Электроннолучевая технология обработки миниатюрных изделий
Сейчас для целей размерной обработки миниатюрных изделий, получения отверстий малых размеров все большее распространение приобретают электроннолучевые установки. Направленный пучок электронов, попадая на поверхность изделия, разогревает его. Наряду с этим поверхностный слой материала на локальном участке размягчается, плавится и частично испаряется. Благодаря остронаправленности электронного луча в соседних территориях значительного увеличения температуры не происходит.
Так, в зоне обработки температура может быть около 600 °С, а на расстоянии всего 0,001 мм от последней — 280—300 °С. Обработку электронным лучом реализовывают в вакууме. Сфокусировать электронный луч возможно на площадку диаметром 0,005—0,1 мм.
Электронный луч представляет собой направленный поток электронов, переносящий энергию от излучателя электронов к изделию. Электроны излучаются катодом, после этого ускоряются в электрическом поле, получая кинетическую энергию, пропорциональную их скорости, формируются электрическими и магнитными полями в узкий пучок и направляются на обрабатываемое изделие.
Электроны попадают вовнутрь материала изделия, взаимодействуя с атомами, свободными электронами и молекулами материала. При сотрудничестве электроны в один момент с передачей встречной частице собственной кинетической энергии изменяют направление перемещения.
В следствии передачи кинетической энергии электроны атомов вещества покупают энергию, покидают свок орбиту и переходят на более большой энергетический уровень либо по большому счету уходят из сферы действия ядра, что приводит к ионизации-атомов. На пути электронного луча создается плазма, плотность, которой пропорциональна плотности тока в луче, возможности ионизации атомов и обратно пропорциоональна длине свободного’ пробега электронов. Сам пучок кроме этого меняет собственные параметры.
Диаметр пучка быстро возрастает, плотность тока в нем падает, энергия электронов значительно уменьшается. Дабы сохранить параметры электронного луча неизменными на пути электронов, в пространстве рабочей камеры создают глубочайший вакуум, так дабы средняя протяженность свободного пробега электронов между двумя соударениями была больше расстояния от катода до поверхности изделия. Принято вычислять, что диаметр пучка возрастает приблизительно на величину, равную глубине проникновения электронов в вещество.
Различают два режима нагрева вещества электронным лучом.
1. Чисто поверхностный нагрев, при котором размеры пучка-много больше глубины его проникновения вовнутрь материала. Размеры пучка при прохождении в материале значительно не изменяются. Данный вид нагрева используется для плавки, термообработки, нанесении пленок испарением.
2. Глубинный нагрев, при котором диаметр пучка сравним либо большое количество меньше расстояния, на которое пучок попадает в материал. Используют таковой нагрев для удаления и осуществления резания узких слоев материалов, сварки, прошивания отверстий. Глубину проникновения электронов в материал изделия возможно выяснить из соотношения
Размерная обработка. Размерную обработку материалов электронным лучом реализовывают при плотности тепловой энергии 10®—109 Вт/см2, что разрешает разогреть до испарения и кипения самые тугоплавкие металлы, жёсткие сплавы, минералокерамику, технические камни. При действии остронаправленного электронного луча в изделиях образуются отверстия диаметром 0,01 мм и более, а при перемещении луча либо изделия получается узкий рез.
Электронный луч попадает в обрабатываемый материал на глубину, в много раз громадную его диаметра, что разрешает делать отверстия и глубокие полости, получение которых иными способами нереально. Обрабатываемость материалов электронным лучом определяется лишь их теплофизическими особенностями и не зависит от механических особенностей.
Малая инерционность электронного луча разрешает вести размерную обработку либо сварку в импульсном режиме с громадным диапазоном регулирования частоты следования импульсов, их пауз и длительности между ними. При работе в импульсном режиме электронный луч имеет громадную удельную мощность в фокальном пятне, чем в постоянном режиме. Исходя из этого при прошивании отверстий в металлах либо керамики, и при размерной обработке целесообразно использовать импульсный режим.
Продолжительность импульсов образовывает от 2 мкс до 0,01 с при частоте повторения от единиц до 5—10 кГц.
Электроннолучевую обработку тугоплавких металлов (вольфрама, молибдена) и металлов, владеющих хорошей теплопроводностью (медь, серебро), создают при удельной мощности луча 107—108 Вт/см2 и выше, поскольку при меньшей плотности время обработки существенно возрастает.
При прошивании поверхностных отверстий их диаметры приблизительно на 10% больше диаметра электронного луча. При глубинах обработки, достигающих стократной величины диаметров отверстия и более, диаметр луча должен быть в несколько раз меньше отверстия. Прошивание столь глубоких отверстий ведут методом трансформации фокусного расстояния магнитной линзы по мере углубления отверстия.
Обработка диэлектриков. При размерной обработке электронным лучом диэлектриков ввиду их малой теплопроводности появляются высокие температурные перепады, что вызывает большие остаточные термические напряжения, приводящие к растрескиванию. Для их исключения создают предварительный подогрев с последующим отжигом в вакуумной печи для снятия напряжений.
При обработке диэлектриков на их поверхности появляются отрицательные заряды, что ведет к понижению энергии электронов, к повышению диаметра луча и его расфокусировки.
Электроннолучевую обработку используют для чернового прошивания отверстий диаметром 0,04 мм и более в алмазных волоках. Обработку ведут в импульсном режиме с частотой 30—500 Гц при ускоряющем напряжении 70 кВ и токе 3—6 мА. Для получения круглого отверстия алмазной заготовке информируют вращение с маленькой скоростью.
Наряду с этим остро сфокусированный пучок электронов отклоняется от оптической оси, обрабатывая разные территории волочильного канала.
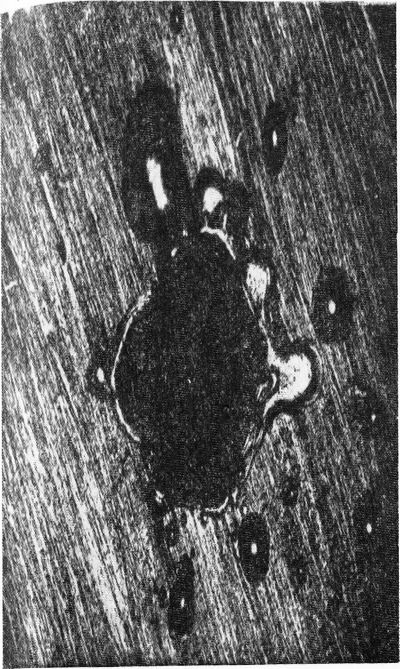
Рис. 1. Форма отверстия, прошитого электронным лучом при 203х повышении
Для прошивани’я выходной распушки волоки ее переворачивают. Так приобретают сквозное отверстие с продольным профилем, родным к профилю готовой волоки, и углом рабочего конуса 14—16°. Время прошивания чернового отверстия диаметром 0,1 мм образовывает 8 мин, диаметром 0,4 и 1 мм соответственно 11 и 21 мин.
Во многих случаях появляется необходимость получения фигурных отверстий в стекле, керамике и других труднообрабатываемых материалах. Для обработки отверстий сложных конфигураций и форм электронный луч перемещают методом отклонения в соответствии с конфигурацией отверстия. Время, нужное для прошивания таких отверстий, зависит от материала изделия, площади обработки, мощности электронного луча и других факторов. К примеру, для прорезания пульсирующим лучом в металлической пластинке толщиной 0,5 мм паза шириной 50 мкм, длиной 3 мм нужно 20-30 с.
Рис. 2. Электроннолучевая установка с программным управлением
Обработка железных изделий. Ввиду того что электронный луч электрически заряжен, при обработке железных изделий имеет место рассеивания и явление отклонения луча, что ухудшает уровень качества обработки. На рис. 1 продемонстрирован при 200х повышении вид входного кратера отверстия, прошитого в странице нержавеющей стали толщиной 1,0 мм. Как нетрудно подметить,, имеет место большой выброс расплавленного металла, застывшего в виде-капель.
очертание и Форма отверстий неправильные. Исходя из этого на электроннолучевых установках самый рационально обрабатывать изделия из керамики, стекла и других труднообрабатываемых неметаллических материалов.
Нужно подчернуть, что firmware отверстий в листовых материалах электронным лучом сопровождается происхождением” больших внутренних напряжений, упругих и остаточных деформаций. Обстоятельством этого происхождения являются высокие температурные градиенты в зоне действия электронного луча на материал. Все это приводит к искривлению прошиваемого изделия.
На уровень качества поверхности изделия, обработанного электронным лучом, влияет диаметр пучка, продолжительность импульсов, теплофизические свойства и мощность пучка материала. Повышение мощности если сравнивать с оптимальной ведет к повышению неровностей, поскольку в ходе обработки выбрасываются большие частицы материала.
Главная масса материала удаляется за первые пара секунд, составляющих 10—20% всего времени обработки. Другое время затрачивается на придание поверхности требуемо» заданных размеров и формы. У многих металлов отмечается, оседание капелек застывшего расплава на стенках отверстия. Прошитые отверстия имеют коническую форму. Величина конуса зависит от размещения фокуса луча относительно поверхности изделия и составляют в большинстве случаев 1—3°.
Для электронно-лучевой размерной обработки используют установки с анодным напряжением! 80—150 кВ при токе в пучке 0,3—20 мА.
Оборудование. На рис. 96 приведена схема универсальной электроннолучевой установки с программным управлением перемещением обрабатываемого изделия, предназначенной для сварки и размерной обработки.
Рабочая вакуумная камера изготовлена из листовой нержавеющей стали. В верхней части камеры установлена сменная электронно-лучевая пушка, питаемая от высококовольтного источника. На лицевой стороне расположено смотровое окно для визуального наблюдения за процессом обработки и два патрубка с окнами для передающей оптического пирометра и телевизионной камеры.
В камеры находится координатный стол для перемещения и закрепления обрабатываемой подробности довольно электронного луча. На столе кроме этого размещают механические при-пособления для фиксирования подробностей. Стол укреплен на тележке, выкатывающейся из вакуумной камеры вместе с боковым фланцем.
Предусмотрены четыре подачи стола (продольная, поперечная, вертикальная и вращательная около оси). Соответственно подачам имеется четыре электропривода, которыми возможно руководить вручную либо с пульта программного управления. Две ступени редукции привода разрешают трудиться по программе с величиной импульса 0,01 либо 0,02 мм. Продольное и поперечное перемещение координатного стола осуществляется посредством роликов и пары винт—шариковая гайка.
редуктор и Электродвигатель размещены на боковом кронштейне. Вращение от приводов передается в камеру промежуточными валиками ввода, каковые установлены в подшипниках качения и уплотнены в крышке камеры фторопластовыми и резиновыми кольцами. Эти валики соединены со звеньями кинематических цепей через упругие муфты, что сокращает люфт привода, повышает точность системы и стабильность работы программного управления.
В вакуумную совокупность откачки входят высоковакуумный агрегат, два насоса предварительного разряжения. Предусмотрена кроме этого особая обособленная вакуумная совокупность откачки электронной пушки. Обработку подробностей на электронно-лучевой установке начинают по достижении определенного вакуума в зоне обработки и в совокупности электронной пушки.
В верхней части электроннолучевой пушки расположен вольфрамовый катод прямого накала и управляющий электрод Питание накала катода осуществляется от высоковольтного источника, высоковольтного выпрямителя и стабилизатора. Питание управляющего электрода производится от импульсного генератора через импульсный трансформатор. Вольфрамовый анод является шайбойс отверстием посредине.
Прямо под анодом расположены обрезающая и подвижная диафрагмы и источник питания. Ниже подвижной Диафрагмы помещена корректирующая электромагнитная линза-стигматор для фокусировки луча и источник питания стигматора. Электромагнитная линза и направляющая заслонка, приобретающие питание от источников, рекомендован для фокусирования электронного луча на подробности до определенного диаметра.
Для контроля за процессом обработки применяют осциллоскоп.
Рис. 3. Электроннолучевая пушка
Совокупность программного управления установки снабжает управление по программе приводами подач, и выключением и включением электронного луча в соответствии с перемещением обрабатываемой подробности.
На данный момент для размерной микрообработки и микросварки применяют электроннолучевые установки как отечественного, так и зарубежного производства.
Для обработки отверстий диаметром 0,005—0,015 мм и выше используют отечественную универсальную электроннолучевую установку ЭЛУРО. На ней возможно осуществлять прошивание отверстий, прорезание пазов и щелей, разметку, локальное легирование, прецизионную пайку, другие операции и испарение металлов. Столь универсальное использование она имеет благодаря возможности регулирования в широких пределах неспециализированной и удельной мощности.
Обрабатываемые изделия помещают на координатном столе, что перемещается в вакуумной камеры на расстоянии 150—200 мм по каждому из двух взаимно перпендикулярных направлений. Приводы к столу выведены из камеры через подвижные вакуумные уплотнения и имеют отсчетные лимбы с ценой деления 0,001 мм для контроля положения стола. Ходовые винты вращаются приводными электродвигателями.
Использование особой камеры разрешает перемещать изделия в горизонтальной плоскости и вращать их. На установке возможно прорезать щели шириной 0,01 мм в кварце, керамике, других материалах и твёрдых сплавах.
В ходе обработки возможно использовано программное устройство для управления перемещениями подробностей и электронного луча. Для контроля обрабатываемых размеров предусмотрен растровый микроскоп, снабжающий 100х повышение.
На базе каскадной электроннолучевой пушки создана установка для сварки и обработки с энергией электронов до 200 кэВ. Она запланирована на обработку разных материалов толщиной от 0,05 мм и более. сварку и Обработку реализовывают в постоянном и импульсном режимах.
Установка создана в двух вариантах: с одной либо двумя магнитными линзами, и с программным управлением от ЭЦВМ либо программным управлением на ограниченное число операций.
Электроннолучевая сварка. Электроннолучевая сварка разрешает соединять разнородные материалы малой толщины. Благодаря высокой локальности нагрева деформация свариваемых подробностей не превышает 10% от деформации при вторых способах сварки.
Хорошая управляемость электронным лучом позволяет распределить энергию луча в фокальном пятне в соответствии с теплофизическими особенностями каждого из пары соединяемых материалов.
Наличие в электронной пушке отклоняющей совокупности разрешает сочетать перемещение свариваемого изделия с перемещением электронного луча, что благоприятно отражается на формировании сварного шва. К примеру, вращение электронного луча по окружности малого диаметра с частотой 10 кГц при наложении прямолинейного шва содействует лучшему перемешиванию сварочной ванны, улучшению структуры и снижению пористости металла шва.
Изюминкой электроннолучевой сварки есть химическая чистота процесса, потому, что она ведется в вакууме. Электроннолучевую сварку удачно используют для соединения элементов микросхем толщиной от нескольких микрон до нескольких десятков микрон.
Возможность трансформации параметров электронного луча в широком диапазоне и громадные удельные мощности в луче разрешают делать фактически все виды швов, используемые при соединении узких и миниатюрных изделий. Своеобразной изюминкой есть правильное дозирование подводимой энергии. Электронный луч владеет данной изюминкой.
Возможность управления перемещением луча посредством электрических и магнитных полей разрешает совмещать пара технологических функций, делаемых лучом в одной камере.
Электронным лучом сваривают тугоплавкие и химически активные металлы, сплавы и высокопрочные стали. Главным показателем сварки есть ее скорость. Электроннолучевая сварка есть одной из самые высокопроизводительных.
Сварка узких листовых заготовок в современных сварочных установках производится со скоростью 10—100 м/ч.
За границей создана специальная малогабаритная электронно-лучевая установка, предназначенная для сварки миниатюрных изделий и изделий, имеющих малую толщину, к примеру датчиков давления, перемещения, ускорения, анероидных коробок, изготовленных из бронзово-нержавеющей стали и бериллиевого сплава толщиной 0,05—0,08 мм. Малые габаритные размеры вакуумной камеры снабжают возможность откачки из нее воздуха за 45 с. В камере предусмотрено многопозиционное приспособление, исходя из этого время откачки в расчете на одно свариваемое изделие образовывает 12 с.
Сварку подробностей толщиной 0,05 мм создают при ускоряющем напряжении 20 кВ, токе луча 2 мА и скорости 45 м/ч, а толщиной 0,38 мм — при ускоряющем напряжении 30 кВ токе луча 8 мА и скорости 45 м/ч. Использование электронного луча в этом случае разрешает приобретать качественный сварной шов, что снабжает стабильную зависимость деформации датчиков при трансформации давления.
Если сравнивать с аргоно-дуговой сваркой, сваркой и пайкой микроплазмой значительным преимуществом электронно-лучевой сварки анероидных коробок есть автоматическое получение вакуума во внутренней полости заваренных коробок. При изготовлении миниатюрных реле электронным лучом приваривают кожух, выполненный из бронзово-никелевого сплава, с основанием реле из нержавеющей стали.
Использование электроннолучевой сварки разрешает избежать перегрева реле и растрескивания их стеклянных выводов. Сварку кожухов реле создают при ускоряющем напряжении 20 кВ, токе луча 4—9 мА и скорости 45—90 м/ч. Сварку миниатюрных реле делают при ускоряющем напряжении 40 кВ, токе 1,5 мА и скорости 180 м/ч.
Небольшой диаметр электронного луча в фокальном пятне, возможность правильного направления его в заданную удобное регулирование и точку детали вводимой мощности разрешают удачно использовать электронно-лучевую установку при изготовлении микрофильтров для фильтрации жидкостей.
При ответе вопроса о применении электроннолучевой размерной сварки и обработки направляться учитывать следующие характеристики: диаметр луча в фокальной точке, нужную точность следования луча по свариваемому стыку и допустимую величину зазора в последнем.
Как мы знаем, что диаметр электронного луча в фокальной точке возрастает с повышением его мощности. При мощности луча в пара ватт его диаметр в фокальной точке возможно доведен до 0,13—0,25 мм. Таковой луч снабжает получение сварного шва глубиной до 2,5 мм и шириной 0,6—1,3 мм. Геометрические размеры сварного шва значительны вследствие того что с повышением ширины шва возрастает нагрев свариваемого изделия и его деформация.
Низкая точность сборки изделий под сварку может привести к непроварам, несплавлению, порам. Довольно часто эти недостатки не видны при визуальном осмотре и требуются особые способы контроля для их обнаружения. В общем случае величина зазора в свариваемом стыке не должна быть больше 0,05 мм.