Фосфатирование поверхности
Фосфатная пленка усиливает защитные особенности и удлиняет срок работы лакокрасочных покрытий. Она образуется при обработке железных поверхностей особыми фосфатирующими растворами и воображает солевой слой нерастворимых в воде фосфатов.
Фосфаты владеют низкой способностью и электропроводностью увеличивать адгезию лакокрасочного покрытия.
Они мешают распространению подпленочной коррозии.
Процессы фосфатирования активно используются в индустрии. Первые патенты по получению фосфатных покрытий относятся к 1906—1909 гг.
Фосфатная пленка образуется при окунании изделия в ванну с фосфатирующим раствором либо при нанесении раствора распылением в струйных камерах. Длительность обработки в ванне образовывает 10— 15 мин, в струйных камерах—1,5—3 мин. В зависимости от состава фосфатирующего раствора на железной поверхности образуются фосфаты с четко выраженной кристаллической решеткой или аморфные фосфаты.
Кристаллические фосфатные пленки осаждаются из растворов, содержащих катионы тяжелых металлов, аморфные фосфатные пленки —из растворов кислых фосфатов щелочных металлов либо кислых фосфатов аммония.
Любой вид фосфатных покрытий имеет собственную прея имущественную область применения.
Кристаллическое фосфатирование. Для фосфатирования самый активно применяются растворы па базе; солей цинка.
В следствии понижается концентрация ионов водорода, т. е. увеличивается рН раствора в приэлектродном слое.; Третичный фосфат цинка Zn3(P04)2, владеющий весьма ограниченной растворимостью, выпадает на поверхности металла при достижении в приэлектродном слое рН, соответствующего началу осаждения. В один момент третичный фосфат цинка осаждается и в толще раствора (шламообразование).
Концентрация водородных ионов приэлектродного слоя понижается за счет катодного процесса. При, в то время, когда им есть выделение водорода, которое протея чает медлительно, формирование фосфатного слоя длится 30—40 мин.
Фосфатирование ускоряется методом повышения скорость катодного процесса. Это достигается введением вюсфатирующие растворы ускорителей, которыми являЯ ются, к примеру, такие окислители, как ионы NOj и NOo. Ускорение фосфатирования в присутствии нона NO3 разъясняется тем, что ион NO3 восстанавливается на железной поверхности до аммиака, поглощая ионы водорода132.
Введение ускорителей в фосфатирующий раствор существенно снижает длительность формирования покрытия, изменяет плотность и кристалличность осадка.
Кинетика роста фосфатной пленки в растворах с ускорителями и без них схематично представлена на рис. 1. Кривая зависимости роста массы фосфатного слоя от длительности фосфатирования в растворах с ускорителями имеет трц характерных участка: I—участок стремительного роста слоя, на котором формируется 60— 70% всей массы фосфатов; II— участок начала торможения; III — участок завершения формирования слоя. В растворах без ускорителей образуются более большие и менее плотные кристаллы.
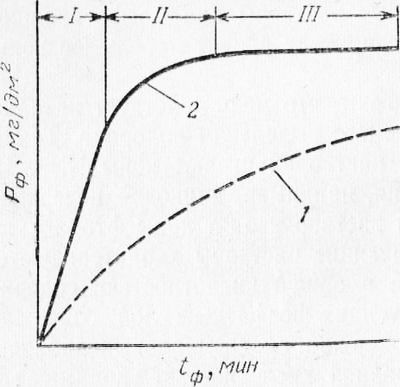
Рис. 1. Зависимость повышения массы фосфатного слоя рф от длительности фосфатирования (tф): 1 — в растворе без ускорителей; 2 — в растворе с ускорителем; I, II, III — участки кривой, характеризующие рост фосфатного слоя
В фосфатирующие растворы нитрат-ион вводится конкретно при составлении раствора и после этого иногда добавляется при корректировке совместно с другими входящими в раствор ионами.
Роль нитрит-иона особенно серьёзна при получении фосфатных покрытий в струйных камерах. В его отсутствии во многих фосфатирующих растворах не образуется фосфатных пленок. Ион нитрита вводится в основном в виде нитрита натрия числом, не превышающем 0,5 г/л; наряду с этим существенно значительно уменьшается кристалличность и масса фосфатной пленки.
В кое-какие растворы для фосфатирования в струе в качестве ускорителя вводят маленькое количество ионов Cu.
Предполагают, что медь действует каталитически на катодный процесс выделения водорода. Такую же роль в некоторых растворах играются ионы №++. Время от времени для активирования, к примеру, цинковой поверхности в фос-фатирующий раствор вводят ионы фтора.
Фосфатирующие растворы характеризуются:
— свободной и неспециализированной кислотностью; содержанием ионов, формирующих фосфатный слой;
— содержанием и содержанием окислителей особых добавок.
Под свободной кислотностью знают концентрацию ионов водорода, образующихся при диссоциации свободной фосфорной кислоты; ее высказывают в условных единицах — точках.
Свободная кислотность раствора характеризует скорость начального растворения в нем фосфатируемого металла.
Неспециализированная кислотность определяется суммарным содержанием фосфатов тяжелых металлов и свободной фосфорной кислоты и выражается кроме этого в точках, но титрование ведется в присутствии фенолфталеина.
Нарушение равновесных значений неспециализированной и свободной кислотностей ведет к дефектам и процесса различным осложнениям фосфатирования фосфатного слоя. Кое-какие из вероятных недостатков приведены ниже.
Содержание нитрата натрия в разных фосфати-рующих растворах колеблется от 2—3 до 30 г/л и более, причем в литературе отсутствуют обоснования выбранных значений. Нитрит натрия вводится в исходный раствор числом до 1 г/л при фосфатировании окунанием и числом 0,2—0,3 г/л при фосфатировании в струйных камерах.
Плотная мелкокристаллическая фосфатная пленка (массой до 30 мг на 1 дм2) формируется при фосфатировании распылением в растворе № 7. Для фосфатирова-ния окунанием рекомендуются растворы № 8 либо № 9, на некоторых фирмах до сих пор употребляются фосфатирующие растворы из препарата «Мажеф». Использование этих растворов перед последующей окраской не рекомендуется из-за большой массы фосфатного слоя и его крупнокристаллической структуры.
В отсутствие в растворе окислителей процесс именуется простым и при их наличии — ускоренным.
В Советском Альянсе фосфатирующие растворы готовят из солей конкретно на фабриках-потребителях.
Нужные количества солей смешивают с водой в особых емкостях, где они нагреваются до рабочей температуры, отстаиваются и перекачиваются в рабочую ванну. На некоторых фабриках практикуется так называемая «варка» растворов — выдержка при большой температуре в течение нескольких часов. Это недопустимо, поскольку содействует усиленному гидролизу, выпадению больших количеств фосфата цинка в виде нерастворимого шлама, непроизводительному кислотности расходу и повышению раствора реактивов.
Недочётами изготовление фосфатирующих растворов из готовых солей являются следующие: необходимость особых отделений изготовление растворов; повышенный расход реактивов; сложность корректировки ванн в ходе эксплуатации; необходимость нередкой очистки оборудования от шлама.
За границей используют фосфатирующие концентраты, каковые представляют собой жидкости плотностью 1,5—1,7 г/см3, транспортируемые в особой кислотоупорной таре. Фосфатирующие растворы готовят в этом случае конкретно в рабочих ваннах введением 2— 3 л концентрата на 100 л воды. Ускорители процесса типа нитрита натрия поставляются раздельно в виде солей либо растворов.
Корректировка фосфатирующих растворов производится добавлением в них маленьких количеств концентрата, что разрешает поддерживать параметры в требуемых пределах. Приготовление фосфатирующих растворов из концентратов экономично и комфортно. Данный метод внедряется в отечественной индустрии.
К кристалличности и толщине фосфатных пленок, являющихся подслоем для лакокрасочных покрытий, предъявляются кое-какие особые требования.
При нанесении лакокрасочных материалов на крупнокристаллические толстые фосфатные пленки увеличивается расход материалов, ухудшается блеск покрытия, понижается его свойство противостоять изгибу и ударным воздействиям. Такое нанесение возможно рекомендовано только в особых случаях, при повышенных требованиях к защитным особенностям покрытия, не испытывающего существенных деформаций и ударных нагрузок.
Максимально допустимая толщина фосфатного слоя, предназначенного под окраску, образовывает 5 мкм.
В которых рекомендуют рецептурах фосфатирующих растворов получаются фосфатные слои толщиной 2,5—3 мкм с хорошими защитными особенностями.
Необходимость пассивирования фосфатированной поверхности связана с пористостью пленки. Пассивирование снижает скорость растворения стали в порах и существенно увеличивает защитные особенности лакокрасочного покрытия.
Лучшим пассивирующим раствором есть раствор хромовой кислоты, концентрация которого зависит от вида фосфатного покрытия. Согласно данным Маху, для пассивации цинкфосфатных покрытий требуется 0,04%-ный раствор хромовой кислоты, для пассивации железофосфатных покрытий — 0,1%-ный.
В некоторых случаях рекомендуется добавление в пассивирующий раствор маленьких количеств фосфорной кислоты с таким расчетом, дабы суммарная концентрация хромовой и фосфорной кислот составляла не более 0,08% (к примеру, 0,25 г/л Сг03 и 0,25 г/лН3Р04). Величина рН пассивирующего раствора находится в пределах 4—5, исходя из этого операцию пассивирования именуют время от времени кислотной промывкой. Окончательной промывки по окончании для того чтобы пассивирования не нужно.
В некоторых случаях производится промывка деминерализованной водой в течение 2—5 сек.
Процесс кристаллизации фосфатных слоев сложен и зависит от многих факторов, таких, как обработка поверхности перед фосфатированием, состав исходного металла, температура и состав фосфатирую-щего раствора, условия проведения процесса фосфатирования (в ваннах либо в струе), длительность фосфатирования, плотность орошения при обработке в струйных камерах и др.
Установлено, что в состав цинкфосфатных слоев, образующихся на металлической поверхности, входят в основном два соединения: Zn3(P04)2-4H20 (гопеит) и Zn2Fe(P04)2-4H20 (фосфофиллит). Оба соединения находятся в слое в виде кристаллогидратов, устойчивых в воздухе воздуха и чувствительных к нагреву.
При повышении содержания железа в ванне понижаются защитные особенности слоя и кристаллы становятся больше.
Образованию крупнокристаллических фосфатных пленок содействует кроме этого использование травильных и сильнощелочных обезжиривающих растворов. Активация поверхности перед фосфатированием и формирование мелкокристаллической фосфатной пленки достигают-, ся предварительной протиркой изделий, применением слабощелочных обезжиривающих растворов и введением в их состав особых активаторов, к примеру солей титана138’ 139.
Значительно чаще фосфатируют металлические поверхности, но время от времени нужно нанести фосфатный слой на другие металлы для улучшения адгезии лакокрасочного покрытия. Фосфатирование высоколегированной стали простым способом нереально, поскольку в фосфатирующих растворах не происходит растворение стали. В этом случае используется или электрохимическое фосфатирование, при котором фосфатируемое изделие есть катодом, или изделие из нержавеющей стали фосфатируют в растворе того же состава, что и для стали, в контакте с изделием из углеродистой стали.
Известны составы для одновременного фосфатиро-вания металлических, оцинкованных и кадмированных поверхностей.
Фосфатирование его сплавов и алюминия вероятно в тех же цинкфосфатных растворах, что и фосфатирование стали, с добавкой в них иона фтора. Фосфатирование алюминия затрудняется тем, что ионы А1+++ являются ядом для цинкфосфатных ванн, исходя из этого при содержании в них 0,3 г/л этих ионов процесс фосфатиро-вания заканчивается.
Добавкой комплексообразующих ионов фтора к цинкфосфатным ваннам удается осадить переходящие с поверхности в раствор ионы алюминия и поддерживать их концентрацию в растворе в- допустимых пределах. Помимо этого, фтор-ионы активируют пассивную поверхность его сплавов и алюминия.
При оценке качества фосфатной пленки одной из главных ее черт есть масса, которую нельзя определить конкретно на изделии. Для контроля массы фосфатов, образующихся в промышленных условиях, в один момент с подробностями обрабатывают пластины, так именуемые свидетели, на которых и определяют массу фосфатов.
Масса фосфатного покрытия на единицу поверхности определяется по разности весов примера до и по окончании фосфатирования. Удаление фосфатов производится в течение 10—15 мин в 5%-ном растворе хромовой (либо ин-гибпрованноп соляной) кислоты при температуре 70— 75 °С.
Время от времени количество осажденного фосфатного покрытия определяют по толщине слоя (в мкм). Согласно данным Маху141, эта черта фосфатного слоя есть менее правильной, чем масса. Толщине фосфатного слоя J мкм -соответствует масса ~ 10—15 мг на поверхности 1 дм2.
Масса металла, стравленная с единицы поверхности металла при образовании фосфатного слоя, кроме этого есть чёртом покрытия. Она определяется по разности весов примера до фосфатирования и по окончании удаления фосфатной пленки.
Защитные особенности фосфатной пленки определяются ее пористостью, характеризуемой в несложном случае числом железа, переходящего в нейтральный раствор при погружении в него фосфатированной пластины.
Окрашенные фосфатированные образцы помещают в камеру солевого тумана, образуемого распылением 3 % -пого раствора NaCl при температуре 35 °С. На фосфа-тированных примерах, не защищенных лакокрасочным покрытием, точки ржавчины появляются через пара часов (а время от времени и мин.); образцы с лакокрасочным покрытием выдерживают опробование в течение от 250 до нескольких тысяч часов.
Адгезия лакокрасочного покрытия в ходе эксплуатации понижается. На фосфатированной поверхности отмечается меньшее понижение адгезии лакокрасочного покрытия, чем на обезжиренной поверхности без фосфатной пленки.
Для наблюдения за трансформацией адгезии лакокрасочного покрытия в ходе ускоренных либо натурных опробований производится надрез покрытия в виде креста, на котором по окончании окончания экспозиции наклеивается липкая лента. Ширина разрушения лакокрасочного покрытия по окончании отрыва ленты характеризует защитные свойства и адгезию покрытий. При хорошем сочетании лакокрасочного покрытия с фосфатным слоем и хорошем качестве последнего ширина поражения не превышает 2 мм.
Рис. 2. Влияние фосфатного слоя на защитные особенности лакокрасочных покрытий: а — образцы по окончании опробования во мокрой камере; б —образцы по окончании опробования в солевой камере; 1 — образцы, окрашенные по окончании протирки поверхности растворителем; 2 — образцы, окрашенные по окончании нанесения фосфатного слоя.
Склонность лакокрасочного слоя к пузыреобразова-нию характеризуется числом пузырей, показавшихся на поверхности при погружении ее в воду либо при опробовании в камере влажности (гидростате). Наличие фосфатной пленки снижает склонность к пузыреобразова-нию, что четко видно на рис. 14.
Присутствие кристаллизационной воды в гопеите Zn3(P04)2.4H20 и фосфофиллите Zn2Fe(P04)2.4H20 делает фосфатное покрытие чувствительным к нагреву благодаря утраты части кристаллизационной воды. Дегидратация особенно страшна при нанесении на фосфатные слои эмалей с большой температурой сушки. Исходя из этого при разработке разработки подготовки поверхности перед окраской такими эмалями необходимо определять теплоустойчивость фосфатных покрытий.
Обычный способ определения теплоустойчивости отсутствует. Маху предлагает следующую последовательность операций при определении теплоустойчивости:
1) обдувка образцов по окончании фосфатирования сжатым воздухом, после этого выдержка в сушильном шкафу при 50 °С в течение 1 ч и взвешивание;
2) выдержка в сушильном шкафу при 100 °С в течение 10 мин\
3) подъем температуры до 180 °С в течение 35 мин и выдержка при данной температуре в течение 45 мин, выдержка в эксикаторе и взвешивание.
Теплоустойчивость определяется по утрата массы и выражается в %.
Фосфатное покрытие считается теплостойким, в случае если при этих опробованиях оно теряет около 10% начальной массы, что для цинкфосфатных покрытий соответствует утрата 1 моль кристаллизационной воды на 1 моль фосфата цинка и заметно не воздействует на защитные особенности фосфатных покрытий.
Кристалличность фосфатного слоя определяют визуально либо посредством микроскопа при повышении от 100 до 250. В некоторых случаях для изучений используют электронный микроскоп.
Однородность фосфатного покрытия определяется, как и шероховатость поверхности, высотой выступов и измеряется посредством профилографа. Ровные и мелкокристаллические фосфатные покрытия имеют шероховатость 1 мкм, негладкие и крупнокристаллические — 10 мкм.
В некоторых случаях к фосфатной пленке предъявляются особые требования. Так, при окраске способом электроосаждения фосфатная пленка обязана прекрасно противостоять анодной поляризации и владеть минимальной растворимостью при напряжении на протяжении осаждения 150—200 в. Растворение фосфатной пленки ведет к загрязнению окрасочной ванны посторонними ионами, к примеру ионами цинка, каковые увеличивают электропроводность лакокрасочного материала и нарушают режим электроосаждения.
Растворимость фосфатной пленки в условиях окраски электроосаждением определяется по особой’ аналитической методике.
В следствии совершённых работ в области фосфа-тирования, направленных на получение плотных, равномерных мелкокристаллических покрытий с маленьким временем формирования, имеются определенные успехи. Температура фосфатирования снизилась с 85 до 45 °С, масса слоя на 1 дм2 поверхности уменьшилась с 50 до 15 мг, расход реактивов вследствие этого снизился с 60 до 20 г/м2, соответственно приблизительно в три раза уменьшилась цена покрытия142.
Понижение кристалличности и. массы фосфатного слоя снабжает лучшее сопротивление лакокрасочного покрытия изгибу и удару, что особенно принципиально важно для современных процессов окраски металла в ленте и листах.
Начинают использовать растворы, в которых в качестве ускорителя применяют хлораты.
Сейчас в фосфатирующие растворы вводят полифосфаты, добавка которых в количествах 200—300 мг/л снижает шламообразование, толщину фосфатной пленки и. расход реактивов145-143 за счет свойства полифосфатов прочно связывать ионы двухвалентных металлов в растворимые комплексы. В следствии гидролиза полифосфаты переходят.в ор-тофосфаты, исходя из этого их нужно непрерывно додавать в раствор равно как и нитрит натрия.
При частичной замене ионов цинка в фосфатирующем растворе иономами Ca, предлагаемой в некоторых патентах, фосфатная пленка уплотняется.
Мелкокристаллические, узкие фосфатные пленки все больше используются в качестве подслоя перед нанесением покрытий из пластмасс, пенопласта и т. п.150-151.
Кристаллические фосфатные слои и процесс их получения имеют кое-какие недочёты:
чувствительность процесса к колебанию температуры ванны; шламообразование; необходимость содержания и кислотности частого контроля ванны некоторых ускорителей, к примеру нитрита натрия.
Аморфное фосфатирование. Вышеперечисленные недочёты процесса кристаллического фосфатирования устраняются при применении щелочного либо аморфного фосфатирования, именуемого в некоторых случаях фосфатным пассивированием.
На железной поверхности осаждается нерастворимый третичный фосфат железа Fe3(P04)2-8H20, что, согласно данным, владеет высокой чувствительностью и дисперсностью к кислороду воздуха. Уже по окончании сушки покрытия происходит окисление, и в слое образуется магнетит Fe304.
Так как образование слоя аморфных фосфатов не связано с реакцией гидролиза, в этом случае допустимы температуры растворов и’ большие изменения кислотности, чем при кристаллическом фосфатировании.
Величина рН при аморфном фосфатировании находится в пределах 5—6, масса образующегося слоя образовывает 2—5 мг на 1 дм2. Уменьшение слоя если сравнивать с кристаллическими фосфатными слоями в 10 и более раз приводит к существенному снижению защитных особенностей. Исходя из этого использование аморфных фосфатных слоев рекомендуется в сочетании с лакокрасочными материалами типа эпоксидных, каковые снабжают хорошую защиту.
Покрытия, полученные при нанесении лакокрасочных материалов на слой аморфных фосфатов, способны выдерживать большие деформации благодаря хорошей адгезии их к железной поверхности и маленькой толщины фосфатной пленки.
Аморфные фосфатные пленки, не обращая внимания на маленькую толщину, улучшают защитные особенности лакокрасочных покрытий, в особенности при применении растворов, содержащих шестивалентный хром, вызывающий пассивацию аморфных слоев перед окраской.
Сначала ванны аморфного фосфатирования содержали лишь кислые фосфаты натрия либо аммония152. Для ускорения образования слоя улучшения и фосфатов их защитных особенностей в раствор вводят ускорители процесса, в качестве которых используют нитраты, хлораты, нитрогуанидин и др.
Но при применении громадных количеств ускорителя вероятно образование стирающегося слоя с нехорошей адгезией. По литературным данным, введение в раствор солей молибденовой либо вольфрамовой кислот мешает образованию стирающихся покрытий. Для получения покрытий удовлетворительного качества в раствор вводят вторичный ускоритель, которым возможно таннин либо какой-либо из дубильных экстрактов.
В таких растворах обрабатываются малозажиренные изделия.
Область применения растворов аморфного фосфатирования расширяется с повышением выпуска окрашенных ленты и листов.
Проведение процесса фосфатирования и используемое оборудование
В зависимости от принятого технологического процесса подготовки поверхности перед окраской операция фосфатирования проводится в ваннах (окунанием) либо в проходных струйных камерах (распылением).
Перед фосфатированием изделия должны быть обезжирены и очищены от ржавчины и окалины. По окончании фосфатирования проводятся операции промывки, пассивирования (кислотной промывки) и сушки.
При проведении процесса в струйных камерах значительно уменьшается продолжительность процесса, понижается энергии и расход реактивов, образуются более узкие, равномерные фосфатные пленки, чем при окунании; помимо этого, вероятно применение конвейера.
Ванна для фосфатирования представляет собой сварную емкость, которая легко возможно очищена от шлама. Для этого дно ванны делают наклонным и снабжают люком. люк и Погружной нагреватель располагают в различных углах ванны.
Ванна может обслуживаться вручную или автоматическими транспортными средствами.
Между ваннами предусмотрена достаточная территория для стекания растворов. Длительность нахождения изделий в данной территории должна быть вычислена так, дабы главная часть раствора успевала стекать и не переносилась в следующую ванну, но дабы наряду с этим изделие не высыхало.
При фосфатироваиии в ваннах требуются меньшие капитальные затраты, чем при применения струйных установок.
Автоматические струйные установки, включающие операцию фосфатирования, выгодно использовать при обработке не меньше 50 штук изделий в смену с неспециализированной поверхностью около 300 м2.
Главными узлами установки струйного фосфатирования являются: корпус, нагреватель раствора, распылительные устройства, и устройства для подачи раствора. Корпус представляет собой сварной кожух, размеры которого определяются большими габаритами обрабатываемого изделия. Потому, что фосфати-рующий раствор имеет кислую реакцию (рН 2—3), чтобы не было разрушения загрязнения и стального корпуса фосфатирующего раствора ионами железа рекомендуется все оборудование, контактирующее с фосфати-рующим раствором, изготовлять из кислотостойкой стали.
Нагреватели фосфатирующего раствора в виде выносных теплообменников нужно делать из латунных труб, каковые обрастают шламом в намного меньшей степени, чем металлические.
Степень обрастания шламом зависит от поверхности температур нагрева и разности теплоносителя. При применении перегретого пара в качестве теплоносителя происходит более интенсивное обрастание греющих поверхностей, чем при применении насыщенного пара. Исходя из этого фосфатирующий раствор нужно обогревать насыщенным паром либо тёплой водой.
Выносные трубчатые теплообменники рекомендуется применять не только в секциях фосфатирования, по п во всех других, поскольку они меньше засоряются и об-• растают грязыо и шламом, чем греющие элементы, загружённые конкретно в ванны. Помимо этого, коэффициент теплоотдачи от движущегося теплоносителя к движущемуся раствору больше, чем при погружных элементов, что разрешает уменьшить греющие поверхности.
Шлам, образующийся в ходе фосфатирования, частично осаждается на обрабатываемой поверхности и при неполной его отмывке может вызывать подпленоч-ную коррозию благодаря осмоса жидкости через лакокрасочное покрытие.
В современных агрегатах шлам из раствора удаляется на непрерывно действующих фильтровальных установках, в которых фильтрация осуществляется на движущейся ленте.
При струйном фосфатнровашш уровень качества фосфатного слоя зависит от количества раствора, подаваемого на единицу фосфатируемой поверхности, и типа струи. По литературным данным76 расход фосфатирующего раствора обязан составлять 100—200 л/м2. Согласно данным компании MetalIgesellschaft (ФРГ), эта величина должна быть равна 250 л/м2 при шахматном размещении форсунок п расстояниях между ними 250—300 мм.
Для распыления фосфатирующего раствора используются форсунки особых конструкций, формирующие распыленную струю под давлением 0,8—1,0 кгс/см2. Вероятные конструкции форсунок представлены на рис. 3, а и б. Форсунки для фосфатирования направляться изготавливать из нержавеющей стали.
Форсунка, представленная на рис. 3, а, имеет внутренний канал, вольный от каких-либо лопастей и стержней, и относительно громадный диаметр выходного отверстия, снабжающие хорошее распыление жидкости; употребляется при обезжиривании, пассивировании и промывках.
Распылительные контуры с форсунками располагают в струйной камере так, дабы обеспечить однообразную доступность всех установок обрабатываемого изделия. Расстояние от изделия до контура с форсунками образовывает 300—500 мм, а между форсунками —250—300 мм.
Рис. 3. Конструкция распылительных форсунок: а — для обезжиривания, пассивирования и промывок; о — для фосфатирования.
Размеры секции фосфатирования определяются габаритами изделия, производительностью (скоростью конвейера) и длительностью обработки, которая зависит от состава раствора, предварительной подготовки поверхности, материала изделия и др.
По окончании фосфатирования следуют операции пассивирования и промывки, каковые значительно влияют на защитные особенности покрытия.
Уровень качества промывки определяется особенностями промывной воды и интенсивностью облива. Средний расход воды для отмывки поверхности образовывает 17—20 л/м2.
При проектировании новых высокопроизводительных установок подготовки поверхности удельный расход воды в СССР принят равным 25 л/м2, в ЧССР — 50 л/(м2-мин), в Японии —300 л/м2 при замкнутой промывке (циркуляционной) и до 10 л/м2 при окончательной промывке обессоленной водой.
Общее число нужной промывной воды зависит от метода промывки. При проточной промывке расход воды большой, при многоступенчатой промывке экономия воды вероятна за счет циркуляционной промывки с частичным применением воды последующих ступеней для первых промывок.
Неспециализированное содержание солей в промывной воде пе должно быть больше 100 мг/л.
При проектировании новых установок подготовки поверхности под окраску в целях экономии производственных площадей нельзя сокращать продолжительность промывок, поскольку это связано с.ухудшением особенностей покрытия.
Последней операцией технологического процесса подготовки поверхности есть сушка сжатым воздухом, нагретым до 110—115 °С, либо сушка в особых сушильных камерах. Длительность сушки определяется сложностью конфигурации изделий, наличием глубоких карманов и т. п.
Длительность сушки изделий сложной конфигурации уменьшается за счет предварительной обдувки нагретым воздухом. При сушке легких узких подробностей скорость воздуха на выходе из сопла образовывает 2— 6 м/сек. При сушке тяжелых подробностей скорость воздуха может быть около 20—60 м/сек, наряду с этим в один момент с сушкой происходит сдувание с поверхности отдельных капель, уменьшение количества солей, остающихся на поверхности по окончании промывки, и увеличение срока работы лакокрасочного покрытия.