Материалы на основе неорганических вяжущих веществ
Материалы на базе неорганических вяжущих веществ приобретают в следствии затвердевания смеси, складывающейся из минерального вяжущего заполнителей и вещества. Обжигу эти материалы не подвергаются. В качестве заполнителей применяют песок, щебень, шлак, пемзу, древесные опилки, стружку, асбест, другие отходы и бумажную макулатуру разных производств.
Введение заполнителей снижает расход вяжущего вещества и усиливает свойства готовых изделий (сокращает объемную массу, усадку, деформацию, теплопроводность, повышает пористость, а при применении волокнистых заполнителей быстро возрастает прочность при изгибе и растяжении и т. д.).
применение и Производство в строительных работах этих материалов из года в год расширяется. По своим особенностям они не уступают вторым материалам, а для изготовления их употребляются недорогие местные материалы. На базе минеральных вяжущих получаются разнообразные материалы, обширно используемые для фундаментов, пролетных конструкций, стен, перегородок, кровли, облицовки и т. д.
Производство этих материалов складывается из подготовки вяжущих заполнителей и вещества; смешивания их, формования изделий; окончательной отделки и твердения.
Твердение материалов на базе воздушных вяжущих веществ происходит на воздухе, а на базе гидравлических — во мокрой среде. Цикл производства изделий 6—72 ч.
Материалы на базе воздушной извести (силикатные). На базе воздушной извести приобретают: кирпич силикатный, известково-шлаковый и зольный, облицовочные плиты, пеносиликатные изделия и др.
Силикатный кирпич представляет собой ненатуральный камень в форме прямоугольного параллелепипеда. Изготовляют его из смеси воздушной извести (5—8%) и кварцевого песка (92— 95%). Для его производства используется быстрогасящаяся известь с содержанием магния и оксидов кальция не меньше 70%. Песок должен иметь зерна разной размера и формы с незначительными примесями и шероховатой поверхностью глины, слюды и др.
Известь по окончании тщательного смешивания с водой подвергается гашению в барабанах либо силосах. Менее распространенным есть силосный метод. При первом методе гашение производится в барабане под влиянием пара и воды при температуре около 100 °С.
По окончании гашения из извести формуют кирпич прессованием под давлением 15,0—20,0 МПа. Наряду с этим частицы извести сближаются с зернами песка, что содействует их химическому сотрудничеству. По окончании формования кирпич запаривают в автоклавах под давлением 0,8 МПа и температуре 175°С в течение 8— 10 ч. При запаривании происходит химическое сотрудничество гидроксида кальция с кремнеземом с образованием гидросиликата по реакции:
Са(ОН)2 + Si02 = СаО • Si02 + Н20
Кристаллы гидросиликата кальция срастаются между собой и с зернами кварца, придавая кирпичу большую прочность. Прочность кирпича увеличивается и на воздухе за счет сотрудничества оставшегося гидроксида кальция с углекислым газом с образованием карбоната кальция, что повышает кроме этого водо- и морозоустойчивость кирпича. Силикатный кирпич выпускается размером 250X X 120X65 (либо 88) мм, шести марок: 7,5; 10,0; 12,5; 15,0;20,0и25,0 как пустотелым, так и полнотелым.
Объемная масса кирпича 1800—1900 кг/м3, водопоглощение 8—16%, морозоустойчивость не меньше 15 циклов. Кирпич в большинстве случаев не редкость светлосерого цвета, но возможно и цветным, в случае если ввести в известково-песчаную смесь красители.
Силикатный кирпич используется для кладки стен жилых и административных строений. Для кладки печей, дымовых труб, фундаментов, и стен бань и прачечных данный кирпич использовать запрещено. При повышенной влажности карбонатная пленка разрушается и образуется растворимый бикарбонат кальция (СаНСОз)2, а при большой температуре происходит дегидратация гидроксида кальция с понижением прочности.
При автоклавной обработке смеси молотой негашеной извести (6—10%), молотого песка (8—15%) и простого кварцевого песка (70—80%) приобретают силикатные бетоны, каковые бывают тяжелыми с объемной массой более 1800 кг/лёгкими3 кг и — 500— 1800 м/м3. По прочности на сжатие (МПа) они делятся на марки от 10 до 40, по морозоустойчивости на три марки: 15, 25 и 30. Изделия на их базе смогут быть как с простой, так и предварительно натянутой железной арматурой .Используют их в виде блоков и панелей для стенку, панелей и настилов перекрытий и т. д.
Известково-шлаковый кирпич получается при затвердевании смеси воздушной извести (3—12%) с гранулированным доменным шлаком. размеры и Производство этого кирпича подобны силикатному. Объемная масса его 1400—1600 кг/м3. По прочности на сжатие (МПа) делится на три марки: 2,5; 5 и 7,5; морозоустойчивость его не меньше 10 циклов. Используется кирпич для кладки стен строений высотой не более трех этажей либо стен верхних этажей высоких строений.
Благодаря малой теплопроводно-ности известково-шлакового кирпича кладка стен из него возможно в 1,5—2 кирпича.
Облицовочные плиты изготовляют из песка и смеси извести с добавкой 7,5% портландцемента запариванием и прессованием в автоклавах. Они используются для облицовки стен жилых и административных строений. Производят плиты рядовые и угловые.
Рядовые плиты имеют размеры 194X219 и 294X394 мм при толщине 30 мм. Прочность их на сжатие 20—30 МПа, водопоглощение не более 16%, а морозоустойчивость не меньше 25 циклов. Они имеют ровную поверхность в большинстве случаев белого цвета, но смогут выпускаться и цветными.
Пеносиликатные изделия приобретают при затвердевании смеси, складывающейся из пены, извести и песка. Пену приобретают методом перемешивания в мешалках с водой столярного клея и канифоли. Для увеличения активности песок подвергают узкому помолу. Взятую однородную массу разливают в железные формы и направляют на твердение в автоклав. Наряду с этим получается высокопористый материал с объемной массой 300—1200 кг/м3, прочностью на сжатие около 20 МПа и малой теплопроводностью.
Изделия из пеносиликатной массы используют в качестве конструкционного либо теплоизоляционного материала для кладки либо утепления стен и перегородок. К пористым силикатным изделиям относится кроме этого теплоизоляционный материал — газосиликат с объемной массой 300—900 кг/м3 и прочностью на сжатие 1,5—10,0 МПа. Используется он для тепловых агрегатов и теплоизоляции помещений.
Материалы на базе гипсобетона и гипса. Из смеси гипсовых вяжущих заполнителей и веществ (3—40%) приобретают обшивочные страницы, панели и перегородочные плиты, гипсобетонные камни, и архитектурно-декоративные изделия (карнизы, розетки и др.). В качестве заполнителей применяют: шлак, кирпичный щебень, пемзу, бумажную макулатуру, солому и др., каковые улучшают свойства изделий.
Для уменьшения объемной повышения и массы теплозащитных особенностей в смесь вводят пену либо пенообра-зующие добавки; для уменьшения хрупкости древесную стружку, волос, бумажную массу и др. Изюминкой их есть то, что они получаются с ровной поверхностью, не требующей дополнительной обработки, имеют малую объемную массу, достаточную прочность и низкую тепло- и звукопроводимость.
Эти материалы не являются водостойкими и используются лишь в сухих помещениях с относительной влажностью воздуха не более 60%. Они легко обрабатываются режущими инструментами и окрашиваются в разные цвета. Для изготовления материалов на базе гипсобетона и гипса употребляется строительный гипс. Производство их складывается из изготовление гипсового теста либо раствора, сушки и формования изделий при температуре не выше 130—150°С.
Продолжительность процесса производства гипсовых изделий образовывает всего лишь пара часов.
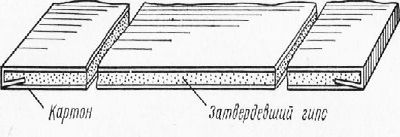
Рис. 1. Обшивочные гипсовые страницы
Обшивочные гипсовые страницы (сухая гипсовая штукатурка) (рис. 1) изготовляют из пеногипсовой смеси (с добавками либо без них) на особых автомобилях. Состоят страницы из двух слоев картона, между которыми находится слой затвердевшего и прочно соединенного с картоном гипсового теста. Обшивочные страницы производят длиной 2500—3300 мм, шириной 1,2 и 1,3 м и толщиной 10 и 12 мм.
По наличию отклонений и дефектов от размеров страницы делятся на два сорта: 1-й и 2-й.
Используются они для отделки внутренних стен и потолков сухих помещений. Стенки помещений по окончании обшивки страницами возможно оклеивать обоями либо окрашивать краской. Выпускаются страницы кроме этого с отделанной поверхностью. Недочётом их есть по-зышенная большой расход и хрупкость картона. Для устранения хрупкости в исходную смесь вводят измельченную солому, бумажную макулатуру и др., каковые, переплетаясь между собой, образуют как бы каркас. Приобретаемые страницы именуют гипсоволокнистыми.
Они если сравнивать с простыми владеют большей прочностью, выпускаются без картона и имеют меньшую себестоимость.
Перегородочные гипсовые плиты изготовляют из гипсового раствора либо бетона, целыми либо пустотелыми. Для увеличения прочности их подвергают уплотнению. По окончании формования их подвергают сушке — твердению. Производят их длиной 80 см, шириной 40 см и толщиной 80 и 100 мм; прочность на сжатие не меньше 5,0 МПа. Используются они для устройства внутренних перегородок и стен.
В районах с жарким, сухим климатом эти плиты употребляются для наружной отделки строений.
Гипсобетонные камни изготовляют целыми либо пустотелыми. Размер их: протяженность 50—70 см, ширина около 20 см и толщина 19—25 см. По прочности на сжатие они делятся на марки: целые — 3,5; 5; 7,5 и 10; пустотелые — 3,5; 5 и 7,5. Используются такие камни для устройства внутренних стен и перегородок сухих помещений.
При сухом климате их возможно применять кроме этого и для кладки наружных стен.
Перегородочные панели изготовляют из смеси гипса с заполнителями (шлак, песок, опилки, льняная костра и др.) способом проката на особых станах. Они имеют ровную поверхность, не требующую дополнительной отделки, правильные размеры по длине и толщине, владеют звуко- и теплоизоляцией, достаточно огнестойки. Панели производят длиной до шести метров, шириной до 3,1 м, толщиной 8—12 см; прочность на сжатие 3,5 МПа.
Употребляются они для устройства межкомнатных и межквартирных перегородок, внутренней облицовки стен, санитарно-вентиляционных коммуникаций и технических кабин.
Материалы на базе магнезиальных вяжущих веществ. Главными из них являются фибролит и ксилолит. Они имеют малую объемную массу, малую теплопроводность, большую прочность на истирание и сжатие и низкую влагостойкость.
Использовать их возможно в качестве звуко- и теплоизоляционных и отделочных материалов в сухих помещениях.
Ксилолит получается в следствии затвердевания смеси каустического магнезита либо древесных опилок и доломита в соотношении 1 : 3. Для увеличения сопротивления истиранию в смесь вводят асбест, другие добавки и тальк, а для получения цветного материала —пигменты (значительно чаще мумию, металлический сурик, охру и др.). Ксилолит имеет объемную массу 1000—1250 кг/м3, прочность при сжатии 30,0—40,0 МПа, при растяжении 3,0—5,0 МПа, коэффициент теплопроводности 0,23—0,29 Вт (м-К).
Используется ксилолит для устройства бесшовных ксилолитовых полов по жёсткому основанию (цементному, древесному) в сухих помещениях. Для увеличения влагостойкости их направляться покрывать олифой либо натирать особой мастикой с воском. Из ксилолитовой пены изготовляют способом прессования плитки для полов 20X20 см и 15?15 см, подоконники и лестничные ступени.
подоконники и Лестничные ступени изготовляют двухслойными, верхний слой — с мелкими опилками и минеральными наполнителями, а нижний слой — с более большими опилками.
Фибролит относится к теплоизоляционным материалам.
Материалы на базе цемента. К ним относятся изделия и материалы, каковые получаются в следствии других смеси видов и затвердевания портландцемента цементов с минеральными заполнителями. Они характеризуются большой прочностью, химической и морозоустойчивостью и используются в качестве несущих, конструкционных, кровельных и других материалов.
По виду исходного сырья они делятся на асбестоцементные материалы, приобретаемые из смеси цемента, асбеста и воды, и материалы из бетонов и растворов, приобретаемые из смеси цемента с небольшими либо большими заполнителями и воды. К последним относятся и бетонные изделия.
Асбестоцементные материалы изготовляются из смеси асбеста (10—18%), портландцемента (82—90%) и воды.
Асбест — это порода волокнистого строения, легко разделяется (распушивается) на отдельные волокна, напоминая вату. Он не горит, но при температуре 670—700°С теряет химически связанную воду, делается хрупким и непрочным, а при температуре 1550°С плавится.
Волокна асбеста владеют большой прочностью при растяжении— 60—90 МПа и адсорбционной свойством, прекрасно удерживают зерна цемента. Волокна асбеста образуют армирующую сетку, что и обусловливает большую прочность асбестоцементных материалов. Асбест употребляется коротковолокнистый — 3-го и 6-го сортов.
Цемент для них используется марок 40 и 50, узкого помола, с ограниченным содержанием трехкальциевого силиката и трехкальциевого алюмината. В случае если содержание указанных минералов будет меньше установленного предела, то процесс затвердевания изделий будет протекать медленнее. При большем содержании в цементе трехкальциевого алюмината готовые изделия будут химически нестойкими.
Производство асбестоцементных изделий складывается из распуши-вания асбеста, смешивания его с водой и цементом, твердения и формования изделий их во мокрых условиях либо в автоклавах под давлением и при повышенной температуре.
Уровень качества готовых изделий зависит и от направления волокон асбеста, которое должно совпадать с направлением появляющихся в материале упрочнений. Асбестоцементные изделия имеют большую морозостойкость и химическую прочность, малую теплопроводность и маленькую объемную массу. Химическая стойкость изделий разъясняется тем, что цемент находится в адсорбированном волокнами асбеста состоянии.
Из асбестоцементных изделий громаднейшее использование в строительных работах им,еют страницы (рис. 2) и фасонные подробности к ним, муфты и трубы, санитарно-технические подробности и т. д.
Асбестоцементные страницы изготовляют из смеси асбеста (18%), цемента (82%) и воды. Они выпускаются трех профилей— обычного (О), усиленного (У) и средневолнистого (СВ). Страницы усиленного профиля отличаются от обычных толщиной и большими размерами; используются они для кровли промышленных сельскохозяйственных строений и зданий.
Обрешетка для них устраивается редкая. Для большей прочности на изгиб страницы имеют продольные волны. По форме страницы различают волнистые, полуволнистые и плоские.
Рис. 2. Асбестоцементные кровельные материалы: а — страницы: 1 — полуволнистые; 2 — волнистые; б — фасонные подробности: 3 — конек; 4 — тройник; 5, 6 — уголки
Волнистые страницы обычного профиля с шестью продольными волнами производят длиной 1200 мм, шириной 678 мм и толщиной 5,5 мм. Страницы усиленного профиля имеют длину 1750 и 2000 мм, ширину 1130 мм и толщину 6—7,5 мм.
Полуволнистые страницы бывают рядовыми, сливными и коньковыми и имеют длину соответственно 1800 и 1200 мм, ширину 553 мм и толщину 6 мм.
Водопоглощение страниц должно быть не более 30%, морозоустойчивость не меньше 25 циклов, прочность на изгиб не меньше 16 МПа. Волнистые страницы имеют громадную жесткость, чем полуволнистые.
Используются волнистые и полуволнистые страницы для кровли, и для облицовки стен жилых и публичных сооружений. Они не горят, не гниют, не требуют периодической покраски. Смогут быть использованы и в качестве теплоизоляционного материала.
Укладываются они на редкую обрешетку и крепятся шиферными гвоздями, болтами либо особыми кляммерами.
Плоские страницы производят двух видов: непрессованные (Б) и прессованные (А). Размеры их: протяженность 600—1600 мм, ширина 300—1200 мм и толщина 6—10 мм. Водопоглощение страниц непрессованных не более 30%, прессованных не более 21%, прочность на изгиб соответственно не меньше 15 и 23 МПа.
Используются плоские страницы для обшивки и облицовки наружных и внутренних стен, и потолков и перегородок. Для облицовки помещений с повышенной влажностью (санузлов, кухонь и др.) используются страницы, покрытые влагонепроницаемым слоем. В наборе с страницами производят уголки, другие детали и лотки, каковые используют для кровли в местах пересечения (скатов, труб, слуховых окон).
муфты и Асбестоцементные трубы к ним изготовляют из асбестоцементной смеси на особых автомобилях. Твердеют трубы сперва в водных бассейнах при температуре около 45°С, а после этого на складе. Для сокращения срока твердения обработку труб создают и в автоклавах.
Если сравнивать с железными эти трубы имеют меньшую массу, высокую химическую стойкость, малую теплопроводность, громадную пропускную свойство и не разрушаются блуждающими в почве токами. По назначению асбестоцементные трубы делятся на водопроводные (водонапорные) и канализационные (безнапорные).
Водопроводные трубы трудятся под давлением и имеют прочность и большую толщину стенок. По величине рабочего давления (атм) они делятся на марки ВТ-3, ВТ-6, ВТ-9 и ВТ-12, водопроводные трубы производят размером: протяженность 2950 и 3950 мм, толщина стенок 9—43 мм, внутренний диаметр 50—450 мм. Они должны выдерживать давление вдвое болыце рабочего.
Используются они для устройства водопроводных и других напорных коммуникаций. Для соединения их между собой производят особые муфты. Трубы марок ВТ-3 и ВТ-6 соединяются асбестоцементными муфтами соответствующих марок длиной 150— 200 мм, рассчитанных на то же давление., что и трубы. Для соединения труб марок ВТ-9 и ВТ-12 используются чугунные муфты.
Для уплотнения в наборе с муфтами и трубами поставляются резиновые кольца.
Канализационные трубы имеют меньшую толщину стенок и вычислены на давление не более 3—4 атм. Производят их двух видов: раструбные (КР) и муфтовые (КМ). Муфтовые соединяют между собой посредством асбестоцементных муфт марки МК. Трубы КР на одном финише имеют раструб, в который входит финиш второй трубы без раструба.
Канализационные трубы производят размером: протяженность 2500—4000 мм, толщина стенок 7—18 мм и внутренний диаметр 44—570 мм. Используются они для устройства внутренней и наружной безнапорной канализации, водостоков, мусоропроводов, дымоходов и т. п. При устройстве коммуникаций они смогут совмещаться с деталями и чугунными трубами.
Материалы из бетонов и растворов. Эти материалы получаются в следствии затвердевания смеси портландцемента с мелким заполнителем и водой. Чтобы получить бетон, к раствору дополняют большой заполнитель (щебень либо гравий).
Готовые конструкции и бетонные детали владеют большой прочностью, морозо- и влагостойкостью и другими нужными особенностями. Применение их и постройке быстро уменьшает древесины и расход металла, усиливает уровень качества, снижает стоимость и сроки строительства, и позволяет применять на постройке технические средства.
Выпускаются цементные и бетонные подробности в готовом виде, а время от времени и с совсем отделанной лицевой поверхностью. Изготовляют их как на больших механизированных, так и на маленьких фирмах, обслуживающих один строительный объект.
Номенклатура цементных и бетонных конструкций и деталей разнообразна. Используются они по большей части в массовом жилищном и промышленном постройке.
Камни цементные и шлакобетонные изготовляют из смеси цемента, песка, щебня либо гравия и воды. Для понижения объемной повышения и массы звуко- и теплоизоляционных особенностей используют легкие заполнители (шлак, туф). Камни имеют верную ровную поверхность и прямоугольную форму. Производят их целыми и пустотелыми.
Размеры камней (мм): протяженность 390— 590, толщина 90—190 и ширина 133—188. По прочности на сжатие (МПа) они делятся на марки: 3,5; 5; 7,5; 10; 15 и 20; камни с пористыми заполнителями выпускаются низких марок: 3,5; 5; 7,5 и 10.
По назначению камни подразделяются на следующие виды: камни для стенку, перегородок и фундаментов и фасонные камни. Из цементной смеси с плотными заполнителями получаются водо- и морозостойкие камни с повышенной прочностью, каковые используются для кладки фундаментов и стен низких строений (один-два этажа). Из цементной смеси с пористыми заполнителями получаются камни с меньшей объемной массой (до 1600 кг/м3) и повышенными тепло- и звукозащитными особенностями.
Такие камни используются для устройства перегородок между квартирами и в квартир. Фасадные камни в отличие от первых имеют более сложную форму, приятный внешний вид, более правильные размеры и высокую атмосферостойкость. Они используются для кладки стен и карнизов, для отделки зданий и наружной облицовки, и для архитектурно-художественного оформления.
Блоки фундаментные производят длиной до трех метров, высотой до 60 см и шириной 40—60 см. Их армируют лишь монтажной арматурой. Прочность на сжатие не меньше 15 МПа.
Используются они для кладки стен подвалов крупноблочных и крупнопанельных сооружений и зданий. Для соединения их между собой на торцовой стороне имеются пазы, заполняемые раствором.
Бетонные изделия приобретают на базе бетонов прочностью на сжатие не меньше 20—30 МПа, а для предварительно напряженных — не меньше 40 МПа. Для армирования их используют металлическую проволоку и горячекатаные и холодносплющенные стержни ровного либо периодического профиля. Главными из бетонных изделий являются: фундаментные плиты, изделия для каркасов, стеновые панели, стеновые блоки, плиты для междуэтажных перекрытий, площадки и лестничные марши, трубы, шпалы, изделия и конструкции для инженерных сооружений и промышленных зданий, блок-помещения и др.
Плиты фундаментные, армированные железной сеткой, выпускаются длиной 80, 100 и 120 см, высотой 40—50 см и шириной 120—320 см. Они имеют трапецеидальную форму.
К изделиям для каркасов относятся колонны, ригели, прогоны и др. Колонны выпускаются длиной, равной высоте двух этажей.
Стеновые панели бывают для наружных и внутренних стен как отапливаемых, так и неотапливаемых строений, для перегородок. Для увеличения теплозащитных особенностей применяют пористые заполнители. Панели производят толщиной 16—40 см, с облицованной либо необлицованной поверхностью, с проемами для дверей и окон либо без них.
Стеновые блоки производят целыми и пустотелыми с объемной массой до 1600 кг/м3, прочностью на сжатие 5—20 МПа и морозоустойчивостью не меньше 15 циклов. Для монтажа стен наровне с блоками применяют кроме этого простеночные, подоконные и перемычные подробности.
Для междуэтажных перекрытий производят панели и настилы с круглыми либо круглыми вакуумами. Протяженность их 6 м, ширина 80— 1500 мм и толщина 200—220 мм. Удачнее для этого использовать изделия с предварительно напряженной арматурой.
Панели производят стандартных размеров для перекрытия полов и потолков.
Из конструкций для промышленных строений громаднейшее использование находят колонны, балки, фермы. Колонны бывают двух-консольными, одноконсольными и бесконсольными. Изготовляются они с простой и предварительно напряженной арматурой из тяжелого бетона прочностью не ниже 30—40 МПа.
Балки для перекрытий производят прямоугольного, таврового и двутаврового сечений разной длины. Для перекрытия пролетов шириной 18 м используют арки и специальные фермы. Для инженерных сооружений (ЖД, дорог , тоннелей, аэропортов и др.) используют разные тюбинги, плиты с большой прочностью (не меньше 30—40 МПа), высоким сопротивлением истиранию и морозоустойчивостью (не меньше 100 циклов).
В транспортном постройке применяют шпалы, стойки для линий связи (длиной 10—15 м).
В строительных работах широкое использование находят кроме этого бетонные трубы, аэродромные плиты, бортовые камни, опоры для светильников, заборы, ограды и многие конструкции и другие изделия.
Бетоны. К бетонам относятся неестественные каменные материалы, приобретаемые при затвердевании смеси, складывающейся из вяжущего вещества, воды и заполнителей (небольших и больших). В качестве небольшого заполнителя употребляется песок, большого — щебень либо гравий.
Состав бетона зависит от назначения и условий получения.
Бетон есть наиболее значимым стройматериалом и активно используется в разных видах строительства. Из него изготовляют разные подробности, конструкции и изделия, использование которых разрешает механизировать строительные работы, повысить производительность труда и снизить их себестоимость. Цементные изделия экономически удачны, поскольку для их изготовления употребляются недорогие каменные материалы (до 85%).
Они смогут быть изготовлены форм и разных размеров с разными особенностями, видом и характером отделки.
Бетон, имеющий железную арматуру, именуется железобетоном. В нем удачно сочетаются большая прочность металла на растяжение и большая прочность бетона на сжатие.
Бетоны классифицируют по виду вяжущего вещества, назначению и объёмной массе. По виду вяжущего бетоны бывают: цементные, силикатные (на базе извести), гипсовые и полимерце-ментные. Полимерцементный бетон приобретают с применением полимерных добавок.
По величине объемной массы (кг/м3) бетоны делятся на четыре вида: очень тяжелые (более 2500), тяжелые (1500—2500), легкие (500—1800) и очень легкие с объемной массой менее 500 кг/м3.
По назначению бетон подразделяется на конструкционный и особого назначения.
Конструкционный бетон в виде разных подробностей, конструкций и изделий используется для гражданских и сооружений и промышленных зданий. По прочности на сжатие (МПа) и морозоустойчивости (в циклах) бетоны делятся на марки. Прочность на морозостойкость и сжатие бетона зависят от вида вяжущего, объёмной массы и природы заполнителей.
Тяжелые бетоны, к примеру, имеют прочность 20—120 МПа и морозоустойчивость 15— 300 циклов. Легкие бетоны имеют прочность на сжатие 1,5— 30 МПа, а морозоустойчивость 10—200 циклов.
Для получения тяжелых бетонов используют цементы большой прочности и плотные заполнители (щебень либо гравий); для легких — пористые заполнители (пемза, шлак, туф, керамзит и др.).. Керамзит в виде окатышей приобретают обжигом глин с повышенным содержанием оксида железа.
К очень легким относятся ячеистые бетоны, каковые имеют в толще большое количество замкнутых пор (до 85% от общего объема). Главными из них являются пенобетон и газобетон.
Газобетон приобретают на базе портландцемента с добавкой извести (до 10%) и алюминиевого порошка либо пергидроля. При сотрудничестве алюминия с гидроксидом кальция выделяется много водорода, что и вспучивает цементную смесь, придавая ей высокую пористость. Прочность его при сжатии 7 МПа.
Пенобетон приобретают при введении в цементную смесь пенообразующих добавок и в первую очередь водных растворов сапонина (мыльного корня) либо клееканифольных растворов.
Пено- и газобетоны применяют для получения теплоизоляционных изделий (скорлупы, сегменты, плиты и др.).
Фундаментальными физико-механическими особенностями бетонов являются плотность, объемная масса, теплопроводность, водопроницаемость, усадка, морозоустойчивость, огнестойкость, стойкость против коррозии и др. Зависят эти показатели от вида заполнителей, соотношения их с вяжущими веществами и от степени уплотнения цементной смеси.
Стойкость бетона против коррозии, к примеру, обусловливается образованием при затвердевании портландцемента гидроксида кальция. Для увеличения ее используют сульфатостойкий портландцемент либо цементы с активными добавками.
К особым бетонам относятся дорожный, жаростойкий, кислотоупорный и декоративный.
Дорожный бетон используют для покрытий трасс , городских улиц, других путей и аэродромов, подвергающихся при эксплуатации многократным механическим действиям, оттаиванию и замораживанию, высыханию и увлажнению.
Приобретают его на базе простого либо гидрофобного портландцемента с содержанием трехкальциевого алюмината не более 10%. В качестве большого заполнителя используется гравий либо щебень из жёстких пород с прочностью на сжатие 60—80 МПа. Морозоустойчивость его не меньше 100 циклов.
На базе этого бетона изготовляют изделия в виде армированных других сборных и плит элементов, каковые используются для верхнего слоя однослойных и двухслойных покрытий и для нижнего слоя двухслойных покрытий.
Жаростойкий бетон приобретают на базе портландцемента, шлакопортландцемента либо глиноземистого цемента на растворимом стекле. В бетон на базе портландцемента вводят порошкообразные добавки шамота, шлака, других веществ и пемзы. В бетон на глиноземистом цементе добавки не вводятся.
В качестве небольших и больших заполнителей используют огнеупорные материалы: шамот, андезит, базальт и др.
По огнеупорности жаростойкий бетон делится на три вида: высокоогнеупорный (выше 1770°С), огнеупорный (1580—1770°С) и жароупорный (ниже 1580°С). Эти бетоны используются для изготовления дымовых труб, фундаментов, мартеновских, доменных и других печей, для других конструкций и тепловых агрегатов, эксплуатируемых при температуре 1000—1800°С.
Кислотоупорный бетон приобретают из смеси, складывающейся из кислотоупорного цемента, кислотоупорных плотных заполнителей (диабаза, базальта, андезита и др.) и растворимого стекла. Его прочность при сжатии около 30 МПа. Затвердевание его происходит на воздухе.
Используется он в химической индустрии в виде труб, другой аппаратуры и резервуаров.
Гидротехнический бетон используется для конструкций и сооружений, неизменно подвергающихся действию воды. Он должен быть прочным, водостойким, влагонепроницаемым, морозостойким и стойким к коррозии.
Гидротехнический бетон приобретают на базе гидрофобного и плотных заполнителей и обычного цемента. По прочности на сжатие (МПа) он делится на марки от 10 до 50, а по морозоустойчивости — от 50 до 500 циклов. По способности выдерживать давление воды (0,2—1,2 МПа) он делится на марки: В2, В4, В6, В8 и В12.
Декоративные бетоны (цветные) приобретают на базе белого либо цветных портландцементов. В качестве красителей применяют охру, металлический сурик, оксид другие пигменты и хрома. Используются декоративные бетоны для наружной облицовки строений. Они должны владеть большой прочностью, стойкостью и морозостойкостью к коррозии.
По прочности на сжатие (МПа) эти бетоны делятся на марки — от 15 до 20, по морозоустойчивости — от 25 до 50 циклов.
Маркировка, упаковка, хранение и транспортирование материалов на базе неорганических вяжущих веществ
Маркируют эти изделия, не считая силикатного и известково-шла-кового кирпича, с тыльной стороны несмываемой краской с указанием марки, завода-изготовителя, даты изготовления, номера ГОСТа и т. д.
Силикатный и известково-шлаковый кирпич не маркируют, а при поставке сопровождают паспортом. На гипсовых плитах для перегородок штамп ставится на торцовую грань, обшивочные гипсовые страницы на тыльной стороне должны иметь надпись «Тыльная», на бензонапорных асбестоцементных трубах надписывают «Безнапорная». Асбестоцементные муфты маркируют с указанием марки труб, для соединения которых они предназначены.
Упаковке эти материалы не подвергаются.
При транспортировании в крытых вагонах, автомашинах и на вторых видах транспорта их укладывают стопами по размерам и видам. Гипсовые обшивочные страницы на маленькие расстояния транспортируют на автомашинах. Силикатный кирпич перевозится на особых поддонах.
Асбестоцементные и гипсовые плиты для перегородок устанавливают на ребро. При разгрузке и погрузке материалы направляться предохранять от ударов.
Гипсовые и магнезиальные изделия нужно хранить в сухих крытых помещениях. Остальные материалы возможно хранить на открытом воздухе под навесом. При хранении материалы нужно укладывать в клетки либо штабеля раздельно по видам, маркам, сортам и размерам.