Конструкции режущего инструмента
Резцы. Различают токарные, расточные державочные, строгальные и долбежные резцы. Самый распространены токарные резцы.
Типы токарных резцов приведены на рис. 1.
Они разделяются: – по виду обработки:
1— проходные; 2— подрезные; 3 — прорезные и отрезные; 4 — расточные; 5—канавочные; 6 и 8 — фасонные; 7 — радиусные; – по характеру установки их относительно детали: 9 — тангенциальные; — радиальные; – по направлению подачи: 11— левый; 12 — правый; – по конструкции головки: 13 — прямой; 14 — отогнутый; 15 — изогнутый; 16 — с оттянутыми головками.
Проходные резцы предназначены для обработки наружных цилиндрических и конических поверхностей, подрезные — для обработки плоскостей, перпендикулярных оси вращения, подрезки торцев на проход. Трудятся они при поперечной подаче. Отрезные резцы помогают для отрезки заготовок от прутка диаметром до 60 мм, расточные — для обработки отверстий, а фасонные—тел вращения с криволинейной либо винтовой поверхностью на револьверных станках и токарных.
Строгальные резцы разделяют на проходные, отрез—ные, подрезные и пазовые. Эти резцы трудятся в более тяжелых условиях, чем токарные, — с ударом в ходе врезания.
Долбежные резцы делятся на проходные двусторонние с углом 45°, прорезные и шпоночные. Проходными резцами обрабатывают вертикальные и криволинейные поверхности, прорезными — долбят пазы, канавки, плоскости с уступом, разрезают металл, шпоночными —. ‘долбят шлицы и шпоночные пазы в отверстиях от 7 до 70 мм.
Типы резцов отличаются друг от друга по конструктивным показателям: по форме сечения державки резца, роду материала режущей части и методу крепления режущих пластинок к державке резца.
Наиболее неотъемлемой частью резца есть головка (режущая часть). Форма режущей части резца и углы заточки определяют геометрию инструмента.
Режущая часть резца складывается из основной режущей кромки и вспомогательной, задней вспомогательной поверхности, вершины, задней передней поверхности и главной поверхности.
Резцы изготовляют цельными, сварными, наплавными, цельнопаяными и сборными. Широкое использование находят резцы цельнопаяные и сборные. По роду материала режущей части различают быстрорежущие, твердосплавные, минералокерамические и алмазные резцы.
С напаянными пластинками из быстрорежущей стали изготовляют резцы: проходные изогнутые с углом в плане ф = 45° (ГОСТ 18868—73); проходные прямые с ф = 45° и ф = 75° (ГОСТ 18869—73); проходные упорные с ф = 90° (ГОСТ 18870—73); подрезные торцевые с ф = 90° (ГОСТ 18870—73); отрезные (ГОСТ 18874—73) и расточные с ф = 45°, ф = 60° и ф-90°.
Конструкционные стали обрабатывают резцами, оснащенными пластинками из быстрорежущей стали марки Р12 (ГОСТ 19265—73), а труднообрабатываемые материалы — марки Р9К10.
Пластинками из жёсткого сплава оснащают резцы: 1х«77дные отогнутые с углом в плане ф = 45° (ГОСТ ibu/7—73); проходные прямые с ф = 45°, ф = 60° и г
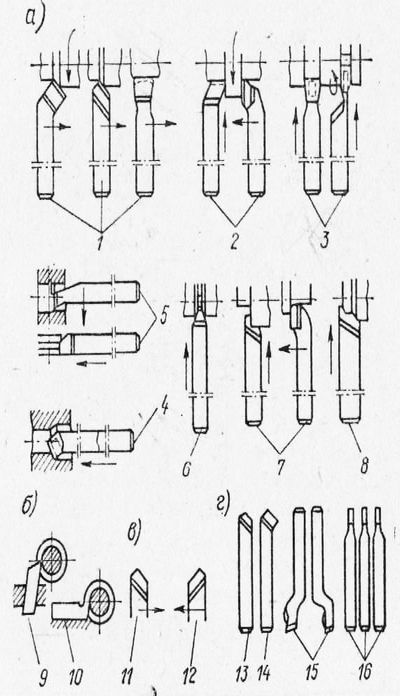
Рис. 1. Типы токарных резцов.
Резцы токарные сборные проходные с механическим креплением многогранных неперетачиваемых пластин из жёсткого сплава предназначены для наружного обтачивания подробностей с громадным отношением длины к диаметру, подрезания торцев, расточки маленьких глухих отверстий громадного диаметра. Для оснащения проходных резцов используют пластины трех-, четырех-, пяти-и шестигранной формы.
Все проходные резцы выполнены по одной конструктивной схеме. Резец с шестигранной пластинкой имеет державку, в которую запрессован штифт. Сменная твердосплавная подкладка закрепляется на конической части этого штифта. Многогранную пластину крепят методом расклинивания ее между штифтом и задней опорной стенкой державки винтом и клином.
Задний угол а образуется за счет установки пластин в державке под углом ууст = 7—8° к главной плоскости резца.
Рис. 2. геометрические параметры и Элементы резца.
С многогранными пластинками из жёсткого сплава изготовляют сборные расточные резцы с углами в плане 45, 50, 60 и 90°, и автоматно-револьверные и резьбовые.
К каждому резцу завод-изготовитель прилагает набор многогранных пластинок (числом 15 —0 шт.). По окончании износа одной режущей кромки пластинку поворачивают и трудятся следующей кромкой, а по окончании износа всех кромок пластинку сдают в инструментальную кладовую для обмена.
Для получистовой и чистовой обработки стали, медных сплавов и чугуна используют резцы, оснащенные минеральной керамикой и керйетами. Эти резцы изготовляют папайными и с механическим закреплением пластинок.
Рис. 3. Проходные твердосплавные резцы.
В напайных резцах минералокерамиче-скую пластинку припаивают красной медью либо вторыми припоями к державке в закрытый либо врезной паз. Прочность напайки минералокерамических пластинок еще ниже, чем твердосплавных, исходя из этого напайные резцы используют редко.
Плоские н многогранные минералокерамические пластинки крепятся к державкам резцов значительно чаще механически. Конструкция для того чтобы креплениямало чем отличается от конструкции крепления твердосплавных пластинок. Резцы, продемонстрированные на рис.
89,6, по большей части употребляются для чистовой закалённой стали и обработки чугуна.
Действенна обработка подробностей из сталей твердостью HRC 50…60 и чугунов резцами, оснащенными эльбором. При растачивании и точении закаленных сталей они снабжают получение поверхностей 6-го…7-го квали-тетов с шероховатостью 0,16 мкм, наряду с этим изменений структуры в поверхностном слое не происходит.
В качестве режущего элемента для резцов применяют поликристаллы эльбора размером до 12 мм, закрепленные в державке из стали 40Х либо 9ХС способом заливки медью, латуныо либо особыми припоями.
Применяются сборные резцы с механическим закреплением вставок с поликристаллом из эльбора-Р. Ведутся работы по созданию многогранных пластин из эльбора-Р громадного размера, с тем дабы механическое крепление их было подобно креплению твердосплавных.
Алмазные резцы активно применяются при растачивании и тонком точении цветных неметаллических материалов и металлов. Владея высокой размерной стойкостью, они разрешают приобретать поверхности 6-го квалитета с шероховатостью до Ra = 0,02…0,01 мкм.
Резцы производят с на-пайным бриллиантом и с механическим креплением его. Масса используемых алмазов — 0,5… 0,8 карата (1 карат равен 0,2 г). Режущая кромка резца должна быть расположена так, дабы равнодействующая составляющая силы резания не проходила по плоскостям спайности бриллианта.
Изготовляют проходные и подрезные алмазные резцы с главным углом в плане ф = 30…90°, расточные с ф = 45…90°, канавочные, отрезные, и резцы для обработки поверхностей способом врезания.
Фрезы. Фреза — это многолезвийный режущий инструмент, любой из зубьев которого представляет собой несложный резец. Фрезерованием выполняются многие операции механической обработки.
Многообразие операций обусловило громадное разнообразие типов, размеров и форм фрез. Главные типы фрез приведены на рис. 5: цилиндрические для обработки плоскостей на горизонтально-фрезерных станках; торцевые для обработки плоскостей на вертикально-и продольно-фрезерных станках; прорезные и отрезные; дисковые пазовые двусторонние и трехсторонние для образования пазов и канавок; угловые для образования стружечных канавок на разных режущих инструментах; фасонные с выпуклым и вогнутым профилем и концевые.
Рис. 4. Минералокерамическиа напайные (а) и с механическим креплением пластин (б) резцы.
Рис. 5. Главные типы фрез.
Фрезы изготовляют цельными и со вставными ножами из быстрорежущей стали и ножами, оснащенными жёстким сплавом, а время от времени керметами и минеральной керамикой.
Быстрорежущие торцевые фрезы (ГОСТ 9304—69) диаметром 40—100 мм предназначены для фрезерования уступов, плоскостей, и поверхностных пазов в подробностях из чугуна и стали. Фрезы торцевых насадок диаметром 80…250 мм изготовляют со вставными ножами из быстрорежущей стали.
Цилиндрические быстрорежущие фрезы (ГОСТ 3752—71) диаметром 40…63 мм с диаметром и мелкими зубьями 50…100 мм с большими зубьями помогают для чистового и получистового фрезерования открытых поверхностей металлических и чугунных подробностей.
Концевые быстрорежущие фрезы с цилиндрическим хвостовиком (ГОСТ 17025—71) диаметром 3…20 мм и с коническим хвостовиком (ГОСТ 17026—71) диаметром 16…63 мм употребляются для обработки уступов, других операций и выемок.
Быстрорежущие дисковые трехсторонние фрезы (ГОСТ 3755—78) диаметром 50…100 мм предназначаются для фрезерования пазов и уступов в металлических и чугунных подробностях.
Изготовляются разнообразные твердосплавные фрезы: торцевые насадные со вставными ножами, оснащенными жёстким сплавом (ГОСТ 8529—69), диаметром 100…630 мм, используемые для скоростного фрезерования открытых поверхностей детален из чугуна и стали с припуском 6…10 мм, концевые с коническим хвостовиком, оснащенные винтовыми пластинками и коронками из жёсткого сплава; дисковые трехсторонние со вставными ножами, оснащенными жёстким сплавом (ГОСТ 5348—69), диаметром 100…315 мм; шпоночные со вставными ножами, оснащенными жёстким сплавом (ГОСТ 6396—78), с цилиндрическим хвостовиком диаметром 8…16 мм и с коническим диаметром 12…40 мм; шпоночные концевые цельные (ГОСТ 16463—70) диаметром 2…12 мм.
Громаднейшее распространение взяли торцевые фрезы с механическим креплением твердосплавных пластин и ножей.
Торцевая фреза с ножами, оснащенными твердосплавными напаянными пластинками, продемонстрирована на рис. 6, а. Ножи крепят в клиновидном пазу корпуса ровными клиньями с углом 5°. Как ножи, так и пазы в корпусе имеют ровные (без рифлений) стены. Для установки ножей предусмотрены винты, каковые ввертываются с задней стороны корпуса фрезы. При ослабленном клине винтом возможно перемещать нож на протяжении паза и совершенно верно установить его вылет под заточку.
В случае если фреза планирует в особом приспособлении, то винты не необходимы.
Не считая ровных ножей в соответствии с ГОСТом 9473—71 изготовляются ножи рифленые (рифления находятся параллельно основанию ножа). Опорные боковые стороны ножей выполнены под углом друг к другу в двух направлениях: параллельно (угол 5°) и перпендикулярно (угол 2°30’) основанию ножа. Такая наличие и форма ножей на них рифлений позволяет восстанавливать не только наружный диаметр фрез по мере их износа, но и величину вылета ножей.
Не смотря на то, что крепление ножей посредством рифления есть распространенным методом сборки фрез, но оно имеет значительный недочёт — напайка пластинок жёсткого сплава к ножам ухудшает уровень качества жёсткого сплава.
Рис. 6. Торцевые фрезы.
Появление многогранных неперетачиваемых пластинок жёсткого сплава разрешило отказаться от напайки пластинок и перейти к механическому креплению их. Существует два главных типа сборных торцевых фрез с многогранными пластинками: с закреплением пластинок конкретно в корпусе с подкладками либо без них и с закреплением в корпусе сменных ножей, к каким прикреплены многогранные пластины.
Торцевая фреза второго типа приведена на рис. 6,б. Она складывается из корпуса, державок ножей с запрессованными в них штифтами, на каковые вольно надевается многогранная пластинка, винтов и кольца для закрепления пластинок и в один момент державок ножей.
Пружина предназначена для предварительного прижатия пластинок к базисным поверхностям корпуса.
Фреза с закреплением пластинок конкретно в корпусе с подкладками продемонстрирована на рис. 7. В корпусе фрезеруют гнезда пол пластинки из жёсткого сплава. Дабы избежать износа гнезд при смене пластинок, в них вставляют опорные вставки (подкладки), изготовленные из вязкого жёсткого сплава.
Они являются более твёрдой опорой для пластин. Установленные в гнезда пластинки крепят клином, что затягивают винтом с правой и левой резьбой.
Рис. 7. Торцевая фреза.
Геометрия режущей части фрез образуется соответствующим размещением пластинки довольно главных координатных осей корпуса.
Принятое размещение опорной поверхности под пластинку на державке ножа и ее положение в корпусе фрезы снабжают задние углы а = 8…10° и передние Y= (—8”)…(—10°). Для получения хороших передних углов пластинку затачивают на протяжении лезвия по передней поверхности.
Торцевые фрезы с шестигранными пластинками предназначены для обработки подробностей с припуском до 6 мм. При обтачивании труднообрабатываемых материалов Целесообразно использовать фрезы с главным углом в плане ф = 40…45° и запасным qi = 15…20°.
Торцевые фрезы с четырехгранными пластинками смогут снимать припуск до 12 мм; их направляться применять на замечательных станках повышенной жесткости.
Сверла, развёртки и зенкеры являются главными инструментами для образования отверстий.
Сверла. По конструкции сверла классифицируют на спиральные, с прямыми канавками, перовые, ружейные, для глубокого и кольцевого сверления и центровочные.
Рис. 8. Разновидности сверл.
Сверла изготовляют из быстрорежущих, легированных и углеродистых сталей, и оснащают пластинками из жёстких сплавов.
Громаднейшее распространение взяли спиральные сверла с коническими и цилиндрическими хвостовиками диаметром от 0,1 до 80 мм, Быстрорежущие сверла с коническим хвостовиком диа-метром’от 6 мм и с цилиндрическим диаметром от 8 мм выполняются сварными. Спиральные сверла смогут быть и твердосплавными. Сверла диаметром от 1,8 до 5,2 мм изготовляются монолитными из жёстких сплавов марок ВК6 и ВК8М, а диаметром более чем 6 мм оснащаются пластинками жёсткого сплава.
Сверла с прямыми канавками в большинстве случаев используют для сверления чугуна и других хрупких материалов. Перовые сверла употребляются редко. Ружейные сверла помогают для образования отверстий малых диаметров, сверла глубокого сверления — сквозных и глухих отверстий громадной длины, а сверла кольцевого сверления — отверстий диаметром более чем 100 мм.
Центровочными сверлами обрабатывают отверстия в заготовках. Они изготовляются комбинированными с предохранительным конусом и без него.
Зенкеры. Зенкерование используют для обработки цилиндрических, ступенчатых, фасонных и комбинированных отверстий по окончании их сверления. Получение конических, цилиндрических и плоских поверхностей, прилегающих к главному отверстию и расположенных концентрично с ним, осуществляется инструментами, именуемыми зенковками.
Рис. 9. Зенкеры: а — спиральный из быстрорежущей стали; б — спиральный с пластинками жёсткого сплава; в — насадной из быстрорежущей стали; г —насадной, оснащенный пластинками жёсткого сплава;д—главные углы зенкеров.
Зенкеры подразделяются на следующие виды: с коническим хвостовиком для обработки отверстий с допускоми отверстий под развертывание; насадные цельные — для отверстий громадных диаметров; насадные со вставными ножами; хвостовые и насадные с напаянными пластинками из жёсткого сплава; сборные со вставными ножами, оснащенными жёстким сплавом.
Рабочая часть цельного зенкера выполняется из быстрорежущей стали и приваривается к коническому хвостовику из конструкционной стали. Ножи насадных зенкеров изготовляют из быстрорежущей стали либо жёсткого сплава.
Развертки. Развертывание — это окончательный процесс обработки отверстий, предварительно расточенных либо просверленных и обработанных зенкером.
Различают развертки цилиндрические, ступенчатые и конические. Они бывают ручными и машинными. По конструкции развертки делятся на хвостовые и насадные, цельные и сборные, постоянного диаметра и регулируемые, со вставными ножами из быстрорежущей стали либо из жёсткого сплава.
Рис. 10. Части и элементы развертки.
Ручная цилиндрическая развертка складывается из рабочей части, хвостовика и шейки. Рабочая часть, со своей стороны, делится на заборную (режущую) и калибрующую части и задний конус. Канавки между зубьями развертки образуют режущие кромки и предназначены для размещения стружки.
У разверток для ручной обработки зубья находятся по окружности с неравномерным шагом, что снабжает увеличение качества приобретаемой поверхности. Машинные развертки изготовляют с равномерным шагом, причем число зубьев у них должно быть четным. Рабочая часть этих разверток в отличие от ручных более маленькая.
Машинные развертки значительно чаще делаются насадными и регулируемыми.
Ручные развертки с цилиндрическим хвостовиком предназначены для обработки отверстий диаметром от 3 до 50 мм; машинные с цилиндрическими и коническими хвостойиками —- отверстий диаметром от 3 до 100 мм на сверлильном и токарном станках, а насадные — отверстий диаметром от 25 до 300 мм. Насадные развертки насаживают на особые оправки с коническими хвостовиками для их крепления на станке.
прошивки и Протяжки.
Имеется пара видов протяжек: – для внутренних поверхностей — с прямолинейным и винтовым относительным перемещением; – для наружных поверхностей—с прямолинейным, вращательным и винтовым относительным перемещением.
Любой вид протяжек имеет разновидности в зависимости от формы протягиваемых поверхностей. Различают протяжки для круглых, многогранных, шлицевых, шпоночных и фасонных отверстий, для фасонных поверхностей и плоскостей.
Главные части и элементы протяжек продемонстрированы на рис. 96, а. Протяжка складывается из хвостовика, предназначенного для закрепления инструмента в патроне и передачи ему тягового упрочнения; передней направляющей части, дающей направление протяжке в начале процесса; режущей части, оснащенной зубьями со стружколома-тельными канавками, которая делает главную работу по снятию стружки с подробности; калибрующей части, придающей обрабатываемой поверхности окончательные размеры и нужную шероховатость; концевой части, предохраняющей протяжку от перекоса при выходе ее из подробности.
Главными конструктивными элементами протяжки являются: геометрические параметры режущих и калибрующих зубьев, подъем на зуб, ход зубьев, количество зубьев и объём впадин. Зуб каждой протяжки имеет основную режущую кромку, заднюю поверхности и переднюю, передние у и задние а углы.
Шпоночные и шлицевые протяжки имеют запасного режущую кромку, заднюю запасного поверхность, вспомогательный угол в плане ср и переходную режущую кромку.
Величину переднего угла режущего зуба выбирают в зависимости от механических особенностей обрабатываемого материала. У протяжек для обработки внутренних поверхностей режущие зубья имеют задний угол a от 2° до 3°30’, а калибрующие — от 30’ до 1°. Громаднейший задний угол берется чтобы при переточках протяжка не была за пределами заданного размера.
Переточка протяжки для обработки наружных поверхностей не воздействует на ее точность, исходя из этого задний угол возможно увеличен до 10°.
Рис. 11. Части и элементы протяжек.
Разность высоты двух смежных зубьев протяжки характеризует толщину слоя, срезанного последующим зубом, либо величину подъема на зуб, зависящую от особенностей обрабатываемого материала, формы и жёсткости детали протягиваемой поверхности.
Для разделения стружки на поверхности режущей части зуба наносят канавки. Число их выбирают в зависимости от диаметра протяжки. К примеру, при диаметром 13—16 мм делают 8 канавок.
Firmware отличаются от протяжек тем, что они трудятся на продольный изгиб и сжатие. Протяженность firmware определяется ходом пресса, на котором производится обработка отверстия, и не превышает 12—15 поперечных размеров сечения firmware, в то время как протяженность протяжек достигает 30—40 поперечных размеров.
Резьбонарезной инструмент.
К резьбонарезным инструментам относятся: – головки и метчики для цилиндрических резьб (ручные, калибровочные, плашечные, маточные, машинно-ручные, гаечные); – головки и плашки винторезные для цилиндрических резьб; – резцы и гребенки для цилиндрических резьб;– фрезы для цилиндрических резьб;– инструмент для конических резьб.
Метчики. Главным инструментом для нарезания внутренних резьб есть метчик, воображающий собой винт с продольными прямыми либо винтовыми канавками, образующими режущие кромки. Метчик складывается из рабочей части, хвостовика, центровых технологических отверстий, режущих канавок и перьев.
В соответствии со стандартом метчики изготовляются четырех степеней точности: С, Д, Е и Н; машинные и гаечные метчики — С и Д, а ручные — Е и Н.
Ручные метчики предназначены для нарезания резьб диаметром от 2 до 52 мм вручную. Они выпускаются набором, складывающимся из двух либо трех метчиков. Гаечные метчики помогают для нарезания резьб в сквозных подробностях малой толщины как вручную, так и на станках и изготовляются с удлиненным хвостовиком для собирания на нем нарезаемых гаек.
Номинальный диаметр нарезаемой резьбы —от 2 до 33 мм. Машинные метчики употребляются для нарезания глухих резьб диаметром от 2 до 52 мм на сверлильных, револьверных и агрегатных станках, на станках-автоматах и полуавтоматах.
Плашками нарезают крепежные резьбы в основном на болтах, винтах и шпильках вручную и на револьверных станках, станках-автоматах и реже на токарных.
Плашки бывают круглые, раздвижные и особые (для нарезания труб). Круглые плашки изготовляются цельными, разрезными и трубчатыми. Круглыми плашками нарезают резьбы диаметром от 1 до 52 за один проход. Цельные плашки владеют болыц0д жесткостью и снабжают получение чистой резьбу но они” малопроизводительны и скоро изнаши! ваются.
Разрезные плашки в отличие от цельных имеют прорезь (0,5…1,5 мм), что разрешает регулировать диа. метр нарезаемой резьбы в пределах 0,1…0,25 мм. Вслед, ствне пониженной жесткости этих плашек резьба полу, чается с не хватает полным профилем.
Рабочая часть круглой плашки с обоих торцев имеет режущую (заборную) часть, что позволяет нарезать резьбу как одной, так и второй стороной. Распределение работы резания между отдельными режущими элементами обеспечивается углом в плане