высокой температуре в течение продолжительного времени, т. е. обладать высокой красностойкостью. Быстрорежущие стали. Наиболее распространенным инструментальным материалом является быстрорежущая сталь.
Особенность быстрорежущей стали: высокая твердость (до HRC65), высокая красностойкость (до 650 °С), способность в случае перегрева восстанавливать режущие свойства после охлаждения на воздухе. Эти свойства достигаются благодаря легированию вольфрамом, хромом, ванадием и другими элементами.
По ГОСТ 9373—60 быстрорежущие стали подразделяются на стали нормальной и повышенной производительности. К быстрорежущим сталям первой группы относятся стали марок Р9 (9% вольфрама), Р12, а также воль-фрамомолибденовые быстрорежущие стали Р6М5—молибдена 5% и Р6М5ФЗ, инструменты из которых для черновой обработки имеют преимущества перед инструментами из сталей Р12, Р9, так как молибден повышает красностойкость. Красностойкость быстрорежущих сталей первой группы 600 °С.
К быстрорежущим сталям второй группы относятся Р9К5, Р9Ф2К10, Р18Ф2К5 и Р10Ф2К5, содержащие соответственно 5 и 10% кобальта, а также Р6М5К8 и Р9М4К8 — кобальта 8%. Красностойкость этих сталей достигает 650 °С. Они применяются для обработки твердых и вязких конструкционных материалов (нержавеющей и жаропрочной стали, титановых сплавов).
Особенно эффективна при обработке труднообрабатываемых сплавов быстрорежущая сталь Р18Ф2К8М. Инструменты из быстрорежущей стали подвергают термической обработке — закалке и отпуску. Для быстрорежущей стали Р6М5 закалка заключается в нагреве до 1230 °С, выдержке до 2 мин и быстром охлаждении в масле.
Режим отпуска: нагрев до 550 °С, выдержка до 90 мин и медленное охлаждение на воздухе (или вместе с печью). Отпуск производят троекратно. Благодаря отпуску структура металла, полученная после закалки (мартенсит), стабилизируется, снимаются внутренние напряжения, инструмент приобретает высокие режущие свойства.
Твердые сплавы. Значительно большей твердостью (до HRA90), красностойкостью (до 1000 °С) и износостойкостью обладают металлокерамические спла вы. Сырьем для их изготовления являются порошки карбидов (соединений с углеродом) вольфрама и титана совместно с порошком кобальта.
Порошки прессуют в пресс-формах, получая пластинки различных форм и размеров. Эти пластинки затем спекают в специальных печах при температуре до 1600 °С (в водородной атмосфере).
Металлокерамические твердые сплавы — непластичны, наоборот, обладают повышенной хрупкостью.
В зависимости от содержания карбида вольфрама, карбида титана и кобальта твердые сплавы приобретают различные свойства. Чем больше кобальта, тем сплав более вязок, лучше сопротивляется ударной нагрузке. Поэтому сплавы с большим содержанием кобальта применяют для инструментов, которыми выполняют обдирочные работы.
Стальная стружка обладает способностью «прилипать» к передней поверхности инструмента и выносить за собой частички металла инструмента. Если твердый сплав содержит карбид титана, то такое «прилипание» (адгезия) наступает только при очень высокой температуре (выше 700°С), что соответствует скоростям резания, на которых практически работы не ведутся. Поэтому для обработки стали применяются твердые сплавы, содержащие карбид титана.
При обработке чугуна стружка надлома давит на переднюю поверхность резца близко к режущей кромке, и это может вызвать поломку режущей кромки. Наличие большого количества карбида вольфрама повышает твердость режущей кромки, т. е. способствует увеличению работоспособности резца именно при обработке чугуна.
Области применения твердых сплавов для режущих инструментов рекомендованы ГОСТ 3882—74: твердые сплавы группы ВК (воль-фрамокобальтовые) — для обработки хрупких материалов (чугун, бронза); сплавы группы ТК (титановольфрамокобальтовые) — для обработки вязких материалов (сталь, латунь). На державках резцов наносится марка твердого сплава.
Мелкозернистые твердые сплавы группы ВК (с индексом М) и крупнозернистые (с индексом В) предназначены для изготовления инструментов, обрабатывающих заготовки из нержавеющей и жаропрочной стали, из титановых сплавов, закаленной стали.
Промышленность выпускает также трехкарбид-ные твердые сплавы титановольфрамокобаль-товые, обладающие высокой ударной вязкостью. Инструментами, оснащенными пластинками сплава ТТ7К12 успешно выполняют работы с тяжелой ударной нагрузкой, например обрабатывают заготовки с прорезями, с наплавленной поверхностью, отливки со следами отрезанных прибылей и т. д. Сплав ТТ10К8-Б служит для отработки труднообрабатываемых материалов.
Минералокерамика. Для оснащения режущей части резца применяется также синтетический материал — минералокерамика (ЦМ332), изготовляемый из дешевого сырья — глинозема. Пластинки минеральной керамики (белого цвета) обладают высокой твердостью (до HRA 93), красностойкостью (до 1200 °С) и изностостойкостью.
Однако повышенная хрупкость этого материала ограничивает его применение.
Резцы, оснащенные минералокерамическими пластинками, испОльзуют для чистовой и по-лучистовой обработки главным образом медных и алюминиевых сплавов и чугуна. Алмазы. Самыми твердыми из инструментальных материалов являются алмазы. Алмазы бывают естественные (природные) и искусственные (синтетические).
Применение алмазных инструментов позволяет производительно и высококачественно обрабатывать самые твердые материалы. Для высокопроизводительной обработки сталей, в том числе легированных и закаленных, успешно применяется новый синтетический материал — кубический нитрид бора (торговые марки «Эльбор-Р», «Композит», «Кубонит»).