Точность обработки и шероховатость поверхности
Понятие о точности обработки подробностей. точные размеры и Форма деталей и изделий, входящих в изделие, определяются чертежом. Размеры подробностей, указанные на чертеже, именуются номинальными. Настоящие размеры подробностей, приобретаемые методом механической обработки заготовок на станках, будут отличаться-в большей либо меньшей степени от номинальных размеров.
При изготовлении подробностей нужно стремиться к получению подробностей правильных размеров, тогда подробности при сборке не будут нуждаться в дополнительной подгонке.
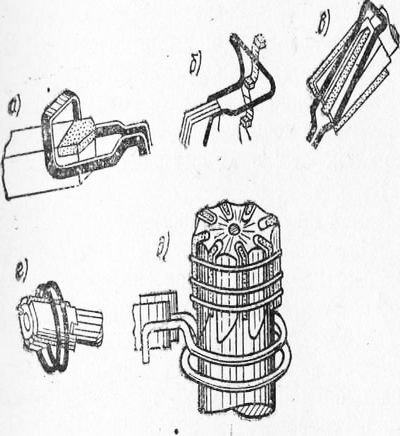
Рис. 1. Соединенние делянок продольными кромками: 1 — на ровную фугу, 2 — в гребень и паз, 3 — на рейку, 4 — в четверть; а — прямоугольный гребень, б — треугольный, в — трапецеидальный, г — «ласточкин хвост»
Точность обработки — показатель того, как изготовленная подробность по форме, шероховатости и размерам поверхности соответствует подробности, заданной по чертежу. Формируется она на первых стадиях технологического процесса.
На точность обработки воздействует последовательность факторов, в частности: свойства обрабатываемого материала, приёмы и методы обработки, выбор технологических баз, точность станков, приспособлений и инструмента, размеры обрабатываемых подробностей и т. д.
На точность обработки подробностей громадное влияние оказывают такие свойства древесины, как изменение влажности, внутренние напряжения, остающиеся в древесине по окончании сушки, твердость, неоднородность строения в продольном и поперечном направлениях, наличие пороков и др.
Изменение влажности обработанной подробности сопровождается трансформацией размеров подробности в поперечном сечейии и часто одновременным трансформацией формы (короблением).
Предотвратить изменение влажности древесины в ходе обработки возможно , если в обработку будет поступать древесина, высушенная до эксплуатационной влажности либо на 1… 2% ниже ее.
Эксплуатационная влажность — это влажность древесины в изделии во время его работы. В зависимости от условий и назначения изделий их эксплуатации эксплуатационная влажность будет разной. К примеру, для строительных изделий (окна, двери) она образовывает 12 … 15%, для мебели, подробностей внутренней отделки помещений, музыкальных инструментов — 6… 10%.
В цехах, где обрабатывают древесину, нужно поддерживать определенную влажность (34… 76%) и температуру (18…25 °С) воздуха.
Изменение влажности древесины может наблюдаться и в ходе ее обработки. Так, при склеивании и облицовывании растворимыми клеями подробности увлажняются водой, содержащейся в клеевом растворе. Дабы избежать отрицательного влияния увлажнения древесины на точность подробностей при предстоящей обработке, нужно подробности по окончании склеивания и облицовывания высушить снова до эксплуатационной влажности и лишь затем подвергать механической обработке.
Влияние способов обработки деталей на станках на точность обработки. Способы обработки деталей на станках для придания им точных размеров и определённой формы смогут быть разными. Различают работу по промерам подробностей, разметке раскраиваемого материала и настройке станка.
В зависимости от способа работы точность обработки подробностей будет разной.
Работа на станке по промерам содержится в том, что нужного размера подробности получают методом многократного прохода ее через станок (рейсмусовый, токарный). По окончании каждого прохода детали через станок ее замеряют и режущий инструмент устанавливают на снятие слоя таковой толщины, которая по окончании нового прохода обеспечила бы получение размера подробности вероятно ближе к заданному.
Точность обработки при таком способе работы будет зависеть от точности измерительного инструмента, употребляемого рабочим для замеров подробности, и от минимально вероятной толщины снимаемого слоя с подробности при приближении ее размера к требуемому. Фактически минимальный слой, снимаемый за один проход, к примеру на продольно-фрезерных станках, образовывает около 0,5 мм. Следовательно, в этом случае возможно достигнуть точности обработки в пределах ±0,25 мм.
Из этого видно, что способ работы по промерам неточен, помимо этого, он малопроизводителен. Исходя из этого он может использоваться при обработке маленького количества однообразных подробностей, т. е. в единичном производстве.
Работа на станках по разметке характеризуется тем, что на раскраиваемом материале либо на обрабатываемой подробности до запуска их в станок наносят карандашом метки, линии, точки, каковые показывают места будущих пропилов, отверстий. Доску, заготовку либо подробность устанавливают на столе либо на каретке станка так, дабы резание происходило по нанесенным меткам.
Точность обработки по разметке зависит от точности применяемой линейки, внимательности рабочего-разметчика, точности совпадения резов с метками и жёсткости и точности станка.
Способ работы по разметке кроме этого мало производителен, трудоемок, точность обработки подробностей еще меньше, она не превышает ±1 мм. Данный способ используют при обработки маленьких партий подробностей и при необходимости раскроя древесины с мельчайшими отходами.
В серийном и массовом йроизводстве главным способом работы есть работа на настроенных станках. Настройка — такое регулирование станка, приспособлений и инструмента, которое заблаговременно определяет положение детали на станке по отношению к инструменту для получения совершенно верно заданного размера. Настраивают станок в два этапа.
Сперва регулируют станок, приспособление и инструмент мерительным инструментом, после этого пропускают пробные подробности и по итогам их обработки создают окончательную регулировку. Наряду с этим направляться учесть, что настройка обязана вестись на пробных подробностях той же размеров и породы, каковые подлежат обработке. Точность обработки подробностей при работе на настроенных станках существенно выше, чем при работе по разметке и промерам.
Технологические базы. Для получения надлежащей точности обработки подробностей нужно, дабы подробности занимали определенное положение на станке по отношению к режущему инструменту. Это обеспечивается соответствующей базированием детали и настройкой станка в станке либо в приспособлении на протяжении обработки. Базирование подробности достигается закреплением либо прижимом ее к тем либо иным поверхностям станка либо приспособления.
Наряду с этим подробность лишается частично или полностью свободы перемещения. Базирование вероятно в том случае, если сама подробность имеет базисные поверхности.
Не считая базисных поверхностей у подробностей, устанавливаемых в приспособление и станок, имеются поверхности прижима и обрабатываемые поверхности. Базирование нужно не только при механической обработке на станках, но и при сборке. Различают конструктивные и технологические базы.
Конструктивные базы —это отправные поверхности, линии либо точки, на каковые ориентируется конструктор при разработке изделия. Они определяют положение разглядываемой на чертеже поверхности, линии либо точки подробности по отношению к вторым поверхностям, линиям либо точкам той же подробности, и положение одной подробности по отношению к вторым подробностям изделия. Конструктивными базами смогут быть осевые линии, поверхности и линии (грани) какой-либо подробности, от которых устанавливают размеры и довольно которых ориентируют положение вторых подробностей изделия.
Технологические базы — это поверхности, линии либо точки, на каковые ориентируются при обработке либо сборке сборочных единиц и деталей. Они смогут не совпадать с конструктивными. Технологические базы, со своей стороны, подразделяются на установочные и сборочные.
Установочной базой именуется совокупность поверхностей подробности, определяющих заданное положение ее довольно режущего инструмента. При наличии установочной базы возможно машинально добиться однообразной степени обработки всех подробностей в партии с заблаговременно заданной точностью.
Сборочная база — совокупность поверхностей, каковые определяют положецие подробности в изделии по отношению к вторым подробностям. К примеру, у поперечных брусков, собираемых в рамку на сквозной открытый шип, сборочной базой будут боковые поверхности их заплечики и шипов. Положение поперечных брусков в рамке по отношению к продольным брускам будет определяться этими поверхностями.
Базирование деталей на станке. Один из факторов, определяющих точность обработки, — верное базирование деталей на станке либо в приспособлении. Базирование подробности производится по установочной базе.
В зависимости от характера обработки подробности количество базирующих поверхностей, составляющих уста^ новочную базу, будет разным.
К примеру, для обработки подробности с одной стороны на рейсмусовом станке достаточно одной базирующей поверхности, которой будет помогать нижняя пласть подробности, опирающаяся на стол станка. Обрабатываемой поверхностью и в один момент поверхностью прижима будет верхняя пласть, противоположная базирующей. При такой же обработке детали на фуговальном станке нижняя базирующая поверхность в один момент будет и обрабатываемой.
При обработки подробности с двух, трех и четырех сторон число базирующих поверхностей должно быть соответственно громадным. К примеру, в четырехсторонних, калевочных, автошпунтовальных и других станках аналогичного типа обрабатываемые подробности базируются по двум базирующим поверхностям — по нижней плас-ти, лежащей на столе, и по’ одной из кромок, прижимаемой к боковой направляющей линейке.
Воздействие поверхности стола станка на подробность равносильно действию трех опорных точек, а воздействие боковой линейки — действию двух опорных точек.
При высверливании отверстий, гнезд и при нарезании шипов нужно, дабы подробность занимала определенное положение по отношению к инструменту, что достигается наличием не меньше шести опорных точек. Базирование подробностей в этом случае самоё сложное.
Базирование подробности будет тем правильнее, чем дальше расположены одна от второй опорные точки. Исходя из этого базировать подробность направляться так, дабы самая длинная и широкая сторона подробности (пласть) опиралась на стол станка, а долгая боковая сторона (кромка) прижималась к направляющей линейке. Торцы смогут прижиматься к маленьким упорам.
Для прижима подробностей при закреплении их в установленном положении используют особые приспособления. Громадные упрочнения прижима нежелательны, поскольку смогут привести к деформации подробности, что повлияет на точность обработки. Прижимы должны размешаться вероятно ближе к месту обработки подробностей.
При окончательной механической обработке подробности правильные размеры приобретают лишь при условии, в случае если черновые заготовки всей партии обработаны верно и одинаково. При обработке черновых заготовок создаются установочные базы для получения правильных подробностей. Для этого сглаживают пласти заготовок на одностороннем фуговальном станке либо в один момент сглаживают пласти и кромки на двустороннем фуговальном станке с получением между ними прямого угла.
В случае если заготовка имеет коробление, при фуговании базирующей поверхностью должна быть вогнутая сторона. При базировании выпукло’й стороной прямолинейность обрабатываемой поверхности не будет достигнута, по причине того, что положение заготовки на столе будет неустойчивым.
При работе на станке нужно смотреть за чистотой опорных поверхностей, на которых базируются подробности. Стружка, опилки и пыль на опорных поверхностях смогут привести к в точности обработки.
Точность, настройка и наладка станков, инструментов и приспособлений. На точность обработки подробностей громадное влияние оказывают- точность, настройка и наладка станков, и инструментов и приспособлений. Станки, приспособления и инструменты должны соответствовать определенным нормам геометрической точности, которая определяется точностью их изготовления и степенью износа.
ТоЧ;Ность изготовления характеризуется такими показателями, как прямолинейность рабочих поверхностей столов и кареток, перпендикулярность и параллельность осей ножевых каретки поверхности и валов стола, радиальное либо осевое биение валов и т. д. Различают три класса точности изготовления станков: повышенную, среднюю и низкую.
Деревообрабатывающие станки по классам точности распределяются приблизительно следующим образом: повышенной и средней точности— фрезерные, сверлильные, шипорезные; средней и низкой точности — круглопильные, ленточнопильные станки, лесопильные рамы и шпалорезные станки.
Периодическая наладка станков производится наладчиками. Она содержится в закреплении и установке элементов станка в таком положении, при котором станок будет трудиться нормально, т.е. отвечать нормам геометрической точности.
Перед обработкой каждой новой партии подробностей либо заготовок станочник настраивает станок. Настройка станка содержится в регулировании опорных и направляющих элементов станка, режущего приспособления и инструмента и их закреплении в определенном положении чтобы получить детали заданных формы и размеров.
Точность режущего инструмента во многом определяет точность обработки подробностей. Диаметр высверливаемых отверстий определяется диаметром сверл, ширина гнезд в подробностях — диаметром сверл либо шириной пильной цепочки. Точность профиля подробностей определяется точностью фрез профиля и изготовления ножей, а равномерность толщины обрабатываемой подробности по ее ширине — прямолинейностью режущей кромки (лезвия) ножа.
Точность изготовления режущего инструмента обязана отвечать определенным нормативам.
посадки и Допуски. Ранее было сообщено, что настоящие размеры подробностей, приобретаемые при обработке, смогут различаться от номинальных размеров, указанных в чертеже. Для обеспечения требуемого качества сопряжений (соединений) подробностей при сборке при массового производства изделий нужно, дабы отклонения настоящих размеров от номинальных были в допустимых пределах.
Нужная точность изготовления подробностей из древесных материалов и древесины регламентируется ГОСТ 6449.1—82… 6449.5—82, в которых установлены поля допусков и их предельные отклонения для посадки и линейных размеров, допуски углов призматических элементов, формы и расположения осей и расположения поверхностей отверстий для крепежных подробностей. Числовые значения допусков установлены по 9 квалитетам и 26 промежуткам номинальных размеров подробностей от 1 до 10 000 мм. Установлено 2 положения положений допуска полей и 11 полей отверстий допуска валов.
Подробности при сборке соединяются подвижно либо без движений. В подвижных соединениях между соединяемыми подробностями образуется зазор, в неподвижных — натяг. Чтобы получить в соединении необходимый зазор либо натяг, сопрягаемые размеры подробностей должны пребывать кроме этого в пределах допускаемых отклонений.
Величина зазора либо натяга определяет темперамент соединения, именуемого посадкой.
Критерием выбора тех либо иных посадок при конструировании изделий должны быть установленные допускаемые крайние значения зазоров либо натягов в соединениях составных частей, снабжающие требуемый уровень эксплуатационных показателей изделия (прочности, подвижности).
Посадки не стандартизированы и не имеют наименований. Образовывать посадки рекомендуется лишь в совокупности отверстия методом сочетания полей допусков валов и главных отверстий.
Взаимозаменяемость подробностей. Использование посадок и системы допусков при верном надлежащем состоянии и базировании деталей инструментов и оборудования дает возможность приобрести подробности с таковой точностью обработки, при которой их возможно собирать в сборочные изделия и единицы без дополнительной подгонки. Каждая подробность, изготовленная в той либо другой одноименной партии, обязана совершенно верно подняться на собственный место.
Такие подробности именуются взаимозаменяемыми.
Взаимозаменяемость — свойство сборочных единиц и деталей соединяться без личной дополнительной обработки (подгонки). При изготовлении взаимозаменяемых подробностей упрощаются процессы сборки, увеличивается уровень качества изделий, производительность труда, создаются благоприятные условия для автоматизации и конвейеризации сборочных процессов.
Контроль точности обработки подробностей предельными калибрами. Нужная точность обработки подробностей возможно взята лишь в том случае, если в ходе обработки размеры будут контролироваться. самый простой метод текущего контроля точности обработки — контроль предельными калибрами.
Предельные калибры разрешают без определения безотносительной величины размеров подробностей определять, находятся ли размеры в пределах заданного допуска.
Для контроля внутренних размеров отверстий, гнезд, проушин используют калибры-пробки, для контроля наружных размеров: длины, ширины, толщины, диаметра подробностей — скобы, для контроля уступов, высоты гребня шипа, глубины паза, ширины четверти — уступомеры.
Предельный калибр имеет два контрольных шаблона. Размер одного шаблона соответствует громаднейшему допускаемому размеру контролируемой подробности, размер другого — мельчайшему размеру. Один из шаблонов будет проходным, второй — непроходным. У калибра-пробки проходным будет шаблон мельчайшего размера.
У калибра-скобы, напротив, проходным будет шаблон громаднейшего размера.
Калибры бывают двусторонние, в то время, когда проходной и непроходной шаблоны расположены на различных финишах либо сторонах, и односторонние, в то время, когда оба шаблона расположены на одной стороне.
Шероховатость поверхности. Точность обработки на станках характеризуется не только точностью размеров и формы подробностей, но и шероховатостью поверхности
На обработанных поверхностях древесины смогут быть разные неровности: риски —следы режущего инструмента (выпивал); волнистость — чередующиеся возвышения и впадины волнообразной формы, приобретаемые при обработке вращающимися резцами; мшистость и ворсистость — неровности, вызванные разрушением связей с поверхностью отдельных волокон либо пучков волокон; выколы и вырывы целых пучков древесины — неровности разрушения. Неровности разрушения появляются, в большинстве случаев, при работе тупым инструментом либо инструментом с выкрошившимся лезвием. Перечисленные виды неровностей и будут характеризовать шероховатость поверхности древесины при обработке.
Требования к шероховатости поверхности древесины определяются назначением подробностей. самые жёсткие требования предъявляются к поверхностям, предназначенным для лакирования и полирования.
Для нормирования древесных поверхности материалов и шероховатости древесины ГОСТ 7016—82 устанавливает следующую номенклатуру параметров шероховатости: Rmmax— среднее арифметическое высот отдельных громаднейших неровностей на поверхности; Rm — громаднейшая высота неровностей профиля; Rz — высота неровностей профиля по десяти точкам; Ra — среднее арифметическое безотносительных отклонений профиля и Sz — средний ход неровностей профиля по впадинам. ГОСТ рекомендует кроме этого границы применения параметров по видам обработки древесины.
Рис. 2. Контроль размеров подробностей предельными калибрами: а — пробкой, б — скобой, в — уступомером; Ai — мельчайший предельный размер, Л2 — громаднейший предельный размер
Рис. 3. Приемы пользования предельными калибрами: а — скобой малых размеров, б — скобой громадных размеров, в — пробкой, г — уступомером
В производственных условиях шероховатость поверхности осуществляют контроль сравнением шероховатости обработанных подробностей с шероховатостью поверхности эталонных образцов, изготовленных из той же древесины и обработанных тем же видом резания, что и контролируемые.