Основные мероприятия по уменьшению деформаций и напряжений при сварке
При сварке изделий нереально всецело избежать остаточных деформаций. При всестороннем защемлении свариваемого изделия возможно только свести деформации изделия к концу охлаждения к минимальной величине.
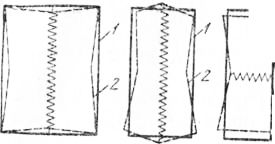
Рис. 1. Деформации в плоскости сварных соединений: 1 — форма соединения до сварки, 2 — по окончании сварки
Всестороннее защемление при сварке изделия фактически осуществить тяжело, исходя из этого таковой метод борьбы со сварочными деформациями практически не используют. Употребляются лишь такие методы, каковые разрешают приобретать сварные изделия с минимальными остаточными деформациями. Кое-какие методы борьбы с деформациями изделия приводят к возрастанию внутренних напряжений, к примеру, закрепление свариваемых подробностей перед сваркой.
Для борьбы со сварочными деформациями используются конструктивные и технологические методы. К конструктивным методам относятся:
1. Уменьшение количества сварных их сечения и швов, что снижает количество вводимого при сварке тепла.
Рис. 2. Деформации вне плоскости сварных!соединений:
Рис. 3. Влияние симметричных швов на деформации: 1, 2, 3, 4 — порядок наложения швов
Исходя из этого минимальная деформация конструкции будет при мельчайших протяженности и сечении швов, к примеру резервуары изготовляют на данный момент нз громадных страниц либо из предварительно собранных в заводских условиях карт и полос.
2. Симметричное размещение швов для уравновешивания деформаций.
3. Симметричное размещение ребер жесткости.
4. Минимальное применение косынок и накладок.
5. Использование стыковых соединений.
К технологическим методам относятся:
1. сварки и Рациональная технология сборки, которая включает верный выбор режима и вида сварки, и верную последовательность наложения швов. К примеру, при ручной сварке деформация в два раза больше, чем при автоматической.
Соединения без скоса кромок дают меньшие деформации, чем соединения с разделкой кромок. Соединения с двусторонним скосом кромок образуют меньшие деформации, чем соединения с односторонним скосом.
Рис. 4. Сборка на прихватках: а — твёрдые прихватки, б, в — эластичные прихватки
Величина деформации зависит от прихватки Детали и способа сборки планируют с твёрдым креплением, не допускающим какого-либо смещения одной подробности довольно второй либо с эластичным, допускающим смещение подробностей. Твёрдое крепление подробностей осуществляется сварочными прихватками в отдельных местах шва (рис. 4, а) либо твёрдыми сборочно-сварочными приспособлениями.
Сборка с эластичным креплением производится особыми пластинами, временно прихватываемыми к подробностям на некоем расстоянии от оси шва (рис. 4, б, в). Твёрдая сборка ведет к меньшей конечной деформации если сравнивать с эластичной.
На величину конечных деформаций воздействует последовательность наложения швов. К примеру, мельчайшая стрела прогиба узла, продемонстрированного на рис. 5, будет при таковой последовательности исполнения швов: сперва — поперечный шов, после этого — продольный и по окончании него — поперечный вертикальный.
2. Твёрдые закрепления подробностей. Собранное изделие всецело сваривается, в случае если закреплено на фундаменте, плите либо приспособлении, каковые имеют жесткость, многократно громадную если сравнивать с сварным изделием. По окончании полного охлаждения и сварки изделия зажимы удаляются. По окончании освобождения изделия деформация будет меньше, чем при сварке в свободном состоянии. Закреплением возможно снизить сварочные деформации на Ю—30% в зависимости от последовательности условий.
Данный метод дает громаднейший эффект при сварке балок малой высоты и мельчайший — при сварке высоких балок (1000 мм и более).
Закрепление рекомендуется при сварке плоских страниц для предотвращения угловых деформаций. Страницы возможно прижимать вблизи шва, к примеру, электромагнитными прижимами. Чем уже свариваемые страницы, тем целесообразнее их закрепление, с тем дабы избежать кроме этого и выпучивания.
Рис. 5. Верная последовательность сварки узла: 1 — продольный шов. 2, 3 — поперечные швы
Рис. 6. Обратный выгиб элемента тавра: а — сборка тавра с обратным выгибом, б — форма тавра по окончании сварки
Всецело устранить деформации закреплением нереально, поскольку при освобождении от зажима сварное изделие деформируетсяза счет силы, сконцентрированной на участке металла с пластической деформацией.
3. Обратный выгиб подробностей. Свариваемые подробности предварительно изгибают перед сваркой на определенную величину f в обратную сторону (рис. 6) если сравнивать с изгибом, вызываемым сваркой.
Данный прием употребляется при сварке узлов таврового сечения. Величина изгиба устанавливается умелым либо расчетным методом. Обратный изгиб перед сваркой делают с приложением упрочнения в пределах упругого, упруго-пластического и пластического состояния. Сварка изделия с упругим изгибом производится в особенных силовых приспособлениях. Изделие с пластическим изгибом сваривается в свободном состоянии.
Но для получения пластического изгиба требуется замечательное оборудование; исходя из этого таковой метод редко используется в сварочном производстве. Пользуясь обратным изгибом, возможно всецело устранить конечные деформации сварных изделий.
4. Верный тепловой режим. Для уменьшения деформации изделий, в особенности из малопластичных металлов, к примеру чугуна либо закаливающихся сталей, возможно использовать предварительный подогрев территории сварки шириной 40—50 мм с каждой стороны шва. Наряду с этим понижается перепад температур между участками сварного соединения, подвергающимися сильному нагреву при наложении шва, и, следовательно, уменьшаются напряжения и конечные деформации.
Температура предварительного подогрева устанавливается в зависимости от состава металла, его жёсткости и толщины конструкции, к примеру: для стали — 400— 600 °С, для чугуна — 500—800 °С, для алюминиевых сплавов — 200—270 °С, для латуни — 300—400 °С. При сварке очень важных конструкций из низкоуглеродистых сталей толщиной более 40 мм устанавливают температуру подогрева 100—200 °С, при сварке низколегированных сталей толщиной более 30 мм — 150-200 °С.
Предварительный подогрев делают газовыми горелками, электрическими либо индукционными нагревателями. Возможно использовать кроме этого сопутствующий подогрев.
5. Многослойные и обратноступенчатые швы. Последовательное введение меньших количеств тепла применением многослойных швов вместо одновременного при однослойном шве содействует выравниванию нагрева сварного соединения и сокращает деформации и сварочные напряжения.
Обратноступенчатый метод содержится в том, что всю длину шва разбивают на отдельные ступени и сварка каждой ступени производится в направлении, обратном неспециализированному направлению сварки. Данный метод снабжает более равномерный нагрев металла шва по всей его длине и минимальные напряжения и сварочные деформации (рис. 7).
Протяженность ступени при обратноступен-чатой сварке зависит от толщины металла, формы, жесткости свариваемого изделия. Она выбирается в широких пределах (100— 400 мм). Чем уже свариваемый металл, тем меньше протяженность ступени.
Довольно часто длину свариваемой ступени рассчитывают по длине шва, получающейся от одного либо двух электродов.
6. Принудительное охлаждение в ходе сварки. Уменьшая территорию нагрева при сварке созданием стремительного и интенсивного отвода тепла, возможно существенно уменьшить остаточные деформации. Отвод тепла реализовывают, погружая изделие в воду и оставляя на воздухе лишь участок сварки.
Данный метод пригоден для незакаливающихся низкоуглеродистых сталей. В других случаях возможно использовать массивные подкладки под швом из меди либо бронзовых сплавов, обл а дающих высокой теплопроводностью. Эти подкладки возможно дополнительно охлаждать циркулирующей в водой.
Бронзовые подкладки дают прекрасные результаты при сварке, к примеру, нержавеющих сталей маленькой толщины.
Рис. 7. Схемы заполнения швов по длине: а г напроход, б — от середины к краям, я-г обратноступенчатый; I, II, iii, iv — ступени, Л—неспециализированное направление шва
7. Использование внешней растягивающей силы. Внешняя растягивающая сила, приложенная к финишам свариваемого изделия, к примеру двутавровой балки, разрешает свести к нулю укорочение нагретого металла обжатием (осадкой). Этим устраняется конечная сварочная деформация по направлению действия силы.
Сила усадки при сварке изделия содействует укорочению, а внешняя растягивающая сила — удлинению волокон металла. В случае если волокна металла будут деформироваться в направлении растягивающей силы, то при верно подобранной величине данной силы возможно добиться полного устранения конечных деформаций сварного изделия.
Данный метод борьбы с деформациями в полной мере целесообразен, но редко употребляется из-за отсутствия соответствующего силового оборудования.
8. Местная силовая обработка сварных швов и околошовной территории. Понижение сварочных напряжений и деформаций в сварных соединениях достигается ковкой (ударной силой), обкаткой (статической силой), вибрационным давлением (пульсирующей силой) и другими силовыми действиями. Все виды силовой обработки металла шва и околошовной территории создают местную пластическую деформацию удлинения, обратную деформации укорочения от сварки.
В следствии этого сварное изделие получает размеры и первоначальную форму.
Ковка производится ручным либо механическим молотком массой 0,5—1,5 кг; холодная ковка выполняется при температуре 20—200°С, тёплая — при температуре 450—1000°С (для стали). Ковка стали в температурном промежутке 200^-450° С не рекомендуется ввиду ее возможности образования и низкой вязкости трещин.
При ручной сварке штучными электродами и при тёплой ковке направляться делать швы длиной 150—200 мм и Сразу же по окончании сварки проковывать их. При многопроходной либо многослойной сварке проковка производится по окончании каждого прохода либо наложения слоя, за исключением первого и последнего (декоративного). Первый, корневой шов проковывать запрещено, поскольку он имеет малое сечение, и при ударе в нем появятся трещины.
Верхний, узкий декоративный слой вызывает очень незначительные деформации; помимо этого, ковка ухудшит внешний вид шва. При ручной сварке с последующей холодной проковкой направляться делать швы заданной длины и проковку вести при температурах не выше 200 °С молотком массой 0,5—1,5 кг.
При изготовлении сварных конструкций время ковки превышает время сварки в несколько раз, исходя из этого ковка используется редко.
Активно используется ковка в ремонтных сварочных работах. Она усиливает структуру металла, уплотняет его и этим увеличивает коррозионную стойкость и повышает механические особенности сварного соединения.
Металлы, имеющие малую пластичность при больших температурах, должны коваться в холодном состоянии. Ковка закаливающихся при сварке сталей не рекомендуется из-за возможности появления трещин.
Сварное изделие исправляется от конечных деформаций (коробления) механической либо термической правкой. Сущность правки содержится в придании изделию новых деформаций, уничтожающих начальные, появившиеся от сварки. Механическая правка изделия выполняется вручную тяжелым молотком либо на прессах и станках, а термическая — местным нагревом изделия газовым пламенем.
Местный нагрев расширяет металл, а соседний холодный металл оказывает расширению тёплого металла сопротивление, в следствии чего в тёплом металле появляются пластические напряжения сжатия.
По окончании охлаждения нагретого участка его размеры уменьшаются во всех направлениях, что ведет к уменьшению либо полному исчезновению деформации. Для получения большого результата возможно создавать нагрев с одновременным охлаждением соседних участков водой.
Термическая правка выполняется рабочими, имеющими особые навыки.