Станки для профильного шлифования
Для профильного шлифования используют универсальные плоскошлифовальные и круглошлифовальные станки повышенной точности, профилешлифовальные станки с ручным и программным управлением и др.
Для изготовления инструмента самые удобными являются плоскошлифовальные станки с продольным ходом стола 600..800 мм, оснащенные медлено регулируемой гидравлической совокупностью и свободным ручным продольным и поперечным перемещениями стола.
На совершенно верно настроенном плоскошлифовальном станке с верно выбранным шлифовальным кругом для чистовой обработки возможно взять точность линейных размеров ±0,01 мм, шероховатость поверхности ±1’ и угловые величины Л?а = 0,32…0,16 мкм.
Универсальный плоскошлифовальный станок модели ЗГ71 повышенной точности с горизонтальным прямоугольным столом приведен на рис. 1. Обработка подробностей производится периферией круга. Простые фасонные подробности возможно обрабатывать непрофилированным и профилированным кругами.
К главным узлам станка относятся станина I, колонка II, крестовый суппорг III, механизм ручного продольного перемещения стола IV, механизм продольного реверса стола V, стол VI, механизм поперечного реверса стола VII и поперечной подачи VIII, шлифовальная головка IX, механизм вертикальной подачи X и сливной бак XI.
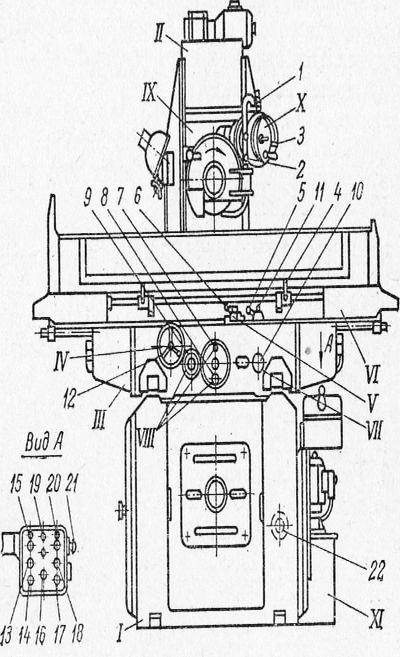
Рис. 1. Плоскошлифовальный станок модели ЗГ71.
Станина станка представляет собой твёрдую коробчатую отливку, на верхней части которой закреплены металлические термически обработанные V-образные направляющие. В станины размещены электроаппаратура и гидроагрегат.
На верхней части колонки установлен редуктор, предназначенный для ускоренного перемещения шлифовальной головки.
На крестовом суппорте имеются взаимно перпендикулярные направляющие. По верхним направляющим перемещается стол с рабочей поверхностью 630X200 мм. Перемещение в продольном направлении он приобретает от гидравлического цилиндра, расположенного между его направляющими.
В нижней части стола размещены механизмы поперечной подачи, продольного перемещения стола, продольного реверсирования его, и распределительная и гидравлическая панели. Шлифовальная бабка перемещается по направляющим стойки, установленной на станине.
Шлифовальный круг размером 250X25X75 мм, закрепленный на шпинделе, основное перемещение приобретает от электродвигателя с N — 2,2 м и квт = 2860 об/мин. Частота вращения шпинделя — 2700 об/мин, а скорость резания v = 33,5 м/с. Вертикальную подачу круга возможно создавать вручную рукояткой 3 либо машинально рукояткой 1. Громаднейшее вертикальное перемещение шлифовальной бабки 375 мм.
Поперечная подача стола кроме этого возможно ручной (посредством маховичка) и автоматической (по лимбам). Громаднейшее поперечное перемещение стола 235 мм. Цена деления лимба ручной подачи равна 0,05 мм, а автоматической—0 ,01 мм. Продольная подача стола возможно ручной и автоматической от гидравлической совокупности. Мельчайшее перемещение стола — 70 мм, а громаднейшее — 710 мм.
В механизме ручного продольного перемещения предусмотрена блокировка, которая машинально отключает зубчатое колесо от зубчатой рейки при установке рукоятки в положение «Пуск стола». При ручном перемещении стола в момент работы гидропривода рукоятка должна быть в положении «Разгрузка гидропривода».
Механизм продольного реверса стола снабжает переключение золотника реверса при крайних положениях стола, каковые устанавливаются в зависимости от длины обрабатываемых подробностей посредством упоров.
Органы управления станка: 1 — рукоятка установки ьЬшчины автоматической вертикальной подачи; 2 — рукоятка крана регулирования подачи рабочей жидкости-3 — маховичок ручной вертикальной подачи; 4 — упоры продольного реверса стола; 5 — рукоятка скорости перемещения стола; 6 — рукоятка ручного продольного реверсирования стола; 7 — маховичок ручной поперечной подачи стола; 8 — лимб микрометрической поперечной подачи стола; 9 — лимб установки величины автоматической поперечной подачи; 10 — реверсирования и кнопка включения поперечной подачи; 11 — рукоятка «Пуск стола», «Стоп стола» и «Разгрузка гидропривода»; 12 — рукоятка ручного продольного реверсирования стола; 13 — кнопка «Пуск шпинделя»; 14 — кнопка «Все стоп»; 15 — кнопка-тумблер магнитной плиты; 16 — барабанный тумблер ускоренного перемещения шлифовальной головки; 17—кнопка «Стоп гидропривода»; 18 — кнопка «Пуск» гидропривода; 19 – лампочка сигнализации «Станок включен»; 20 — тумблер освещения; 21 — тумблер режима работы «С плитой» и «Без плиты»; 22 — вводный пакетный выключатель.
Рис. 2. Схемы шлифования угловых участков профиля плоским кругом.
Как уже отмечалось, на плоскошлифовальных станках возможно обрабатывать фасонные подробности непрофили-рованным, т. е. плоским, кругом. Им обрабатывают поверхности, профиль которых образован прямыми линиями, в тех случаях, в то время, когда шлифуемую поверхность возможно совместить с периферией либо торцем шлифовального круга. Для данной цели используют особые приспособления.
На рис. 2 приведены схемы обработки на плоскошлифовальном станке угловых участков профиля плоским кругом посредством синусного кубика (рис. 2, а), синусной линейки (рис.
2,б), синусных центров (рис. 2, б), синусного магнитного столика (рис. 2, г), приспособлений для шлифования многогранных подробностей (рис.
2, д), синусных магнитных призм (рис. 2, е).
Непрофилированным кругом возможно обработать с одной установки любой незамкнутый профиль инструмента (подробности), составленный из дуг окружностей и прямых линий, посредством универсального приспособления для координатного шлифования. При применении копирных приспособлений возможно обрабатывать замкнутый профиль подробности либо отдельные криволинейные участки ее профиля.
Шлифование профилированным кругом есть одним из распространенных способов воспроизведения фасонных поверхностей.
Для расширения технологических возможностей плоскошлифовальных и круглошлифовальных станков их оснащают оптическими устройствами, благодаря которым увеличенный контур круга и детали проецируется на экран. Оптическая совокупность закрепляется на столе, станка и перемещается вместе с подробностью.
Станки для обработки профилей круглых подробностей. Шлифование цилиндрических подробностей со сложным профилем возможно осуществлять на универсальных кругло-шлифовальных станках (рис. 3), где головка и передняя бабки с шлифовальным кругом смогут поворачиваться около вертикальной оси и устанавливаться под любым углом с точностью ±5’.
Потому, что круг установлен под углом, наклонные участки профиля возможно обрабатывать его периферией либо боковыми сторонами без профилирования.
Рис. 3. Круглошлифовальный станок.
Станок имеет мобильной упор ограничения продольного перемещения стола, подставку для концевых мер длины, индикаторный указатель продольного перемещения стола, заднюю бабку. Органами управления являются: рукоятка реверса стола, рукоятка упора, маховик продольной подачи стола, маховик механизма подачи шлифовальной бабки, рукоятка переустановки лимба врезной подачи шлифовальной бабки, рукоятка отвода пиноли задней бабки и рукоятка зажима пиноли задней бабки.
Станок имеет бесступенчатое регулирование частот вращения подробности. Он снабжен балансировочным механизмом, укрепленным на фланце круга. Очистка охлаждающей жидкости от абразивной пыли и металлической стружки производится посредством магнитного сепаратора.
Обработка профиля у подробностей маленького диаметра осуществляется на специальных станках с двусторонней шлифовальной головкой.
Модернизированные универсально-заточные станки типа ЗА64М эргономичны тем, что имеют поворотную шлифовальную головку с двусторонним шлифовальным шпинделем и поворотный стол. Обработку подробностей на них рекомендуется осуществлять кругами диаметром 250 мм, дабы круг поддерживалпределы шлифовальной головки. Частоту вращения шпинделя направляться снижать до 1900—2000 об/мин.
Станок нужно оснастить передней бабкой с задней вращения бабкой и приводом детали с центром.
Профильное шлифование возможно осуществлять и на резьбошлифовальных станках. Их используют в тех случаях, в то время, когда профиль шлифуется на маленькую глубину и имеет мелкие радиусы закругления с твёрдыми допусками. Шлифование создают кругом относительно громадного диаметра, продолжительнее сохраняющим острые кромки.
На резьбошлифовальных станках возможно обрабатывать и плоские подробности при наличии приспособления с возвратно-поступательным перемещением стола.
Профилешлифовальный станок модели 395М рекомендован для обработки сложных наружных профилей пуансонов, составных матриц и других аналогичных подробностей любого профиля.
Способ обработки профиля основан на визуальном совмещении контура обрабатываемой подробности, увеличенного в 50 раз особой оптической совокупностью и спроецированного на экран, с чертежом заданного профиля, вычерченного на прозрачной кальке с повышением в 50 раз и закрепленного на экране.
Оптическая схема профилешлифовального станка модели 395М продемонстрирована на рис. 4. От источника света лучи падают на наклонно установленный отражатель, что направляет их на обрабатываемую подробность.
Рис. 4. Схема оптического профилешлифовального станка модели 395М.
От подробности пучок лучей отражается в обратном направлении, проходит через щель в систему и отражатель повышения и проецируется в прямом рабочем изображении на зеркало 6, которое отражает лучи на стеклянный экран. Чертеж закрепляется между экранными стеклами. Профиль обрабатываемой подробности проецируется в виде резкого чёрного изображения на ярко освещенном экране.
Методом снятия припуска приобретают профиль подробности до 7-го квалитета с шероховатостью обработанной поверхности Ra~ 1,25…0,63 мкм.
Обработка осуществляется при перемещении шлифовального круга 10 по двум взаимно перпендикулярным координатам за счет перемещения двух суппортов шлифовальной головки вручную либо механически. Кроме вращательного и двух поступательных перемещений в горизонтальной плоскости шлифовальный круг имеет возвратно-поступательное перемещение, что снабжает обработку профиля по всей высоте подробности.
Деталь устанавливается на станке так, дабы по всему контуру либо его части, подлежащей обработке, оставался припуск. Подробности, изображение профиля которых не помещается на экране, шлифуются по участкам. Переход от одного участка к второму осуществляется за счет перемещения суппорта стола, на котором закреплена подробность.
В тех случаях, в то время, когда по одному чертежу обрабатываются повторяющиеся профили, перемещение суппортов стола контролируется посредством концевых мер длины. В то время, когда же на соседнем участке шлифуется профиль другой конфигурации, чем прошлый, чертеж-калька перемещается либо заменяется, причем на новом участке чертежа либо на новом чертеже должна быть линия уже обработанной части профиля, являющаяся началом нового участка. В этих обстоятельствах перемещение суппортов стола осуществляют контроль методом совмещения части контура обработанного участка профиля с линией чертежа.
Станок позволяет обрабатывать подробности, не снимая их со стола, со большими размерами профиля, вписывающегося в прямоугольник 150X60 мм.
Правка кругов. Способ копирования разрешает осуществлять профильное шлифование на универсальном оборудовании, к примеру на плоскошлифовальных станках высокой точности с горизонтальным шпинделем и прямоугольным столом.
Точность обработанных поверхностей при профильном шлифовании зависит от точности правки шлифовальных кругов, каковые профилируют бриллиантами либо роликами. Профилирование бриллиантами производится посредством разных приспособлений. Имеются приспособления для профилирования лишь наклонных либо лишь дуговых участков, и универсальные, каковые профилируют как наклонные, так и дуговые участки.
Разглядим кое-какие из приспособлений.
Для профилирования круга по дуге окружности используют приспособления, у которых острие бриллианта смещено относительно оси алмазодержателя на величину заправляемого радиуса. Бриллиант устанавливают посредством калиброванной концевых и оправки мер. Порядок правки круга следующий. Основанием (рис. 5) приспособление устанавливают на стол шлифовального станка.
Бриллиант, закрепленный винтом в алмазодержателе, подводят к калиброванной оправке диаметром d. В этом положении алмазодержатель закрепляют винтом 7. Зная радиус профиля круга, определяют величину блока концевых мер: li = d/2±R, где d — диаметр калиброванной оправки, a R— радиус шлифуемой поверхности, в мм. В случае если круг должен иметь вогнутость, принимают символ « + », в случае если выпуклость — символ «—».
Блок концевых мер устанавливают между плоскостью и кольцом стойки. Затем кольцо закрепляют, винт ослабляют и алмазодержатель отводят назад для удаления блока концевых мер и калиброванной оправки. После этого алмазодержатель перемещают до соприкосновения торца кольца с плоскостью стойки и закрепляют винтом.
Рис. 5. Приспособление для правки круга по дуге окружности.
Приспособление подводят к поверхности круга и, поставив бриллиант перпендикулярно его образующей, гайкой закрепляют стойку. Сначала правят круг по цилиндру до получения ровной поверхности. После этого острие бриллианта устанавливают посредине круга. В этом положении стол фиксируют упором.
Для профилирования круга ослабляют гайку так, дабы стойка вольно вращалась. Поворачивая стойку с бриллиантом за рукоятку и информируя бриллианту поперечную подачу, создают профилирование круга по дуге окружности.
Универсальное приспособление, продемонстрированное на рис. 6, предназначено для профилирования кругов с разным сочетанием прямых и Дуговых участксз, и одноименных и разноименных дуг. На основании находится поворотная каретка, в пазах которой может перемещаться суппорт.
По верхнему выступу суппорта передвигаются салазки со стойкой, несущей алмазодержатель. В центральном положении салазки фиксируются штифтами. При выдвинутых штифтах салазки и алмазодержатель смогут вольно перемещаться в обе стороны от центрального положения.
Поворотная часть приспособления возможно закреплена в требуемом положении либо вольно вращаться посредством рукоятки.
Профилирование кругов производится по элементам. Для профилирования дуговых участков алмазодержатель, закрепленный в стойке, вместе с салазками, суппортом, что застопорен винтами и штифтами, и поворотной кареткой посредством рукоятки приобретает вращательное перемещение относительно основания приспособления. Радиус дуги устанавливается суппортом методом измерения микрометром расстояния между штифтом на каретке и планкойна суппорте.
В случае если это расстояние будет равняется постоянной величине данного приспособления, к примеру 75 мм, а алмазодержатель будет установлен по шаблону, то величина радиуса R будет равна нулю. В случае если суппорт сместить вперед на размер 75 — R, то приспособление будет настроено для профилирования на круге вогнутого дугового участка профиля. При обратном смещении суппорта на величину 75 + /? будет осуществляться правка дуги выпуклого профиля.
Профилирование прямолинейных участков производится возвратно-поступательным перемещением салазок. Для профилирования прямых участков круга, наклоненных к оси профиля, суппорт устанавливают в исходное положение, а каретку на угол 90° — а и фиксируют стопорной рукояткой.
Рис. 6. Универсальное приспособление для правки круга.