Размерная обработка миниатюрных изделий
Ввиду локального характера действия лазерного излучения большим диаметром отверстий, каковые целесообразно прошивать, нужно считать 0,5—1,0 мм. Самый рационально использование лазера чтобы получить отверстия микронных размеров, впредь до 2—3 мкм, в материалах, механическая обработка которых затруднена либо неосуществима. К ним относятся керамика, стекло, бриллианты, разные технические камни, двуокись кремния, окись алюминия, высокопрочные, различные сплавы и нержавеющие стали.
При прошивании отерстий в материалах с нехорошей теплопроводностью благодаря недостаточного теплообмена появляются большие температурные напряжения, вызывающие появление микротрещин, а в некоторых случаях и приводящие к раскалыванию изделия. Для предотвращения этих нежелательных явлений обработку таких материалов ведут серией импульсов ограниченной энергии. Наряду с этим появляющиеся температурные напряжения находятся в допустимых пределах и неспешно исчезают.
Напротив, материалы с высокой теплопроводностью, такие как медь, алюминий, бериллиево-бронзовые сплавы, ввиду интенсивного рассеяния тепла за время импульса не хорошо поддаются обработке лазерным лучом.
При обработке лазерным лучом твёрдость материалов и механическая прочность не имеет значения. Главным причиной есть степень поглощения (адсорбции) энергии. Прозрачные материалы, прекрасно отполированные поверхности, имеющие высокую отражательную свойство, интенсивно рассеивают энергию лазерного излучения, преломляя и отражая луч. Обработка таких материалов затруднена.
Для улучшения обрабатываемости прозрачных материалов на их поверхность наносят слой непрозрачного материала, прекрасно поглощающего свет. испарения материала и Продукты плавления удаляются из территории обработки.
Режимы обработки. Фактически выбор режимов обработки лазерным лучом при получении отверстий сводится к определению плотности фотонного потока, энергии излучения, условий фокусировки и длительности импульса луча. Для их сплавов и металлов плотность потока должна быть больше 106—107 Вт/см2.
Для получения цилиндрических отверстий цилесообразно применять световую трубку, образующуюся при определенном размещении лазера и фокусирующей совокупности.
Установление оптимальных параметров обработки световым лучом создают посредством таблиц и номограмм, взятых умелым методом. При обработке отверстий в большинстве случаев рекомендуется сначала произвести 10—20 импульсов на умелых примерах для того, чтобы добиться стабилизации режимов.
Обработка изделий из жёстких неметаллических материалов. Одним из перспективных направлений лазерной разработке есть обработка отверстий в жёстких материалах: керамике, кварце, бриллианте, рубине, сапфире и т. д. Изюминкой лазерной обработки отверстий в этих материалах есть опасность появления трещин в зоне обработки, возникновение и растрескивание заготовок-большого (толщиной 0,015—0,020 мм) дефектного слоя, что имеет рыхлую, пористую структуру, отличающуюся механическими и теплофизическими особенностями от главного материала.
Происхождение дефектного слоя обусловливается наличием, при одноимпульсной обработке большого количества жидкой фазы, остывающей на стенках прошиваемого отверстия. Для устранения опасности появления трещин, уменьшения толщины дефектного слоя и получения приемлемого для целей практики качества поверхности обработку ведут многократным действием световых импульсов, энергия которых уменьшена приблизительно на один порядок при одновременном таком же оскращении их длительности. Для получения достаточной производительности обработки увеличивают частоту следования импульсов как минимум также на один порядок.
Так, чтобы получить отверстия диаметром 0,05—0,07 мм в рубиновой либо сапфировой заготовке толщиной 0,4—0,5 мм за 3—5 импульсов нужная энергия одного импульса равна 0,05— 0,08 Дж при длительности импульса 70—150 мкс. С учетом утрат энергии в оптической совокупности (на отражение, рассеивание, диафрагмирование и поглощение) лазер с активным элементом из стекла с неодимом обязан снабжать энергию импульса 0,1—0,15 Дж при расходимости луча не более 40—50 мин. Этот режим генерации с частотой следования импульсов 5—10 Гц при импульсной накачке 50—90 Дж возможно реализовать в лазере на стандартном стандартной лампе и активном элементе оптической накачки.
Приемы прошивания отверстий. Оптические квантовые генераторы, в силу природы генерируемых световых лучей, снабжают получение круглых отверстий разных глубины и диаметров. Обработка отверстий сложных конфигураций вероятна методом последовательного перемещения луча, т. е. «фрезерованием» по контуру либо методом формирования в зоне обработки светового поля соответствующей конфигурации.
Последнее производится при помощи соответствующих диафрагм, и посредством цилиндрической оптики, владеющей свойством изменять симметрию поля.
Требуемая форма обрабатываемому отверстию придается методом установки на пути луча диафрагмы с пропускной щелью соответствующей конфигурации либо благодаря применению особых линз, дающих фокусировку луча в форме, хорошей от круговой. Так возможно прошивать круглые, прямоугольные, звездообразные и другие формы отверстий.
Но обработка с применением диафрагм ведет к понижению эффективности применения излучения лазера. Исходя из этого предпринимаются попытки для обработки фигурных пазов и отверстий сложной конфигурации использовать излучатели, снабжающие требуемый профиль. Достигается это за счет разной расходимости светового потока в направлениях, перпендикулярных оси излучения.
Такое излучение разрешает при фокусировании его простыми оптическими совокупностями с осевой симметрией взять в зоне обработки конфигурацию светового пятна, соответствующую характеру асимметрии исходного излучения. Разность в расходимости по разным направлениям определяет размеры и конфигурацию светового пятна.
Вопросы точности обработки. Учитывая малые размеры обрабатываемых лучом лазера конструктивных элементов изделий актуальным являются вопросы точности лазерной обработки. На точность обработки воздействуют многие факторы, главными из которых являются неточность позиционирования обрабатываемого настройки и изделия оптической совокупности, нестационарность оптической накачки и режима излучения и др.
Помимо этого, влияют процессы старения и тепловые явления оптической совокупности. Любая из приведенных обстоятельств оказывает определенное влияние на точность обрабатываемых конструктивных элементов. Анализ главных обстоятельств, вызывающих неточности лазерной микрообработки, совершён в работе.
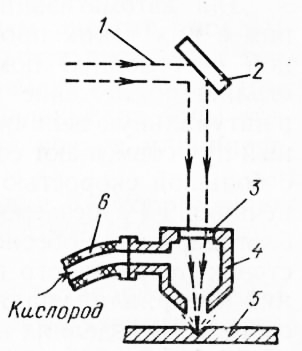
Рис. 1. Устройство для лазерной резки
Выброс жидкого материала из кратера есть как правило нежелательным, поскольку кратер в большинстве случаев не редкость окружен разными по величине застывшими каплями выкинутого материала — грата, что удаляют механическим методом. В случае если наличие грата нежелательно, то на обрабатываемую поверхность накладывают узкую пленку либо фольгу. Наряду с этим грат и кратер образуются на ней. По окончании удаления фольги
остается чистое отверстие. На обратной стороне обрабатываемого изделия грата не образуется. Каналы, прошитые лучом лазера, как правило имеют коническую форму (больший входной и меньший выходной диаметры).
Получение каналов, глубина которых существенно превышает диаметр отверстия, в большинстве случаев осуществляется серией импульсов. Наряду с этим луч фокусируется на поверхности изделия, а стены появившегося канала отражают лучи, фокусируя их на дно. В следствии имеет место некое улучшение качества поверхности стенок прошиваемого канала.
Получение микропазов и резка. Возможность острой фокусировки лазерного луча все шире применяют для получения узких пазов и щелей. Ширина реза малый, исходя из этого лазерный луч используют для резки материалов с малыми отходами.
Так, к примеру, при резке титановых сплавов возможно применять луч лазера, разрушающее воздействие которого интенсифицировано кислородной средой. Благодаря наличия кислорода в зоне реза появляется энергично протекающая экзотермическая реакция окисления с выделением большого количества тепловой энергии. Данный процесс происходит в основном под действием химических реакций, исходя из этого мощность самого оптического квантового генератора маленькая.
Диаметр сфокусированного луча при резке в большинстве случаев равен 0,05—0,15 мм.
Генерируемый лазером луч из горизонтального направления отклоняется в вертикальное посредством зеркала, а после этого фокусируется посредством линзы, помещенной в верхней части мундштука (рис. 1). Листовой материал, подвергаемый резке, движется с определенной скоростью. Кислород к месту действия лазерного луча подается по шлангу. Скорость перемещения страницы должна быть согласована с режимами резания.
Так, к примеру, резание нержавеющей стали толщиной 1,3 мм на лазере мощностью 250 Вт производилось со скоростью 0,7 м/мин при ширине реза 0,5 мм; страницы из титаного сплава и циркония толщиной по 0,5 мм разрезались со скоростью 1,5 м/мин при ширине реза соответственно 0,4 и 0,5 мм. Кроме кислорода в зону резания время от времени подается пар.
Для автоматизации профильной резки материалов, прореза-ння в них узких прорезей используют станки с фотокопировальной совокупностью. Посредством фотокопировальной головки осуществляется слежение за линиями чертежа, что делают в натуральную величину. С целью интенсификации процесса лазерный луч совмещают со струей кислорода либо воздуха, выходящего с громадной скоростью из отверстия соосно расположенного наконечника.
Разрезаемое изделие помещают под наконечником, благодаря чему обеспечивается параллельность и высокая чистота, стенок прорезаемого паза. Газ, образующийся в ходе испарений материала, удаляется посредством вытяжной вентиляционной совокупности. В изделиях из карбида кремния, асбеста и других труднообрабатываемых материалов ширина пазов может составлять 0,2—0,3 мм. Изделие перемещается совместно со столом в двух координатных направлениях по командам следящей головки.
Обработка может производиться непрерывно либо с промежуточными выключениями лазера, что позволяет приобретать пазы с перемычками. Для обеспечения безопасности обслуживания станок оборудован блокировкой, исключающей возможность включения лазера до установки изделия.
Газовый лазер, трудящийся на смеси гелия с неоном, употребляется для фрезерования узких пазов методом импульсного действия с перекрытием отдельных кратеров. Взяты пазы шириной 0,007 мм и более в нержавеющей стали. Обширно употребляется луч лазера для резки узких железных пленок, нанесенных на подложку из стекла либо другого материала.
Твердотельные лазеры применяют для нанесения ультратонких делений и штрихов на нониусах, лимбах и линейках устройств.
Оборудование для лазерной разработки. Отечественная индустрия производит технологические лазерные установки-разной мощности. Большая часть изготавливаемых лазерных установок носит универсальный темперамент и по заложенным в них основным характеристикам и технологическим решениям (прежде всего энергетическим) предназначено для исполнения широкого-круга операций микрообработки.
Лазерная установка К-ЗМ предназначена для сварки и прошивания отверстий. Оптическая совокупность со сменными объективами разрешает сфокусировать излучение в пятно от 0,003 до 0,3 мм при расстоянии между плоскостью и объективом предметного столика от 0,15 до 28 мм. Повышений визуальной совокупности — от 29х до 675х.
Большая плотность мощности в фокусе до 108 Вт/см2, что разрешает прошивать отверстия диаметром от 0,003 до 0,2 мм в металлах толщиной до 1 мм, в зависимости от их теплофизических особенностей, и создавать сварку проводников диаметром до 0,2 мм и железной фольги. Универсальный рабочий сток с вертикальным ходом 25 мм перемещается в двух перпендикулярных направлениях посредством микрометрических винтов. Точность отсчета перемещения —0,01 мм.
Установка снабжена встроенным цифровым измерителем энергии, показывающим энергию излучения каждого импульса в джоулях с точностью до сотых его долей. Деятельный элемент — рубин. Для более стремительной эвакуации продуктов расплавления из территории действия лазерного луча используют сжатый воздушное пространство либо инертный газ давлением 5—25 атм.
Для прошивания отверстий не считая установки К-ЗМ используют кроме этого лазерные установки К-ЗМБ, КВАНТ, КАРАВАН, ГОС-ЗОМ, ГОР-100М, ГОР-ЗОО, ГОС-1000 и др.
Универсальная лазерная технологическая установка КВАНТ может трудиться как с лазерной головки, активным элементом которой есть синтетический рубин (1-я головка), так и с головкой, активным элементом которой есть стекло с неодимом (2-я головка).
Большая энергия импульса 1-й лазерной головки равна 2 Дж при частоте их повторения три импульса в 1с, а 2-й головки соответственно 15 Дж при частоте 6 импульсов в 1 мин. Оптическая совокупность установки разрешает сфокусировать луч в пятно радиусом от 0,002 до 0,5 мм. При применении цилиндрической оптики обеспечивается получение светового луча в форме линии толщиной 0,05 мм, что разрешает осуществлять прорезание узких пазов, щелей и создавать резание.
Установка снабжена двумя предметными столами. Первый стол универсальный. Он имеет два взаимно перпендикулярных перемещения посредством микрометрической подачи. Большой движение — 50 мм. Точность установки — 0,01 мм. Второй стол в одном направлении перемещается через передачу от электродвигателя со скоростью, изменяющейся в пределах от 18 до 180 мм/мин.
В другом направлении перемещение стола производится вручную. Величина обоих перемещений — 200 мм. Точность установки — 0,05 мм.
Для получения отверстий сложной конфигурации используют генератор КАРАВАН. Он снабжен цилиндрической оптикой, существенно расширяющей его технологические возможности.
Определенными технологическими возможностями владеют замечательные оптические квантовые генераторы с рубиновым активным элементом ГОР-ЮОМ и ГОР-ЗОО. С их помощью возможно создавать операции прошивания отверстий, сварки и пайки микросоединений, и распыление вещества в вакууме. Конструкция генераторов блочная.
Главными блоками генератора ГОР-100М являются оптическая головка, две конденсаторные батареи, холодильное устройство, пульт контроля и управления.
Генератор ГОР-300 складывается из шкафа и оптической головки, в котором размещены конденсаторная батарея, высоковольтный выпрямитель, охлаждающее устройство, органы контроля и управления. Для оптической накачки применяют две ксеноновые импульсные лампы. Высоковольтный блок питания снабжает заряд конденсаторных батарей неспециализированной емкостью до 4400 мкФ до напряжения 3,8 кВ. В генераторе применено водяное охлаждение по замкнутому циклу.
Большая энергия излучения — 300 Дж при частоте повторения 5 импульсов в 1 мин. Большие энергии излучения генераторов ГОР-100М и ГОР-300 снабжают получение отверстий разных диаметров в тугоплавких и сверхпрочных материалах.
Рис. 2. Лазерная установка для получения узких прорезей
Более замечательным, если сравнивать с обрисованными генераторами, есть генератор ГОС-1000, активным элементом в котором есть стекло с присадкой неодима. Большая энергия его излучения 1000 Дж при режиме работы — 1 импульс за 6—8 мин.
Лазерный луч применяют для получения узких прорезей в трафаретах, масках, шаблонах, применяемых при производстве интегральных схем.
На рис. 91 приведена схема лазерной установки для получения узких прорезей (шириной 0,01 мм). Луч, генерируемый лазером, через совокупность плоских зеркал, линзы, модулятор и десятигранное вращающееся зеркало направляется на заготовку маски.
Стол с укрепленной на нем заготовкой маски может перемещаться. В следствии действия громадного количества импульсов отверстия сливаются в целые линии -— пазы толщиной 0,01—0,02 мм.
Оборудование с программным управлением. Процессы лазерной обработки стремятся автоматизировать, поскольку тяжело обрабатывать вручную подробности, имеющие малые размеры. На рис. 3 продемонстрирована принципиальная схема станка с цифровым программным устройством.
Координация перемещений стола с работой лазерной головки осуществляется блоком, управляющим посредством особого детекторного устройства. Головка детекторного устройства посредством волоконной оптики улавливает луч лазера в момент завершения образования им сквозного отверстия, и световой сигнал направляется к детекторному устройству, которое дает команду на включение работы цикла и выключение лазера позиционирования стола станка. По завершении позиционирования стола машинально включается излучение лазера, и цикл обработки отверстий повторяется до образования всех отверстий в соответствии с закодированной на перфоленте программой.
Используемая оптическая аппаратура снабжает возможность надлежащей фокусировки световой энергии на изделии и постоянного наблюдения за процессом прошивания. Это достигается методом проецирования увеличенного изображения территории обработки на экран, смонтированный на верхней части станка.. Изображение рабочей территории на экране приобретают посредством проекционного микроскопа.
Оно будет в фокусе, в случае если луч лазера, проходящий через линзу, окажется сфокусированным в некоей точке, находящейся ниже поверхности обрабатываемого изделия. В большинстве случаев фокус обязан пребывать приблизительно на половине толщины обрабатываемого материала. Особое устройство с дихроматичным зеркалом мешает попаданию луча лазера на экран.
В целях предохранения объектива устройства фокусировки от брызг материала, расплавленного лазерным лучом, под объективом размещают особый, непрерывно поворачивающийся экранирующий диск, что меняют по окончании его загрязнения.
Стол станка смонтирован на сварном основании. Продольные и поперечные перемещения стола в направлении осей X и Y осуществляется от двух свободных механизмов. Для вертикального • перемещения стола, в направлении оси Z, употребляются два шариковых ходовых винта, исключающих возможность перекоса стола кроме того при выдвинутом его положении.
Яркий импульс на перемещение по координатам X, Y и Z осуществляется от совокупности цифрового программного-управления. Рабочая территория станка закрыта двумя дверками, снабженными тумблерами, блокирующими работу станка при незакрытых дверках. В качестве материала для генерирования луча лазера применяют кальциевый вольфрамит с присадкой неодима.
При каждом импульсе лазер генерирует световую энергию, равную 1 Дж. Частота пульсации лазера равна 5 импульсам в 1 с, но работа лазера возможно форсирована до 10 импульсов в 1 с.
Рис. 3. Схема лазерного станка с цифровым программным управлением
Кальциевый вольфрамит применен в качестве активного элемента вместо синтетического рубина не только как более недорогой в изготовлении, но и как снабжающий лучшую работу и большую мощность лазера. Световой луч, генерируемый лазером, может прошивать отверстие диаметром до 0,75 мм в материале толщиной не более 5 мм. При прошивании отверстий в изделиях из нержавеющей стали требуется приблизительно 3 импульса, дабы по-.лучить отверстие глубиной 2,5 мм.
Отверстия в продольном сечении имеют коническую форму.
В лазерных установках с цилиндрической оптикой, генерирующих параллельно направленные световые лучи, смогут быть взяты отверстия с высокой степенью параллельности образующих кроме того в том случае, если глубина отверстий в 20 раз превышает их диаметры.
Имеются станки для прошивания отверстий в алмазных волоках для притягивания проволоки диаметром от 0,01 мм. Отверстия приобретают способом круговой вырезки. Наряду с этим они имеют некую конусность в продольном сечении и приближающиеся к окружности в поперечном сечении.
По окончании образования отверстий их калибруют. Отверстия пригодны для алмазных волок. Территория •обработки при прошивании не проецируется на экран, а отмечается через особую телевизионную установку.