Некоторые механические испытания покрытий
Опробования покрытий на истирание (износостойкость). Изнашивание — это изменение поверхности предмета благодаря отрыва от нее небольших частиц. Отрыв частиц может случиться благодаря чисю механического действия, но довольно часто, в особенности для железных пар, в один момент с механическими повреждениями происходят и химические реакции между трущимися парами либо с окружающей средой (воздухом, смазочным материалом); при работе электрических контактов происходит электроэрозия.
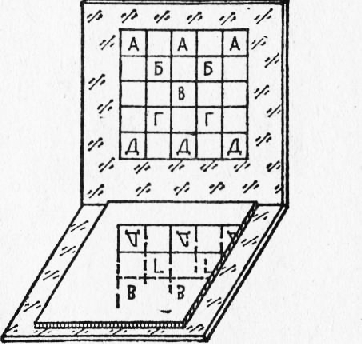
Рис. 1. Прибор для определения износостойкости электролитических покрытий: 1 — плоскопараллельная пластина, закрепленная без движений; 2 — подвижный диск; 3 — съемная гиря; 4 — коромысло с противовесом и поводковым пальцем
Мерой износа в большинстве случаев есть уменьшение массы материала в следствии опробования, определяемое взвешиванием. Такие опробования именуют опробованиями на истирание. Время от времени износ характеризуют трансформацией состояния поверхности, которое возможно выяснить особым прибором.
В некоторых случаях пользуются вторыми показателями (к примеру, длительностью опробования либо числом шлифовального материала, нужного с целью достижения определенного состояния поверхности). Эти показатели являются, само собой разумеется, не безотносительную меру износа примера, а только относительные размеры.
Для опробования на истирание возможно советовать прибор, главным элементом которого есть латунный барабан с натянутым на него сукном (для мягких покрытий) либо наждачным полотном (для жёстких покрытий). Вместо наждачного полотна во многих случаях возможно применять бумагу (чертежную), которая владеет высокими абразивными особенностями. Пример закрепляют в патроне рычага, что расположен на барабане под нагрузкой.
Через каждые 50 либо 100 оборотов пример приподнимают, охлаждают и посредством индикатора контролируют, обнажился ли главный металл. Мерой износостойкости покрытия есть число оборотов барабана, нужное для истирания электролитического покрытия определенной толщины при постоянной нагрузке. К недочётам прибора направляться отнести нехорошую воспроизводимость результатов опробований.
Хорошую воспроизводимость результатов опытов достигают на приборе, созданном в ЛТИ им. Ленсовета и снабжающем возвратно-поступательное перемещение примера (рис. 30). Трущаяся пара представляет собой металлический либо латунный диск 2 диаметром 15 мм с нанесенным на него покрытием; диск перемещается по неподвижной плоскопараллельной пластине. Неподвижную пластину 1 при необходимости покрывают соответствующим электролитическим покрытием.
В качестве нагрузки на пример используют съемную гирю 3. В один момент подвергают истиранию пара образцов. Износостойкость покрытия определяют по времени истирания примера до обнажения базы. При высокой износостойкости образ-* ца определяют утраты его массы.
Определение антифрикционных особенностей покрытий. При выборе покрытия для трущихся деталей конструируемой автомобили, и при ее ремонте либо изыскании способов увеличения износостойкости прибегают к лабораторным изучениям. Наряду с этим для оценки покрытия самый ответственны следующие антифрикционные и прочностные характеристики: износостойкость, прирабатываемость, коэффициент трения, прочность сцепления, параметры шероховатости, свойство выдерживать высокие удельные нагрузки и длительно трудиться без смазочного материала, противостоять схватыванию либо заеданию, сопротивляться циклическим контактным и динамическим ударным нагрузкам.
Методы оценки антифрикционных особенностей материала покрытий разны. Из них возможно советовать следующие. Износостойкость и прирабатываемость покрытий возможно оценить- на машине трения АЕ-5.
Машина АЕ-5 разрешает испытывать на износ покрытия в широком диапазоне заданных давлений, скоростей скольжения, температур и при разных режимах смазывания. На данной же машине возможно определять коэффициент трения, предельные нагрузки, каковые способно выдержать покрытие при долгой работе в заданных условиях трения, и свойство материала покрытия длительно действующий при выключении подачи смазочного материала.
Свойство материала покрытия противостоять схватыванию (заеданию) возможно определять на особом приборе для опробования металлов на заедание. Между двумя параллельными маленькими цилиндрическими примерами сжимается расположенный перпендикулярно им третий долгий пример. При опробовании этого примера на разрывной машине приобретают зависимость путь — сила трения.
Разбирая характер силы и значение трения ее трансформации, возможно оценить склонность испытуемой пары к схватыванию. Меняя место контакта, возможно.испытывать одинаковые образцы пара раз. Наряду с этим расхождение значений большой силы трения в большинстве случаев не превышает 10%.
Обрисованный способ разрешает совершенно верно определять место контакта и удельную нагрузку при заедании, оценивать влияние на заедание и схватывание узких оксидных покрытий и электролитически нанесенных слоев металлов, и влияние Вторых факторов (особенностей смазочных материалов, температуры и др.).
Прочностные характеристики покрытий либо их свойство сопротивляться разным нагрузкам определяют в большинстве случаев на особых устройствах. Так, свойство покрытия сопротивляться циклическим контактным нагрузкам возможно определять на машине трения, динамическим нагрузкам — на особом приспособлении, которое разрешает подвергать испытуемую поверхность действию ударной нагрузки (мгновенное сжатие либо сжатие со сдвигом).
Рис. 2. Прибор для определения хруп. кости (эластичности) покрытий: 1 — испытуемый пример; 2 — ролики; 3 — цилиндрическая опора; 4 — лимб; 5 — опорная” втулка; 6 — шпонка; 7 — гайка рабочая
Комплексная оценка антифрикционных и прочностных особенностей покрытия разрешает установить его пригодность к эксплуатации в условиях трения.
Определение хрупкости (эластичности) покрытий. Хрупкость — один из главных показателей качества электролитического покрытия, определяющий возможность применения ег.о в тех либо иных условиях эксплуатации. В ходе предварительной обработки и электроосаждения поверхности металла не считая хрупкости покрытия вероятно самого изделия и охрупчивание.
Повышенная хрупкость подробностей возможно обстоятельством их стремительного разрушения при эксплуатации, исходя из этого нужно определять хрупкость изделий при их контроле.
Чёртом покрытия, обратной хрупкости, есть его эластичность.. Чем больше хрупкость покрытия, тем меньше его эластичность.
Прибор для определения относительной эластичности покрытий, предложенный Н. Д. Томашовым, М. Н. Тюкиной и Г. К- Блинчевским (рис. 31), выстроен по принципу винтового пресса и разрешает определять угол изгиба примера.
Испытуемый пример в виде пластинки размерами 15X60X1 мм подводят под ролики и хорошо прижимают к ним особой пружиной. Ролики изгибают пример, опирающийся в центре на цилиндрическую опору, и стрелка прибора начинает двигаться по Лимбу. Степень эластичности (либо хрупкости) покрытия определяют по углу изгиба до момента появления весьма маленьких (длиной 1—2 мм) трещин на поверхности примера.
Чем больше угол, при котором покрытие начинает растрескиваться в месте изгиба, тем меньше хрупкость покрытия. Появление первичной трещины возможно замечать визуально, в случае если глаз наблюдателя и источник света находятся по одну сторону от грани излома покрытия (наряду с этим трещина прекрасно видна).
хрупкости покрытий определения и Этот способ эластичности возможно советовать для заводских лабораторий при необходимости стремительной оценки качества покрытий. Прибор дает относительную оценку эластичности разных покрытий только при нанесении их на одинаковый материал и однообразной толщине образцов. Перед опробованием образцы рекомендуется выдерживать в эксикаторе не меньше 24 часов.
Рис. 3. Пример для опробований на разрыв
Образцы для опробований готовят следующим образом. На полированную пластинку из коррозионно-стойкой стали наращивают электролитический слой покрытия толщиной 50— 100 мкм, что после этого легко отделяют. Из отделенного покрытия штампом вырезают пример особой формы (рис.
32). Полученный пример испытывают на разрывной машине, предназначенной для опробования образцов тонкой ленты и проволоки на растяжение. Для этих же целей возможно применять микроразрывную машину конструкции Я. Б. Фридмана.
При применении штампа для того чтобы на его кромках образуются неровности. Помимо этого, действие штампа может привести к искажениям кристаллической решетки, что кроме этого отражается на приобретаемых итогах. Эти недочёты способа возможно исключить при следующем методе изготовления образцов. По окончании снятия и электролиза покрытия с базы поверхность покрывают воском; по воску прочерчивают контур испытуемого примера (см. рис.
3), и после этого пример вытравливают по контуру. Раствор для вытравливания подбирают в каждом определенном случае. К примеру, для бронзовых покрытий применяют FeCl3 (300 г/л).
Воск с поверхности примера удаляют промывкой в бензине.
Определение предела выносливости покрытий. Усталость — процесс постепенного накопления повреждений металла под Действием переменных напряжений.
Как мы знаем, что нанесение электролитических покрытий существенно снижает предел выносливости стали. В следствии электролитического осаждения хромовых покрытий предел выносливости стали понижается существенно, причем это понижение находится в прямой зависимости от толщины слоя покрытия. Во многих случаях это ведет к разрушению подробностей в про-нессе эксплуатации.
В связи с изложенным по окончании нанесения покрытия направляться контролировать предел выносливости изделий. Опробования выполняют по методикам, принятым для металлических образцов без покрытия. При этих опробованиях нагружение, талантливое привести к усталостному повреждению, реализуют многократным повторением циклов нагружений от громаднейшего значения к мельчайшему и обратно.
Число циклов нагружения на протяжении опробования — его наиболее значимая черта, в большинстве случаев машинально регистрируемая особым счетчиком.
Автомобили для опробований на усталость очень разнообразны; их возможно классифицировать по разновидности напряженного состояния примера, и по способу и схеме его нагружения. По первому показателю автомобили разделяют на осуществляющие циклы переменного нагружения на изгиб, кручение, растяжение — сжатие, сложные напряженные состояния и т. д. По второму показателю автомобили направляться поделить на две многочисленные группы: автомобили с задаваемой нагрузкой на пример, трудящиеся по принципу постоянства нагрузки в течение всего опробования; автомобили с задаваемой деформацией примера, реализующие принцип неизменности деформации в течение опробования.
В частности, опробования образцов с покрытиями возможно проводить на машине типа Шенка; наряду с этим применяют цилиндрические металлические образцы диаметром 7,2 мм. База опробований на усталость 5-106.
Определение параметров шероховатости поверхности покрытий. Для внешнего вида поверхностей с нанесенным покрытием, их износостойкости, и коррозионной стойкости очень значительны параметры шероховатости поверхности.
В ходе осаждения электролитических покрытий происходит изменение микрогеометрии поверхности. В некоторых случаях в ходе нанесения покрытия сглаживаются микронеровности поверхности базы, что ведет к ее улучшению (никелирование); в других случаях, напротив, высота неровностей возрастает (цинкование), а время от времени процесс покрытия происходит при неизменной микрогеометрии (лужение, кадми-рование и др.).
Предложен последовательность способов измерения параметров шероховатости поверхности. Часть из них дает лишь качественные эти, которых в большинстве случаев достаточно для технологического контроля в производстве. Другие способы дают количественные информацию о микрогеометрии поверхности и так удовлетворяют более Высоким требованиям научных исследований и технологического процесса.
Довольно обширно применяют так именуемые эталоны шероховатости, каковые разрешают взять числовые характеристики качества поверхностей подробности их визуальным и осязательным сравнением. Эталоны изготовляют гальванопластикой по исходному примеру, форму придают штамповкой. С эталонами, имеющими определенные параметры шероховатости, сравнивают испытуемые изделия.
Опробование посредством микроскопа в отраженном свете разрешает выяснить параметры шероховатости поверхности покрытия фокусированием микроскопа на вершины и впадины профиля. Параметры шероховатости так определяют как разность высот установки микроскопа.
Значительно чаще для измерения параметров шероховатости поверхности используют способ ощупывания. Устройствами этого типа (профилографами, профилометрами) осуществляют контроль поверхность механическим щупом в двух измерениях. Колебания игольчатого щупа по окончании оптического повышения либо электронного усиления есть мерой шероховатости.
Благодаря малого радиуса закругления острия игольчатого щупа (2— 10 мкм) уже при нагрузке на щуп «1 мН появляются такие высокие давления, что в ходе измерения на поверхности смогут появиться остаточные деформации. Это нужно учитывать, в особенности для мягких металлов. Посредством регистрирующего устройства возможно взять диаграмму профиля. Такие диаграммы поверхности в один момент с количественной дают последовательность качественных черт поверхности.
Протяженность участка, на котором делают ощупывание, должна быть по возможности громадной. В большинстве случаев пределы измерения параметров шероховатости поверхности 0,1—1000 мкм.
По методам усиления и преобразования колебаний профи-лографы подразделяются на механические, оптико-механические и электромеханические. Механические устройства фактически не используют. В электрохимических изучениях обширно применяют индуктивный профилограф-профилометр «Калибр» отечественного производства.
Предложен кроме этого оптический способ определения шероховатости, заключающийся в измерении поперечных шлифов и связанный с разрушением изделия. Параметры шероховатости в этом случае возможно определять в один момент с измерением толщины покрытия. направляться подчернуть, что для определения параметров шероховатости поверхности возможно применять все оптические способы, каковые используют для определения толщины покрытий.
Потому, что параметры шероховатости поверхности характеризуют различие между настоящей поверхностью примера и его номинальной поверхностью, то, выяснив параметры шероховатости покрытия, возможно выяснить и его подлинную поверхность.