Изготовление мебельных щитов
Изготовление щитов со стружечным заполнением. На мебельных фирмах изготовляют щиты со стружечным заполнением, цена которых немного выше стоимости древесностружечных плит, производимых специальными фирмами. Но их изготовление имеет то преимущество, что мебельное предприятие может скоро приобретать щиты любой нужной сейчас толщины, рационально применять отходы древесины и более полно загружать гидравлические прессы.
Технологический процесс изготовления щитов со стружечным заполнением складывается из подготовки рамки-каркаса и стружечно-клеевой массы, склеивания и формирования щита.
При подготовке каркаса предварительно обработанные бруски соединяют впритык при помощи съемных пружинных приспособлений (сжимов), каковые стягивают каркас на прессования щита и время формирования.
Подготовка стружечно-клеевой массы складывается из операций изготовления стружки, ее транспортирования, просеивания, смешивания и сушки с клеем.
Стружку изготовляют из отходов либо из низкосортной древесины, измельченной на особых станках, и от них по трубопроводу ее собирают циклоном и высыпают в бункер.
Станки для того чтобы, бункер и циклон устанавливают, в большинстве случаев, вне помещения, где изготовляют щиты.
При маленьком количестве производства щитов кое-какие фирмы применяют лишь стружечные отходы, каковые от станков пневмотранспортом подаются в бункер.
Из бункера стружка поступает на сортировочную машину— грохот. Тут она методом вибрации на ситах освобождается от излишне небольших и больших частиц, ухудшающих уровень качества щитов. Просеянная стружка по конвейеру поступает в сушилку, где ее высушивают до влажности 4—6%.
При большей влажности стружки, в следствии усиленного парообразования на протяжении прессования, может случиться вспучивание щитов.
Высушенную стружку определенными дозами подают в смеситель, куда в один момент вводят определенное количество клеевого раствора.
Несложный смеситель представляет собой древесный цилиндр длиной 1,2—1,5 м и диаметром 0,8—1,0 м, закрепленный на столе. В цилиндра расположена ось с 8—12 лопастями, приобретающая вращение от электродвигателя через редуктор со скоростью около 50 об/мин. Цилиндр сверху имеет прорезь, через которую засыпают просеянную стружку.
По окончании того как в смеситель засыпали стружку, прорезь закрывают древесной либо железной воронкой, в дне которой сделаны отверстия диаметром 3—? мм. В воронку заливают клей, что через эти отверстия и поступает в цилиндр. В течение 5—10 мин лопасти шепетильно перемешивают стружку с клеем.
Готовая масса через отверстие внизу цилиндра поступает в коробку, а после этого ее подают на формирование
пакета. На время смешивания стружки с клеем отверстие закрывают задвижкой.
Формирование щитов осуществляется так. На рабочий стол помещают железную прокладку, на которую кладут облицовку щита, складывающуюся из двух страниц шпона либо страницы фанеры. В первом случае на прокладку укладывают первый лист шпона, а на него второй, с обеих сторон смазанный клеем.
В случае если облицовкой помогает фанера, то клей наносят лишь на внутреннюю ее сторону. После этого укладывают бруски каркаса и стягивают их сжимами. На каркас устанавливают древесную формировочную рамку, заполняют ее стружечно-клеевой массой, которую разравнивают рукой для того, чтобы уровень массы совпадал с уровнем формировочной рамки.
Затем рамку снимают и поверх стружки кладут вторую облицовку, подготовленную равно как и первую. Пакет накрывают железной прокладкой и подают на подъемный стол к гидравлическому прессу.
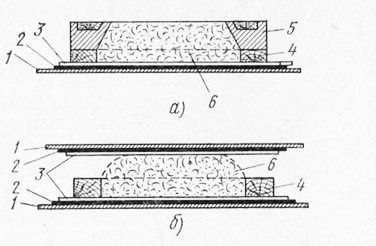
Рис. 1. Схема формирования пакетов мебельных щитов со стружечным заполнением: а, б — порядок операций; 1 — железные прокладки, 2 — чистовая облицовка, 3 —черновая облицовка, 4 — рамка щита, 5 — формировочная рамка, 6 — стружечное заполнение
По окончании того как пачка пакетов будет организована на подъемном столе, его устанавливают с таким расчетом, дабы верхний пакет был на уровне верхнего промежутка между плитами, и пакет заталкивают в пресс. После этого стол опускают до отметки следующего промежутка, заталкивают в пресс следующий пакет и т. д.
Прессование ведут с удельным давлением 5— 10 кгс/см2 при температуре плит пресса 120—140 °С.
Рис. 2. Схема конвейерной организации участка склеивания щитов со стружечным заполнением: 1 — распределительный конвейер, 2 — штабель с брусками для рамок, 3 — клеенаносящий станок, 4 — стопа черновых облицовок, 5 — стопа железных прокладок, 6 — стол для создания пакета, 7 — стопа чистовых облицовок, 8 и 9 — столы, 10— стол с формировочной рамкой, 11 — дозатор со стружечно-клеевой массой
Время прессования при данной температуре образовывает от 0,7 до 1 мин на 1 мм толщины готового щита. На рис. 2 продемонстрирована схема конвейерной организации участка склеивания щитов со стружечным заполнением. На участке установлен распределительный конвейер, воображающий собой стол, посредине которого движется цепь с упорами для движения формируемых пакетов.
Работа на конвейере осуществляется в таковой последовательности.
Из стопы берут железную прокладку и укладывают ее на стол. После этого кладут на прокладку лист строганого шпона из стопы и намазанный клеем на клеенаносящем станке лист лущеного шпона из стопы. Поверх намазанного клеем страницы укладывают бруски каркаса из штабеля и стягивают пружинными сжимами.
Собранный так пакет сдвигают на конвейер в позицию А. При передвижении пакета на конвейере из позиции А в позицию Б на пакет устанавливают формировочную рамку и насыпают в нее стру-жечно-клеевую массу из дозатора, расположенного над конвейером (на схеме условно продемонстрирован сбоку). После этого рамку снимают, и пакет поступает на позицию В. Тут поверх стружечно-клеевой массы укладывают лист шпона, смазанный клеем, сухой лист строганого шпона и железную прокладку.
Организованные так пакеты перемещаются к загрузочным подъемным столам и подаются в пресс. Склеенные щиты выгружаются на столы и отправляются на подстопные месга для выдержки.
Дозировочным устройством при подаче готовой смеси на стол для создания пакетов помогает формировочная рамка; массу насыпают и разравнивают вровень с поверхностью рамки. Формировочную рамку проектируют с таким расчетом, дабы ее внутренний количество, сложенный с количеством каркаса щита, вмещал при формировании по массе лишь то количество массы, которое нужно для создания щита данных размеров.
Высота формировочной рамки, а следовательно, и толщина засыпаемого слоя стружечно-клеевой массы зависят от требуемой плотности заполнения. К примеру, для плотности заполнения 0,35—0,45 г/см3 высоту формировочной рамки делают в 1,5—3 раза больше толщины брусков каркаса щита.
Уровень качества щитов со стружечным заполнением сильно зависит от верной дозировки количества клея и стружки при загрузке их в смеситель. Чем больше клея в смеси, тем прочнее получается щит. Но громадный расход клея экономически невыгоден.
Помимо этого, щиты с повышенным содержанием клея тяжелее обрабатывать, они посильнее подвергаются короблению и тяжелее по массе. В большинстве случаев к массе стружек додают около 10% смолы в пересчете на сухую массу.
Изготовление щитов с сотовым заполнением. Технологический процесс изготовления щитов с сотовым заполнением содержится в подготовке брусков каркаса, изготовлении сотового заполнения, склеивании и формировании щита.
Подготовка брусков каркаса складывается из поперечного раскроя и фрезерования заготовок на бруски нужных размеров.
Сотовое заполнение изготовляют следующим образом. На заготовки шпона с двух сторон наносят раствор карбамидного клея.
После этого страницы шпона помещают в сушильные камеры либо укладывают на стеллажи для подсушки клеевого слоя в условиях цеха. Длительность подсушки клеев К-17 и МФ при температуре 18—25 °С — 18—24 ч, клея М-70 — 4—8 ч, а при температуре 50—60 °С длительность подсушки указанных клеев образовывает соответственно 0,5—1,0 и 0,2—0,5 ч. По окончании подсушки страницы шпона раскраивают на гильотинных ножницах либо бумагорезательных автомобилях на полосы шириной 20— 30 мм.
После этого приступают к формированию пакета сотового заполнения. Пакет складывается из четного количества полос шпона и нечетного количества страниц оберточной либо второй подобной бумаги. Пакет собирают на особом приспособлении в таковой последовательности.
Лист бумаги разматывают с рулона и укладывают на крышку приспособления. Затем рабочий кладет между зубцами гребенок полосы шпона. В то время, когда полосы шпона будут уложены между всеми зубцами гребенок, их накрывают листом бумаги. После этого рабочий вручную сдвигает гребенки на заданный ход вправо либо влево и укладывает между зубцами гребенок второй последовательность полос шпона.
Так формируют целый пакет, в котором полосы шпона будут уложены в шахматном порядке между листами бумаги.
Организованные пакеты помещают между железными прокладками, загружают в пресс и прессуют при температуре плит пресса 100—130° С и удельном давлении 6—14 кгс/см2. Время прессования — 0,5 мин на 1 мм толщины пакета. По окончании выгрузки из пресса пакеты выдерживают в условиях цеха в течение 3 ч и после этого распиливают на круглопильных станках на заготовка. Высота заготовок должна быть на 0,5 мм больше толщины брусков рамки каркаса.
Готовые заготовки подают на формирование пакета щита.
Рис. 3. схема формирования пакета сотового заполнения: 1 — полосы шпона, 2— листы бумаги
Формирование щита реализовывают так. На рабочий стол помещают железную прокладку, на которую кладут облицовку щита, складывающуюся из двух страниц шпона либо страницы фанеры, либо древесноволокнистой плиты. В первом случае на прокладку укладывают первый лист шпона, а на него второй, с обеих сторон смазанный клеем. В случае если облицовкой слу-
Рис. 4. Сборка пакета сотового заполнения в приспособлении: 1 — гребенки, 2— листы бумаги, 3— крышка, 4 — полосы шпона
жит фанера либо древесноволокнистая плита, то клей наносят лишь на внутреннюю сторону фанеры либо плиты. После этого укладывают бруски каркаса, вовнутрь которого вправляют растянутое сотовое заполнение.
Края затянутого заполнения приклеивают к внутренним кромкам брусков каркаса глютиновыми либо вторыми быстросхватывающимися клеями. Затем поверх кладут вторую облицовку, подготовленную равно как и первая. Пакет накрывают железной прокладкой и подают на подъемный стол к гидравлическому прессу.
Склеивать элементы смоляными клеями возможно и холодным методом в прессах без обогрева. Выдержка в запрессованном состоянии образовывает в этом случае 3—5 ч.
По окончании распрессовки заготовки перед предстоящей обработкой выдерживают в свободном состоянии в условиях цеха не меньше 48 ч.
На рис. 6 продемонстрирована схема участка изготовления плосковыклейных элементов из шпона производительностью 800 штук в смену на базе полуавтоматической линии ПЛФМ-1. Работа на участке происходит в таковой последовательности.
Рис. 6. Схема участка изготовления плосковыклейных элементов из шпона: 1 — конвейер, 2,4 — подставки для заготовок шпона, 3 — клеенаносящий станок, 5 — рабочие столы, 6 — ленточный конвейер, 7— полуавтоматическая линия ПЛФМ-1, 8 — столы для склеенных элементов
С участка подготовки шпона заготовки поступают по конвейеру и на подставках подаются к рабочим местам. Клей на заготовки шпона наносится на клеена-носящих станках. Организованные на рабочих столах пакеты по ленточному конвейеру подаются к полуавтоматической линии.
Склеенные элементы кладут на столы и отправляют на подстопные места для выдержки.