Литейные свойства
Не все сплавы в однообразной степени пригодны для изготовления фасонных отливок. Из одних сплавов (оловянной латуни, силумина, серого чугуна и др). без особенного труда возможно взять отливки сложной конфигурации и соответствующих особенностей, из вторых (титановых легированных сталей, латуней и специальных бронз) получение отливок сопряжено с громадными технологическими трудностями.
Возможность получения доброкачественных тонкостенных отливок, сложных по форме либо громадных по размерам, беэ раковин, трещин, других литейных и пригара недостатков предопределяется литейными особенностями сплавов.
К литейным особенностям относят технологические особенности сплавов и металлов, каковые прямо и конкретно воздействуют на получение отливок заданной конфигурации, нужных эксплуатационных показателей, с поверхностями требуемой точности и чистоты размеров.
Проявляются они на протяжении заливки жидкого металла в форму и в ходе кристаллизации.
Значение литейных особенностей весьма громадно и должно быть учтено в следующих случаях:
1) при разработке и изыскании новых сплавов; направляться останавливаться на композициях, снабжающих самоё благоприятное сочетание рабочих (механических, физических и др). и литейных особенностей;
2) в ходе проектирования и создания отливки; долговечность и надёжность изделий в большой степени предопределяется литейными особенностями применяемого для их изготовления сплава;
3) на протяжении разработки технологического процесса изготовления отливок; в любых ситуациях при других равных условиях, направляться отдавать предпочтение сплавам с лучшими литейными особенностями.
Литейные свойства сплавов проявляются в жидком состоянии, при затвердевании, в жидко-жёстком и твердо-жидком и жёстком состояниях.
Номенклатура литейных особенностей в зависимости от общего производства развития и уровня сплавов техники может со временем изменяться. К фундаментальным литейным особенностям относятся следующие:
1) жидкотекучесть — свойство сплавов и металлов в жидком состоянии заполнять формы и совершенно верно воспроизводить в отливке ее очертания;
2) склонность к поглощению газов и образованию по данной причине недостатков в отливках:
3) склонность к образованию неметаллических включений;
4) усадка (объемная в жидком и жидко-жёстком состояниях, объемная и линейная в твердо-жидком и жёстком состояниях, а кроме этого при фазовых превращениях) и склонность к образованию усадочных пор и раковин;
5) склонность к ликвации;
6) склонность к образованию в результате первичной и вто-пичной кристаллизации макро- и микроструктуры;
7) склонность к образованию литейных напряжении и трещин.
Жидкотекучесть
Жидкотекучесть проявляется в способности сила и металлов вов в жидком состоянии течь по литейной форме, заполнять ее полости и четко воспроизводить все контуры отливки. Жидкотекучесть зависит от многих физических и физико-химических особенностей сплава и ее нельзя охарактеризовать какой-либо одной физической либо физико-химической константой.
Хорошая жидкотекучесть серьёзна при проведении комплекса мероприятий для получения плотных доброкачественных отливок (усиливает условия вывода за пределы отливки усадочных раковин, сокращает опасность образования всех видов пористости, трещин и т. д.).
При сравнении жидкотекучести разных сплавов и металлов предложено (Ю. А. Нехендзи) различать подлинную, нулевую и практическую жидкотекучесть.
Подлинная жидкотекучесть определяется при однообразном перегреве выше температуры нулевой жидкотекучести.
Нулевая жидкотекучесть наступает тогда, в то время, когда металл либо сплав перестает течь, пребывав лишь под статическим напором.
Нулевая жидкотекучесть сплавов наступает при температуре, лежащей в промежутке ликвидус-солидус, в момент, в то время, когда вязкость быстро возрастает благодаря образования заметного количества жёсткой фазы.
Практическая жидкотекучесть — это жидкотекучесть, измеряемая для разных сплавов при однообразной температуре заливки независимо от величины перегрева выше температур нулевой жидкотекучести и ликвидуса.
В производственных условиях тяжело установить температуру нулевой жидкотекучести, исходя из этого определяют жидкотекучесть сплава при однообразном перегреве выше температуры ликвидуса. Такую жидкотекучесть именуют «условно подлинной».
Природа жидкотекучести весьма сложна и зависит от многих факторов, каковые возможно поделить на три группы.
К первой группе относятся факторы, связанные со особенностями, и строением сплавов и металлов в жидком состоянии (природой сплава, вязкостью, поверхностным натяжением, наличием включений, изюминкой строения и кристаллизации образующейся жёсткой фазы, теплоемкостью, теплопроводностью и др.).
Известна определенная связь между характером кристаллизации и жидкотекучестью. Установлено, что при интенсивном развитии дендритной кристаллизации утрата жидкотекучести наступает кроме того при малом количестве жёсткой фазы.
Количество жёсткой фазы, при которой наступает нулевая жидкотекучесть, зависит от размеров и строения первичных кристаллов. К примеру, в простых условиях заливки нулевая жидкотекучесть чугуна и стали наступает соответственно при содержании 20 и 30% жёсткой фазы.
большинство и Чистые металлы эвтектических сплавов затвердевают с быстро очерченным фронтом кристаллизации и характеризуются лучшей жидкотекучестью, чем сплавы, образующие жёсткие растворы и кристаллизующиеся в промежутке температур. Тройные сплавы эвтектического состава владеют большей жидкотекучестью, чем двойные эвтектические сплавы.
Наличие в сплавах и металлах примесей может в одних случаях ухудшать жидкотекучесть, а в вторых — улучшать ее. Модифицирование время от времени существенно усиливает жидкотекучесть, а время от времени сокращает ее (к примеру, у сплавов совокупности Al-Si). Присутствие в алюминии малого количества железа, титана и кремния заметно ухудшает его жидкотекучесть.
Во всех сплавах легкоплавкие эвтектики улучшают жидкотекучесть.
Жидкотекучесть связана и со степенью переохлаждения. При заливке в железные формы заэвтектических алюминиевых сплавов отмечается громадная жидкотекучесть, чем у эвтектических. Как мы знаем, что вязкость любой жидкости зависит от наличия в ней суспензированных частиц (для литейных расплавов такими частицами смогут быть графит, окислы, карбиды, нитриды j т п.).
В соответствии с установленной А. Эйнштейном зависимостью’ вязкость жидкости увеличивается линейно с повышением количества (количества) суспензий и не зависит от их размера. направляться подчернуть, что сама по себе высокая вязкость жидкости не мешает заполнению формы. (Очень вязкий алебастр, а кроме этого пластмассы и малоподвижные смолы смогут прекрасно заполнять формы, в которых они растекаются под действием собственного веса.
Для этого требуется лишь достаточное время.) Жидкий металл в момент заливки в формы имеет вязкость, соизмеримую с вязкостью воды при простой температуре. Но благодаря громадной теплоотдаче жидкий металл скоро делается более вязким, в результате значительно уменьшается скорость его перемещения в форме.
Если бы удалось поддерживать большую температуру перегрева металла в течение всего времени перемещения его по каналам формы, то нетрудно было бы взять из довольно вязких литейных сплавов тонкие отливки. Экспериментально было обнаружено, что жидкотекучесть зависит от вязкости в меньшей мере, чем от промежутка кристаллизации сплава.
Свойство сплавов заполнять полости формы связана и с поверхностным натяжением. Чем больше поверхностное натяжение, тем меньшей жидкотекучестью владеет сплав. Значение поверхностного натяжения проявляется тем в большей степени, чем уже полость литейной формы.
Жидкотекучесть зависит кроме этого и от характера перемещения потока. При турбулентном перемещении она будет меньшей, чем при ламинарном. На практике жидкотекучесть определяют при помощи разных технологических проб и методов.
Применяемые способы возможно поделить на три группы. В первой группе фиксируют прекращение перемещения металла в сужающемся канале. Жидкотекучесть характеризуется линейными размерами заполненной либо незаполненной полости канала, к примеру клиновой пробы (рис. 2, а).
Прекращение перемещения жидкого металла может наступить в результате кристаллизации и в жидком состоянии под действием сил поверхностного натяжения. Во второй группе прекращение течения металла наступает благодаря кристаллизации его в узком сечении маленького канала. Величина жидкотекучести возможно оценена по массе металла, вытекшего от начала опробования до прекращения течения.
В пробах третьей группы фиксируют длину затвердевшей части металла в канале постоянного сечения. Известно большее разнообразие проб последней группы, каковые активно применяются в лабораторных исследованиях и производстве. Спиральную пробу (рис.
2, б) обширно используют для цветных жидкотекучести металлов и определения чугуна. Она складывается из чаши, фильтра, стояка, металлоприемника и спирального канала трапециевидного сечения с маленькими выступами.
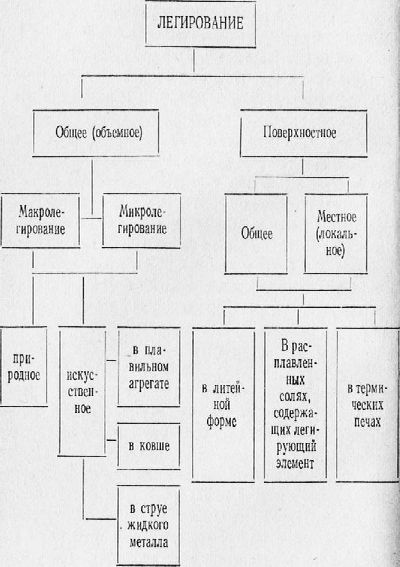
Рис. 2. Технологические пробы для определения жидкотекучести
Газы
Газы (так будем именовать элементы, существующие в простых условиях в природе в газообразном состоянии, независимо от формы существования в сплавах либо отливках) в литейных сплавах в одних случаях являются вреднейшими примесями, а в вторых употребляются для получения отличных плотных отливок и кроме того для улучшения последовательности особенностей (к примеру, прочности, твердости, жаропрочности и др.)
В сплавах и металлах газообразные элементы смогут находиться в следующих видах:
а) сферических включений (пузырей и газовых раковин);
б) жёстких химических соединений с элементами, входящими в состав сплава (окислов, нитридов, гидридов и др.);
в) жидких и жёстких растворов, в этом случае атомы газообразных элементов смогут размешаться между атомами главного металла либо войти (внедриться) в его кристаллическую решетку;
г) узких слоев, адсорбированных на поверхности металла либо сплава, к примеру, в чугуне адсорбция газов может происходить на поверхности графитовых включений, расположенных в толще железной матрицы.
Растворимость газов в сплавах и металлах в большой степени зависит от свойств и вида газа, природы растворителя, давления и температуры. Из особенностей газа на его растворимость громадное влияние оказывает молекулярное и ядерное строение.
В простых жидкостях увеличение температуры сокращает растворимость газов. В сплавах и жидких металлах растворимость газов с увеличением температуры может возрастать.
Процесс растворения газов в сплавах и металлах начинается с адсорбции, которая в большинстве случаев приводит к понижению поверхностного натяжения на границе раздела: жидкость — газ.
Поверхностная физическая адсорбция есть начальной стадией сорбционных процессов для большинства случаев сотрудничества в совокупностях жидкость-газ.
С увеличением температуры приобретает развитие процесс активированной адсорбции, являющейся предварительной стадией диффузии газов в металл. Данный вид адсорбции, характерный для большинства совокупностей металл — газ, отличается от простой повышением количества адсорбированного газа на поверхности адсорбента с увеличением температуры.
Теплота активированной адсорбции существенно превышает соответствующие размеры физической адсорбции и приближается к размерам теплоты химических реакций. В ходе активированной адсорбции молекулы адсорбируемого газа на поверхности адсорбента диссоциируют и смогут вступать с ним в химическое сотрудничество.
Громадное развитие приобретают процессы активированной адсорбции в совокупностях металл-водород.
Газы, адсорбируемые поверхностью металла в атомарном состоянии, диффундируют в металл. Процесс диффузии регулируется температурой, адсорбцией и давлением, величина которой, в собственную очередь, зависит от структуры металла и состояния поверхности- адсорбента. Чем больше активная поверхность адсорбента, тем громадным будет и количество диффундирующего газа.
В отличие от простых жидкостей в жёстких и жидких металлах растворимость газов с увеличением температуры возрастает. Это возможно растолковать тем, что растворение газов в металлах есть эндотермическим процессом. Вместе с тем, в некоторых случаях растворимость газов в металлах с увеличением температуры значительно уменьшается (к примеру, растворимость водорода в титане, цирконии, ванадии при увеличении температуры значительно уменьшается).
Процесс растворения газов в этих случаях есть экзотермическим.
Закон квадратного корня настоящ в случаях, в то время, когда двухатомный газ, адсорбируемый металлом, предварительно подвергается диссоциации с образованием двух атомов, растворяющихся независимо друг от друга, причем образуется раствор либо химическое соединение с одним атомом растворяющегося вещества в молекуле. Данный закон нельзя применять для газов из присутствующих в форме и металле недиссоциированных химических соединений, в молекулы которых входит более одного атома растворяющегося газа. Это же относится и к случаю, в то время, когда молекула, растворяясь в металле либо взаимодействуя с ним, распадается на много атомов,
На растворимость газов в металлах весьма воздействуют величина электроотрицательности и размерный фактор атомов металла и растворяющегося газа. С этим, к примеру, связывается разная творимость в сплавах и металлах водорода и азота. Азот от РаСорода отличается громадными высоким знанием и размерами атомов первого ионизационного потенциала. Азот, в большинстве случаев, Частворяется в металлах, с которыми он образует нитриды.
Р Скорость растворения газов в металлах зависит от агрегатного состояния металла либо сплава, его структуры, интенсивности перемешивания в плавильном агрегате, характера перемещения потока жидкого металла и т. п. Так, скорость растворения газа в жидком металле больше, чем в жёстком.
При перемещении металла небольшими струйками либо каплями в газовой среде растворяется больше газа, чем при перемещении потока газа над расплавленным металлом, находящимся под слоем шлака.
Турбулентный поток жидкого металла захватывает и растворяет при других равных условиях больше газа, чем ламинарный.
Барботаж жидкого металла газом может в одних случаях расширить содержание газов, а в вторых содействовать дегазации сплава.
изменения и Фазовые превращения сплавов и агрегатного состояния металлов смогут сопровождаться быстрым трансформацией растворимости азота в железе. Присутствие в металле разных примесей кроме этого значительно изменяет растворимость. На рис. 4 продемонстрировано влияние некоторых элементов на растворимость азота в железе, а на рис.
5 — связь растворимости между температуры и водорода в разных металлах.
Получение отливок без пористости и газовых раковин есть одной из самых тяжёлых задач литейного производства. Исходя из этого принципиально важно знать особенности не лишь растворения газов в металлах, но и обратного процесса — их удаления. Вероятны два случая зарождения газовых пузырей в количестве жидкого кристаллизующегося металла: гомогенное и неоднородное.
Рис. 3. Растворимость азота в железе 1, 2 — в жёстком и жидком алюминии; 3,4 — в жёсткой и жидкой меди; 5,6 — в жёстком и жидком железе; 7,8 — в жёстком и жидком никеле; 9, 10 — в жёстком и жидком магнии
Рис. 4. Влияние элементов на растворимость азота в железе
Рис. 5. Влияние температуры на растворимость водорода в разных металлах:
Расчеты говорят о том, что гомогенное зарождение газовых пузырьков в количестве жидкой (либо кристаллизующейся) стали (либо чугуна) вероятно в случае, в то время, когда появляется внутреннее давление порядка либо больше 2000 ат. Существенно легче и возможнее происходит неоднородное зарождение — газовые пузырьки появляются не в количестве жидкости, а на имеющихся поверхностях раздела, т.е. в местах, где нарушается сплошность строения жидкого металла. Такими местами смогут быть фронт кристаллизации, взвешенные неметаллические включения, появляющиеся в металле кристаллики, микроскопические газовые образования, стенки и подина плавильного агрегата, копильника, а кроме этого стены желоба литейного ковша, формы и т. п.
При громадных краевых углах смачивания работа образования зародышей пузырьков минимальна, и, следовательно, интенсивность их зарождения в жидком металле возрастает.
Форма газового пузырька, появляющегося на ровной горизонтальной поверхности, определяется соотношением межфазных натяжений на границах жёсткого тела с жидким расплавом и с газом, а кроме этого газа с жидким расплавом. В появившийся пузырь из одного газа смогут диффундировать в атомарном состоянии другие газы, поскольку их парциальное давление в данном пузыре фактически равняется нулю.
В пузырька атомы газов смогут ассоциировать в молекулы, чем обусловливается предстоящая диффузия этих газов вовнутрь пузырька. Достигнув определенного размера, пузырёк отрывается от поверхности зарождения и всплывает.
Всплывающие пузырьки, барботируя жидкий металл, содействуют повышению поверхности раздела фаз с высокой активностью и являются центрами газовыделения. Отдельные пузырьки газа при столкновении соединяются, что увеличивает скорость их всплывания.
Понижение температуры жидкого металла на протяжении кристаллизации сокращает растворимость газов в нем и повышает скорость дегазации. Но, происходящее наровне с этим повышение вязкости жидкого металла затрудняет удаление и подъём газов.
Введение в жидкий металл поверхностно-активных веществ может очень сильно оказать влияние на величину поверхностного натяжения и на межфазную энергию на поверхностях раздела, поменять краевой угол смачивания 0 и сказаться на росте и зарождении газовых пузырьков.
Определенную группу сплавов и металлов возможно использовать Для изготовления отливок лишь при условии отсутствия в них измеримого количества газов либо их следов. К ним относятся титан, цирконий, молибден, тантал, вольфрам, бериллий, уран.
Новые качественные характеристики сплавов совсем исключают возможность содержания в них водорода, азота и кислорода. В простых отличных литейных сплавах допускается незначительное содержание газов, но наряду с этим должны быть созданы условия, дающие предупреждение выделение их из раствора и образование газовых пористости и раковин.
Особенное внимание при приготовлении литейных сплавов должно быть обращено на чистоту шихтовых материалов. К примеру, в ходе плавки стали много водорода вносится в сталь с старой шихтой. В плавильный агрегат 1% ржавчины в шихте вносит около 2,5 м3 водорода на 1 т стали.
Многие ферросплавы тяжело высвободить от водорода кроме того при высокотемпературном прокаливании, к примеру ферромарганец около 1000° С может содержать до 30 см3/100 г. водорода, ферросилиций при данной же температуре — до 60 см3! 100 г. водорода, хром и никель — соответственно 8 и 12 см31100 г.
Меры, снабжающие минимальное содержание газов и дающие предупреждение образование газовых пористости и раковин в отливках, возможно поделить на три группы:
1) дегазация исходных шихтовых материалов, а кроме этого предупреждение поглощения газов металлами на протяжении плавки, при выпуске в ковш, заливке в формы и в ходе затвердевания отливки в форме;
2) дегазация жидкого металла перед заливкой в формы;
3) предупреждение выделения газов из раствора в ходе кристаллизации металла в форме.
Первая несколько мер охватывает фактически целый производственный цикл изготовление жидкого металла, кристаллизации и заливки форм. Она учитывает состояние шихтовых материалов, свойства жидкого и жёсткого металла, ведение процесса плавки по оптимальному режиму, конструкцию литниковой совокупности, свойства формы и т. п. Меры первой группы являются неспециализированными для всех сплавов, но использование на практике их должно быть дифференцированно для различных сплавов в зависимости от требований, предъявляемых к отливкам, и от склонности сплава к газопоглощению, а кроме этого, от разности растворимости газа в жёстком и жидком металле.
К первой группе мер относят подбор и подготовку качественных шихтовых материалов, вакуумирование и сушку их до загрузки в плавильный агрегат, ведение плавки в условиях той либо другой среды (вакуума, защитной воздуха), разные способы дегазации в ходе плавки и перед выпуском готового сплава из печи в ковш. Среди способов первой группы, разрешающих взять металл с низким содержанием газов, громадный интерес воображает дуговая плавка с расходуемым электродом.
Жидкий металл, отделяясь от электрода под действием силового электромагнитного поля, распадается на отдельные капли, из которых в вакууме благодаря громадной поверхности появившихся капель и большой температуре в территории дуги интенсивно выделяются газы. Не обращая внимания на большую дегазацию сплава в вакууме, отсутствие регулирования времени нахождения в нем капель металла исключает возможность полного удаления газов.
Второй метод получения более чистых по содержанию газов металлов содержится в том, что в намерено сконструированного индуктора помещают металлы, каковые поддерживаются во взвешенном состоянии в электромагнитном поле и нагреваются токами высокой частоты до плавления. Жидкий металл в этом случае имеет форму капли.
Особенная сокровище для того чтобы способа плавки в том, что металл возможно не лишь расплавить в вакууме без контакта с тиглем, но и сходу залить в форму, чего нельзя осуществить в дуговой печи. Для плавки громадных порций важных сплавов применяют высоковакуумные индукционные печи, в которых в ходе плавки происходит дегазация. Удалению газов наровне с вакуумом содействует и энергичное перемешивание сплава под действием электромагнитного поля.
Вторая несколько мер предусматривает создание условий для дегазации сплавов вне плавильного агрегата. К ним направляться отнести вакуумирование сплава вне плавильного агрегата (в ковше либо на протяжении разливки), разливку в вакууме, выдержку перед разливкой с медленным охлаждением и последующим стремительным подогревом, простую выдержку, фильтрацию, введение в расплав элементов, реагирующих с растворенным газом и образующих негазообразные продукты, продувку расплава газами (к примеру, аргоном, хлором, молекулярным азотом), другие методы и ультразвуковую обработку физического действия.
Для изготовление особых тугоплавких сталей и сплавов применяют комплекс мер, относящихся к первой и второй группам (вакуумную плавку, разные способы вакуумной дегазации, разливку в вакууме и т. п.).
Определенные мероприятия, целью которых являются удаление и дегазация нежелательных неметаллических включений, вошли в технологические процессы плавки. К примеру, раскисление при выплавке сталей и многих цветных сплавов, «кипение» при выплавке стали, «дразнение» при выплавке меди и бронзовых. сплавов, выдержка сплавов в печи и в ковше, и т. д.
К третьей группе мер относится способ кристаллизации под давлением, созданный А. С. Бочваром и А. Г. Спасским для отливок из легких сплавов. Способ основан на том, что при повышенном давлении (4-5 am), создаваемом над кристаллизующимся в форме сплавом, в растворенном состоянии в металле может остаться больше газов, чем при атмосферном давлении. Исходя из этого над формами по окончании заливки в автоклаве создают повышенное давле-ние, поддерживаемое до окончания затвердевания металла.
Подобно большому давлению при кристаллизации действует Ускоренное охлаждение. Задержать газовыделение из раствора До перехода в жёсткое состояние и предотвратить образование газо-раковин в отливках может и повышенная скорость охлаждения промежутке кристаллизации. Помимо этого, повышенная скорость хождения есть благоприятной еще и вследствие того что обеспе-Вает громадный температурный градиент по сечению отливки
Литейное производство в период кристаллизации. Это сокращает слой, в котором протекает кристаллизация в этот момент. Исходя из этого газы, успевшие выделиться из раствора, смогут легче и стремительнее уйти через жидкость в область, где сосредоточены усадочные раковины, каковые при верном технологическом ходе выводят в прибыли.
Само собой очевидно, что это частный случай для условий, в то время, когда фронт кристаллизации не опережает газовыделение.
Неметаллические включения
Неметаллические включения в затвердевшем сплаве являются телами, нарушающими единообразие и сплошность его структуры. Жёсткие неметаллические включения довольно часто имеют края и острые углы, в которых образуются большие концентрации напряжений. Тугоплавкие для данного сплава включения, температура плавления которых превышает температуру плавления данного сплава, в большинстве случаев находятся в кристаллов.
Легкоплавкие включения входят в эвтектические «сетки» и находятся по границам зерен, довольно часто приводя к красноломкости либо хрупкости. Неметаллические включения смогут неблагоприятно сказаться и на процессах вторичной кристаллизации.
Кое-какие включения смогут уменьшать химическую стойкость сплавов, поскольку они образуют с главным металлом сплава коррозионные гальванические пары, содействующие формированию электрохимических процессов коррозии.
Различают три главных источника неметаллических включений в сплавах и металлах.
1) Неметаллические включения смогут появляться благодаря изюминок технологического процесса изготовление сплавов и их последующей кристаллизации. К примеру, растворимость элементов, образующих включения, зависит от температуры: чем выше температура, тем больше концентрация [элементов в растворе.
При понижении температуры кристаллизации эти элементы выделяются из раствора в виде небольших частичек и самостоятельно либо, соединившись с вторыми компонентами сплава, образуют неметаллические включения. Часть неметаллических включений постоянно имеется в шихтовых материалах и может остаться в сплаве.
2) Источником неметаллических включений смогут быть химические реакции, происходящие в сплаве в результате целенаправленного процесса удаления нежелательных примесей (к примеру, раскисления и др.). В следствии таких реакций образуются нерастворимые в расплаве вещества (к примеру, окислы, нитриды и др.). Вероятно и образование окисных включений в ходе разливки в результате вторичного окисления.
3) Источником неметаллических включений в отливках смогут быть частицы шлака, футеровки печей, желобов, ковшей, а кроме этого литейной формы и литниковой системы.
Количество удаляемых неметаллических включений при продувке расплава нейтральным газом тем больше, чем меньше пузырьки продуваемого газа.
При фильтрации сплав пропускают через пористую среду, которая может или неметаллические включения, или задерживать их благодаря химического сотрудничества с ними. Для успешного осуществления процесса фильтрации нужны предварительный подогрев материала фильтра либо создание над фильтрующимся сплавом вакуума.
В качестве материалов фильтра для фильтрации легких сплавов используют синтетический корунд, глинозем, обожженный чистый магнезит, циркон, карбид кремния и т. п.
Фильтрацию возможно совместить с продувкой жидкого сплава нейтральным газом. В этом случае наровне с удалением неметаллических включений достигается и определенная степень дегазации.