Оборудование для сверления
На данный момент отечественная индустрия серийно производит универсальные сверлильные станки с электромеханическим и пневматическим приводами главного перемещения.
Станки с электромеханическом приводом. Для сверления отверстий диаметром от 0,2 и более в изделиях из тёмных и сплавов и цветных металлов на фабриках взял распространение настольный сверлильный станок С-ЗМ. Шпиндель станка вращается в закаленных втулках, выполненных из износостойкой высокохромистой стали. Смазка трущихся пар станка централизованная. Направление вращения шпинделя правое. Зажим инструмента в шпинделе— цанговый.
Плоский столик размером 90?90 мм помогает для установки изделий. Подача инструмента ручная посредством лапки. Частота вращения шпинделя — 10 ООО об/мин.
Большой движение инструмента — 18 мм.
Для сверления отверстий диаметром от 0,2 мм помогает такой-сверлильный одношпиндельный станок С-155. Шпиндель станка в значительной мере разгружен от натяжения ремня и вращается в шарикоподшипниках. Смазка подшипников централизованная.
Подача ручная, осуществляется за счет поворота рукоятки. Частота вращения изменяется в пределах от 1900 до 12 000 об/мин.
Изменение частоты вращения достигается сменными шкивами. Число ступеней — 9. Глубину сверления устанавливают микрометрическим винтом. Стол станка прямоугольной формы с поперечным Т-образным пазом.
Для сверления отверстий диаметром от 0,2 мм в разных материалах, среди них и неметаллических помогает настольно-сверлильный станок 2Н103П, станок 2В103-—повышенной точности и др. При сверлении отверстий громадное значение имеет постоянство скорости подачи сверла. Создано особое устройство к сверлильным станкам, которое руководит скоростью подачи шпинделя независимо от скорости его вращения.
Для радиальных влияния биений и уменьшения вибраций сверла, вызываемых ремённой передачей и шкивами, в некоторых конструкциях сверлильных станков исключают шкивы и ремённую передачу. Вращение от электродвигателя конкретно передается шпинделю. На рис. 36 продемонстрирован настольный сверлильный станок для того чтобы выполнения. К плите прикреплена колонка, по которой возможно перемещать кронштейн.
Ротор электродвигателя через фланец соединен со шпинделем, к нижнему финишу которого прикреплен патрон со сверлом. Вертикальное перемещение шпинделя создают посредством реечной рукоятки и передачи. Возврат электродвигателя вверх осуществляется пружиной.
Фиксация кронштейна в требуемом положении на колонке делают зажимом.
Для сверления отверстий, расположенных под разными углами к оси (к примеру, в форсунках двигателей), помогает полу-
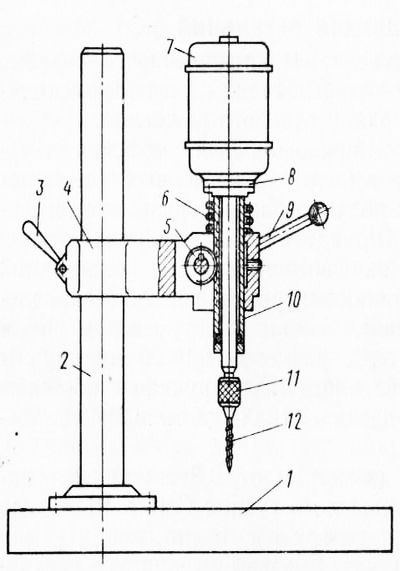
Рис. 1. Сверлильный станок с электромеханическим приводом
непроизвольный сверлильный станок. Станок складывается из трех главных узлов: шпинделя с приводом, поворотного устройства и механизма подачи для крепления обрабатываемой форсунки. На кронштейне смонтирован поворотный диск с цангой для зажима форсунки.
Поворот диска производится электродвигателем через редуктор (на схеме не продемонстрирован). Фиксация диска осуществляется подпружиненным пальцем, входящим в один из радиальных пазов, число которых равно обрабатываемых отверстий в форсунке. Палец перемещается электромагнитом. Привод шпинделя, разгруженного от радиальных упрочнений, производится от отдельного электродвигателя через ременную передачу.
Продольный разрез шпинделя продемонстрирован на рис. 1, б. Сверление отверстий создают через кондукторную втулку.
Регулирующие грузы создают неизменно осевое прижимающее упрочнение. Величина подачи определяется кулачком, влияющим через рычажную совокупность на шпиндель. Кронштейн устанавливают под требуемым углом к оси вращения шпинделя, а форсунку зажимают цангой. При включении станка сверлится первое отверстие.
По окончании отхода шпинделя в исходное положение нажимается конечный выключатель и выдается команда на индексацию поворотного диска. После этого сверлится последующие отверстия и второе. По окончании обработки всех отверстий в форсунке станок машинально выключается.
Оператор снимает обработанную и устанавливает следующую форсунку.
При необходимости сверления и мелкосерийном производстве торцовых и радиальных отверстий разных диаметров от 0,1 мм и более используют универсально-сверлильное приспособление. При его применения отпадает необходимость в изготовлении сверлильных кондукторов. Для сверления торцовых отверстий применяют вертикальный шпиндель приспособления, имеющий личный привод от электродвигателя.
Изменение частоты вращения при сверлении отверстий в разных материалах осуществляется за счет применения легкого многоступенчатого шкива. Для сверления радиальных отверстий помогает горизонтальный шпиндель. Положение его фиксируется рукояткой, которая связана с двумя полумуфтами.
Для сверления бтвёрстий диаметром 6,1 мм и более в подробностях с громадным числом отверстий употребляется станок с цифровым программным управлением. Он оснащен пневмогидравлическим приводом подачи. Величина подачи регулируется посредством лимба, расположенного на пневмоцилиндре.
Для наблюдения за состоянием свёрл и процессом сверления станок снабжен увеличительными устройствами.
Станки с пневматическим приводом. Для уменьшения влияния вибраций, появляющихся при вращении шкивов и электродвигателя при сверлении отверстий, и сокращения поломок сверл используют сверлильные станки с пневматическим приводом главного перемещения.
Станки с пневматическим приводом возможно подразделить на две группы: а) с пневматическими шпинделями — турбинками и б) бесшпиндельные. В станках первой группы вращение сверла, укрепленного в шпинделе, осуществляется посредством пневматической турбинки, ротор которой связан со шпинделем либо выполнен с ней как одно целое.
Примером для того чтобы станка есть станок, предназначенный для сверления отверстий диаметром 0,3 мм и более, продемонстрированный на рис. 2, а. По вертикальной направляющей колонке может перемещаться кронштейн. Перемещение осуществляется при помощи реечной передачи. Вращение инструмента производится от воздушной турбинки.
Сжатый воздушное пространство подается по трубопроводу, проходит через редукционный клапан и поступает в турбинку, приводя в перемещение шпиндель. Отработанный воздушное пространство отводится в воздух. Ротор турбинки связан со шпинделем скользящей шпонкой, через которую передается вращение. Регулированием давления подаваемого сжатого воздуха медлено изменяют частоту вращения шпинделя от 0 до 35 тыс. об/мин.
Для предотвращения проворота шпинделя при креплении в нем инструмента помогает стопорное устройство. Подачу шпинделя на нужную глубину создают посредством реечной передачи. Кроме этого кронштейн, на котором укреплена пневматическая сверлильная головка, возможно закреплен в требуемом по высоте положении зажимными винтами.
Станок возможно прикреплен посредством плиты к верстаку либо столу.
Рис. 2. Полуавтомат для одновременного сверления нескольких отверстий
Рис. 3. Сверлильные станки с пневматическим приводом
Для исполнения сверлильных операций помогает пневматический сверлильный станок, вращение инструмента которого осуществляется от головки пневматической быстроходной шпиндельной машинки. К корпусу станка крепится кронштейн с пневматической головкой. Подача инструмента осуществляется методом поворота рукоятки.
На конец шпинделя станка надевается патрон, что употребляется при сверлении на относительно маленьких оборотах. С целью биений и уменьшения вибраций при сверлении на громадной частоте вращения инструмент крепится в цанге. На рис. 3, в представлен разрез пневматической головки.
Сжатый воздушное пространство из магистрали через штуцер, пробковый кран подается в камеру рассекателя воздуха, проходит через отверстия сопла и вращает турбину, укрепленную в верхней части шпинделя. Отработанный воздушное пространство через просверленные отверстия выходит в воздух. Скорость вращения шпинделя может быть около 30—40 тыс. об/мин.
Для изготовления сверлильного станка в заводских условиях возможно применять серийно производимую сверлильную машинку пневматического действия.
Для сверления отверстий диаметром 0,05—0,25 мм с высокой точностью применяют точный пневматический станок, подшипники для поддержания шпинделя у которого выполнены с воздушной смазкой. Привод шпинделя пневматический. Частоту вращения регулируют трансформацией давления поступающего воздуха посредством игольчатого клапана.
Громаднейшая частота вращения шпинделя — 150 тыс. об/мин. Радиальный и осевой воздушные зазоры в подшипниках порядка 7 мкм.
Бесшпиндельные станки. Новыми являются конструкция привода и принцип действия главного перемещения пневматических бесшпиндельных станков. Установлено, что ровные валики, попав в отверстие, в которое подается сжатый воздушное пространство, начинают вращаться и стремятся занять центральное либо уравновешенное осевое положение довольно впускных отверстий для подачи воздуха.
При определенном зазоре между стенками отверстия и валиком, и определенных углах подвода воздуха вращения происходит со большим крутящим моментом. Направление вращения ровного валика противоположно перемещению воздуха. Это явление использовано для сверления отверстий.
Наряду с этим шпинделем помогает ровный удлиненный хвостовик сверла, которое засунуто в цилиндрическое отверстие гильзы. В случае если в верхней полости Я, цилиндрического отверстия давление воздуха больше, чем в нижней полости, то покажется направленное вниз осевое упрочнение. Наряду с этим ровный хвостовик сверла делает роль поршня. В случае если в полости, понизить давление воздуха, то сверло начнет перемещаться вверх.
Так, за счет разности давлений в полостях П1 и П2 возможно обеспечить подачу сверла вывод и ввод его из отверстия для удаления стружки. Ввиду малости зазоров создаются нужные аэродинамические условия для поддержания сверла в осевом направлении. Наряду с этим стенки и гладкий хвостовик сверла цилиндрического отверстия создают подшипник с воздушной смазкой.
Рис. 4. Схема головки бесшпиндельнОгд сверлильного станка
На обрисованном принципе трудится четырехшпиндельный станок с цифровым программным управлением.
Для исполнения сверлильных операций на этом станке применяют особые спиральные и перовые сверла. Протяженность режущей части образовывает примерно 5% от общей длины сверла; протяженность ровного хвостовика образовывает 85—88% неспециализированной длины. Другая протяженность приходится на переходную часть между хвостовиком и режущей частью. Торец хвостовика сверла должен быть плоским и строго перпендикулярным к оси сверла. На хвостовике не допускаются заусенцы, вмятины и маркировочные символы.
Шероховатость поверхности должна быть Rz sg 0,040 мкм. Для сверления отверстий диаметром от 0,15 мм и более используют спиральные твердосплавные сверла, а для отверстий менее 0,15 мм применяют перовые сверла с твердосплавной режущей частью и металлическим цилиндрическим хвостовиком. Время сверления отверстия диаметром 0,13 мм в изделии толщиной 1,27 мм составило 6 с. Неспециализированным недочётом сверлильных станков с пневматическим приводом есть нестабильность скорости вращения шпинделя и довольно громадный расход сжатого воздуха.
Малогабаритные силовые агрегатные головки. Для сверления; зенкерования, резьбонарезания малых отверстий (диаметром более чем 0,5 мм), фрезерования узких пазов, щелей в изделиях приборостроения взяли распространение малогабаритные агрегатные станки, каковые компонуются из унифицированных агрегатных головок.
Малогабаритные агрегатные станки, предназначаемые для целей обработки миниатюрных изделий, должны владеть универсальностью и снабжать обработку изделий из разных материалов (конструкционных и легированных сталей, цветных их сплавов и металлов, неметаллических материалов). Наряду с этим обработка обязана вестись на оптимальных режимах. При сверлении часто требуется делать глубокие отверстия с отношением глубины сверления к диаметру отверстия равным десяти.
В отличие от особых станков для обработки определенных изделий, переналадка которых на другие изделия не предусматривается, малогабаритные агрегатные станки смогут быть относительно легко переналажены. Главными рабочими элементами агрегатных станков являются малогабаритные силовые агрегатные головки. Громаднейшее распространение взяли силовые головки пинольного типа с электрическим приводом главного перемещения и механическим (кулачковым), пневмогидравлическим и гидравлическим приводами подач.
За границей изготовляют малогабаритные силовые головки с винтовым приводом подачи, что если сравнивать с кулачковым приводом позволяет осуществлять непростые циклы работы инструмента, причем изменение цикла не требует изготовления сменных подробностей.
Для улучшения процессов обработки во многих случаях применяют вибрацию. Сверление, резьбонарезание, точение, фрезерование с вибрациями снабжает надежное и действенное разделение стружки, повышает производительность, качество и стойкость инструмента обработанной поверхности. Широкую номенклатуру малогабаритных силовых головок производят и за границей.
К примеру изготовляются головки с пневмогидравлическим приводом подачи, предназначенные для глубокого сверления с промежуточными выводами инструмента из обрабатываемого отверстия; выпускаются головки с приводом главного перемещения от единого централизованного привода вращения шпинделей, представляющего собой редуктор с нужным числом выходных валов, от которых вращение через эластичные валы передается шпинделем. За счет применения эластичных валов уменьшаются габаритные размеры головок, освобождается рабочая территория и уменьшается число электродвигателей агрегатного станка.
Эластичные валы разрешают приобретать скорости вращения шпинделей до 25 тыс. об/мин. Потом выпускаются агрегатные станки со шпиндельными узлами, выполненными в виду блоков со особыми высокооборотными электродвигателями. Блок мельчайшего типоразмера имеет диаметр 26 мм и длину с электродвигателем 216 мм.
Блок оснащен высокочастотным двигателем мощностью 60 Вт. В зависимости от частоты подводимого тока скорость вращения шпиндёля соответственно равна 24, 18, 12, 7,5 тыс. об/мин.
Измерение отверстий. Для измерения отверстий диаметром от 0,1 мм и более помогают калибры-пробки. Конструктивное исполнение их возможно разным. Калибры-пробки ровные двусторонние с разрезными втулками включают две вставки: проходную и непроходную, каковые вставляют по посадке в латунные втулки.
Крепят вставки и втулки в металлической оксидированной ручке. Аккуратные размеры диаметра назначаются в зависимости от класса точности контролируемого отверстия.
Рис. 5. Калибры-пробки
Для измерения отверстий диаметром от 0,3 мм и более используют кроме этого двусторонние ровные калибры-пробки с вклеенными вставками. Проходную (ПР) и непроходную (НЕ) пробки закрепляют клеем в металлической рукоятке. Клеевой шов обязан снабжать неразъемность и достаточную прочность соединения, и владеть водо-, масло-, бензостойкостью.
Во многих случаях используют ровные двусторонние калибры-рукоятки, каковые выполнены из фенопласта. непроходная пробки и Проходная должны быть надежно и без перекосов закреплены. Измерение отверстий, линейных размеров изделий, и их конструктивных элементов возможно с успехом создавать посредством микроскопа с цифровым отсчётом и проекционным устройством типа БМИ-ЦЭ.
Микроскоп представляет собой измерительный визирный прибор и складывается из следующих главных узлов: основания, продольной и поперечной измерительных кареток с вращающимся круглым столом, колонки, визирной совокупности, реостатных датчиков и осветительного устройства для цифрового перемещений прибора и отсчёта кареток. Измерительные каретки прибора смогут перемещаться в продольном и поперечном направлениях. Отсчет перемещений производится по экрану цифрового прибора.
Измеряемое изделие размещают на столике микроскопа, а его изображение отмечается на экране проектора. Соответствующими перемещениями кареток получают того, дабы штриховые линии сетки визирной совокупности были размещены на измеряемом предмете.
Предельные погрешности измерения в продольном и поперечном направлениях не превышают ±0,003 мм. Микроскоп снабжает 30х и 50х повышение измеряемых объектов.