Водные противопригарные краски
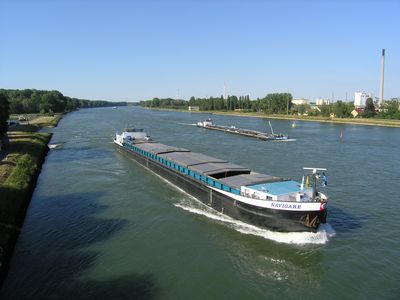
Водные противопригарные краски для сухих форм выпускают предприятия Всесоюзного объединения «Союзформоматериалы» в виде паст по ГОСТ 10772—64. На заводах-потребителях эти пасты разбавляют водой и получают краски требуемой плотности (табл. 20—22).
В производственной практике, готовя краски ‘ применительно к конкретным отливкам, централизованно изготовляемые пасты иногда применяют в качестве исходного противопригарного наполнителя, добавляя различные связующие.
Ниже приведены составы водных красок, приготовляемых предприятиями для собственных нужд. Описываемые водные краски распределены согласно классификации по роду зерновой основы (кислые, нейтральные, основные и углеродистые).
Кислые водные краски. Зерновую основу этих красок представляют кислые огнеупорные материалы: пылевидный кварц, дистен-силлиманит, кианит.
Встречающиеся в практике заводов краски, содержащие пылевидный кварц, иногда несколько отличаются от состава пасты СТ. Для повышения противопригарных свойств в состав краски вводят алюминиевую пудру, хлористые соли и марганцевую руду, а для лучшей седиментационной устойчивости добавляют подмыльный щелок. Марганцевая руда уменьшает смачивае-мость формы металлом и увеличивает поверхностное натяжение промежуточных силикатных расплавов.
В красках для чугунных отливок рекомендуют использовать кианит в сочетании с молотым коксом и графитом. Для использования в качестве наполнителя противопригарных красок при получении толстостенных отливок из углеродистой стали киани-товый концентрат целесообразно прокаливать при 750—800 градусов С
Нейтральные водные краски. К нейтральным относятся краски, в состав которых входит циркон, хромит (хромистый железняк) или корунд. Благодаря высокой огнеупорности и химической инертности этих наполнителей нейтральные водные краски применяют для получения отливок как из углеродистых, так и легированных сталей.
Цирконовые краски обладают низким коэффициентом линейного расширения, не отслаиваются и не растрескиваются под воздействием теплоты жидкого металла. Входящая в состав ряда красок, приведенных в табл. 24, сульфитно-спиртовая барда является поверхностно-активным веществом, хорошо разжижающим красочную суспензию. Это способствует лучшему проникновению краски в поры уплотненной формовочной смеси (сцеплению слоя краски с поверхностью формы) и повышает ее кроющую способность.
Вместе с тем, разжижая суспензию, ССБ (СДБ) снижает седиментационную устойчивость красок, что следует учитывать при использовании тяжелых нейтральных наполнителей. Противопригарная краскасодержит в качестве стабилизатора КМЦ, а вместо ССБ введена смола ПК-104. Краска такого состава более устойчива по сравнению с красками, содержащими бентонит и ССБ, и не расслаивается в течение 3 ч.
Поскольку цирконовый порошок обладает высокой дисперсностью, его применяют в качестве наполнителя красок, улучшающих чистоту литой поверхности отливок из легких сплавов алюминия и магния (табл. 25). Борную кислоту вводят в состав красок при получении отливок из алюминиевомагниевых и магниевых сплавов.
Во время заливки форм борная кислота превращается в борный ангидрид, который вступает во взаимодействие с окислами металла и образует на поверхности расплава защитный слой, предохраняющий отливку от соприкосновения с влагой формы. Сравнительно невысокая температура заливки легких сплавов позволяет применить в качестве связующего водный раствор поливинилового спирта.
Хромит (хромистый железняк) при контакте с жидким металлом спекается в газонеппонипаемую копку, плптнп ппилегяюптую
к поверхности отливки. Такая корка затрудняет доступ кислорода к раскаленной поверхности отливки и тем самым сдерживает образование окислов железа и фаялита, а также предотвращает просачивание окислов в поры формовочной смеси. После охлаждения отливки образовавшаяся корка сравнительно легко удаляется при очистке.
Покрытия, защитные свойства которых проявляются в результате их спекания, можно успешно применять только в известном интервале температур, обычно ниже температуры заливаемой стали на 100—150 °С. По этой причине положительные противопригарные свойства огнеупорных хромито-вых облицовочных смесей, красок и паст могут быть использованы в полной мере лишь при получении крупных стальных отливок с толщиной стенок более 40 мм, обеспечивающих спекание хромита.
Противопригарные краски, содержащие корунд, применяют при изготовлении крупных стальных отливок наравне с цирконовыми.
В связи со сравнительно высокой стоимостью корунда для противопригарных красок используют отходы белого корунда, образующиеся в абразивной промышленности. “Краски, приготовленные из отходов белого корунда, применяют для изготовления отливок из углеродистых и низколегированных сталей массой до 30 т с толщиной стенок до 400 мм. Использование корундовых красок для производства тонкостенных стальных отливок, где с лучшими результатами можно применить более дешевые краски из пылевидного кварца, нецелесообразно.
Основные водные краски и пасты. Наполнителями в основных покрытиях служат хромомагнезит, магнезит, форстерит, оливин, тальк и некоторые шлаки. Благодаря высокой огнеупорности и малой химической активности материалы с сильно выраженной основной реакцией применяют при производстве крупных отливок из легированных сталей. Тальк и основные шлаки используют в покрытиях для получения отливок из чугуна и цветных сплавов.
Для получения красок пасты разбавляют водой до требуемой вязкости. Хромомагнезитовые краски и пасты применяют для приготовления отливок из хромо-никелевых и высокомарганцовистых сталей. Магнезит обладает большой химической устойчивостью к железу и марганцу и их окислам.
Не подвержен полиморфным превращениям при нагреве. В результате взаимодействия между окислами железа и окисью магния образуется магнезиоферрит(MgO- Fe203), обладающий высокой температурой плавления (1750 °С), что обусловливает отсутствие жидкой фазы на поверхности раздела металл—форма. Магнезитовые краски хорошо зарекомендовали себя при производстве отливок из высокомарганцовистой стали.
Недопустимо при окраске форм смешивать сильные основные краски (хромомагнезитовые, магнезитовые, форстеритовые) с кварцевым песком, так как при этом значительно снижается огнеупорность покрытия и возникает пригар. По этой причине необходимо наносить основные краски на песчаные формы пульверизатором, а не кистью.
Форстеритовую краску для стальных отливок выпускают по ГОСТ 10772—64. Оливиновые порошки и краски для литейного производства в настоящее время отечественной промышленностью не выпускаются. Опыты показали, что оливиновые краски не совместимы со смесями из кварцевого песка.
В силу различной величины коэффициентов термического расширения оливиновые краски, нанесенные на образцы из кварцевого песка, растрескиваются.
Тальковые краски приготовляют в основном из пасты ТБ (ГОСТ 10772—64), применяют их для чугунных отливок массой не более 1 т, а в некоторых случаях, в сочетании с углеродистыми материалами, и для более крупных отливок (табл. 28). На Ярославском моторном заводе для окраски сырых форм автомобильных блок-цилиндров применяют краску, в состав которой входят (% по массе): 44,4 талька; 3,4 ПВАЭ; 52,2 воды.
Плотность краски 1,36—1,42 г/см3. Краску наносят на формы пульверизатором и просушивают на конвейере газовыми горелками. На сумском заводе «Центролит» разработано покрытие, включающее тальк и молотый асбест (% по объему): 40 талька; 48 молотого асбеста; 4 бентонита; сверх 100% — 10 связующего СБ (ГОСТ 8830—58).
Пасту приготовляют в бегунах. Сначала загружают и перемешивают в течение 15 мин сухие компоненты, затем вводят связующее СБ и продолжают перемешивание еще 20—25 мин, после чего добавляют воду до 40%-ной концентрации сухих веществ в красочной суспензии. Полученную пасту доводят до плотности 1,35—1,34 г/см3 в лопастной краскомешалке, разбавляя водой. Приведенный состав краски отработан в производственных условиях на сложных чугунных отливках цилиндровой группы массой до 5 т.
Равноценным заменителем талька (а в некоторых случаях графита и циркона) может быть пирофиллит. Краски и припылы из феррохромового шлака впервые в Советском Союзе начали применять на заводах Урала. Шлак был опробован в качестве противопригарного материала на бронзовых, чугунных и стальных отливках.
Предлагается в качестве огнеупорного наполнителя противопригарных красок использовать также хромитовый шлак — отход при производстве металлического хрома. Огнеупорность шлака, как правило, выше 1850 °С.
Углеродистые водные краски. Анализируя составы этих красок, можно заметить, что в большинстве красок наряду со скрытокристаллическим графитом введен кристаллический графит, тальк или кокс. Особенно ощутимо повышенное содержание кокса в красках для литья изложниц и прочих тяжелых отливок (краски № 7—11), где необходимый сравнительно толстый слой покрытия должен быть газопроницаемым.
Добавки таких материалов, как кокс, шамот, тальк одновременно понижают и склонность графитовых красок к образованию трещин.
Покрытия на металлофосфатных связующих. Эти покрытия обладают повышенными свойствами по сравнению с известными, содержащими неорганические и органические связующие. Они практически негазотворны, отличаются хорошей седиментационной устойчивостью и кроющей способностью, длительное время сохраняют живучесть.
Металлофосфатные связующие хорошо сочетаются с высокоогнеупорными наполнителями: цирконом, электрокорундом и дистен-силлиманитом. Краски, приготовленные на металлофосфатных связующих, не отслаиваются и не растрескиваются при высоких температурах и поэтому хорошо противостоят образованию окислов металла на отливках и их проникновению сквозь покрытия в поры формовочной смеси.
Испытания красок на крупных отливках из высоколегированных сталей массой до 15 т показали, что металлофосфатные (в частности алюмохромо-фосфатные) связующие придают им более высокие противопригарные свойства по сравнению с пастой ЦБ. Доступная стоимость и недефицитность связующих обеспечат покрытиям на металлофосфатной связке широкое распространение. Составы некоторых покрытий на металлофосфатных связующих приведены в табл.
30.
Выводы.
1. Получение мелких и средних чугунных и стальных отливок с чистой поверхностью при соблюдении технологии формовки обеспечивают противопригарные пасты, выпускаемые серийно по ГОСТ 10772—64; необходимую термическую стойкость и достаточно прочное сцепление с поверхностью уплотненной смеси при температурах заливки этим краскам придает сочетание органических и неорганических связующих в виде ССБ, патоки и бентонита.
2. Получение крупных и толстостенных чугунных отливок без пригара обеспечивают краски, содержащие графит и кокс. Наличие в краске молотого кокса придает достаточную газопроницаемость и прочность красочному слою повышенной толщины, полученному при двух- и трехразовой окраске.
3. Высокие противопригарные свойства обеспечивают краскам для высоколегированных стальных отливок магнезит, циркон, дистен-силлиманит и форстерит.
4. Для особо ответственных стальных отливок с толщиной стенок порядка 200—400 мм следует применять высокоогнеупорные нейтральные наполнители (электрокорунд, циркон и др.) в сочетании с алюмохромофосфатным связующим или этилсили-катом. Не имея в своем составе плавней, эти связующие придают краскам особо высокие противопригарные свойства.
5. Применять в водных красках только одни органические связующие I класса без сочетания с глиной или бентонитом допустимо только для тонкостенных чугунных отливок и отливок из цветных сплавов.
6. Выбор состава покрытия во многом зависит от конфигурации отливки. При наличии преимущественно горизонтально расположенных плоскостей большой протяженности, сильно размываемых и облучаемых расплавом, следует подбирать более термостойкие краски, включающие в основном неорганические связующие.