Расположение оборудования с точки зрения соблюдения необходимых разрывов и проходов между станками
Одним из главных требовании к размещению оборудования будет соблюдение нужных минимальных габаритных проходов и разрывов между станками, и между стенами и станками, другими предметами и колоннами оборудования цеха. Это нужно для обеспечения безопасности трудящегося, обычных правильной работы и условий труда станка, и для транспортирования полуфабрикатов и свободного прохода по цеху.
Ввиду важности этого вопроса законодательством Альянса предусмотрены правила расположения и общие нормы оборудования в цехе. Эти правила изложены в книге Якимчика «Законодательство по промышленной санитарии и технике безопасности» и др.
направляться, но, подчернуть, что в необходимых распоряжениях даны только неспециализированные указания, как нужно располагать станки. Детальное же и правильное формулирование всех правил размещения оборудования было бы очень затруднительно, поскольку было нужно бы в неспециализированных распоряжениях охватить чрезвычайное разнообразие случаев и способов размещения оборудования.
Так указанные правила, являясь основанием для разрешения вопроса о расстановке оборудования, — для проектирования цеха, не всегда могут дать достаточное указание, как направляться поступать в разных случаях. Ниже приведен последовательность таких указаний по размещению станков при проектировании с позиций соблюдения нужных разрывов (взятых из практики):
1. Станки должны быть так расположены, дабы разрывы (расстояния) между ними (и между частями зданий и станками) были либо исключающими возможность прохода между ними , либо же, напротив, не меньше минимального расстояния, снабжающего вольный проход.
2. При размещении станков и другого оборудования на замысле нужно для установления надлежащих разрывов показывать на замысле (в масштабе) не только станки, но и размещение рабочего на протяжении работы, размещение тележек либо коробок для обрабатываемых подробностей (если они размером более 500X500 мм) и транспортеров. Полезно показывать кроме этого и размещение вала шкивов и трансмиссии контрприводов. Лишь наряду с этим условии возможно верить всоблюдении верных разрывов.
3. Нижеуказанные цифры разрывов направляться разглядывать как минимально допустимые размеры, меньше которых идти не нужно, поскольку это увеличивает опасность в отношении несчастных случаев, затрудняет работу станков и приводит к ряду неудобств в производстве, и очень затрудняет и осложняет междуоперационный транспорт. При повышении же разрывов нужно не забывать, что чрезмерное их повышение влечет за собою излишки в площадях цеха производственных строений, а значит, вызывает излишние капитальные вложения и удорожание производства.
При составлении замысла размещения оборудования цеха в большинстве случаев пользуются масштабом 1 : 50 либо 1 : 100, причем станки показываются на замысле собственными габаритами в соответствующем масштабе. Положение рабочего показывается кружками диаметром 600 мм в принятом масштабе. Валы трансмиссий направляться показывать условным пунктиром; кроме этого условно обозначаются контрприводы и шкивы трансмиссий.
Под габаритом станков принимается контур, очерченный по крайним, выдающимся частям станка, причем для движущихся стола и частей включается в наибольший размах и габарит их как в одну, так и в другую сторону. В габариты автоматов и револьверных станков, предназначенных для прутковой работы, нужно кроме этого включать и величину выступающего у станка прутка. Для протяжных станков в габарит нужно включать кроме этого протяжный дорн в положении перед протяжкой .
Габариты станков несложного очертания в большинстве случаев представляются в виде очерченного прямоугольника, но в некоторых случаях направляться давать и другие формы габаритов, к примеру, для фрезерных, шлифовальных и других станков, в которых форма прямоугольника была бы мало приемлема, поскольку она не характеризовала бы габарита этих видов станков. Так, фрезерный станок имеет относительно длинный стол и узкое основание, что перемещается в ту либо другую сторону на большую величину.
В случае если очертить станок, в этом случае—в виде прямоугольника, оказался бы через чур большой габарит. При пользовании подобными габаритами в планировке площадь цеха не была бы достаточно прекрасно использована.
На рис. 1 приведен пример габарита фрезерного станка в виде контура, очерчивающего станок, со всеми выступающими частями и движущимся столом. На данной же фигуре слева продемонстрирован габарит в его простом виде, лак это делается при планировке цеха.
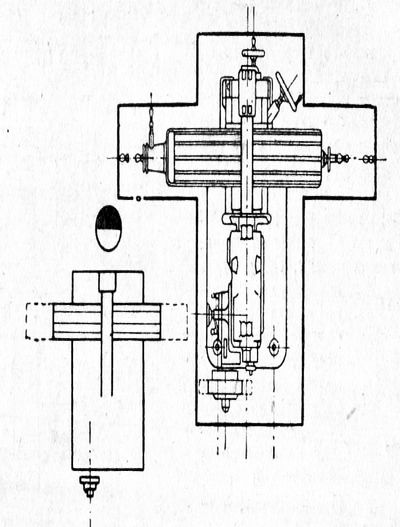
Рис. 1. Габарит горизонтально-фрезерного станка,
Рис. 2.
Ниже приведены минимальные размеры разрывов при разных случаях расположений станков.
1. Расстояние от стенки либо перегородки до задней стороны станка должно, в большинстве случаев, составлять не меньше 600 мм. При станках небольших размеров и при условии, что позади станка не имеется движущихся частей и при разрыве между станками по фронту не меньше 600 мм, возможно устанавливать станки и прикасаясь к стенке, т. е. на расстоянии около 200 мм от стенки.
Расстояние между колонной и задней либо боковой стороной станка, на которой нет движущихся частей, должно быть не меньше 300 лш. В том месте, где имеется движущиеся части, расстояние должно быть не меньше 400 мм при условии отсутствия необходимости рабочему проходить между колоннами и станками на протяжении работы.
2. Расстояния между станками, Между сторонами станков, где имеется движущиеся части, расстояние берется не меньше 500— 600 мм.
3. Расстояние между станками меньше 500 мм чтобы не было прохода рабочего направляться заграждать цепочками либо перилами. Эти промежутки полезно применять для установки шкафчиков для инструментов либо рабочих столиков. В этом случае заграждения не требуются.
4. Установка верстаков может производиться прикасаясь к колоннам, стенкам либо перегородкам. Расстояние между тисками должно быть не меньше 1500 мм при массовом производстве; при небольших работ это расстояние возможно снижено до 1000 мм.
5. Неспециализированная протяженность линии станков без проходов, в большинстве случаев, не должна быть больше 25—30 м.
6. При размещении станков так, что между стеной либо передней и перегородкой стороной станка либо фронтом станка находится рабочий, расстояние между станком и стеной должно составлять не меньше 1000 мм.
При наличии у стенки отопительных и других устройств на высоте не более чем 2 м от уровня пола указанное расстояние нужно вычислять от самый выступающих частей на стене.
7. Расстояние между задней и передней стороной станков при наличии одного рабочего между ними и при отсутствии неспециализированного прохода, перемещения тележки и т. д., — должно составлять не меньше 1000 мм.
Рис. 3.
Рис. 4.
8. Расстояние между фронтами станков, т. е. при наличии двух рабочих между ними, но без общего прохода и движения тележек, должно быть не меньше 1502 мм. При больших станках это расстояние возрастает до 2000 мм. При обслуживании же одним рабочим двух станков расстояние между фронтами этих станков принимается около 1000 мм, в случае если между этими станками нет неспециализированного прохода.
Рис. 5.
9. Минимальный размер проходов для перемещения тележек определяется следующим образом:
а) при перемещении тележек в одном направлении величина проходов между последовательностями станков, обращенными фронтами к проходу, т. е. при наличии двух рабочих в проходе, составляется из ширины габарита нагруженной тележки, плюс по 700 мм на каждое рабочее место, — т. е. 2000 мм и выше;
б) при наличии одного рабочего места величина прохода равна 700 мм на рабочее место плюс 400 мм на промежуток от задней стороны другого станка до габарита тележки и плюс ширина габарита нагруженной тележки, т. е. 1700 мм и выше;
в) расстояние между последовательностями станков, обращенных к проходу задними либо боковыми стенками, берется равным ширине габарита нагруженной тележки плюс 400 мм с каждой стороны тележки, от линии станков до габарита тележки, т. е. 1500 мм и выше;
г) при встречном перемещении тележек (в ту и другую стороны) сохраняются те же составные эти для неспециализированной ширины прохода и, помимо этого, прибавляется неспециализированная ширина габарита второй тележки и 300 мм на зазор между тележками для их разъезда;
д) для прохода, без перемещения тележек, направляться прибавить к рабочему месту еще 700 мм (для свободного прохода). Так в этом случае, при одном рабочем в проходе, ширина его будет не меньше 1400 мм и при двух рабочих в проходе — не меньше 2100 мм;
е) при наличии в проходах вместо тележек вторых видов транспорта, к примеру, рольгангов, ровных столов, конвейеров и пр., величина проходов определяется обрисованным выше методом, т. е. к величине габарита, занимаемого транспортными устройствами, добавляются вышеуказанные размеры. Проходы между стеной, перегородкой либо линиями и колонной станков определяются кроме этого изложенным выше методом.
Рис. 6.
Рис. 7.
Рис. 8.
10. Большие и сложные станки находятся в большинстве случаев более вольно, поскольку это не редкость нужно для их наладки и, в особенности, для всякого рода ремонта на месте. В этих обстоятельствах направляться давать разрывы кругом станка не меньше 500—600 мм. В случае если же станок требует и обслуживания с разных сторон на протяжении работы, то направляться разрывы для таких станков давать не меньше 1000 мм.
11. Станки, обрабатывающие большие подробности, в особенности в серийном производстве, должны размешаться кроме этого более вольно, учитывая нужные площади для необработанных и обработанных подробностей в пределах намеченных размеров партий либо серий этих подробностей.
12. Станки, обслуживаемые одним рабочим, расположенные в линию, нужно ставить вероятно ближе друг к другу, впредь до самых минимальных разрывов, для облегчения их обслуживания. Это приводит к уменьшению вспомогательного времени обработки и повышению производительности.
13. В массовом производстве, в целях наиболее наилучшей увязки и надёжной поточности рабочего места с транспортированием подробностей направляться, в большинстве случаев, в направлении потока давать кроме этого минимальные разрывы, потому, что повышение разрывов не нужно какими-либо особенными производственными условиями либо изюминками станка.
14. Для большинства станков направляться признать более целесообразным, с позиций применения площади цеха, ставить станки задними сторонами друг к другу. Это разрешает свести к минимуму промежутки между ними и расширить проходы.
Приведем пара примеров размещения оборудования с позиций соблюдения нужных разрывов. На рис. 286 продемонстрирован пример продольного размещения токарных станков в многоэтажном строении для серийного производства.
Кроме станков, на упомянутых фигурах продемонстрировано размещение и рабочих на протяжении работы, и размещение инструментальных шкафчиков и габариты проходов, в зависимости от габарита тележки.
Рис. 9.
Продольное размещение для многоэтажных строений есть простым, в особенности при трансмиссионном либо групповом приводе станков, поскольку в этом случае трансмиссионное валы эргономичнее располагать на протяжении строения. При личных моторах возможно использовать то либо иное размещение, но нужно подчернуть, что и в этих обстоятельствах для многоэтажных строений продольное размещение есть, в большинстве случаев, более эргономичным.
Рис. 10
В одноэтажных строениях, с верхним светом, продольное и поперечное размещение станков в большинстве случаев не различается, поскольку тут безразлично на протяжении какой оси строения располагать станки. Предпочтительнее, но (с позиций применения площади цеха) при разной ширине пролета располагать станки на протяжении более широких пролетов.
Более непростым представляется вопрос размещения прутковых автоматов, и и прутковых револьверных станков. Размещение этих станков в значительной степени зависит от конструкции, размеров станка, длины обрабатываемых прутков, количества установленных в цеху автоматов, и и количества станков, обслуживаемых одним рабочим. Кроме этого, при размещении станков приходится особенно принимать во внимание с конфигурацией строения и отводимой площадью под эти станки.
Размещение прутковых автоматов и револьверных станков затрудняется в особенности из-за необходимости оставления достаточного места для зарядки этих станков, которая производится с фронта либо с тыла станка: пруток в большинстве случаев помещается либо в целую газовую трубу, поддерживаемую особыми подставками, либо вставляется в две маленьких трубы, из которых одна находится у станка, а вторая на стойке, в конце прутка. Время от времени пруток помещается в раскрывающийся на две половины желоб, древесный либо из листового железа. Это позволяет без проблем вкладывать пруток конкретно с фронта станка.
В основном автоматы находятся так, что зарядка производится с тыла станка, причем прутки вращаются в газовых трубах. Разъясняется это тем, что не любая конструкция автомата допускает комфортно зарядку с фронта. В особенности это относится к автоматам громадных размеров.
При зарядке с фронта труба ставится пара наискось от оси автомата и пруток заводится в трубу спереди. При таковой зарядке требуется меньше дополнительной площади для выдвинутого из трубы прутка, чем это нужно для зарядки с тыла. При зарядке автомата с тыла нужно к занимаемой на протяжении работы длине прутка прибавить размер выдвинутого прутка из поддерживающей трубы с таким расчетом, дабы не загораживать прохода (либо же давать особый проход для зарядки автоматов).
Существует два главных метода размещения автоматов: 1) наклонное и попарное 2) расположение .
Попарное размещение автоматов, не обращая внимания на последовательность преимуществ перед наклонным, существенно реже видится в практике и, в основном, по причине того, что обслуживание в этом случае группы станков одним рабочим более затруднительно, чем при наклонном размещении. Оба эти метода владеют недостатками и своими достоинствами. направляться подчернуть, что наклонное размещение автоматов есть пара более компактным, чем попарное размещение, не смотря на то, что отличие в это же время и вторым методом по занимаемой площади в общем достаточно незначительна.
Рис. 11.
Компании, изготовляющие небольшие автоматы, время от времени советуют создавать размещение собственных автоматов в порядке попарного размещения, основываясь на нижеследующих аргументах: такое размещение не дает никакого трансформации в направлении поперечных проходов и дает некое удобство при зарядке станков. При наклонном же размещении и при наличии многочисленной группы автоматов рабочему для зарядки приходится проходить всю линию станков, в случае если станки заряжаются с тыла.
Потом, при наклонном размещении контрпривод должен быть поставлен совершенно верно над шкивом станка, в то время как для попарного размещения это не имеет значительного значения. При попарном размещении труба, в которой находится пруток, возможно вольно выдвинута влево от рабочего места, благодаря чему получается более эргономичная зарядка с фронта, чем при наклонном размещении станков.
Зарядка с фронта при наклонном размещении для некоторых автоматов, в силу изюминки их конструкции (в случае если основной шкив расположен со стороны прутка), время от времени не редкость очень неудобна либо кроме того совеем неосуществима. К преимуществам наклонного размещения направляться отнести то событие, что станки расположены фронтами в одну сторону и на маленьком расстоянии друг от друга благодаря чему существенно облегчаются обслуживания и условия наблюдения всей линии станков.
Время от времени при обоих методах размещения автоматы расставляются так, что проходы получаются по диагоналям, как продемонстрировано на рис. 294—295. Такое размещение автоматов в большинстве случаев занимает пара большее место, но воображает больше удобства в смысле их зарядки и обслуживания.
Рис. 12.
При размещении станков нужно учитывать, какая протяженность обрабатываемого прутка будет поступать в цех. В большинстве случаев на рынке имеются прутки длиною 5—6 м, но не всегда на автоматы пускают прутки данной длины. В большинстве случаев их разрезают на две половины, благодаря чему проходы между станками очень сильно уменьшаются и облегчается зарядка станков, в особенности для прутков громадных диаметров. При прутках особенно громадных размеров (более чем 60 мм) в большинстве случаев заправка автоматов ведется прутками еще меньшей длины.
Расстояние между соседними станками и прутками получается довольно часто очень незначительное: пруток практически близко подходит к корыту либо к щиту автомата. Но в работе данный пруток совсем не мешает, поскольку рабочему очень редко приходится заходить на противоположную сторону станка, собирание уже обработанных подробностей либо удаление стружки производится с передней стороны станка. Но при четырехшпиндельных и шестишпиндельных автоматах это расстояние направляться увеличивать до 300 — 400 мм.
Автоматы, обслуживаемые с обеих сторон должны иметь расстояние от задней стороны до прутка соседнего автомата не меньше 700 мм.
При наклонном размещении автоматы ставятся в большинстве случаев под углом от 10 до 20° и редко больше. Выбор этого угла зависит от конструкции станка, длины прутков и местных условий размещения станков в цеху. При наклонном размещении автоматов направляться их ставить маленькими группами при зарядке станков с тыла, так, дабы рабочему приходилось проходить не больше 10—16 м для зарядки.
На рис. 13 дан пример наклонного размещения автоматов в многоэтажном строении для зарядки с фронта и с. тыла. Расстояние между автоматами при наклонном размещении зависит от того, откуда производится его зарядка. При зарядке с фронта направляться давать разрыв между ними от 600 до 700 мм в зависимости от прутка и размеров станка.
При зарадяке с тыла возможно снизить данный размер до 400—600 мм. При громадных размерах автоматов и прутков, направляться эти размеры увеличивать, причем не рекомендуется использовать методы зарядки с фронта. В особенности это относится к многошпиндельным автоматам.
В отношении револьверных станков необходимо сообщить то же самое, не смотря на то, что при простых конструкциях и небольших размерах револьверных станков возможно пара и снизить вышеуказанные размеры.
Рис. 13.
Рис. 14.
Для этих станков чаще используют методы наклонного расиоложения и зарядки с фронта, поскольку это дает лучшее применение площади.
На рис. 15 продемонстрировано наклонное размещение автоматов с оставлением между ними проходов (продольных). В таких случаях расстояния между автоматами (между параллельными их сторонами) делаются от 600 до 800 мм в зависимости от размеров автоматов.
Таковой метод есть простым для многошпиндельных, и больших автоматов.
Рис. 15.