Обработка режущих элементов инструмента
Быстрорежущие пластинки крепятся к корпусу инструмента методом пайки, сварки либо механическим методом. Прекрасно зарекомендовали себя инструменты с запрессованными пластинками. Инструментальными фабриками выпускаются дисковые фрезы, развертки и зенкеры с ровными запрессованными пластинками.
Большие фрезы, развертки и зенкеры оснащаются клиновыми рифлеными ножами из быстрорежущей стали.
Изготовление пластинок. Режущие пластинки для резцов и многолезвийного инструмента выполняются из полосовой быстрорежущей стали. Технологический процесс их изготовления для дисковых фрез складывается из следующих операций: рубки полос с припуском на механическую обработку; правки полос (стрела прогиба должна быть не более 0,2 мм); обработки плоскостей фрезерованием либо шлифованием (в случае если режущие пластинки имеют уклон в пределах 1…30, то шлифуется вся заготовка); разрезки заготовки на отдельные пластинки; термической обработки пластинок чтобы получить твёрдость HRC 62…65; проверки 10% партии пластинок на твердость; пескоструйной очистки.
Последняя операция очистки — пассивирование в 10%-ном растворе нитрита натрия при температуре 50…70 °С.
Шлифование пластинок. По техническим условиям глубина выкрашивания на рабочих кромча пластинок не должна быть больше 0,2 мм, а на нерабочих— 0,5 мм. По широким опорным поверхностям пластинок допускается выпуклость и вогнутость в пределах 0,05…0,2 мм.
Для многих режущих инструментов такое отклонение от плоскостности недопустимо, и перед напайкой либо механическим закреплением пластинки шлифуют абразивными и алмазными кругами либо доводят карбидом бора, а на некоторых фирмах шлифуют химико-механическим методом.
Абразивными и алмазными кругами пластинки обрабатывают на плоскошлифовальных станках. Чтобы не было происхождения на них трещин толщина слоя, снимаемого за один проход, не должна быть больше 0,007 мм. По окончании шлифования пластинки обезжиривают в кипящем 10…12%-ном растворе кальцинированной соды, после этого промывают в тёплой воде и подвергают пескоструйной обработке. После этого в течение 10 мин их кипятят в 20…25%,-ном растворе смеси буры с фтористым калием.
По окончании сушки пластинки покрывают узкой стеклообразной пленкой флюса, которая предохраняет их от окисления.
Посадочные поверхности твердосплавных коронок — торец и коническое отверстие со стороны паза — должны быть шлифованными. Обработку отверстия коронки реализовывают химико-механическим методом, исправляя эллипсность, доходящую в некоторых случаях до 0,05 мм.
Многогранные пластинки по окончании спекания имеют дЛ статочно верную геометрическую форму и шерох01 ватость боковых поверхностей Ra= 1,25…0,63 мкм, этому пластинки с выкружками доводят по опорным фаскам и торцевым поверхностям на протяжении режущих кpoмок, плоские—по обеим торцевым поверхностям. Обра] ботка их может производиться на доводочном станке модели ЗБ-8164 на чугунном диске с применением пасты карбида бора на алмазном круге.
При изготовлении торцевых фрез, расточных головок и других многолезвийных инструментов, оснащенных многогранными пластинками, нужна предварительная сортировка их по главным размерам, воздействующим на биение инструмента. Биение основных режущих кромок у торцевых фрез с шести-, пяти- и четырехгранными пластинками на двух смежных зубьях должно быть не более 0,12 мм, а суммарное биение — не более 0,2 мм. Торцевое биение не должно быть больше 0,2 мм.
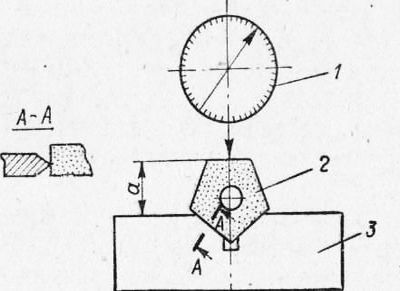
Рис. 1. Схема сортировки пластинок.
Правильные многогранные пластинки для черновых фрез целесообразно сортировать по схеме, приведенной на рис. 1. Пятигранная пластинка поджимается двумя гранями к сторонам угла закрепленного шаблона, и по положению стрелки на шкале индикатора определяется партия, в которую она обязана попасть. Угол шаблона соответствует углу при вершине пластинки.
Для исключения влияния отдельных факторов на точность сортировки пластинок их направляться поджимать в угол шаблона средней частью по толщине (см. сечение А—А), а не кромками верхнего либо нижнего торца. Отклонение размера а упорядоченных пластинок в пределах одной партии не должно быть больше 0,05… 0,08 мм.
Державки для резцов дековаными либо литыми.
Исходным материалом для штучных заготовок державок являются прямоугольные либо круглые прутки. Заготовку приобретают резкой либо рубкой. образование и Загибку головки задних поверхностей реализовывают тёплой штамповкой.
Державки сечением до 12X20 мм возможно ковать в холодном состоянии. Головки державок отрезных резцов штампуют способом облойной штамповки по одной штуке с последующим удалением облоя в обрубном штампе.
Обработку опорных плоскостей реализовывают фрезерованием либо шлифованием. Задние поверхности державок прямых и отогнутых резцов приобретают фрезерованием.
Одной из важных операций есть фрезерование паза под пластинку. Существуют две главные формы паза под режущие пластинки: открытый паз, используемый для большинства резцов, и закрытый либо полузакрытый — для отрезных и резьбовых резцов.
Открытый паз самый целесообразно обрабатывать на горизонтально-фрезерных станках в поворотном приспособлении, где закрепляется пара державок. Получение нужного угла наклона паза обеспечивается клином, на котором устанавливаются державки.
Полузакрытые и закрытые пазы фрезеруют на вертикально-фрезерных станках концевой фрезой с креплением державок в поворотном приспособлении. Диаметр концевых фрез обязан соответствовать радиусу закругления пластинки.
Поверхности пазов должны быть ровными и ровными—без впадин, выпуклостей, глубоких царапин; шероховатость поверхности обязана соответствовать г —20… 10 мкм. По окончании механической обработки паза разрешается только снятие заусенцев личным напильни-ко л и запиловка острых кромок. При громадных парти резцов заусенцы рекомендуется удалять на вибрац11оЯ* них установках.
Изготовление корпусов концевого инструмента. 1
самые ответственными операциями изготовления корпусов инструмента являются обработка прямых, наклонных и винтовых канавок и фрезерование спинки винтовых зубьев.
У сборных инструментов режущую часть изготовляют из инструментальных сталей, а хвостовую — из углеродистой конструкционной. Главным методом получения составного инструмента есть контактная сварка, а сейчас используется и сварка трением.
Концевые режущие инструменты изготовляют с цилиндрическими либо коническими хвостовиками, обработка которых осуществляется на токарных станках либо на особых станках — автоматах и полуавтоматах.
Квадраты у разверток, других инструментов и метчиков фрезеруют, протягивают либо штампуют. Лапки у свёрл и машинных развёрток обрабатывают на горизонтально-фрезерных станках двумя трехсторонними фрезами в мелкосерийном производстве и на особых автоматах — в крупносерийном.
В серийном производстве винтовые канавки и прямые фрезеруются на горизонтально- и универсально-фрезерных станках в одношпиндельной делительной головке. Прямые канавки у разверток фрезеруют в много-шпипдельных делительных головках в основном на продольно-фрезерных станках. Винтовые канавки у концевых и зенкеров фрез фрезеруют в трехшпиндельных универсальных делительных головках на универсально-фрезерных станках.
Рис. 2. Процесс обработки корпуса сверла.
Затем сверло поступает на заточку и шлифование.
При обработке корпуса сверла базами помогают цец. тры, исходя из этого на торце хвостовика на начальной стадии обработки производится сверление и зенкерованпе центро-вого отверстия, а со стороны рабочей части — обточка наружного центра.
Изготовление корпусов насадного инструмента. К насадным режущим инструментам относится большая часть фрез, имеющих цилиндрические отверстия. В условиях мелкосерийного производства корпус насадного инструмента диаметром до 50 мм целесообразно изготовлять из горячекатаной прутковой стали на револьверных станках, а при личном производстве — из штучных заготовок на токарных либо револьверных станках.
Последовательность обработки отверстий до термической обработки: центрование, сверление, снятие фаски и подрезка торца, выточки и растачивание отверстия, развертывание. В крупносерийном производстве развертывание отверстий заменяется протягиванием. В условиях личного производства отверстия обрабатывают на револьверных станках.
Так как отверстия насадного инструмента являются главной базой при его эксплуатации и изготовлении, их шлифуют и доводят. Шлифование реализовывают на внутришлифовальных станках способом продольных подач. Для обеспечения перпендикулярности торца оси обрабатываемого корпуса торец и отверстие целесообразно шлифовать с одной установки.
В этом случае торец шлифуют чашечным либо плоским крутом.
Обработка пазов. В зависимости от способа крепления и конструкции инструмента ножей к корпусу пазы бывают прямые, клиновидные и с рифлением. Пазы шириной 2…2,5 мм обрабатывают прорезными фрезами, шириной 6…8 мм — пазовыми затылованными шириной и фрезами до 10 мм — дисковыми трехсторонними фрезами. Громаднейшую производительность снабжают дисковые трехсторонние фрезы с раскошенными зубьями.
Они используются при фрезеровании пазов шириной более чем 5 мм.
Клиновидные пазы в корпусах торцевых дрез обрабатывают посредством особых делительных головок с ярким делением. Головка имеет верхнюю плиту, которая может поворачиваться относительно оси вращения нижней плиты, закрепленной на столе горизонтально-фрезерного станка. Обработка производится в два перехода При первом все пазы фрезеруют с одной установки, а при втором делительную головку поворачивают на задний угол (в этом случае на угол 5°) и все пазы фрезеруют вторично.
Делительные головки с ярким делением предназначены для обработки клиновидных пазов в корпусах фрез диаметром до 500 мм.
Рифления в пазах, расположенных параллельно оси либо под углом к ней, образуют посредством особых протяжек на протяжных станках, а в клиновидных пазах посредством клина. В случае если рифление в пазах направлено радиально, то его обработка осуществляется на долбежных станках особыми пластинчатыми Долбяками. Для направления долбяка в паз корпуса ставляют направляющий клин, соответствующий углу наклона паза.
Подача на любой движение долбяка осуществляется пятью-шестью сменными клиньями.
Рис. 3. Обработка клиновидных пазов.
Напайка твердосплавных пластинок. Подготовк державки либо корпуса к пайке содержится в тщательной обработке пазов подтвер. досплавные пластинки. Поверхности пазов должны иметь ровную плоскость, без выпуклостей и впадин, с шероховатостью Rz — 20… 10 мкм.
Фрезерование пазов и затылков на корпусе производится до напайки пластинок.
При фрезеровании открытых пазов и при маленькой длине пластинок рекомендуется оставлять перемычку толщиной 1…1.5 мм по передней плоскости паза. В этом случае пластинки возможно закреплять методом подчеканки по передней плоскости перемычки. В ходе заточки инструмента по передней! поверхности перемычку нужно удалять. Ширина паза обязана соответствовать толщине пластинки.
Зазор между пластинкой и плоскостями паза должен быть не более 0.05…0,15 мм.
Размещение дна паза должно снабжать припайку пластинок под нужными углами, с тем дабы они употреблялись самый рационально.
Так, у резцов паз направляться располагать под углом, величина которого больше переднего угла резца на 3…5°. При фрезеровании паза в корпусе инструмента кроме этого нужно учитывать угол наклона режущей кромки “К.
Открытый паз для винтовых пластинок не имеет перемычки, поскольку крепление их осуществляется особыми штифтами.